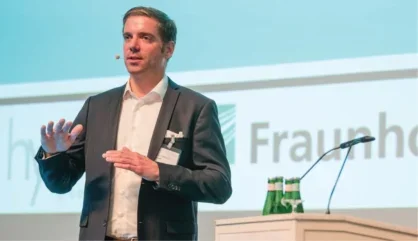
The European Wood-Based Panels Symposium is an annual event, organised by Fraunhofer WKI and the European Panel Federation (EPF), in co-operation with the International Association for Technical Issues related to Wood. The two-day symposium covers a number of topics related to woodbased panel production and of course resins are a very important part of that process.
We are going to summarise three of those presentations, covering sustainable amino resins, hydrophobic agents and fire-retardant MDF.
SUSTAINABLE AMINO RESINS
Dr Ralph Lunkwitz, of German chemicals giant BASF, spoke about the company’s approach to sustainable amino resins under the headings: Rethink; Recalculate; and Reform.
Under ‘Rethink’, he said: “The principle of sustainability, which has been applied in forestry for centuries, can be described as a way of doing business in which current needs are satisfied without depriving future generations of their livelihoods”.
He said that anthropogenic [human activity] disturbance through greenhouse gas emissions, mainly driven by industrial processes, has caused CO2 emissions to rise from 280ppm in 1850 to 410ppm in 2020. He also mentioned other greenhouse gases – methane, nitrous oxide (laughing gas), FKW gases (synthetic refrigerants) and SF6 (sulphur hexafluoride).
The speaker said that BASF aims to achieve net zero emissions by 2050 and its interim target is a 25% reduction (compared to 2018) by 2030. It has already made progress in that direction.
This brought Dr Lunkwitz to his second heading ‘Recalculate’. He talked of a “cradle to gate” approach concerning the carbon footprint of a product throughout its life cycle, with the vision that “all actors along the wood working value chain calculate, in a consistent fashion, and pass-on, their PCFs (Product Carbon Footprints) for their respective products to their customers. Finally, consumers can assess the emission associated with the products they buy,” said the speaker.
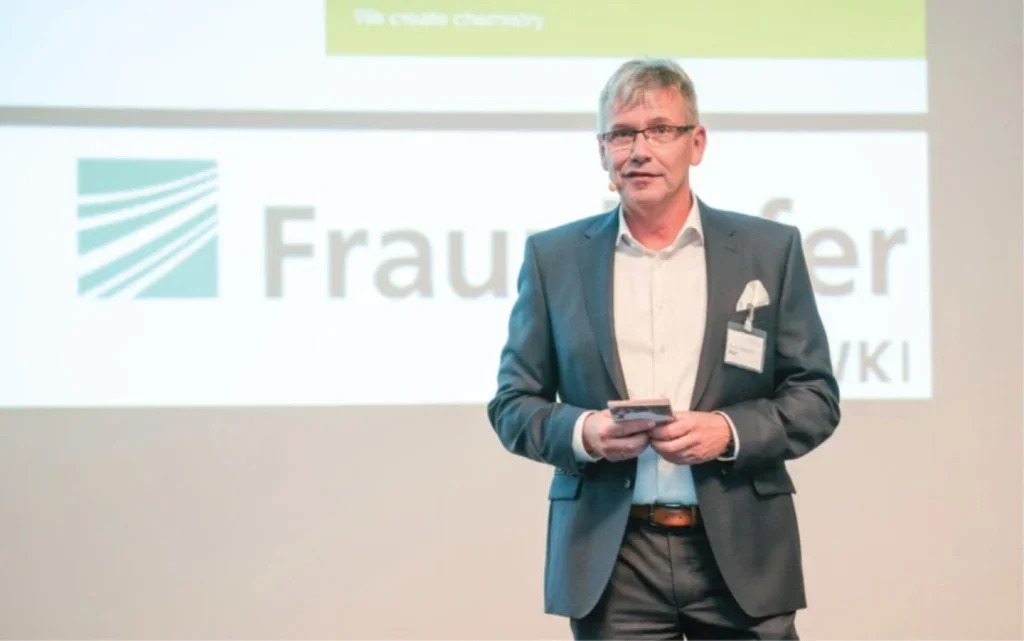
He went on to say that BASF has developed a digital, TüV-certified, solution to determine PCFs according to ISO-compliant methodology.
