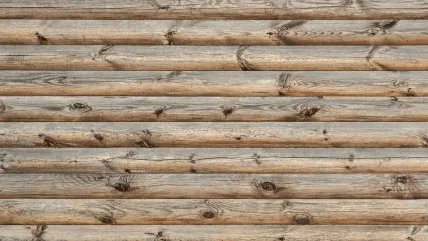
In the northern Italian city of Modena, the busy wood-based panels production machinery and technology hub of IMAL PAL Group continues to work on new innovations and respond to new market opportunities.
The Group, led by managing director Loris Zanasi, was as keen as ever to update WBPI on its developments at a time when traditional wood-based panels sectors are experiencing a reduction of demand.
One piece of news from the Modena HQ is the official opening recently of comprehensive new lab facilities called UP-CYCLE IMALPALAB, intended to help wood-based panel producer customers test new products.
The new research centre in the IMAL PAL Group lab is able to receive raw materials and produce fibre or particles, dry the material and complete gluing and pressing operations.
The lab creates a test panel production plant in miniature to help global customers test materials without interfering with their main lines.
“We can produce samples of a final product in the lab, whether it is particleboard, MDF, OSB or another board,” said Mr Zanasi.
The facilities include a lab forming machine able to make different layers.
If customers want to test recycled wood raw material, then Group company PAL – which specialises in cleaning recycled wood – can test it at its own lab facilities, where machines eliminate contaminants from the wood.
If a customer wants to use virgin wood or even different materials, then the clean material is processed in the IMAL lab, which now has a mini refiner, a hammer mill, a mini belt dryer, a blender, forming and the press.
It is this comprehensive combination that Mr Zanasi believes makes a unique testing lab for the global wood-based panel sector. In addition, test pallet blocks and moulded composite wood pallets can be made in the facility.
GLOBAL PANEL SECTOR MARKET DYNAMICS
On the subject of current market trends for wood-based panels, Mr Zanasi referenced the current changed environment for producers over much of the globe.
“The price of boards around the world is very low,” he commented.
“The producers are not happy and the margins are small at the moment. So it’s not so easy for them to make new investments in technology.”
Brazil, he added, was seeing some very low capacity utilisation rates at the moment, which he regarded as a brake on investment plans. Meanwhile, Europe has seen instances of producers reducing production output/ stopping production for periods in an effort to manage the situation and maintain product price levels.
Against this background, IMAL PAL Group has continued to promote its expertise in updating plants to customers to help them be more resource and energy efficient, as well as diversify its offering with its R&D programme in order to seek out new markets to maintain business levels.
According to Mr Zanasi, this plan has been working, evidenced by the Group’s factory order levels.
“We still have good orders and frankly speaking for the next year we are expecting to have a huge amount of projects, maybe more than we could manage next year.”
One of its areas of innovation is in moulded composite wood pallet production, with the first line recently installed at wood recycling enterprise Iren in the north of Italy, at Vercelli, near Turin.
As well as the first moulded pallet line, IMAL PAL Group has supplied and commissioned six pallet block press lines at Iren in a €40m project.
The moulded press pallet has a 1,500kg weight capacity to match the standard Euro pallet and is also the same size at 800mm x 1200mm. These pallets can run on a roller conveyor line and be handled on both sides by a forklift.
IMAL PAL Group is now negotiating two more moulded pallet factories like this in Italy.
Prospective customers are generally government-related large entities recycling waste, with Italy being one of the global leaders in reusing waste wood. These enterprises collect huge quantities of recycled waste wood, tables, doors, chairs and roofs.
Making pallets out of the waste product gives additional value-adding to their activities.
Detailed negotiations and pre-engineering drawings have already been shared with the two new prospective projects and permissions are awaited.
BELT DRYERS
A key factor in producing a good quality composite wood product is the need to have dry wood with a very low moisture content.
For that reason IMAL PAL Group has developed its own belt dryers – a product which has gained momentum in the woodbased panels sector in recent years.
The Group has supplied about 30 units around the world so far, with two of the most recent going to a new particleboard project at Kastamonu in Turkey, each dryer with a capacity of about 30t/hr.
IMAL PAL Group supplied the wood preparation systems for the line including gluing, belt dryers and screens. The belt dryers dry the particles to below 2%. Further supply of these products for a new project is being discussed with Kastamonu.
French panels producer Linex Panneaux also ordered IMAL PAL Group belt dryers recently and the two large dryers are currently being manufactured in the IMAL production halls, which will ship to site next March.
Mr Zanasi said the belt dryers were perfect machines to be linked to electric cogeneration to basically provide free energy for drying particles, getting free hot water from co-generation.
