Tolko Industries owns 75% of Meadow Lake OSB Ltd Partnership and manages its new mill in central Saskatchewan. It is a rather greenfield operation but a nearby pulp mill and sawmill have used the resource there for a number of years.
The OSB market has soared since late spring and the company managed to trim three weeks off the new mill’s start up date to try to get some product on the market promptly.
A 400,000ft2 sheet steel building houses the mill that started just 470 days after ground-breaking. Company employees and contractors joined forces to produce an effective planning and construction team.
Eventual production goal for the Can$200m (US$146.3m) mill is 600 million ft2, 3/8in basis.
Manager Ricardo Hillmann said: “This has been designed as a commodity plant. In the beginning we will be running 7/16in as the main product, although we can go down to 1/4in and up to more than 1in thicknesses.
The layout was designed to accommodate a possible second line to produce value-added speciality products. This initial line’s goal is high production of high quality standard products at minimum cost.
The new mill is based on proven technology. Tolko has used lessons learned from its big OSB mill located in High Prairie, Alberta.
Tolko has its own wood supply area with logging and hauling contracted, but will buy about 20% of its supply from private owners and nearby farmers. Eighty per cent of the raw material will be aspen with the balance in various pine species. The conifers will be handled in 8ft lengths.
Average log size is 71/2in with a minimum 3in top. The system will handle up to 20in diameter but this limit will not be reached. There is a nine-month logging season but most of the wood will arrive in the winter with up to 200 truckloads daily. Estimated annual consumption is 900,000m3.
The logs are trucked in through a scaling station to the decking area. The log yard is subcontracted using mobile equipment.
A front end loader feeds two conditioning ponds that will hold 16ft logs for eight hours of production. Pond temperature is between 40°C and 60°C. A separate feeding system handles 8ft logs, lengths that will make up about 20% of the raw material supply.
Two CAE Fuji King tumbling debarkers were chosen to handle the quite varied logs that can range from straight to knotty, dry or frozen. These can simultaneously and efficiently handle diameters of 2in and greater and lengths from 24in and up.
Barking plates are arranged to rock the logs as the rotor turns. Rotation speeds and the outlet gate regulate residence time to prevent over or under debarking.
A twin Tanguay PL460 crane installation assures continuous feeding to the two CAE 28/81 stranders producing targeted strands of 1×51/2in. Output of those goes to 600m3 wet bins. These provide nearly an hour of strands for the line. The cranes, hard-wired to computers, remotely control the head end of the operation.
The two energy units by CTS Energy, Marietta, Georgia, burn mill residues during the summer, but purchased fuel will be necessary during the winter. Residuals from debarking and bucking and from other areas of the plant are stored in bins and metered into the units that supply hot oil heat to the dryers, hot press, log conditioning ponds and, in the winter, to the plant building.
A West Salem Machinery hog processes residues. The 2,000m3 of ash produced annually will be land-filled. These energy units furnish 300oC heat to the twin Büttner 24ft by 80ft single pass rotary dryers as well as maintaining the mill temperature at 20°C, even in -45°C outside temperature. The outlet gas passes through an electrostatic precipitator and the dried flakes are then directed to 600m3 dry bins.
UMA did the detailed design work on all the chain conveyors and flake transportation systems in addition to its principal job of designing the entire plant.
The plant is self-sufficient for fuel in the summer, but requires extra fuel in the winter. The mill has about 26,000 connected horsepower and requires 16MW of incoming electrical power.
The strands are metered into the blender where they receive 3% MDI resin and 1.5% wax. Borden and Tembec supply resins.
Dieffenbacher took over at the forming line that includes metal detection, four forming heads, trim and cut-off saws and press feeder. The surface layer is parallel and the core is cross-oriented.
The huge 12-opening 12ftx24ft press has perforated platens with 1/4in holes providing steam injection to the mat. This feature, not yet in operation during our visit, enables pressing thicker boards with shorter press times.
The cauls impress serrations on one board face to provide a non-slip surface for workers when installing the OSB as roof sheathing.
Press emissions rise to a large hood from where an air suction system moves them through cyclones into baghouses.
Board density is 625kg/m3 with 1,000ft2 of board produced from 1.6m3 of wood. Although the plant can produce thicknesses from 1/4in to more than 1in, 4ftx8ftx7/16in will be the main product.
The glassed-in control room is located above and to the side of the main line. From here, operators and their computers control the forming line, press, dryers, and EFP.
Workers servicing the line from the formers to the press outfeed wear respirators for safety. Production workers work 12-hour shifts with four shifts allowing continuous operation.
The pressed boards offbear to the Globe finishing line that has a two-pass saw system that can cut boards from full 8ftx24ft down to 3ftx6ft. A paint booth and twin Samuel Acme strappers end the line.
The warehouse area beside the saws will hold 31/2 days’ production when the plant reaches full capacity. Both trucks and rail cars can be loaded inside the building as well as outside.
North America and the continent’s central north will be the mill’s main market. About 80% of the mill’s output will be rail shipped and the balance trucked.
Environmental considerations had high priority during mill planning. A high earth bank surrounds the plant and no effluents leave the site. There is a storm water pond which will contain all but 10-year events. Sewage lagoons and 1.25 million gallons of fire pond storage are on the site.
In case of an energy system shutdown, propane can provide heat for the mill with a small vertical standby boiler, but not for operations. Building temperature can be kept at 20°C during the cold winters.
For efficiency, all the offices are in one area. The laboratory adjoins the control room which, in turn, overlooks the forming and pressing line.
Others in the team include production manager Cedric Magic, technical manager Randy Thomas, woodlands manager Dave Knight, maintenance manager Pablo Carbajal, human relations manager Jim Hurd and controller Roger Cook.
Tolko Industries’ general manager for OSB and paper is Rick Huff, based in the company’s head office in Vernon, British Columbia.
Project safety supervisor Bob Callahan is particularly proud of the 850,000 man-hours that have gone into construction and start-up without a single lost-time accident.
Wabi was the general contractor on the project with Pyramid providing the electrical work. Hinz Automation did the electrical engineering and programming work. UMA Engineering Ltd of Vancouver, British Columbia carried the project from the preliminary feasibility study through to detailed engineering.
Allied Blower, Surrey, BC, did all the extraction systems. Grecon handled spark detection as well as the quality system including thickness, weight, and blow detection. The mill has six bag houses.
Although experienced managers and supervisors were recruited from the industry, operators and other hourly workers were hired locally. Management interviewed about 1,500 candidates for the 121 positions. “We did quite a lot of work with the aboriginal community, 30% of our operational group are aboriginese. Performance Associates was contracted to train them. They wrote technical manuals for the various responsibilities. Management individuals also received training,said Mr Hillmann.
APA is the product inspection agency.
With Tolko holding 75% investment in the mill, the balance is owned by Crown Investments Corp, Meadow Lake Tribal Council, and Northwest Communities Wood Products. The organisation is a limited partnership.
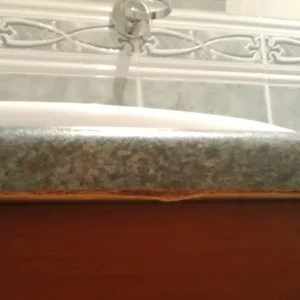