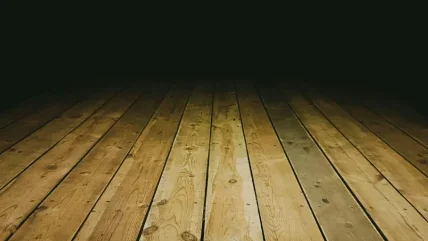
In our Focus on China Part 1 in WBPI Feb/ March issue, we looked at the massive market for wood-based panels in the country and how technology providers are supplying the industry.
For our Part 2 report, we again interview key technology players active in the market – this time Shanghai Wood-based Panel Machinery Co Ltd (SWPM) and its parent company Dieffenbacher.
SWPM general manager David Ye, along with Matthias Ruebsam, Dieffenbacher sales director China, Business Unit Wood, joined WBPI by video conference to give us their latest updates and market observations.
Located on a 90,000m2 site in Shanghai’s Anting district, SWPM is a leading Chinese supplier of wood-based panels production equipment and has a history of more than 70 years in business. The company manufactures 4ft continuous presses for MDF, particleboard (PB) and OSB production, as well as multi-opening (MO) presses.
Shanghai has of course been in the news recently in relation to the Covid-19 pandemic and the stringent measures being undertaken there to control a latest surge in cases in the city.
Mr Ye said the Chinese government’s zero-Covid policy meant not only lockdown restrictions on movements of the general population but on numbers of workers operating on site.
SWPM’s factory is a major manufacturing plant in the area with 450 employees.
At the time of our interview, the company had special local government approval to continue operating during the lockdown, with a reduced workforce of 80 employees allowed on the factory site and having to stay there 24/7 with dormitories on site.
“The manufacturing operation can partly continue, while the sales and communications with customers are still ongoing and major communications with Dieffenbacher in Germany continue on a daily basis with no interruption,” explained Mr Ye.
Mr Ye said his observation from his home in the Pudong district was that though most supermarkets and pharmacies had closed in the lockdown, government food supplies were working and the situation was calm, with the expectation that things would open up again soon. “The atmosphere is completely different to the earlier Wuhan outbreak,” he added.
SWPM BACKGROUND
For most of SWPM’s long history, the company was 100% state-owned. A huge milestone was the 70% majority share acquisition by international wood-based panels technology manufacturer Dieffenbacher in 2009. Buying the 70% stake in SWPM from Kronospan made Dieffenbacher the majority shareholder of SWPM.
“It was very important that SWPM became integrated into the Dieffenbacher group,” said Mr Ye.
“Before the takeover, SWPM had a much more diversified product portfolio. After joining, SWPM became much more focused on wood panel machinery, particularly on continuous lines. Previously we were mainly doing MO lines. 2009 was the phase that the industry started shifting from MO lines to continuous presses.”
Technical help and know-how from Dieffenbacher helped propel SWPM’s growth and develop its engineering expertise.
To date, SWPM has sold 80 continuous lines, 90% of which are installed in China. It has also completed some international projects – some lines in eastern Europe, Thailand and Mexico.
The company operates with fewer staff than its state-owned days, runs more efficiently and is experiencing increasing order inputs. “We’ve been growing on an annual basis,” Mr Ye added.
Dieffenbacher and SWPM obviously have a close working relationship.
“It is a very beneficial operation for both sides as China is a very important market for Dieffenbacher,” said Mr Ruebsam.
“We need to have a strong footprint in China to grow and have long-term success there. And that’s what the acquisition of SWPM gave to Dieffenbacher.”
When it comes to the actual press line itself, Dieffenbacher supplies the bigger 8ft wide continuous press lines from Germany to Chinese customers and SWPM focuses on the 4ft press size.
“For our 4ft continuous press lines, a big majority of the line is produced in-house by SWPM,” added Mr Ye.
“For some lines, particularly for PB and OSB lines, some critical parts and components – mainly the forming station – we import from Dieffenbacher Germany.
“This gives us a technical advantage against the local competitors. The advantage of local manufacturing in China, together with the input and engineering support and some parts from Germany creates a package offering for customers and a unique USP for SWPM.”
