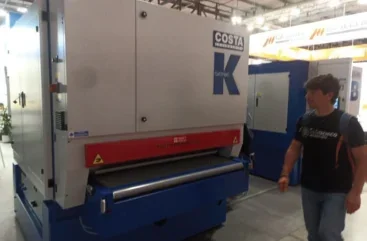
The biennial woodworking machinery exhibition that is Xylexpo was back in Milan in its familiar May calendar slot this year.
After a flirtation with an autumn timing two years ago and co-siting alongside fellow exhibitions 33.BI-MU and Viscom Italia, Xylexpo returned to the Rho fairgrounds to show the best innovations across timber and wood-based panels production technology. Even before Xylexpo – the world exhibition for woodworking technology and components for the furniture industry – opened its doors, organisers were playing down the possibilities of the exhibition size and visitor number attendance because of the difficult times experienced by the wood industries in the past year, essentially acknowledging that the background economic landscape made it difficult to present a big version of Xylexpo.
But organiser Acimall – the Italian Woodworking Technology Association – is nothing if not dogged in doing everything it can to make the long-running event a success.
By the time the 28th edition of Xylexpo closed its doors on May 24, Acimall said 11,288 people had been in attendance. This was down from about 16,000 at the last 2022 show, but better than Acimall had feared.
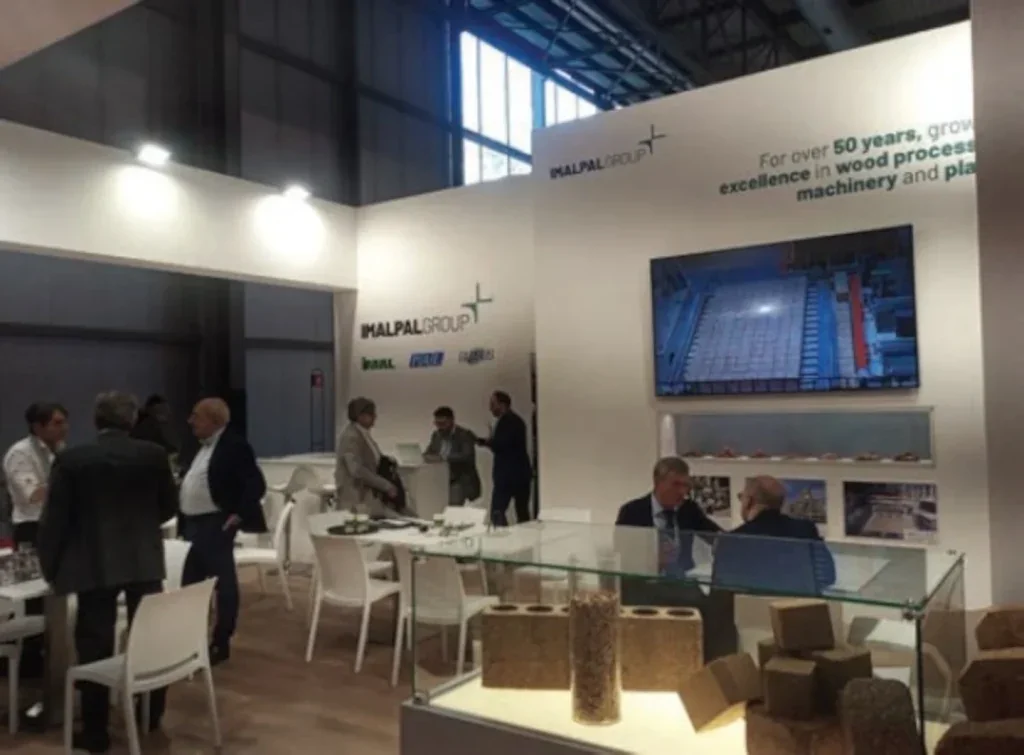
Acimall described the result as “more than satisfactory” when factoring in the general poor economic environment.
“We must admit we expected lower figures, considering the difficult period for trade fairs, but as it seems, Xylexpo’s long tradition has once again shown its attraction power,” said Dario Corbetta, exhibition director.
