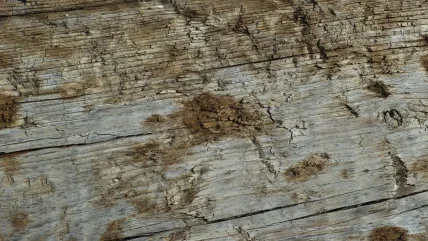
Whether it is the latest on wood panel chemistry, recycled fibre, fire retardancy or new products, the International Panel Products Symposium (IPPS) in Wales serves up a comprehensive feast of useful research.
The latest event held on October 3-4 at the Imperial Hotel, Llandudno on the coast of Wales was the first event for four years due to an enforced absence from the Covid Pandemic.
From the evidence, people are as hungry as ever for knowledge and the 70 delegates attending this year would have gone away with a great deal of information.
The event is organised by the BioComposites Centre, Bangor University – staffed by a world-leading team of wood scientists and researchers.
Panel producers represented included Kronospan, Finsa, Medite SmartPly, Kastamonu and Pfleiderer, while chemicals providers were BASF, Dynea, Hywax, Evertree, Ecose Technology, CRC and Burnblock. Other stakeholders from across Europe ranged from universities and institutes to machinery companies. Sponsors this year were CRC, MDF Recovery, Accsys and Hywax.
With so much attention on the circular economy and environmental matters generally, the keynote speaker – Alastair Kerr, director general of the UK-based Wood Panel Industries Federation (WPIF) – kicked off proceedings by tackling the decarbonisation of the UK wood panel manufacturing sector.
Mr Kerr outlined both the opportunities and challenges of the drive towards ‘Net Zero’.
He told delegates that the UK was the first major economy to commit to reduce greenhouse gas emissions with a target of Net Zero by 2050.
He also shared about research that WPIF commissioned by environment consultants SLR, designed to see how the WBP manufacturing sector can decarbonise towards 2050 and to identify what interventions were needed by Government to enable the transition.
The research looked at primary energy use at four WBP manufacturing members at eight sites producing chipboard, MDF and OSB – Egger, Kronospan, Medite SmartPly and West Fraser.
With factory drying and heat components accounting for the largest share of energy consumed, some 59% of the sector’s energy consumption comes from biomass, with 29% from natural gas and 12% from main grid electricity.
Use of alternative hydrogen energy for plants was unlikely in Mr Kerr’s view, since wider uptake of the energy source was unlikely before the late 2030s. “All the alternative options to the national grid are a long way off, and limited by location,” he added.
Panel production plants, he explained, tended to be located where the raw material resource (trees) was, in remote or semiremote locations.
Some forms of renewable energy are big investment items, but Mr Kerr thinks the economics of biomass combined heat and power plants are changing and they could become more viable as an option.
“The rate of decarbonisation of the electricity grid will be critical to the WBP industry achieving Net Zero.”
Mr Kerr said if fossil-based electricity and the natural gas grid continued to decarbonise, then the UK WBP manufacturing sector could achieve a 67% carbon emissions reduction by 2050.
A brighter forecast is possible if the sector also undertakes process technology improvements, with a carbon reduction of 79% by 2050.
His conclusion was that the UK WBP sector could achieve Net Zero by 2050 only if the emissions were offset in some way – it can’t be achieved by technology alone.
The need to reduce emissions comes at a time when a shortage of housing in the UK is likely to drive a need for more WBP products.
“There is investment in the OSB sector and demand is increasing and is likely to do so for a while yet,” said Mr Kerr.
He said the increasing demand for panels would likely be met by process improvements rather than new lines, with the exception being OSB, which is progressively substituting plywood. But Mr Kerr highlighted wood availability as a big barrier to increasing production.
MDF RECYCLING
Mark Irle, of Ecole Superieure du Bois, presented initial results from the European project EcoReFibre (Ecological solutions for recovery of secondary materials from postconsumer fibreboards) on the presence of waste fibreboard in recovered wood streams.
The project, comprising 20 companies and organisations from seven countries, aims to recycle wood fibres at the end of their life cycle and use them to produce new fibreboard. Currently, fresh wood is used almost exclusively to produce wood fibreboard.
It also seeks to separate different forms of wood waste so recycled material used to make new particleboard is not contaminated by the presence of waste fibreboard.
The rapid growth of MDF production and the increasing level of waste fibreboard entering the waste stream has made the topic of great importance.