“Cradle to gate PCFs for BASF’s portfolio, based on process emissions, energy demand and upstream emissions have been available since end-2022 for all our customers,” said Dr Lunkwitz
He said that BASF’s structure is ideal for low CO2 emissions and offers synergies in logistics and infrastructure, use of byproducts and minimisation of waste. He added that European emissions trading benchmarks show that BASF’s chemical plants operate at above-average energy efficiency. Combined heat and power plants and integrated energy Verbund prevented 6.4 million metric tons of CO2e emissions in 2019, claimed the speaker.
BASF uses fossil raw materials responsibly, he said, with 75% of carbon being converted to products and 25% consumed for process energy and converted to CO2 equivalents.
Dr Lunkwitz next heading was ‘Reform’, under which he outlined BASF’s route towards sustainable glues and resins.
In terms of its process, firstly, under the heading “grey to green”, the company is setting up a wind farm in a joint venture with the Vattenfall company, with a capacity of 1.5 gigawatts of electricity and a Wind Energy PPA (Power Purchase Agreement) with the Oerstedt company and others.
Secondly, under the heading “Power-to- Steam”, it is moving to steam generation with renewable gas/electricity and industrial heat pumps, in cooperation with Siemens energy, said Dr Lunkwitz.
Thirdly, under the heading “New technologies”, it is setting up an E-cracker with SABIC, based in Saudi Arabia, and Linde, a global industrial gases and engineering company (an E-cracker uses electricity to reduce CO2 emissions in the chemical industry). BASF also has a methane pyrolosis test plant at its Ludwigshafen site in Germany and is working on Dry Reforming, again with Linde.
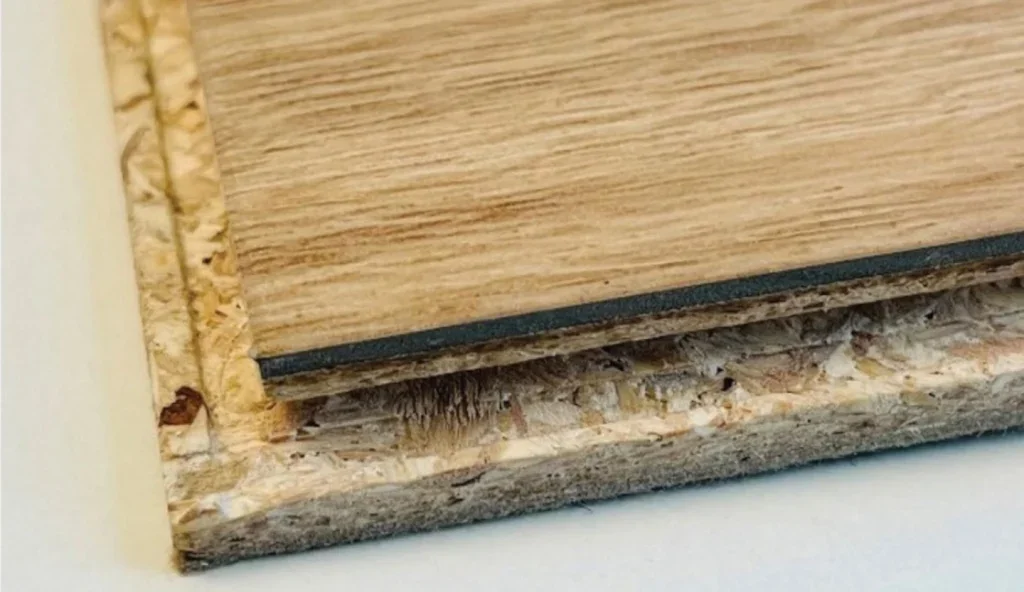
This Reform programme looks at feedstock – from natural gas to bio-gas, processes – from energy-efficient to CO2- free and products – from risk-assessed to safe and sustainable by design. As a result, BASF produces Kaurit Low PCF and Kauramin Low PCF resins (PCF reduced by 10-15%) and Kaurit ZERO and Kauramin BALANCE. He claimed the latter offer up to 100% CO2 savings.
