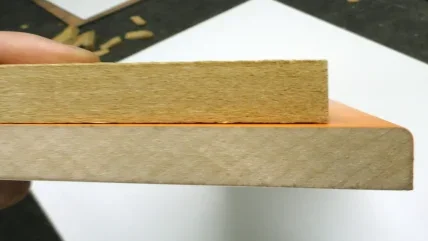
Wood fibre insulation boards have proved to be a star performer in the world of wood-based panels in recent years, with their growth trajectory look set to continue.
Several large projects for new wood fibre insulation board facilities have recently been completed or are moving forward, with leading producers still rating 2023 to be a positive year for the business, despite the unsettling economic and geo-political background.
European wood fibre insulation giant Steico said recently that it expects renewed mid-range single-digit percentage revenue growth and an EBIT margin of between 12% and 15% in 2023, which is encouraging.
Although 2022 production statistics for the European wood fibre insulation board (or ‘softboard’) industry are not publicly available yet (they will be published in June), EPF stats on wood fibre insulation from its 2021-2022 Annual Report show the recent trend.
The headline stat in 2021 was the largest ever production year for softboard in Europe.
European softboard production accelerated its growth from 5.7% in 2020 to 12.6% in 2021 thanks to announced new capacity. The output reached more than 5.6 million m3, surpassing the historical high reached in 2018 by 455,000m3.
Rigid softboard accounted for 57% (61% in 2020) of the output and flexible softboard for the remaining output. And 96% of the sales went towards the EU-27-UK, EFTA, Russia, Turkey and the Balkans.
Installed production capacity for rigid softboard remained stable at 3.42 million m3 in 2021, while for flexible softboard it increased by a further 450,000m3 to 3.32 million m3 thanks to an extension project in France.
Poland remained the largest producer of rigid products, while France overtook Poland as the largest producer of flexible products in 2021. Norway was the third largest producer of flexible products. Germany, France and Norway are the next biggest rigid product manufacturers.
The largest individual application was in building shells – 35% for rigid and 28% for flex. Rigid underlays were also a big segment.
EU imports of softboard amounted to 75,000m3 in 2021 – 56% higher than 2020, mainly due to shipments from Norway and China.
EU softboard exports amounted to 453,000m3 in 2021, up by 4.2% compared to 2020. Switzerland was the largest importer of EU softboard (34%), followed by the UK (19%).
When it comes to showing how the sector is doing, Steico’s financial results give a good clue as to the current trajectory.
In early February, Steico reported total annual operating revenue up by 18.2% to €467.6m (e) in 2022 (2021: €395m) . EBIT was around €63.8m (e).
The company operates the single largest integrated plant for the production of wood fibre insulation materials at Czarnków, incorporating four wet process board lines, two dry process lines, two lines for flexible mat products and a line for wood fibre airinjected insulation.
Also in Poland, at Czarna Woda, there are four wet process production lines (one under construction) and in Gromadka, Poland there are two flexible mat lines and one dry process manufacturing line. In France, at Casteljaloux near Bordeaux, a dry process line has recently been constructed and there are two existing flexible matt lines.
The company says it is operating in a market environment that is experiencing a “phase of normalisation” after booming demand for around two years.
“Wood-fibre insulation materials are now again enjoying short-term availability, which is why dealers and processing companies are returning their stocks to normal levels,” it said. “This development also characterised the fourth quarter of 2022. The winter season in the record-breaking year 2021 was extraordinarily strong, however, customer ordering behaviour in the winter of 2022/2023 got back to normal, with inventory levels falling.”
Steico is now using the winter months again to replenish its own inventories in order to be well equipped for the coming construction season.
Despite increased challenges from high inflation, increased interest rates and more intense competition, the company’s management is taking a positive view of 2023.
The company’s management is still convinced that demand for ecological construction materials will continue to enjoy dynamic growth and is aiming for its revenues to grow to around €750m by 2026.