CHINESE WOOD-BASED PANELS MARKET
Looking at the Chinese economy, annual growth is still exceeding the majority of developed nations globally.
“The GDP in China is not as high as it was in the past,” said Mr Ruebsam.
“Nevertheless, I look at the market situation and China’s dual circulation strategy [to increase domestic demand while remaining open to international trade and investment] and the Belt & Road Initiative and how it might affect our industry. So far, the wood-based industry is not slowing down and the market situation is very good at the moment in China, with our customers having a high demand there and good prices on the market.”
Mr Ye concurred, pointing to the country’s 4-6% annual growth rate.
“Compared with 10 years ago this is much lower as the figure used to be 15-20% annual growth. But globally this is still a good number and means that the demand for furniture and wood-based panels will continue growing.”
For most of its history, China’s wood-based panels industry has focused on manufacturing with MO press lines. SWPM’s project history shows this trend – as it supplied only MO lines before 2006/07, delivering some 350 MO projects to date, mainly in China and the remainder in developing countries worldwide.
The industry shift in China to continuous lines after 2010 and accelerating after 2013, led to a big investment in MDF continuous lines, with SWPM building and delivering many of these.
“Then, since 2016, we can see very clearly that the demand for PB started to increase quickly,” Mr Ye explained. “Today, the PB market is increasing and the market for MDF is going down.
“This is the number one observation in the Chinese wood-based panels market. In the past MDF was around 80% of the market demand, now PB and MDF is 50/50. I believe this shift will continue in the coming years.
“We understand there are a couple of key drivers behind this shift from MDF to PB in the Chinese market. The number one driver is IKEA – it entered China in 1998 with a flagship store in downtown Shanghai. It not only sells furniture, home improvement and furnishings but also represents a kind of household style and culture.”
Mr Ye explained that most IKEA furniture was PB-based – the furniture company had basically pioneered this application. Beforehand, the Chinese market used solid wood and MDF.
But PB’s lighter weight and more economical nature means it is a cheaper product to use than solid wood and MDF.
“For the young generation – consumers in their 30s and the newly married couples – the consumption habits are also changing. The last generation liked to buy and use their furniture for the next 20-30 years.
“Now the young generation will maybe only keep the furniture for three to five years and then they want to redesign their homes. Furniture made from PB fits with this kind of consumption.
“At the end of the day, you have to follow the customers’ changing habits.”
Putting all those drivers together gives a clear change in direction from MDF to PB.
“In the last four years all PB customers have had a very good commercial performance, whereas for MDF it is mixed, some are making money and some are losing money. This is because the segment for MDF is harder and the increased material costs and pressure from the government – mainly environmental pressure – is making MDF profitability more difficult.”
Of course, use of alternative raw materials is a growing trend worldwide, particularly where wood raw materials are in short supply and expensive.
Dieffenbacher in Germany has considerable experience in this field worldwide and particularly in China, with customers like Wanhua Ecoboard.
These applications often see straw and wood used in the raw material mix, boosting economic use of raw materials and sustainability. Wanhua is a big customer for Dieffenbacher and the partners have worked on 10 projects together.
SWPM has recently fulfilled three orders with Wanhua, all 4ft PB lines.
Environmental compliance has been a huge issue in China in the last few years due to increased Chinese government regulations.
“This has created a trend towards larger producers using continuous press lines,” said Mr Ruebsam. “MO press producers feel the pressure of environmental regulation and maybe are more likely to close down. So, we see larger continuous lines taking bigger and more of the overall market share and smaller companies and MO lines growing less.”
The trend is also being seen in the plywood industry, with many smaller manual plywood plants already shut down by government regulations and the larger more modern plants continuing.
Mr Ye said demand for PB, OSB, and the hybrid ‘Fine OSB’ panels, would continue to be strong in the next one to two years, even with the consideration of the pandemic.
“We have a very strong pipeline of projects,” he said. “So we are optimistic for our business in the next few years.”
In 2021, SWPM recorded five new line orders in China and three further orders in the international market.
2020 saw a higher order intake, with more than nine orders. Mr Ye thinks the better 2020 performance, compared to 2021, was due to a delayed impact of the pandemic.
