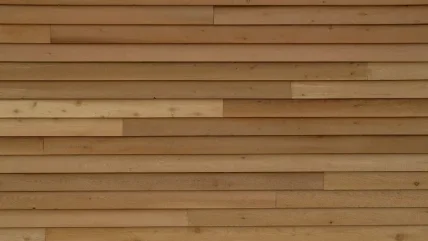
French bio-based adhesives producer Evertree has made a lot of progress in the last two years.
In 2021 it teamed up with French MDF producer Panneaux de Corrèze, based in the Limousin region of south-central France, to launch the NEXT “natural” panel with no added formaldehyde.
The product is billed as better for the environment and better for people’s health, with Evertree’s adhesive and additive products for the wood-based panel sector made from plant-based materials, rather than traditional petroleum-based technology.
Now Evertree has a second French partnership but involving wood-based panels manufacturer Seripanneaux, launching what they say is the first 100% Made-in-France biobased particleboard.
The move, the partners say, is a muchanticipated development for the furniture industry that will help accelerate its shift toward sustainability.
The new product is called PANTair and is made at Seripanneaux’s production site in Saint-Vincent-De-Tyrosse, south-west France.
The latest success with PANTair is seen as having big potential in markets due to particleboard being used in 63% of all furniture manufactured for the European market, as well as the current emphasis on sustainability, environmentally-friendly products and carbon emission reduction.
For Evertree, the momentum has definitely picked up and its hard work over the past seven years since its formation is starting to pay off.
Evertree’s raw material is derived from the rapeseed and sunflower oil agricultural industries. Oils in these industries are produced through a refining process during which the seeds are crushed and pressed to extract the oil. This produces a by-product known as oilcakes, which are used to produce Evertree’s plant-based resin.
PANTair
Seripanneaux specialises in the manufacture of raw and melamine-coated particleboard and has operated since 1962. It operates out of a 10ha site in the Landes department, employing a workforce of 90, producing 120,000m3 of product each year and generating €35m in annual turnover.
Evertree’s sales and marketing director Maxime Legendre told WBPI that the level of bio-based resin in both PANTair and NEXT is almost 100% (98% bio-based), switching conventional urea-formaldehyde resin over to Evertree technology.
“For sure both the panels are made without added formaldehyde and isocyanates,” he said.
“We cannot say the panels are totally without formaldehyde because there is still the emission from the natural wood, but we are not putting formaldehyde into it.
“This is definitely a great achievement for us and we have done a lot of R&D to get to this situation.”
Mr Legendre explained that PB was one of Evertree’s main goals. It had gone first with a MDF solution because it was ready with this and panel producers had asked for it.
Evertree has its own laboratory and press where it can test panels using its resin technology.
“It took only nine months – between July 2022 and March 2023 – to work together with Seripanneaux to develop this panel and commercialise it,” added Mr Legendre.
With the PB and MDF products, Evertree believes this represents the ability to provide fully bio-based kitchen furniture panels.
“Now the market is able to make fullybased bio-based panel furniture with PB and MDF and we are quite happy we have achieved this.”
Seripanneaux has two production lines, with one of these producing PANTair.
“For now the factory is not fully using the PANTair capacity as it’s a new range for them. For sure we will be happy if in a few years’ time the company is only making PANTair.”
So now that MDF and PB partners are producing bio-based boards using the Evertree technology, what is the next step?
“Our commercial vision is to keep developing with our existing partners – Panneaux de Corrèze and Unilin for MDF – and Seripanneaux for the chipboard.
“The first objective before we go to other panel producers is to keep growing with our partners. We are open to grow with other panel producers in Europe, but this is the second objective,” said Mr Legendre.
“We plan to extend our range of products, such as moisture resistant (MR) and fire retardant (FR) panels. Also, we want to propose our technology to other applications, so we are putting a lot of R&D effort into being a bio-based resin reference on the global wood-based panel markets.”
Evertree is also working with architects, specifiers and the furniture industry to develop projects to make tomorrow’s kitchen fully bio-based, beds for children featuring no added formaldehyde or a new office making it with only bio-based panels.
Mr Legendre said having a bio-based wood panel was one thing, but it was necessary for the market to change in this direction also.
Evertree exhibited for the first time at the Interzum show in Cologne in May, where it had the opportunity of showing the solutions to furniture producers and interior designers.
France, Germany and the UK, Mr Legendre said, were particularly keen in wanting to move in the bio-based panel direction.
“On the NEXT panel we have at least a 40% carbon footprint reduction, which is validated by a third party. On the PANTair we have 30%.” The PANTair carbon footprint reduction is currently going through the review process for validation.
THE FUTURE
Mr Legendre said Evertree understood the important priorities in the bio-based resins market – that first of all that this alternative solution must provide the same mechanical performance or better as conventional resins. Being better “for the planet” and for people provides the additional sustainability advantage.
“We believe Evertree is part of the answer because our solutions are working. But we also believe we will not be the only company to replace urea formaldehyde in panels. There will be different solutions adapted to different applications so there probably is space on the market for different bio-based technologies. But we believe we have a strong solution for the wood panel industry.”
Evertree’s director of innovation and business development Xavier Le Fur has many years previous experience working in the wood-based panels industry with Sonae Arauco.
Mr Legendre said it wasn’t just the furniture industry looking for healthy products with good sustainability credentials and a low carbon footprint – the construction industry was also looking for solutions.
This includes plywood, OSB and wood fibre insulation boards – which are all within Evertree’s target markets.
Evertree already has its Green Boost product – an adhesive for OSB which replaces part of the conventional resins (such as PMDI) typically used in OSB manufacture.
“We are making some progress in the plywood industry,” said Mr Legendre.
“Wood fibre insulation board is still undergoing R&D but this is definitely one of our projects.”
OSB uses different technology in its manufacture and moisture resistance is important for many applications, so currently Green Boost is used to reduce PMDI by at least 20% to reduce the carbon footprint production of the OSB panel at a competitive cost.
Evertree has a team of five people in the US to serve the giant OSB industry there.
“We have much more advances with the product in the US than in Europe because the OSB market is much bigger there.
“It has been a long journey to get to this point and we have a long journey ahead of us,” reflected Mr Legendre.
“It is quite exciting as we really believe we are part of a change happening in the woodbased panels industry. The panels industry uses a great material – wood – and now the remaining part, which is fossil-based resin needs to be changed and we are part of the solution. We believe the market is changing now.”