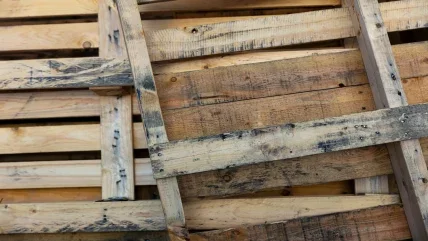
When WBPI caught up with Michele Pagnoni at Ligna earlier this year, the Pagnoni stand had certainly been busy, with numerous customers visiting.
The company had been looking forward to the event, after long enforced absences on the exhibition calendar due to the Covid pandemic period. The attendance was made all the more special as the company celebrated its 175th anniversary at the exhibition – testimony to an incredible history and a brand known across the world.
Six months later and talking this time via video conference call, Mr Pagnoni reflected that it had been good to be part of such a large, physical wood-based panels community in one place again.
“Ligna was nice; we had the opportunity to meet a lot of people we already know, but we had a few new companies also see us,” said Mr Pagnoni.
“I think it was positive to be at Ligna and positive for our industry to have the event again,” he added.
While Pagnoni met with customers from as far-flung places as Australia, South America and North America, the company these days is putting a great emphasis on seeing its customers direct, with sales staff travelling widely to discuss business.
And, of course, the rapid, accelerated use of video conferencing following Covid meant companies have a quick and effective method to get in front of customers.
“For us it is very important to be very smart and open to every requirement from the market, not missing anything,” said Mr Pagnoni.
“It’s very important to understand when the market situation is changing and get any positive effects from any changes quickly. We need to have a continuous contact from the customers, even if there is lower business this year.
“Our sales managers have met a lot of companies in the last year. We are spending a lot of time and energy going to the customers, because you have to be there when the customer says, ‘maybe I can now invest in something’”.
MARKETS
Based near Monza, Pagnoni Impianti is, of course, one of the longest established Italian woodworking plant manufacturers in the country. Founded in 1848, the company’s core offering serves the value-added short cycle press (SCP) and high-pressure laminate (HPL) markets for application of melamine papers, or other decorative surfaces, to wood-based panels.
Pagnoni can also restore platens for nearly every make of hydraulic press, regardless of the original manufacturer. When platens wear out or get damaged, they will produce imperfections in the end product and temperature inconsistencies on the platen’s surface.
Services include re-machining damaged platens and restoration of specifications from normal wear and tear.
“We had a very good 2021 and 2022 receiving good order levels,” continued Mr Pagnoni.
“We have had a good 2023 but not at the same level as 2021 and 2022. The world market is getting tighter.”
Pagnoni was seeing good business in Russia until the Ukraine war broke out. Until then it had at least one order every two years for a large plant from Russian customers. The spare parts market was also strong, with good margins. This market has obviously stopped while the conflict continues.
Far Eastern markets had already weakened before this, but more positive signals have been seen in Europe and North Africa.
“In Europe we are able to propose solutions to some customers that we had never met before because we either did not have the right products for them or they were being served by other suppliers,” said Mr Pagnoni.
He added that video conferencing has helped with this, making it easier and faster to have interactive conversations and presentations with customers.
“The situation in the market this year is different from the past two years. This is something we see directly and what customers in the wood-based panels industry are telling us about the situation.”
Pagnoni is involved in many project negotiations and planning, but there are delays with orders requiring extra time to be converted.
“We have been working in several fields – short cycle press lines, high-pressure laminate and compact press lines – this is for sure our core business. And from the production capacity and technology point of view we are able to supply state-of-the-art machinery, something we can consider our proper know-how.
“We also followed some new business trends, such as transformer boards.”
The latter relates to a Pagnoni installation in Turkey for the production of insulation boards to be used with electric transformers.
The process is very similar to wood-based panels production, but instead the raw material is pulp/paper waste.
Pagnoni has also recently installed a new press in Germany for cement-bonded particleboard manufacturer Amroc Baustoffe GmbH. This sort of application requires tough and durable machinery.
Amroc has a production facility located to the north of Magdeburg. Amroc was a previous customer for Pagnoni, which had previously supplied the original press to the company over 30 years ago.
“We are not in the particleboard, OSB or MDF [raw board] continuous press market,” added Mr Pagnoni.
“We’re now focused on value-added lines, big multi-opening lines or singleopening lines for specific manufacturing applications.”
Melamine and phenolic lamination applications are among the projects carried out.
Pagnoni has had high hopes for more business in the phenolic plywood lamination industry, especially after it installed a very large plant in Russia in 2020. But the Ukraine war has hampered these ambitions in Russia.
It is currently working on a phenolic lamination project involving a singleopening press with Finnish plywood producer Koskisen. The latter manufactures customised birch plywood panels and flooring products for construction, light and heavy-duty commercial vehicles (such as vehicle and trailer floors), packaging, interior design, furniture and the carpentry industry.
ENERGY-SAVING SOLUTIONS AND TRENDS
Saving energy is currently one of the biggest subjects in panel product manufacturing and one that Pagnoni has been ahead of the curve on. The company developed technology for energy saving in HPL production many years ago.
“In HPL manufacturing you have a lot of energy needed for heating the press plates then you have to cool down a volume of steel,” explained Mr Pagnoni.
Pagnoni has different options to saving energy and cooling down the press platens, such as energy saving tanks storing water at different temperatures.
“Now we are discussing with an Italian customer making HPL, to not only save energy in the manufacturing but less quantity of energy, starting with a re-design of press platens. We are in the first stages of this, starting with the design, and we hope we can develop it in the next months.”
Low demand in the market at a time with high energy, chemicals and wood costs are creating additional reasons for product manufacturers to increase the efficiency of their lines.
Efficiencies are also extending to changes in customer production trends.
“Two to three years ago everyone was talking about flexibility. There was a lot of one-piece and half board production because manufacturers wanted to follow the requirement of every single customer. Now our customers want to focus on stability, on lines that need low maintenance and no stops, not extreme production capacity.”
Mr Pagnoni said the company’s strength in helping its customers maximise stability in production was with its reputation for strong machinery and proven technology.
MARKET PREDICTIONS
As far as how the value-added woodbased panels market will develop in the foreseeable future, Mr Pagnoni sees the uncertain geo-political background, including the Ukraine and Gaza conflicts, as having a dampening effect on markets. However, some of the company’s customers have expressed positive indications that business can increase.
Mr Pagnoni reasons that the nature of negative current markets meant it was unlikely that positive changes would happen suddenly. It was important, he added to be prepared for positive signals when they happened.
And, of course, there are many production lines existing that still require improvement and optimisations.
“There are still some optimisations that can be obtained by automation,” he added.
“This can give a boost to the existing mechanical technology. We have focused a lot in recent years on the automation side.”