For 2022, SWPM estimates about eight new line orders in the Chinese market and maybe another two to three for the international market.
“China still operates a big quantity of MO lines and there are many old, inefficient and highly polluting plywood plants. Most of these plants will either be shut down by government enforcement or they will not be able to make any profits so they will have to close their business step by step. This means there are opportunities for large, modern, efficient continuous line producers.”
Mr Ruebsam concurred that phasing out of MO lines was a key factor when looking at future market and project dynamics.
“If you look how much market share MO lines have and how many boards are coming out of MO presses then you see how much future potential there is for continuous presses,” he explained.
“We see this trend from MO to continuous production continuing. International demand for wood panels is rising and prices for products like OSB and other boards are increasing.”
Mr Ye again emphasised the demographic shifts in China.
“The Chinese family used to be big, with two or three generations staying together but this is not the case anymore. The family becomes smaller and the newly married couples move out to a new house with new furniture. So, if we put all these factors together, we are very optimistic about the future of wood-based panels.”
Regarding future industry threats, Mr Ye pinpointed raw material scarcity and price.
“Raw material becomes less and less in China and some of our producer customers are nervous in some regions as it’s not easy to secure supply of raw wood and the purchasing price is becoming higher.”
While some panel producers – such as Wanhua Ecoboard – are pioneering alternative and locally available raw materials, the vast majority are still focused solely on wood.
Mr Ruebsam believes the future will see a mixture of solutions – increased planting of fast-growing tree species, increased use of alternative materials, use of waste wood and further innovation and efficiencies in manufacturing.
“About 50% of the raw material used by the panel industry in China is imported,” he said. “Efficiency will become more important and the wood industry will be driven to innovate.” He said digital solutions like Dieffenbacher’s Evoris platform, which helps give producers deep insights into their manufacturing processes and boost efficiencies, would become more important for producers.
Dieffenbacher’s focus, he added, was by striving to be the most innovative technology supplier and thus helping customers to be more efficient and competitive in the market place.
“You make money when your plant is running efficiently. Every delay in production costs you money. Part of our success in China is having a strong local footprint, including SWPM. All these factors combined have helped give Dieffenbacher success in China during the last years.”
He described China as the “most innovative” market in the global wood-based panels industry, with trends being the result of development working together with customers. “It’s their drive and readiness for innovation that create new trends.”
Mr Ye said SWPM was very focused to help customers increase their daily output.
“We put a lot of effort with our close communications with the customers and their plant managers and engineers, doing internal research on how to remove the bottlenecks and how to improve our equipment to improve that daily output,” he said.
PROJECTS
Mr Ruebsam said most of Dieffenbacher Germany’s projects in China that are currently in the pipeline are OSB or Fine OSB plants, product areas which Dieffenbacher has a lot of experience in, with many case studies in the country.
“I can confirm this is a trend and is in high demand, with good prices to be achieved in the market at the moment for OSB,” he added.
OSB POTENTIAL
SWPM does not have so great a focus in OSB, but sees future potential in the product and also in short cycle lamination, the latter for which the company is improving its designs and competitiveness.
In terms of current projects, Mr Ye highlighted the Chengde Sengxi Super PB project in Chengde City, Hebei province.
The project, planned to have its first board on May 1, has seen SWPM supply four forming heads, a 38.9m x 4.5ft press, raw board handling and inter-storage. Production capacity is 1,000m3 per day.
Previous reference projects for Dieffenbacher 8ft wide lines in China include Ganzhou Aigesen in Ganzhou (2017) with a 23.4m long CPS line for PB production and a 900m3 capacity per day; a similar capacity straw/PB plant for Wanhua Ecoboard in Chenzhou (2017); and a 970m3 capacity per day PB plant – Danzhou Huashengxin – in Danzhou with a comprehensive scope of supply.
SWPM’s international projects have included the Big Star MDF project in Algeria – North Africa’s first continuous wood-based panel plant – with its first board already produced.
For a particleboard project for Ghamoud in Algeria, SWPM is currently working on the final stages of foundation plant construction, with installation to start soon.