Dr Irle shared results from the examination of waste woodstreams at French waste wood sites between June 2022 and June 2023.
Researchers recovered 57 piles of recovered wood from 24 different sites in western France. They found that some recycling centres in France use up-stream sorting to separate flat-pack type furniture (DEA) from mixed Class B waste wood.
The research showed that DEA contains significantly more panel products and, especially fibreboard. Recycling centres that conduct such sorting can offer particleboard manufacturers the choice between recovered wood with low or high levels of fibreboard.
Staying with fibreboard waste, Craig Bartlett of MDF Recovery (MDFR) presented with PAL’s Luca Ballarin about the commercial reality of MDF recycling, following the recent partnership announcement between the two companies.
Mr Bartlett told delegates the attempts to launch MDF recycling technologies by several parties in previous decades had found the market not ready. But the situation has now changed.
Some 65million m3 of MDF waste was being generated annually.
“We can’t continue the way we’re going, especially with the cost of resin and virgin fibre increasing,” he said. In addition, regulatory pressure towards Extended Producer Responsibility (EPR) is encouraging companies to design more sustainable and recyclable products and manufacturing processes.
Mr Bartlett said MDFR has established a new HQ, pilot plant and funding, recently achieving its first licence sale in the UK for loose recycled MDF fibre insulation production.
The partnership with PAL will see the latter create an end-to-end recycling solution for the MDF manufacturing sector, incorporating MDFR fibre disaggregation technology.
PAL’s Luca Ballarin predicted the partnership would have a great future, with PAL’s globally recognised sorting and recycling machinery, plus R&D labs forming a strong backbone to the partnership. 100% recycled fibre has been produced in the PAL lab, with only tiny specks of melamine, bark and paper that would have no effect on lacquer when used in a new panel product. PAL will roll out its MDF recycling system from 2024.
Another presentation touching on MDF waste was by Bartlomiej Mazela of Poznan University, who shared about XyloMatrix technology designed to produce packaging products from MDF waste. Samples of moulded food containers were handed out to delegates.
The scientific goal was to use the phenomenon of urea-formaldehyde resin hydrolysis to increase the efficiency of pulping of contaminated wood raw material.
The pulp obtained was tested for its content and emission of formaldehyde and its papermaking capacity.
The conclusion was that waste from MDF board processing represents a potential raw material base for packaging purposes. MDF pulp combined with recycled paper pulp meets the expectations for the production of packaging in the moulded fibre technology.
RESINS
Moving on to chemicals, a vital part of WBP production, Graham Ormondroyd of the BioComposites Centre gave an overview of advances in resins for wood composites followed by presentations by speakers on specific research and development projects.
Dr Ormondroyd referenced alternative adhesives based on proteins, polysaccharides, cellulose, dextrin, tannins and lignin.
Rob van Hooghten of Emulco shared how combining bio-based resins with bio-based wax emulsions could produce zero emission panels.
The research was by Emulco (bio-based wax emulsions) and Sestec (bio-based resins). MDF and PB samples produced with the natural products achieved results comparable to, or better than the reference paraffin wax emulsion panel. The panels met the IB and MOR standards for class P2 and MDF.
Additionally, with the use of natural emulsions it was possible to significantly improve the water resistance of boards with natural adhesives – this improvement is said to be so meaningful that researchers will expand their tests and activities.
Alexander Scharf, of Lulea University, Sweden presented on using imidazole as an adhesive system in PB manufacturing.
The research involved production of PB panels with different combinations of imidazole, citric acid and sorbitol. Boards were pressed to a target density of 700kg / m3, with the hydroscopic and mechanical properties of boards better at 220C pressing than 200C.
A combination of imidazole (14.4 wt%) and citric acid (11.3wt%) led to the best results, where the thickness swelling after 24h of water immersion was 6.3% and the internal bonding strength was 0.57 MPa.
Cyclic accelerated weathering showed exceptional stability with a thickness change after boiling and drying of only 2.1% compared to initial dry thickness.
Further research is needed to ascertain the discrepancy between high internal bonding strength and low bending strength.
Research conducted in Turkey into the investigation of cross-linking of esterified wood fibres for wood-based composites production was shared by Ebru Sanoglu of Koc University.
Dr Sanoglu said esterification and crosslinking mechanisms were the best-known methods for enhancd durability of wood composites. But both are lengthy processes.
The research focused on a quick twostep wood surface modification strategy to overcome the problem.
First, the fibre surface was reacted with methacrylic anhydride using microwave radiation. Then methacrylated groups on the wood fibres were covalently linked under UV irradiation.