“Also, the decision to stay within the standard working days – Tuesday to Friday, leaving the Saturday free – was rewarded and ensured consistent attendance, after the opening day, on all exhibition days”.
Some 27% of visitors were from outside Italy, with 70% of these from Europe, 18% from Asia, 5% from the Americas, and 5% from Africa.
Acimall said many of the 270 exhibitors attending reported high-quality contacts and closing several deals during the exhibition.
Very positive figures were recorded by Xylexpo’s online activity: from April 24 to May 25, the number of “contacts” was described as “huge”, with quoted figures including 58,000 on Facebook, 77,000 on Linkedin, 145,000 on Instagram, and over 13,000 views on YouTube.
Xylexpo Digital attracted more than 3,200 “visitors” during the trade fair.
The return of better economic times, expected in 2025, will surely provide a better indicator of Xylexpo’s position in the woodworking technology fair calendar, running in the off years to the leading Ligna exhibition in Hannover.
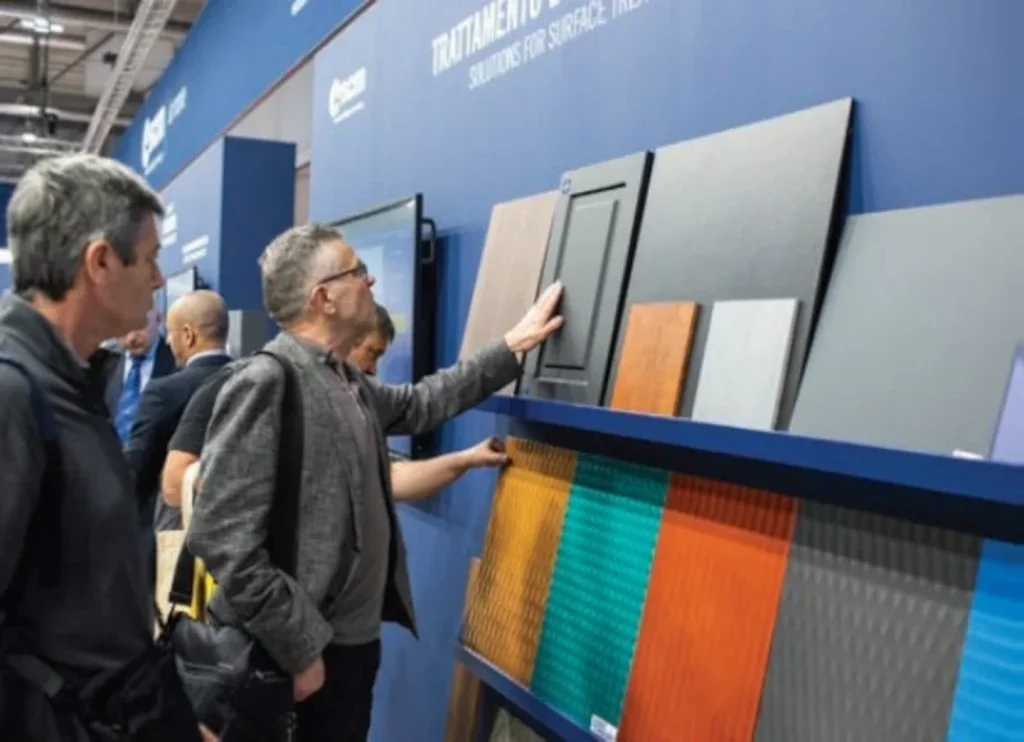
WBPI was at this show for three days and though it was a smaller edition than those attended in the past, we can report many good contacts, news and innovations, which helped show how the wood product manufacturing industry is moving forward with its technology.
EXHIBITOR HIGHLIGHTS
On the wood-based panels front, IMAL-PAL Group was the only manufacturer present that supplies whole lines for the primary wood panel production sector. Siempelkamp had initially been listed as an exhibitor in the months leading up to the show but did not exhibit in Milan.