By using biomass feedstocks, BASF replaces one tonne of natural gas with biogas, thus reducing CO2 emissions by two tonnes, said the speaker.
“Using biomass emits CO2 that was absorbed as the plants grew. It is a closed cycle, so the CO2 in the atmosphere remains constant,” asserted Dr Lunkwitz.
Using the polymer Polylisine, BASF has produced, in several industrial production trials, its LycoritTM resin and used it to produce fully bio-based, zero formaldehyde, panels. This resin, said Dr Lunkwitz, is available for industrial scale trials, is usable in existing industrial assets and is compatible with existing glues (such as (M)UF).
BASF offers Kaurit and Kauramin, with a 20% PCF reduction; Kaurit LowPCF and Kauramin Low PCF, with more than 30% PCF reduction; Kaurit ZERO and Kauramin BALANCE, each with PCF reduction to levels up to zero; and Lycorit, which is, claims the company, 100% bio-based and 100% hazardfree.
HYDROPHOBIC AGENTS
Fabian Meinker, sales manager with Hywax GmbH, spoke about hydrophobic agents for the production of particleboard with biobased binder. He said that there is increasing demand from the wood-based panel industry for these agents, as well as a regulatory requirement.
He went on to say that Bio-based binders can be protein-based, carbohydrate-based, tannin and lignin-based, as well as other origins.
Mr Meinker then reported on a test series with BASF’s Lycorit resin, using adapted hydrophobing agents in the laboratory production of particleboard. The tests concluded that: Swelling improved with synthetic waxes, by up to 7% after 24 hours; the chain length of linear molecules has a significant influence on performance; the oil content of the dispersion influences swelling behaviour; emulsifier compatible with Lycorit affects the performance of the system; and that mechanical properties were not negatively affected by the dosage amounts.
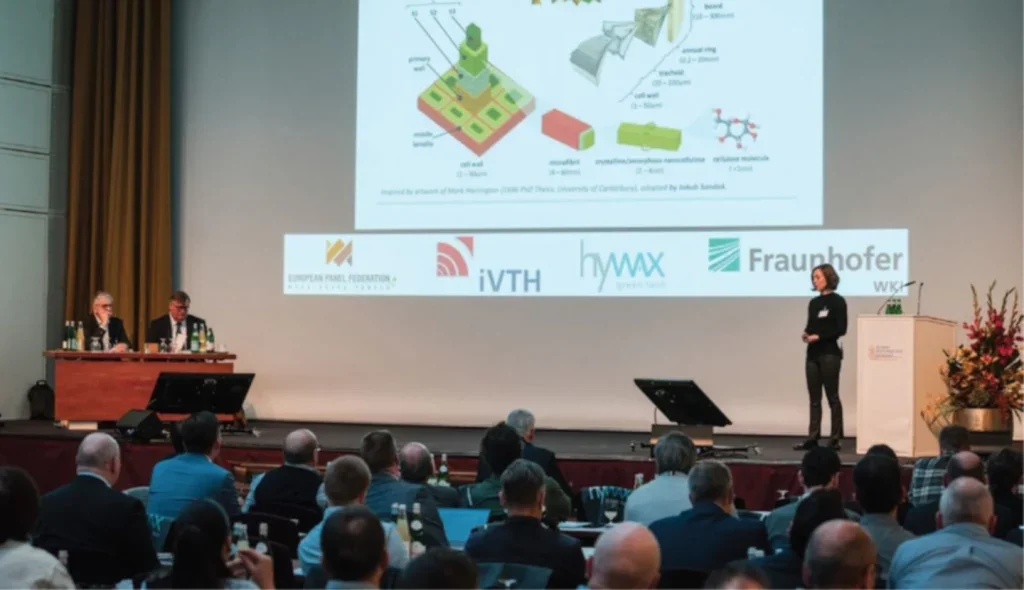
Mr Meinker then reported on a test series with Sestec Group’s protein-based binder, again in particleboard, and concluded that: Swelling improved with synthetic and semisynthetic wax blends; swelling after 24 hours was improved by up to 12.3%; the chain length of wax molecules has a significant effect on performance; the oil content of the dispersion influences swelling behaviour; and mechanical properties were not adversely affected by dosage amounts.
