The original Maier company celebrated its 70th anniversary in 2002, having started as a manufacturer of turbines.
The company moved into wood chippers, flakers and hammermills in the 1950s and, while that is still the core of the business, the Maier company has changed a lot since then.
The real turning point came in 1996, when Robert Loth bought the company and took a completely new look at the way it was doing business. For years, it had been selling single machines, which were mainly delivered to the major contractors as part of the supply package for a complete panel production line. And its marketing approach was fixed on the particleboard industry. Today, things are rather different.
“The first thing I did on taking over the business was to switch the sales effort towards the panel mills as direct customers,says Mr Loth, speaking at his factory in Bielefeld, not far from Hannover. “This put us more in touch with what was happening at the clients’ factories and with what their needs really were.”
Even if Maier does supply through a main contractor, or OEM, today, Mr Loth says the company knows the final client and what he really needs. “This means we can provide a professional after-sales service including information about our developments which, for example, reduce the running costs or increase the quality of flakes and so on,he says.
“What we would like to emphasise is that the customer should treat the chipper lines, the drum chipper, the flaker, the screen and so on up to the dryer, and the mills after the dryer, as a separate package employing the expertise of the machinery maker. This special know-how of Maier is of benefit to the client and the main contractor. Interfaces today are easy to define and Maier is used to offering a guarantee for this. It is far better for any panel factory to split the whole package into specialist areas.”
Of course Maier still makes a wide range of machines for size reduction and it has made many changes to their designs and method of operation in recent years. The emphasis today, though, is on supplying those machines as part of a ‘frontend package’ to the mills.
As a result of being in touch with its clients’ needs, says Mr Loth, Maier developed technologies such as the 60-knife ring flaker, then high-speed flaking. It moved on to a lot of development of the drum chipper and is now in the area of screening.
All the developments of the chippers, flakers and hammermills have been centred on the quality of chip, flake or strand produced as well as on increasing the efficiency of the process, claims Mr Loth.
The latest major development for Maier is a new trans-Atlantic marketing agreement which it has entered into with Acrowood Corp of the US. This is a ‘two-way street’ arrangement in which Maier offers Acrowood’s products in Europe, while Acrowood offers Maier’s in Canada and Mexico.
The US company brings screening systems, disc chippers and a chip cracker, all of which will give Maier access to the pulp and paper industry.
“Maier is focused on screening fines and oversize material, but the Acrowood screens also select a chip size for the digester in pulp and paper mills,explains Mr Loth. “Thus the agreement also gives us additional possibilities to enter the MDF industry. With access to the Acrowood technology, we don’t have to start from scratch in this area. Also, Acrowood has a strong presence in the OSB industry.
“We successfully developed two-stage flaking for OSB two years ago but didn’t have the equipment to screen the strands until now. Acrowood’s technology adds this and so we can now offer flaking and screening right through to the wet strand silo.”
In many OSB mills, the strander can become the bottleneck as line capacities increase and it is expensive and really ‘overkill’ to install a second strander, explains Mr Loth.
“Our two-stage flaking lowers the cost and increases the range of sizes of wood raw material which can be used – small wood, recycled, crooked, whatever,he says. The two stages are a drum chipper then a flaker. “It is an ideal system for all cheap kinds of wood because they can go directly to the drum chipper or to the flaker,he adds.
A new product from Maier is the Heavy Particle Separator (SGA), showcased at Ligna in Hannover last May. This includes non-ferrous separation because more recycled wood is going through the knife ring flaker and a lot of aluminium and other non-ferrous metals can be contained in it.
“You normally have a big non-ferrous separator in the line after the screens and the efficiency of these big machines is not always the best because they are running large quantities, so we have installed the SGA in front of the knife ring flaker or mill,says Mr Loth. “If you have a six to eight tonne recycling throughput, you can use the SGA, or if you have a higher volume, you can use it as an additional station.”
The SGA works by having an infeed chute with detectors below, which work by using an electric field and automatically operate one of three or four flaps to reject unwanted material with minimal loss of wood. The system can be retro-fitted to older particle separators or adapted to fit flakers and mills made by other manufacturers where the air does not pass through the rotor as it does in Maier machines.
Mr Loth points out that most of his company’s major developments have come about because of the needs of customers, using two contracts in Germany to illustrate his point.
For Glunz at Meppen, Maier refurbished a 1989 chipper by another supplier and also supplied the infeed lines, including long log and slab conveyors, a vibration feeder and electrical controls. All this was integrated with existing conveyors as well, in an upgrade of the existing line.
For Kronotex’s mill in Wittstock in Germany, Maier supplied a long log flaker and vibration conveyor, as well as a conveyor for bought-in chips. Then came the drum chipper and a silo to coordinate with the existing silos. The job included all electrical equipment and was carried out as a turnkey contract by Maier.
But this company is setting its sights much further afield than just Europe. In September 2003, it received an order from Fuzhou Particleboard, which was adding a new particleboard line to its existing one.
“We offered four knife ring flakers with a knife ring for normal flakes of 0.5-0.7mm and another set of KFRs for 0.25-0.35mm for homogenous board, so the customer can switch from homogenous to standard board,explains Mr Loth.
The contract also includes a Maier automatic grinding machine in which the operator enters the specific number of the ring and the grinder automatically knows if it is a 0.5mm or 0.25mm ring.
This is Maier’s first major contract in China; several others are under discussion.
Maier has an agent in Beijing, Beijing Europe-China S&T Trade Co Ltd, run by Stephan Dong. It also represents other German companies which together give Mr Dong’s company coverage of the front end, the middle and the finishing end of panel making lines.
He also has good connections with clients and universities in China.
In South East Asia, Maier won the order for Vanachai of Thailand’s new particleboard line to supply flaking and milling, and a dumping chain conveyor followed by a vibration conveyor before the drum chipper, and an additional slabs conveyor.
The MPM mill supplied for this contract for surface layer material has new grinding tracks which can be combined to adjust the fineness of the material.
“Vanachai had high demands on the surface quality of its board and this gave the impetus to the development of these grinding tracks,explains Mr Loth, using the point to underline one of his central philosophies for Maier.
“We are changing ourselves as quickly as the market is changing, to increase our ability to respond quickly.”
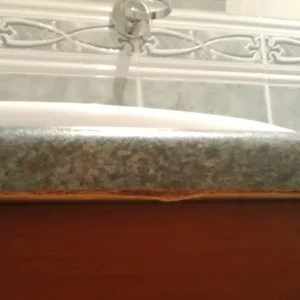