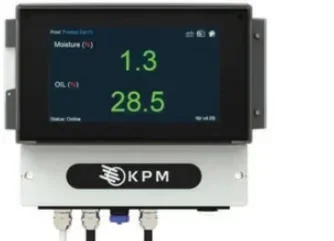
This week I found myself in a meeting with someone who said: “You can’t get wood to dry to zero moisture content anyway…”.
Now, in my experience there are two types of persons who say this – wood physicists, who know that the final few water molecules can only be prised from their locations in the wood’s cell wall under various combinations of vacuum and prolonged heating and industry-minded folk with an eye on the cost of energy and the practicalities of drying large planks to acceptable levels.
This guy was neither but had probably met plenty of industry folk in his time. Also, we were talking about measuring the moisture content, not drying planks. There is a germ of truth in his comment, but given the number of good technologies available it shouldn’t be impossible to get good moisture content values.
So, I thought, what an ideal topic to brush up in this month’s Technically Speaking!
It’s not just about kiln drying timber. There are good reasons to want to measure moisture content for making high quality wood-based panels – especially the MDF and particleboard families of products. The moisture content (MC) of the furnish at the time it moves into the press can be critical for heat transfer, curing and density profile development.
If enough moisture is present, the fibres or chips can be more flexible, more easily compressed into a good network with better quality bonding, and hopefully, less spring back when the pressure is removed. So how do we measure it?
In the lab, when we make panels, we get rapid MC results using a moisture analyser. A small sample of the furnish is put in a pan on a balance, the lid is closed, heat is applied, and the weight loss is quickly turned into an MC value. You probably have similar instruments.
This is doing a quick version of the slower laboratory method, where a cube of wood is weighed, then dried at 105°C overnight then reweighed the next day. The weight loss divided by the dry weight is expressed as a percentage to give the MC value.
The moisture analyser for furnish can work faster because the fibres or flakes are smaller, so dry quicker. The lab version uses cubes to allow bulk density to be calculated at the same time, and neat shapes are easier for the maths of that.
In other wood processing fields other instruments exist, using changes in the electrical resistance (or the capacitance for electromagnetic waves in pinless meters) that occur as the wood dries. These are also very accurate. They need to be calibrated for the species being measured – many of the main commercial softwoods are similar but some softwoods and most hardwoods can show large differences – do check!
The pin-type meters apply a small current across a short distance between the two pins that get inserted into the wood. The electrical conductivity changes as wood dries because of the way the water interacts with the cell wall material. When there is plenty of water present, a lot of the molecules are free to move or become energised with the small electrical current. As you approach a dry state, only tightly bound water molecules remain, so it takes more energy for them to interact with the current and mobilise electron transfer.
It’s similar for the moisture meters that use electromagnetic waves, but here the instrument measures changes in the capacitance (ability to store energy from the EM field) or power loss (amount of energy absorbed by the wood) or impedance (the wood’s resistance to the field). The power factor for the dielectric is high for moist wood and low for dry. But the reading is also higher for denser woods, so density has to be known to get an accurate moisture reading.
For both techniques a graph, or calibration curve, can be made between the property (electrical resistance or EMF power loss) and MC at multiple points. This is then used to predict the moisture content at any point within this correlation. Accuracy can be very high, if all the factors are taken into consideration. These systems might be used in the log yard, or early in the handling stages in the mill. Methods using an EM field (e.g. microwaves) may be used inline to monitor furnish MC, so can near infrared systems (NIR) but that might have to wait ‘til a future column issue.
What about very wet wood though? When wood is freshly felled, or ‘green’, the cells themselves are full of water. This is a bit different to drier wood where the water is only in the cell walls. Well – the moisture meter will struggle to tell the difference between wood at 30% MC (fibre saturation point) and wood that is fresh from the forest. The calibration isn’t good above the point where the free water starts to be present in the cell lumens.
Note – 105°C for oven dry weight measurement is quite a specific temperature. If we dry wood at 50°C for the same time it won’t reach the same level of dryness (it might, eventually if we left it in the 50°C oven for longer). 105°C is used to give the water enough energy to efficiently break the bonds it has with the hygroscopic cell wall polymers (like hemicellulose) and evaporate. This is where the purists (the wood physicists who seek to measure activation energy changes at super-low levels of hydration, or the size of cell wall nanopores, or related concepts) start to want even higher levels of certainty that every single water molecule has been removed. But for most applications 105°C is enough.