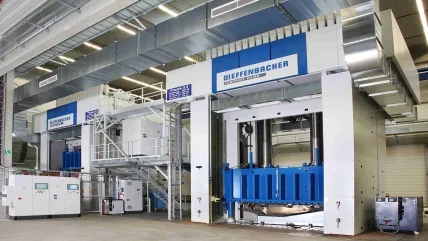
Dieffenbacher has been a leading force in the world of wood-based panel production technology for a long time now.
Its growth plans and R&D work has seen it expand its realm of expertise over the years, with it now also having a big focus in the waste material recycling sector, digitalisation and boards made from alternative raw materials.
There was a further big development with the acquisition of the assets and know-how of the Austrian power plant manufacturer BERTSCHenergy, in a move to complement its solution-based portfolio.
The acquisition took place via the newly created Dieffenbacher Energy GmbH subsidiary, with energy now forming a fourth business unit of Dieffenbacher’s portfolio, in addition to wood-based panels, forming and recycling.
The acquisition was designed to accelerate the German company’s ability to support its customers, while helping to shape Europe’s rapidly evolving energy future.
BERTSCHenergy’s existing company headquarters in Bludenz was retained, the existing product portfolio kept and most of its former employees were recruited.
Dieffenbacher’s increased portfolio now includes fluidised bed combustion systems for solid fuels (biomass and RDF), gas and steam turbines for power and steam production, plus industrial waste heat systems. In addition, the acquisition further extends the company’s long-time use of reciprocating grate-firing systems.
Wolfgang Lashofer, who previously worked for the Austrian Andritz Group for more than 35 years, was recruited to lead Dieffenbacher Energy as managing director.
At Andritz he was senior vice-president and global division manager, with his most recent responsibilities there including paper and tissue machines, stock preparation and recovered paper treatment systems, mechanical pulping systems as well as fibreboard (MDF) and recycling.
Johannes Ohlsson, head of product division group solid fuel fired power plants, is another key person in the division and had already been leading Dieffenbacher’s existing energy systems business, which is now integrated and part of the new business unit Energy.
COMBINING CAPABILITIES
Prior to the acquisition, Dieffenbacher already had an energy department, with a team of 15 at Eppingen. It has been focused solely on the wood-based panels industry, supplying energy systems to help customers generate process heat in production.
Most of the Dieffenbacher projects for process heat involve flue gas for the dryer and heating thermal oil for the press.
Its reference list for these projects extends to dozens of clients, starting in 2009 with the supply of a 22MW plant to a particleboard plant run by Rauch GmbH at Markt Bibart.
The acquisition of the assets of a US energy technology company and its knowhow in 2011 added to its capabilities and led to a number of projects in the US.
“It was around 2008 that Dieffenbacher decided that customers were demanding complete plant solutions and we needed our own energy solutions,” said Mr Ohlsson.
Recent projects include a 65MW plant at Camsan Ordu in 2021 for an MDF plant; an 85MW system at Berneck’s new particleboard plant in Curitibanos, Brazil (2023); and a 49.5MW project at Homanit in Pagiriai, Lithuania for its MDF line (2023).
Two projects due to start up in 2024 include a 31.4MW solution for Fletcher Building Products’ OSB project in Taupo, New Zealand and a 58MW plant for Swiss Krono’s OSB plant in Vásárosnamény, Hungary.
One previous co-operation with Bertsch was a project for IKEA industry Poland in 2012. On this project, Dieffenbacher supplied a reciprocating grate design for a refractory lined combustion chamber to heat thermal oil. It also needed to design a superheated steam boiler with a turbine to generate electrical power, so Dieffenbacher bought a waste heat boiler from Bertsch.
Like most operators in the energy systems sector, Dieffenbacher has been doing the design and engineering on the projects and working with manufacturing partners, while producing some key parts in-house at Eppingen.
Mr Lashofer explained that the technology offered by BERTSCHenergy was completely different and aimed at supplying mainly big power plants, using biomass or gas heat to produce steam to power turbines for generating energy and process heat.
Dieffenbacher began discussions with the company about a possible acquisition in early 2022, when the latter became financially distressed and its financiers were looking to restructure the business.
When it went into bankruptcy at the end of 2022, Dieffenbacher stepped in to acquire the assets.
About 95% of the former BERTSCHenergy workforce has been retained at the Bludenz, Vienna and Poland locations.
Dieffenbacher’s energy department now has three main product groups – solid fuel fired power plants (biomass, RDF or other waste material), which could be aimed at panel plants or industrial power companies. This is the largest sector and is headed by Mr Ohlsson, remaining part of business unit wood.
Secondly, there is the product group gas and liquid fuel fired power plants, while the third is service and lifecycle management.
Dieffenbacher was obviously keen to retain the BERTSCHenergy order pipeline.
“Dieffenbacher offered to all the BERTSCHenergy customers the ability to finalise their projects and offer service,” said Mr Lashofer.
Two major projects were acquired in Germany and two in Austria.
The move has effectively taken Dieffenbacher’s existing expertise in refractory line combustion chambers and thermal oil systems, and extended it to steam generation.
“When we did an MDF plant we supplied thermal oil heat and generated steam by thermal oil, but depending on investments and layout there are also reasons to generate steam directly,” said Mr Ohlsson.
“We were searching how to do this and then in 2021 there was increased demand from customers who said they don’t want to generate just process heat, they also want to generate electric power.”