Staff from IMAL PAL Group’s various group activities attended to talk to visitors about the Group’s expertise: IMAL in dosing and blending systems, online quality controls and laboratory testing equipment, plus forming and press technology; PAL in screening, selection and cleaning of raw materials; and GLOBUS in debarking and chipping systems, along with all the machinery and equipment required for log yard management and preparation of the work process material.
Clearly, the IMAL PAL Group sees great potential in its new partnership with MDF Recovery, bringing MDF waste fibre recycling into commercial reality, opening up a potential new raw material stream for MDF producers.
Group CEO Loris Zanasi told WBPI that a number of new contracts with wood-based panels producers were at the stage of being ready to sign, including in Asia, while in Germany screening and gluing equipment is being supplied to German particleboard producer Elka.
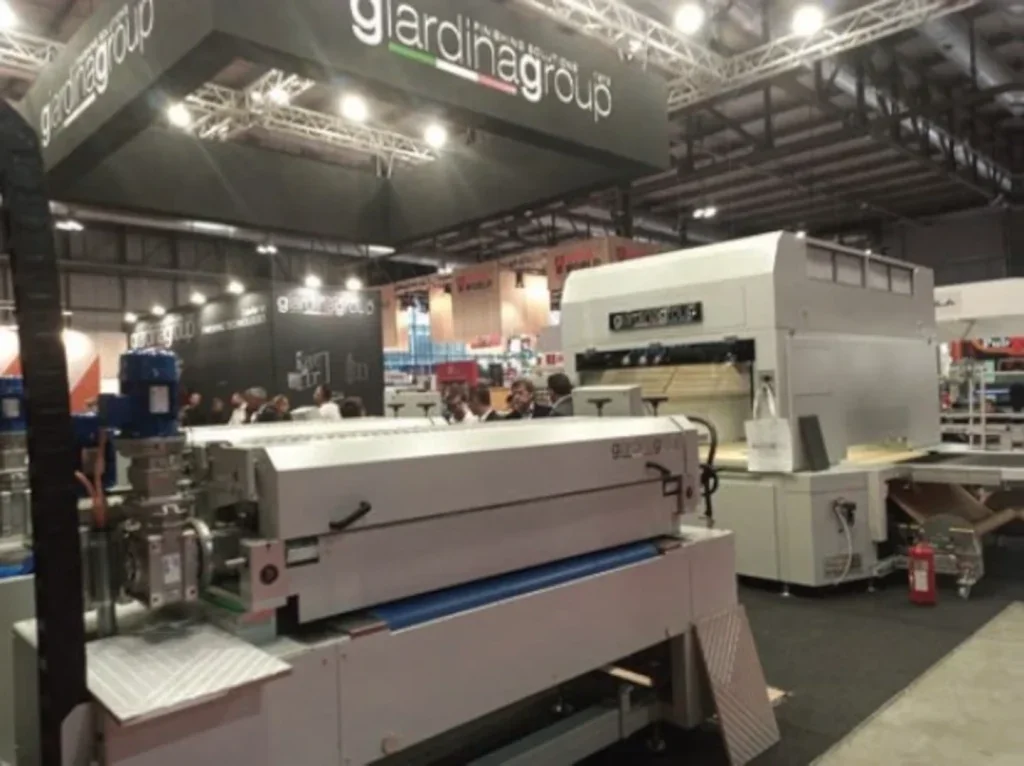
Panel finishing technology was again a popular sector at Xylexpo, with the likes of Giardina Finishing and Barberan attracting a noticeably high number of visitors.
Giardina performed live demos in co-operation with a number of paint manufacturers.
The Rolltech Flexi was in the spotlight – a roller coater machine designed and built to apply UV and conventional primers on 3D surfaces, but which has also proved to be an excellent solution for the application of special coating cycles on flat surfaces.
Business area manager Mark Robinson explained how a series of processes to apply paint, wipe off excess, touch up and cure had the ability to achieve a superior finish and save on materials. Effective finishing of grooves in MDF substrate was particularly noteworthy.
Other Giardina technology promoted at Xylexpo included Dualtech 400, an automatic spraying machine, the Destefani “Mvt 3000” edge sander, and the “Uvtech GST” oven – a new UV LED oven.