A third test series was run with Evertree’s bio-based binder with hydrophobing agents in particleboard.
The tests concluded that swelling after 24 hours was improved by up to 4.8%; the chain length of wax molecules has a significant effect on performance; the type of wax or blend influences the swelling behaviour; and again, mechanical properties were not negatively affected by the dosage amounts.
Mr Meinker pointed out that paraffin waxes are a by-product of crude oil refining and therefore do not have a promising future as crude oil refining declines.
Hywax expects that synthetic wax capacities will gain further momentum and that there will be a strong growth in supply of FT (ie synthetic) waxes from both established and new suppliers and a similar strong growth in the supply of LLCO. Meanwhile, the company expects major investments in this field to come on stream.
Mr Meinker concluded that: Tailor-made synthetic dispersions improve the swelling properties of a particleboard made with bio-based binders; consistent high quality could be obtained with synthetic solutions; and there is supply security with synthetic dispersions. “R&D work is ongoing with all partners in the wood-based panel industry,” concluded Mr Meinker.
FIRE RETARDANTS
Andreja Kutnar of InnoRenew CoE, and the University of Primorska, both of Slovenia, spoke on Fire retardants in wood-based panels – compatibility of materials.
Professor Kutnar said that InnoRenew’s mission is to advance the state of the art in nature-based solutions, especially using wood, which support and accelerate the adoption of regenerative sustainability.
In terms of fire safety, she outlined the essential requirements as: Load-bearing capacity can be assumed to be maintained for a specific period of time; the generation and spread of fire and smoke is limited; the spread of fire to neighbouring structures is limited; occupants can leave the building or be rescued by other means; and the safety of rescue teams is taken into consideration.
There is no question that fire retardants are necessary in panel products and veneers. The problem is whether they react with adhesives and coatings and whether they give off harmful emissions, such as ammonia – especially in indoor environments.
Professor Kutnar posed the following questions: “Certified according to EN 13986:2004 Wood-based panels for use in construction: The fire retardancy of the MDF board is often achieved with ammonium polyphosphate according to EN1350-1.
“But,” asked the speaker “do we know if it will react with any adhesive, coating, or environmental conditions? Is it suitable for veneering with any wood species?
“Fire retardants in wooden products may produce unwanted secondary effects, such as increased moisture content, reduced strength, and increased potential to corrode metal connectors (LeVan and Winandy, 1990),” she said.
“Additionally, most traditional fire retardants used in MDF are acidic, organic or inorganic, compounds (such as ammonium sulphate, ammonium phosphate, ammonium polyphosphate, organic phosphates) and when these fire retardants are in direct contact with wood fibres, they catalyse and degrade those fibres, especially in regions with hot and humid climates.
“Such environmental conditions may significantly impact the strength of fire retardant–treated MDF (Wang et al, 2010),” explained Professor Kutnar.