The trend towards green energy – the use of biomass and other alternative fuels instead of fossil fuels – is another factor driving customers to make investments. Sustainability, a big driving force for both customers and Dieffenbacher, was highlighted by the company’s CEO Christian Dieffenbacher at the recent 2023 Ligna exhibition.
“There is now a great opportunity for Dieffenbacher to have access to more customers and a wider spectrum of the sector outside the wood-based panels industry,” explained Mr Lashofer.
“Bertsch was not a major player in the WBP sector. It had supplied two plants to Kronospan, but was mainly supplying power plants to the energy industry for industrial purpose and also waste recovery boilers for big power plants.
“It was a completely different field of activities and, of course, this is a nice opportunity for Dieffenbacher to strengthen its technology in the WBP industry to enable Dieffenbacher to quote a high-end [energygeneration] solution. But the major business will come from outside the WBP business – from the energy and paper industries, as well as other applications.”
Mr Lashofer explained that some WBP customers in Europe and the Americas were already operating independent power plants, which supply heat for the factory processes and also selling it to others, as well as producing electricity for the grid.
He cited a European customer as having a huge installation – running power stations based on biomassand waste wood. Others in Europe are doing the same.
Dieffenbacher Energy will also use its newfound experience to target power stations switching from coal to gas. This move away from coal to gas is backed by the German Federal Government and Dieffenbacher Energy already has some orders in this sector.
“If they switch from coal to gas, there are already steam turbines that could be used. The heat from the newly installed gas turbines can be recovered to produce steam in order to generate electricity and use the remaining process heat for central heating systems for the community.”
There are also trends to burn alternative biomass materials – rejects from the paper industry and RDF (refuse-derived fuel) and plastics to produce steam, heat and electrical energy.
“It is a wide field of opportunities,” added Mr Lashofer.
While the supply of large power plants will make up the greater share of turnover for Dieffenbacher Energy, the business does not intend to compete with the international giants and instead stay in the middle power generation bracket.
“We are not able to quantify 500MW power plants. We can execute power plants up to 150MW, this is our range.”
ENERGY INDEPENDENCE
Dieffenbacher Energy cites a definite trend of customers seeking to become more independent from energy suppliers.
Gas prices were unpredictable in 2022 and big rises were experienced – something which may be repeated in the future.
With wood product manufacturers having access to biomass, many are wanting to utilise it to make their own energy and thus insulate themselves from the fluctuations and uncertainties of fossil fuel-driven energy.
“This will have a positive impact as they have to buy CO2 certificates if they burn oil or gas, and if they burn biomass this will reduce their dependency on oil and gas,” explained Mr Lashofer.
“There is also an opportunity of burning waste wood, as more of this material is becoming available on the market and furniture sellers are having to take used furniture back.”
This provides two opportunities. Customers can run Dieffenbacher recycling lines (Dieffenbacher successfully sells these for waste wood operations), with the topquality recycled wood used for making new wood-based panels, while part of the lowergrade waste wood can be burned for energy.
Of course, there are many factors that must come into alignment when decisions are made to invest in new energy-generation, especially greenfield site investments. The price of biomass and waste wood and the price of energy are scrutinised by customers.
Dieffenbacher Energy currently has many interested customers in range of potential projects, some expected in the near term and some in the coming years.
“We definitely see a positive trend in this business,” said Mr Lashofer.
“The demand for panel products is declining a little because the market is currently reduced, so manufacturers may rather invest in a power station to create more independence from energy rather increase their PB or MDF capacity.
“Some of our customers making panel products are still very dependent on gas and are trying to become more independent from it, so there is a strong wish to find alternative sustainable power supply opportunities.”
Mr Ohlsson, who has been with Dieffenbacher 15 years, has witnessed what he calls a “tremendous change” over those years, with many WBP producers switching from gas or oil to invest in biomass combustion plant projects.
“This was quite a big change because it meant much higher investment for the WBP producer. There were some customers already in the field of co-generation.”
The trend experienced a peak two years ago linked to the peak in electricity prices. Since then, the trend has moderated.
Part of the reason for this change, aside from energy price fluctuations, is the demand and price of biomass, with virgin wood fibre sometimes being seen as too valuable to burn. Panel producers are more focused on using waste/recycled wood.
“All the recycled material goes into the panel and what remains is for the fuel. So now we are confronted in the panel industry with many ideas.”
FUTURE TRENDS
Dieffenbacher Energy has an annual turnover target of around €100-150m. It enjoyed a good start to 2023 and its order book at the end of the year was at about €200m. The project pipeline is good, said Mr Lashofer.
He said the business would aim to grow at a safe and sustainable rate, ensuring that it has sufficient resources to meet demand.
Mr Lashofer highlighted the move by some European governments to move away from residential gas heating systems in the future.
“How can that be replaced in the cities?” he questioned, adding that extension of central heating systems powered by green energy would provide part of the solution.
“Everyone has different opinions and strategies, but I feel everyone wants to reduce risk and be energy independent.”
Mr Ohlsson said there would be strong links between his team in Eppingen and the former Bertsch operations in Austria and Poland, with advantages in terms of the flexibility of the different sites and the different forms of expertise.
There is some knowledge that is only based in Eppingen – the design of the reciprocating grate for example. In Bludenz and Vienna there is the knowledge and experience for fluidized bed technology as well as process heat recovery.
“In terms of combustion size the fit is perfect,” said Mr Ohlsson. “Bertsch was not a supplier of small solutions that are not useable in wood-based panels plants, nor was it supplying giant solutions that do not apply to the industry, so we had the synergies from the very beginning.”
With energy systems a hot topic globally, Dieffenbacher’s energy business looks set to grow in the future.