Visitors were also able to visit Giardina’s nearby facility to see specific spray coating trials with the “Zerogloss” excimer technology.
At Barberan’s stand, DeepBlue EIR technology was a strong draw. Launched last year with Unilin, Deep Blue is aimed at bringing new benefits to single-pass digital printing, including endless design possibilities (at a lower cost), quicker speed to market, increased flexibility and the ability to produce small, medium and large production runs.
The roll-to-roll digital printing line is designed to print and apply a topcoat, transforming raw roll materials into finished products. The Barberan Jetmaster digital printer is the centrepiece of the line, with an impressive 600dpi resolution and the ability to print up to six colours and accommodate widths from 630mm up to 1300mm.
A series of finishing modules enables limited finished designs in multiple materials, giving the flexibility to create a wide range of products with finished effects, both haptic and optical textures.
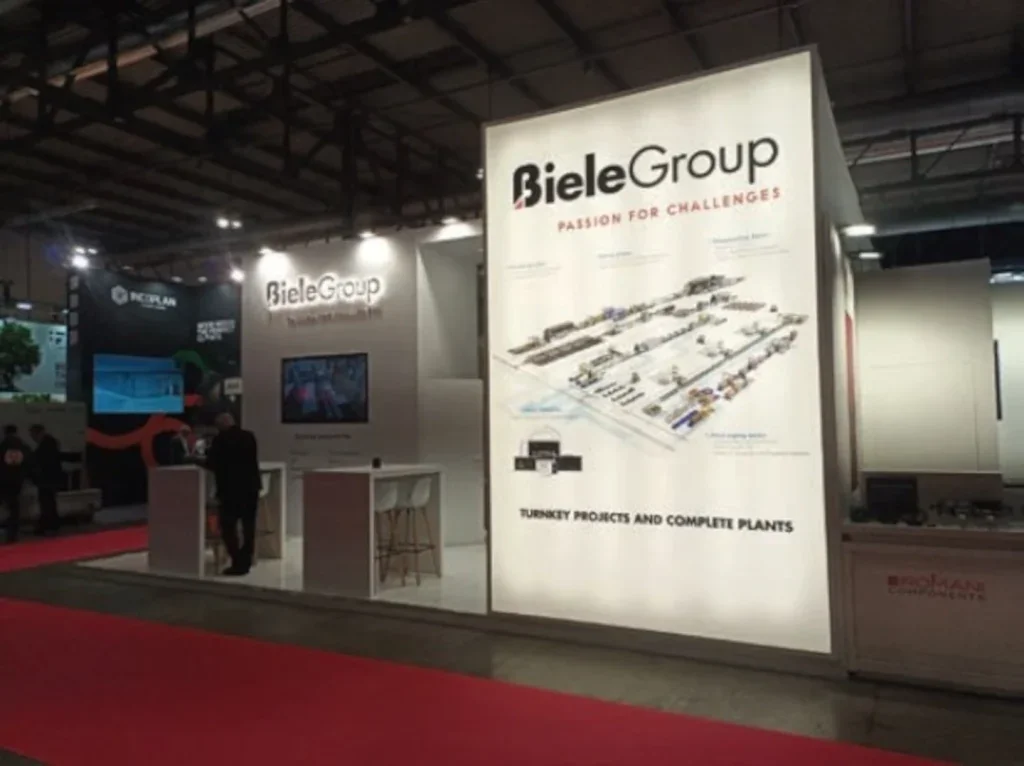
Unlike existing EIR technologies, Barberan DeepBlue brings design sharpness and texture depth via a different method – modifying the properties of the wet coat only in selected areas of the pattern and at different depths and then the texture is generated.
Other technologies, sees the texture generated directly by printing on the board.
SCM FOCUS ON MULTIMEDIA PRESENTATION
Italian machinery giant SCM took a radical approach to its stand by deciding not to display any machines but using multimedia technology instead to communicate its range of products, which includes machining centres, edgebanders, finishing systems and timber construction technology.