The cross-linked structure showed increased bonding strength and dimensional stability, while hydroxyl groups on the wall were modified and pits on the surface were closed, resulting in fewer water molecules contained in the cell wall and reduced thickness variation of wood panels.
“This particular and unique technology has been successfully used to change and functionalize wood at the molecular level, allowing macroscopic properties to be controlled and improved,” said Dr Sanoglu.
Cross-linking, she said, was a fast and promising way to produce multi-functional wood composites.
EMERGING PRODUCTS AND INNOVATION
Emerging new products are always an area of fascination and IPPS had several papers focusing on innovations.
An alternative to cross-laminated timber (CLT) for construction was presented to delegates by Duncan Mayes of Lignutech Oy. Lignor of Australia started a journey many years ago to convert fast-growing eucalyptus plantation logs into high strength engineered strand lumber. The most recent development is Cross Laminated Strand Timber (CLST).
The product has longitudinal and cross layer laminations derived from LSL and is assembled into a large billet. Unlike OSB, the strands are classified and orientated to ensure mono-directional load transfer across them.
Testing has successfully met the US Mass Timber standard PRG 320. In comparison with standard grade CLT panels, the strength and stiffness values in both major and minor axis were significantly greater in the CLST panels, indicating potential to use thinner cross sections to meet required load bearing capacities. In addition, CLST features half the waste of CLT production.
Potential applications include multifloor public and residential buildings, offsite prefab housing, as well as truck and container flooring. Lignor has carried out extensive testing with Maersk in the container flooring sector with positive results.
The first commercial production plant is planned in Maine, US, with start up in late 2025/early 2026.
Fire retardancy was another focus in the new product innovation section.
Dr Dennis Jones of Lulea University shared recent studies by the university into improving fire retardancy of particleboards.
Lulea University’s work in recent years has focused on combining wood modification and fire treatment, specifically encapsulating fire treatments with the resin system, or directly modifying the wood fibres before or during manufacture.
Methods used included combining guanyl phosphate and boric acid with various systems; treatment of maleic anhydride with hypophosphite; a mineralisation process; phosphorylation of kraft lignin; and development of FRs from naturally occurring phosphorus-containing compounds.
The research has showed that several treatments offer opportunities for composite products, as well as solid wood.
Work is continuing to further advance these treatments, including the development of FRs to work in conjunction with dimensionally stable particleboards made using imidazole.
Bartlomiej Mazela, of Poznan University, presented on a two-layer based composite with fire-resistant cellulose-carbon core.
The research aimed to develop thin two-layer composite materials (max 5mm thickness) showing potential classification Bs1,d0, according to EN 13501-1.
Materials used were bleached softwood Kraft fibres, graphite and carbon nanotubes, with pine wood veneer as exterior layers.
The production process of materials includes stirring adhesives and cellulosic fibres, floating of fibres, water removal and vacuum drying. Exterior veneer is glued by starch/acetic glue in a hot press.
Control and reference samples emitted significantly more CO2 than the composite, with fire resistance increased in the latter. Total smoke emission was almost four times less with the composite.
The material’s high ability to retain carbon in the structure significantly (positively) impacts the development of environmentally friendly materials and it would likely be classed as Class C in EN 13501-1, with an additional coating likely needed to increase fire resistance to a B classification.
IPPS also focused on ‘Panels – Processing, Modelling and Properties’. This section saw IHD Dresden research on high frequency pressed lightweight particleboards from different density wood species, as well as TU Wien’s research to model the thermal processes in a short cycle press to improve product quality.
Fabian Meinker of Hywax covered ‘Hydrophobic agents in the wood-based panels industry: Wax dispersions as hydrophobic agents’, while Edze Tijsma of Accsys Technologies spoke on MDF panels made from acetylated wood chips.
The final session was on VOC management and measurement and looked at: VOC emissions from fast-curing particleboards made with lignosulphonate and pMDI binders; formaldehyde emissions from panels produced with Pinus Pinaster and different UF resins; screening of volatile carbonyl compounds in wood-based panels using a new GDME-HPLC-DAD-MS/MS methodology; and plasma treatment as an approach to lower formaldehyde emission from MDF and PB.
Some of these papers will be reported in more detail in a subsequent issue of WBPI. Overall, this was a welcomed return for IPPS and shows a huge level of research and innovation is ongoing to help meet the challenges, demands and opportunities for wood-based panels.