NEW CAPACITY
The positive view appears to be shared by Gutex, the German based producer, which was the first company in Europe to manufacture insulation boards from wood fibre back in 1932.
Gutex was also the first manufacturer in the world to produce single-ply homogeneous wood fibreboard insulation using a dry process with Siempelkamp equipment in 2006.
The company’s current mill is in Gutenburg in the Black Forest, with the company’s annual production at around 1 million m3.
Its plans for a new plant at Eschbach near Freiburg have been progressing, with the original schedule for a start-up in the second quarter of 2023 and commercial production envisaged before the end of the year.
The plant on the Breisgau industrial park is intended to be a CO2-neutral facility and will have a 30,500m2 floor area, using regional softwood in production.
Gutex is investing more than €100m in the project, with 60 new jobs created and double that when it reaches full production.
The dry process plant is to be operated in three shifts all year round and the drying plant has a production capacity of up to 4,800m³ per day.
The raw density of the wood fibre insulation boards is between approximately 100kg/m³ and 190kg/m³, depending on the area of application.
Gutex said the investment would help to meet growing demand from builders who want to insulate their buildings in a healthy and sustainable way.
The Eschbach site was chosen for the possibility of realising a CO2-neutral energy supply, good infrastructure and high availability of wood in the surrounding Black Forest and in the Vosges. Photovoltaics will generate green electricity and a biomass plant is to supply process steam and heat. Additional process heat is obtained from the neighbouring waste incineration plant.
The direct motorway and industrial rail connection, the central location in the border triangle Germany-Switzerland-France and the proximity to the main plant in Gutenburg also had a positive effect.
Andritz is one of the technology suppliers involved in the project, supplying a fibre preparation system.
The scope of supply comprises a complete fibre preparation line, including a debarking and chipping line as well as the steel structure, piping material and installation work.
Technical aspects include wood processing technology for receiving of logs, an Andritz RotaBarker debarking system, a horizontally fed HHQ-Chipper, a fully automatic chip storage system with reclaiming and screening equipment; a high-consistency (HC) refiner ensuring a constant refining gap that is essential to obtain high fibre quality and low specific energy consumption; and a steam recovery system (SRS) for efficient recovery of surplus steam and greater thermal efficiency of the fibre preparation system.
Michael Rupp, vice-president for Panelboard Systems at the Andritz Paper, Fibre and Recycling Division, said the company was delighted to have the opportunity to install its complete front-end technology at Gutex’s new plant.
Meanwhile, Ziegler Group has started its new wood fibre insulation board mill less than a year after construction was started.
The investment, based on Dieffenbacher technology, produced its first board in Grafenwöhr on August 30, 2022. The line produces rigid wood fibre insulation boards.
Production is designed for 500,000m³ of fixed and 1.5 million m³ of flexible panels per year, as well as 20,000 tons of blow-in insulation.
Despite a change of location at short notice from Bärnau, 50km west, to Grafenwöhr, construction of the new plant began just five months after Dieffenbacher received the order.
Dieffenbacher’s scope of supply for the complete plant included a fibre dryer, EVOjet M 2.0 gluing system, the forming station and forming line with pre-press, a CSS continuous steam press system, the raw board handling system, electrics and automation and the MyDIEFFENBACHER digital service platform.
“The change of location and the procurement crisis during the pandemic made this feat all the more remarkable,” said Andreas Sandner, commercial managing director at Ziegler Group.
In addition to the plant just completed, Ziegler Group commissioned Dieffenbacher to supply another fibre dryer for flexible insulation mat production at the Grafenwöhr site, with the 10-tonne-per-hour capacity dryer going into operation in 2022.
“It makes us proud to be able to say that our insulating fibre board plant is one of the largest and most modern plants of its kind,” said Ziegler.
Moving into France, insulation giant Soprema is moving forward with several projects, one of which involves additional woodfibre insulation board capacity for its Pavatex Brand.
A plant is currently being assembled in Chavelot, France, near the existing site in Golbey.