SCM came into Xylexpo on the back of a record 2023, which saw turnover up to €900m, with good margins. However, SCM general manager Luigi De Vito, told assembled journalists at a press conference that 2024 was a “challenging” year.
He said “multi materiality” was a big focus for SCM, with the group aiming for success with technology for a range of materials, as material use was changing very quickly. This involves the integration of CMS solutions, another of the group’s brands specialising in technologies for machining other materials such as glass, marble, metal, plastic and composite materials.
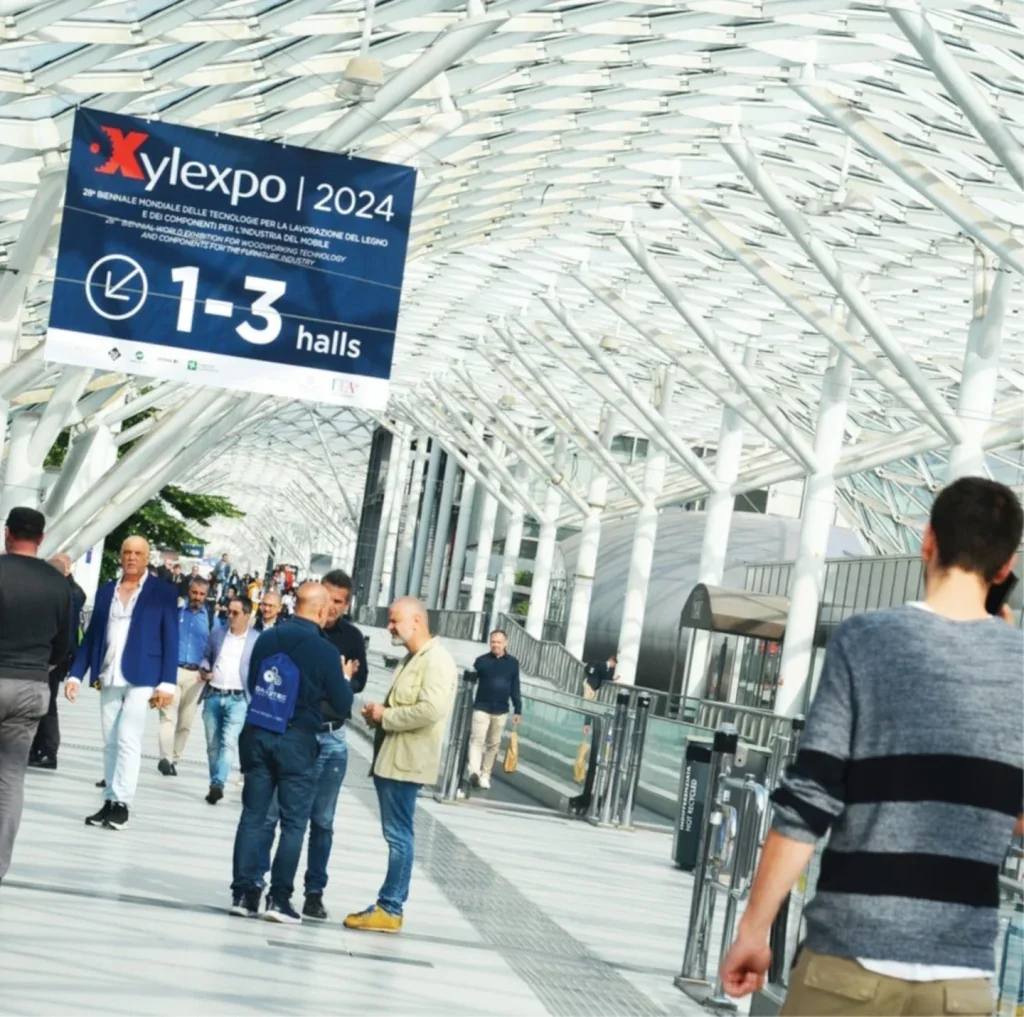
Pietro Gheller, the new director of SCM’s Wood Division, said the division posted a record €630m turnover in 2023 – accounting for 70% of Group turnover. Current order intake was a much bigger problem due to the geo-political and economic situation.
