The two lines have a common feed source but once the wood enters the building, the lines are entirely separate. As product line manager, Bob Hickey also serves as plant manager in a system which ensures complete accountability. Mike Brumwell is line 1 superintendent and Elvin Carmen has the same responsibility for line 2, the newer thin board line. Finish end superintendent Chris Hader is responsible for sanding through shipping. Mr Hickey said this results in strict accountability. "There’s one person you go to see if there is an opportunity. These three individuals have taken this plant to a whole new level. They get the most out of their equipment and the most out of their people.
"In Plum Creek, one of the best assets we have, besides timberland and manufacturing facilities, is our people. With more than eight million acres, it is the US’ largest private timberland owner – in fact it is the largest private land owner," said Mr Hickey. "We run four shifts, 24/7. The only time this plant shuts down is Christmas Eve and Christmas Day," he said. Millwrights and electricians on every shift handle any problems. A day shift support maintenance group helps. Ralph Albert is maintenance superintendent. Mr Hickey reiterated the chain of responsibility, saying, "These guys are responsible for everything. From the time the wood drops in here from the truck to the time the product goes out the back door, all the way to our customers. They’re very involved with the whole process, and our customers and our marketing group. Customers come into the mill quite often – it’s very important. And we visit them. It’s not just sales people calling on them, it’s superintendents, mill managers, product line managers, sander operators, quality control people and coordinators."
As might be expected, two thirds of the mill’s raw material comes from Plum Creek sources. Plywood and lumber residues are contract-trucked, 100 trucks per day, from within a 200-mile radius of the mill. It’s all softwood species with no urban waste. An inside truck dump handles shavings, which are stored inside, and an outside dump takes the balance. A separate long, inclined covered belt serves each line. Andritz refiners process the furnish before drying in Westec dryers with Coen burners. Fuel is Sander dust and trims. The number 1 line used mechanical blending originally, but quality went up with blow-line blending. Washington Iron Works supplied the entire original line. The mats have two face and two core layers. The 5x18ft 20-opening unit presses 3’8in to 11’4in thicknesses at 3400F and 2,400psi pressure. Only side-trimming is done. The master panels pass through the Kimwood four-opposed-head sander and are then cut to desired sizes.
The mill runs strictly to order, rail-shipping 80%, with the balance trucked. Line 1 has 121 employees working four shifts. The entire operation employs 208. Line 2’s flow is similar to that of line 1 with an Andritz system through refining (one refiner is powered by a 14,000hp motor), Coen burner, and Westec dryer. From there, Siempelkamp takes over with metering and forming bins and forming line. The mill uses Hexion resins. The Siempelkamp continuous press is a 29m unit working to 400ºF as the panel speeds through at 220fpm. An Imeas four-head machine sands the master panels, after which a Schelling book saw line sizes them. Signode automatic strappers use plastic strapping. The line was designed for annual production of 90 million ft2, 3’4in basis, but Mr Hickey said this number will push 120 million ft2 this year. He continued, "Some other mills have the capabilities, but the risk of running the thin stuff we do is pretty great because of possible belt damage."
The mill’s production growth prompted a recent 42,000ft2 warehouse addition. The plant has the most advanced fire protection. Emissions control has been an important consideration in the planning, particularly with the new MACT federal regulations. The largest installation is the 1’2 acre PPC Biofilter, which uses much less power than some air-cleansing methods. The emissions are treated at ambient temperatures, not heated as in some other systems, resulting in reduced energy requirements. However there is a strong air flow with 600,000ft3 of air per minute pulled and pushed through with four Reliance-powered 800hp fans. The air is pulled from the dryer through the three beds of bacteria which feed on hydrocarbons and break them down into carbon dioxide and water. The system removes formaldehyde and methanol. Mr Hickey said further investment will be needed to get line 1 up to the anticipated 2008 EPA (Environmental Protection Agency) level, but line 2 is "good to go".
He added, "A lot of other people will have to make decisions whether they’re going to run their businesses or not. Not everyone can put a biofilter in. Some will have to install RTOs (regenerative thermal oxidisers). There will be some tough decisions. The cost of maintenance and natural gas, alone…" He said the complex doesn’t generate electricity, "at this time".
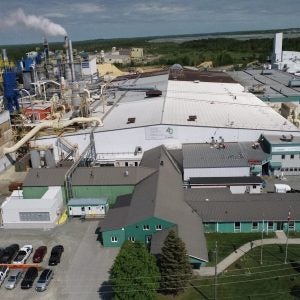