“Reactions can also be seen as discolorations and can occur when the fire retardant is leached from the composite, or when a wooden product impregnated with fire retardant is exposed to humid and/or hot environments (LeVan and Winandy, 1990),” cautioned the speaker.
“Because of solubility and molecular size, the inorganic salts (like ammonium polyphosphate) are susceptible to moisture movement and migrate with the movement of water in wood or wood-based composites.
“The fire retardant may therefore react with surface coatings and finishes, glues, contaminants, the chemical systems used to manufacture products, moisture, or due to other causes,” said Dr Kutnar.
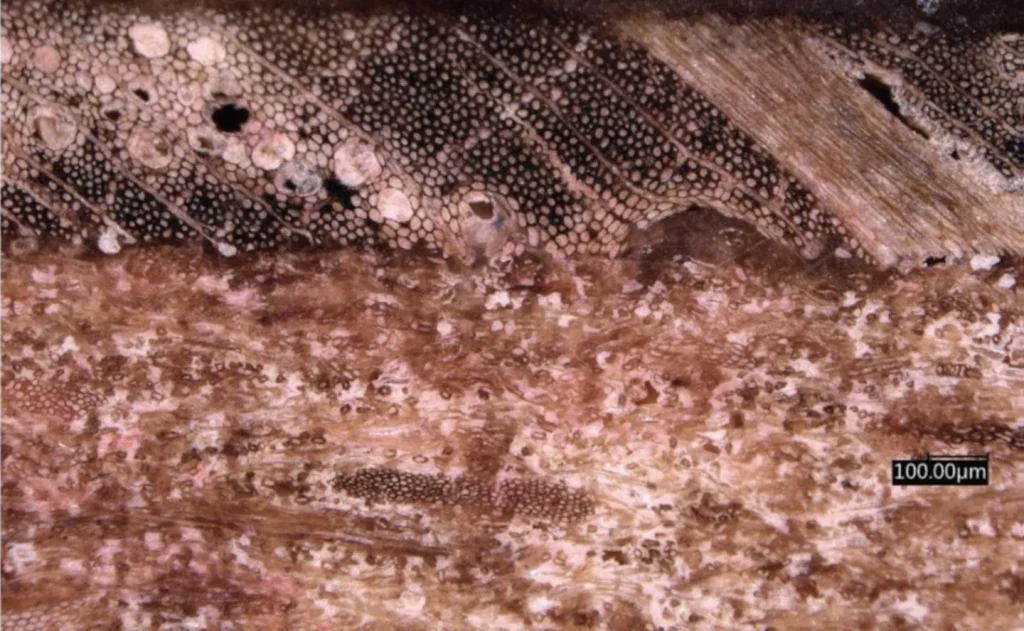
“Therefore, it is essential that producers of fire-retardant panels examine the compatibility of the panel with materials into which it would come into contact. With complete understanding of the product, the unwanted discolorations can be avoided,” she advised, pointing out that one wood species which should always be examined is oak, due to the tannins it contains, which react with ammonia and lead to a fuming effect.
“The technical data sheet of the fireretardant panels should include information about which wood species it can be used with; and which adhesives are to be used,” cautioned the professor.
“Extensive research on the compatibility of the materials should be performed before the product is placed on the market.
“The manufacturers of fire-retardant wood-based panels should examine – and communicate in their technical data sheets – the compatibility of their products with adhesives, veneers and coatings, to prevent any discoloration of surfaces when in use.”
Dr Kutnar concluded with a warning to the wood-based panels industry.
“With the increasing trend of using wood-based panels in construction, where fire regulations are clearly defined, the wood panel industry should be ensuring that unwanted aesthetic changes do not occur. Only with this assurance can we be confident that wood-based panels do not lose their attractiveness within the trend of using renewable-based materials in the construction sector.
“It would be a shame if current positive trends for the sector were lost due to a lack of research performed on fire retardant wood-based panels, prior to their introduction to the market.”