Another belt dryer order is pending in the Far East, while a further one in Vietnam also involves IMAL PAL Group supplying the customer a complete OSB line with a 30m continuous press. The capacity will be 250,000m3 / year, with the press line and belt dryer (a double deck design similar to the Kastamonu project). This line, for a customer new to the wood-based panels business, will be delivered in 2024 and be commissioned in 2025.
In total, the Group is talking with four customers for the supply of complete wood-based panels plants. “We are in a good condition with negotiations because we have pre-engineering work from them,” added Mr Zanasi.
This includes particleboard projects in Europe and a wood fibre insulation board project, also in Europe.
The latter has already involved pre-engineering work so there is high confidence that the complete plant will be ordered.
The customer is totally new in the wood business. The customer viewed the Sardinia wood fibre insulation board plant recently completed by IMAL PAL Group and is waiting for permission from the authorities for its own project. More news is expected on this project in 2024.
In other regions, the IMAL PAL Group is also competing for a new OSB line project in Latin America. Again, while technology suppliers have completed their offers, the client is awaiting final permission of the authorities but a decision is expected in the near future.
Other prospective projects include particleboard plants in India, Indonesia and Italy, though on the latter it is understood that the large projects on the drawing board there are not likely to be realised soon.
GLUING TECHNOLOGY OPPORTUNITIES
IMAL PAL Group has a long established background in gluing technology and this continues to be a big focus in terms of its development and promotional work.
In particular, the company is very focused on its new resination system for OSB production. In doing so it is competing against the traditional North American rotating drum blender products. IMAL’s solution is a blender based on a rotating shaft and installations can be found across many of the major panel producing groups such as Kronospan, Arauco, Swiss Krono, Ipan and Egger.
The technology features a lance equipped with high pressure nozzles that coat the strands when they fall down.
Mr Zanasi admitted that it takes time to convince customers to switch their method of glue blending because the traditional technology has been on the market for so long.
But he says the efficiency gains and cost savings in switching over made a compelling case for investment, citing a minimum glue saving of 1.5kg/m3 via the IMAL method.
By way of explanation, Mr Zanasi said a 350,000m3 capacity OSB plant could save 450t per year of PMDI glue. This, he claims, could result in an €800,000 saving per year, with a very fast payback on the investment cost, when also factoring in reduced cleaning time/costs and the resultant reduced downtime on the production line.
A key factor of the technology is no gluing inside the blender, but spraying of the glue in a cone before the blender, so the glue remains on the surface of the strands when they fall down into the blender.
This, he added, led to less waste glue and waste glue build-up within the blender.
A scraper inside cleans the interior and a normal steam cleaning system can be used to clean the inside, without the need to employ expensive external contractors.
A standard nozzle is used to spray the glue rather than the traditional spinning heads inside the blender. This, IMAL says, means the technology can be certified as ATEX 22 for fire protection, with the added advantage of insurance premium savings.
Manufacturers of OSB are said to be interested in the technology.
MEASURING SYSTEMS
The group also continues to improve its quality control equipment – which ranges from X-ray units for measuring density profiles on MDF lines, thickness gauges and blister control.
Measuring systems is an area that has seen significant investment by the IMAL PAL Group in recent years.
It’s a critical area for producers as the final thickness of the board has to be very accurate and reliable. The IMAL thickness control system has about 900 systems installed worldwide.
One aspect which many people may not be aware of is sanding technology manufacturer Steinemann is now using a specific IMAL thickness control gauge for its sanding machines, used to adjust the sanding process to control the thickness of the board.
IMAL PAL Group has also reported good business recently with installing IMAL thickness gauges on main production lines.
One new scanning method is its Millimetre Wave Gauge (MMW) technology for transversal surface density and moisture measurement. Based on wave scanning technology, it is typically used in the military for radar and in airport security for full body scans.
The Group sees great potential in this technology.
Elsewhere, the group’s GLOBUS business specialising in knife ring flakers has seen a strong growth curve in recent years, selling 130 knife ring flakers in China alone to date.
Mr Zanasi said the turnover of GLOBUS had grown by seven times since coming into the IMAL PAL Group. The GLOBUS (SRC) knife ring flaker with 54 knives, a diameter of 1400mm and just 315Kw can reach a capacity of 18-20 BD wood. About 240 of these flakers have been sold to date.
The PAL business was covered recently in WBPI following its partnership arrangement with MDF Recovery (MDFR). The partnership will provide PAL with exclusive rights to integrate the MDFR process with its own market-leading wood cleaning and recycling technologies.
Mr Zanasi reported that PAL was full of orders for 2024 and has roughly €160m in orders for the year ahead.