Two other Soprema insulation projects are non-wood, though one involves natural products – rice waste for a natural insulation board facility near Nimes, which is being commissioned in 2023. The additional ‘Pavatex 3’ woodfibre insulation plant in Chavelot involves Siempelkamp technology, with assembly due to start in the final quarter of 2023.
Its design capacity is approximately 55,000t of boards per year; which effectively doubles Pavatex woodfibre insulation board capacity to 110,000t per year.
It is the second Siempelkamp plant for the production of its Pavatex wood-fibre insulation, with the scope of supply being almost identical to the Golbey plant, which started up in 2013.
The technology focuses on the dry production process, with a ContiTherm calibration press. After screening, the wood chips are thermally and mechanically defibreed and dried in the long flash dryer supplied by Siempelkamp’s subsidiary Büttner. The Siempelkamp control system Prod-IQ.quality is also part of the plant concept.
Another feature is flexibly applicable gluing units, where the fibres are glued only after drying.
The Pavatex products manufactured meet the strict requirements of natureplus, the quality label for ecological, health, environmental and function-compatible building products, and carry numerous other environmental labels.
Going back to Steico’s capacity expansions, the new production plant using the dry process at Casteljaloux has started regular operations, with a capacity of 250,000m3.
The new 135,000m3 capacity production plant for wood fibre insulation materials from the wet process at the Czarna Woda site is still in the commissioning phase.
And at the new Gromadka site, work on the construction of the new insulation plant is progressing. Commissioning is expected to start in mid-2023.
Valmet succeeded with orders for two second-generation EVO Defibrator systems for the new plant at Gromadka. Valmet says this move further strengthens its position as a supplier of fibreboard and insulation board front-end systems.
In addition, Steico has plans for other large production plants: two for flexible wood fibre insulation mats with a production capacity of over 1 million m3 / year and one for wood fibre insulation boards with a 500,000m3 / year capacity using the dry production process.
In Switzerland we have an update on plans to recommence wood fibre insulation board production in the country.
Schilliger Holz AG says the absence of such a plant currently in Switzerland has created a large gap in the Swiss wood processing chain.
Its development plans focus on the Perlen Papier AG factory site near Lucerne and involve the erection of a factory building with a maximum height of almost 40m on a floor area of 6,000m2. Production of the insulation boards will be distributed over two floors.
Boards will be made under the “Lignatherm” product label.
“This will add an important element to the wide range of Schilliger wood products and the comprehensive customer service,” the company said.
The CPH Group is believed to be leasing the company a 20,000m2 land plot for the plant’s construction, and will also supply power and water for the new operation.
Commissioning is scheduled for 2024.
TIMBERHP
In North America, the first wood fibre insulation plant has been taking shape in Madison Maine and the commercial roll-out of products is getting ever nearer.
And with the nearing of completion, the company name itself has changed from GO Lab to the brand name of TimberHP.
“We are fortunate to have such a strong, recognisable brand name and identity in TimberHP,” the company said.
“The change is timely with the launch of our new website and our entrance into the market with our product line in early 2023.”
Loose fill wood fibre insulation is being launched in the spring, followed by 4in flexible batts in the summer and then rigid wood fibre insulation boards in the autumn. The rigid boards are composed of softwood fibre, PMDI adhesive and paraffin. TimberHP is utilising the dry manufacturing process.
The rigid TimberBoard product is designed as a vapour open, continuous insulation with a stable R-value, high heat capacity and high compressive strength.
A grand opening ceremony is due to be held on July 21.
It’s been a long journey for the US$125m project, which was originally announced back in 2015.
Much of the equipment was sourced from the European wood fibre board producer Homanit and shipped to the US. The equipment had originally been installed by Dieffenbacher at the latter in 2009.
Dieffenbacher supported the company in financing the relocation and planning of its re-installation. Dieffenbacher has also modernised the plant and installed new equipment, including a gluing system and dryer.
Building Green has already named TimberHP as one of its top 10 new products for 2023.