Having started as an independent company and then spent a brief period as a subsidiary of Biesse of Italy, Schelling Anlagenbau returned to private ownership in 2003.
Wolfgang Rohner and Stefan Gritsch, both managers of Schelling at that time, got together with two locally-based companies, Alpla and Mawera, who supported the two entrepreneurs in their buy-out of the company. Each partner took 25% of the holding.
Then in 2007, a Swiss group looking for investment in the Swiss/Austrian Rhine region, Rheintal Assets, bought 24% of the company. At this time SAB Holding was founded, owning the other 76% of the business.
These developments produced a strong capital base for the continued development of the company and its technologies.
Schelling Anlagenbau is an international business. It has a company in Slovakia, Schelling SK, which manufactures some steel components for Schelling as well as for other clients, but the main manufacturing base for the company’s products remains in Schwarzach, close to Lake Konstanz.
The company also has sales and service facilities in the US, Poland, the UK, Singapore, China, Italy, Australia and Russia – all 100%-owned subsidiaries. Other areas are covered by experienced sales agents.
“In the furniture industry, we also have a strong partnership with IMA Klessmann GmbH of Germany, which specialises in edgebanding and CNC machining centres, and this enables us to offer turnkey solutions to customers by working together,said Mr Rohner.
While the company is famous for its sawing and handling systems for the wood related industries, about a third of its turnover (total approximately €23m) is in supplying sawing technology to the aluminium, plastic and electronic circuit board sectors, using its experience in handling thin, flexible materials. Schelling has also developed a saw for steel.
Before the buy-out at the end of 2003, the company had experienced a very poor year for sales but grew continuously from that time until late 2008 when the global slow-down began to take its toll.
“Last year was very slow,said Mr Rohner, echoing the experience of most European machinery makers. “But we still managed not to lose money in 2009 and business has picked up nicely in 2010.”
Continuing evolution
A major step forward for Schelling in terms of its fundamental saw design was the launch of the Schelling Evolution sawing concept, as Mr Rohner explained.
“In older sawing systems, the saw carriage always moved the motor with its whole chassis when the saw was raised and lowered. Our goal was to find a way in which the motor was fixed to the saw carriage and it was only necessary to move the saw blade.
“This led to higher cutting speeds, less vibration and longer blade life; and where the customer is operating the old and the new system together, that difference is clear.”
The company’s Evolution computer control system, in combination with optimisation and involving several software systems, can be adapted for the customer by Schelling technologists to give a ‘hand-shake’ with existing equipment software.
“Our engineering people have a lot of experience in adapting to the customer’s needs with tailor-made solutions,said the managing partner.
“We are also doing a lot of retro-fits these days because electronics, for example, are changing very fast,continued Mr Rohner. “Thus a 25-year-old machine can be upgraded to last another 10 or 15 years.”
That indicates another part of Schelling’s philosophy – with most panel mills normally operating on a three-shift basis, the machines themselves need to be very sturdy.
Of course the saw line itself is only part of the whole sawing process. A fast-operating saw has to have infeed and outfeed systems to match – to handle the boards at the required speed – and with today’s very thin boards that is a challenge in itself.
Mr Rohner said that his company offers good solutions for sophisticated stacking and infeed requirements and also offers a complete sawing system in conjunction with a sanding line supplied by others.
“We can supply a handling system for a sanding line without involving the sawing line but normally our first contact is because of a requirement for a saw.”
Current cut-to-size projects in the primary panel industry for Schelling include a plywood mill in Russia delivered in late October and several plywood lines for Poland, plus an order in October for a big angular cut-to-size plant for Swedspan in Hultsfred, Sweden. There are also several projects under discussion, according to Mr Rohner.
The Schwarzach factory employs around 240 people, including 35 apprentices and around 50-60 graduate designers, and operates an engineering exchange programme with the US.
Capital expenditure on machinery for the factory is a continuous process, said the managing partner, including a new SHW machining centre installed last year.
And if you were to have any problems or queries about your Schelling machine? A 24-hour hotline operates from the factory and Mr Rohner said that 70-80% of queries are solved in this way, without the need for, or expensive delays incurred by, visits to customers’ factories.
Homanit Poland
A major project for Schelling, completed this year, was an installation for Homanit’s factory in Poland and the significance of this is that Homanit is famous for its high-quality thin MDF/HDF production.
This German-headquartered panel manufacturer already has eight Schelling saw lines in its factories in Losheim, Germany, and in Poland at Karlino.
Schelling developed a special thin board infeed employing two vacuum infeed carriages and a nip roller. Boards are lifted one at a time by the vacuum carriage and transferred to the nip roller.
Due to two alternately-operating vacuum carriages, speeds of more than 25 cycles per minute are claimed, with technical availability of more than 98%.
While one infeed cycle is running, the other is already being prepared – the systems are interleaved without hindering each other. As a result, Homanit says it was able to double the speed during infeed and has had some of its other saws upgraded to take advantage of the new technology.
Meanwhile, Schelling says it has developed several infeed options depending on the required weighting between capacity and protection of the surface finish: a combination of ‘nip roller system and pusher’ or ‘nip roller system and vacuum feeding rails’, as well as the dual vacuum system, if maximum protection of the surface is required.
To minimise trim waste, the alignment tables on the cut-to-size plants in Homanit’s Losheim and Karlino factories have electronically positioned, adjustable devices to align even the thinnest boards without damage and within the necessary cycle time, says Schelling.
The saw maker has also developed a saw gap closing device to avoid small trim waste fouling the system, while in Homanit’s Karlino factory, a turntable in front of the rip saw enables the cutting of complex patterns with head cuts.
To protect the material during cutting, the steel saw tables have a hard chromium-plated work surface equipped with air nozzles to provide floating panel transport.
For its stacking solution, Homanit decided on a combination of automatic stacking devices and manually-operated stacking places. A software program developed by Schelling indicates precisely to the manual stacking operators which format is to be placed in which stacking place, using colour-coding on a monitor.
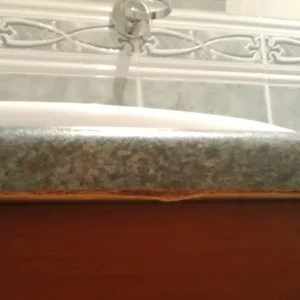