“We are quite optimistic about the second half of 2024 and 2025,” he said.
“We are seeing some signs of recovery, and some markets are seeing signs of stability, such as eastern Europe. There are also positive signs in North America and South America.”
In the home market of Italy, Mr Gheller reported Q1 had performed significantly better.
SCM centred its Xylexpo presentations around new market demands in terms of digitalisation and sustainability, and on new Industry 5.0 scenarios. Focus has shifted away from the client’s product and towards their needs in terms of support, control advice and productivity.
Innovations included the new WIN MES software to deal with factory IT flow, while visitors could explore the SCM fully operational Digital Control Room including the proactive service enabled by the Maestro connect IoT system and sustainability.
Xylexpo was also an opportunity to inaugurate the new SCM-Superfici Technology Centre in nearby Villasanta, in the heart of Brianza.
Machinery innovations included a new version of Windorflex, an automatic cell to create complete windows and doors, with two loading devices and a front-loading bench.
New gabbiani p95 and gabbiani pt95 panel saws are designed for both batch 1 production and the production line.
On the sanding front a new DMC system with laser unit is designed to create sophisticated finishes and three-dimensional scorings on parquet, wooden pieces and panels, while the DMC system xl is an automatic sanding-calibrating machine for CLT walls.
Biele Group was presenting the latest innovations in lay-up and press lines, finishing lines, packing lines and Biele Digital at Xylexpo.
“It has been a successful exhibition, with many interesting discussions, where business and personal relationships have grown,” the company said.
One of the most colourful stands was the “Wood Pub”, which brought together four companies – cut-to-size specialist Salvamac, kiln drying technology supplier Incoplan, Paoletti (finger-jointing) and Sia (adhesives).
The irrepressible Christian Salvador said the Italian market was good. “The UK market was not as good up to six months ago but is starting to recover again,” he said.
He sees further potential in the UK due to what he calls thousands of older machines in workshops which no longer meet modern health and safety requirements.
Salvamac’s mantra is the ‘three S’s’ – Simple, Solid and Safe.
Also at the Wood Pub was Italian kiln drying technology specialist Incoplan.
Production manager Carlo Sossai said connectivity/data sharing, health and safety and energy-efficiency were big issues with kiln drying. Incoplan is having a big focus on being environmentally-friendly with its technology approach – getting good drying results but using less energy.
Mr Sossai said the current market situation was slow, with many customers waiting longer to make investment decision, but he was optimistic because wood had a bright future, with signs of increased building with wood, even in southern Europe.
In the past, Russia was a top export market, but now it is targeting an increased range of regions, including North and South America, plus the Far East.
Incoplan also produces small kilns (either self-assembly or pre-assembled) and has good experience in the pallet industry.
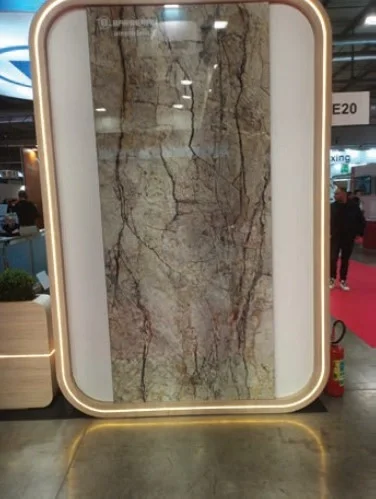
Termolegno exports to more than 80 countries and takes a holistic approach to business with a turnkey installation service to ensure quality. It offers machines for drying, steaming and HT heat treatment (ISPM-15) of wood, including tropical wood.
In the realm of handling technology, Italy-based Dalso had a large stand. Based near Vicenza, the company supplies a whole range of automation technology, including feeders, robots, manipulators, conveyors and customised automatic handling lines.
Typical markets include joinery, parquet flooring, pallets and furniture. Its main focus is supplying special customised systems for specific requirements.
It recently supplied a high-speed pallet line to an Italian customer near Parma with a speed of 240 pallets/hr. One of the more unusual projects was supplying technology for the handling of vehicle licence plates.