Many companies involved in the MDF business in China are now realizing the need to produce a high-quality panel that will meet the kind of standards expected in western Europe, for example.
Asia Dekor Industries (Shenzhen) Co Ltd, headquartered in Shenzhen City in China’s southern province of Guangdong, has been making overlaid panels to those high standards for some years.
In fact, the company claims to be the largest manufacturer and distributor of laminate flooring in China and the Power Dekor brand has been ranked by the China Industrial Information Issuing Centre as the best selling laminated floor product in China for five consecutive years from 1998 to 2003.
The company is part of Asia Dekor Holdings Ltd, a truly international company in both structure and manufacturing policy. Asia Dekor Holdings Ltd is incorporated in Bermuda and its ordinary shares are listed on the main board of Singapore Exchange Securities Trading Ltd.
The group has a total of three factories in Guangdong and started out with one line for tongue-and-grooving (T&G) flooring in Shenzhen in 1997. Two years later, a second factory was built, also in Shenzhen, with two paper impregnation lines, one by Vits of Germany and the other of local manufacture, and two laminating lines, one by Dieffenbacher and the other by Wemhöner, again both German companies.
The second factory also added two T&G lines by Torwegge to replace the first machining line. The first factory was also closed and the equipment moved to another factory closer to the second one.
In order to achieve the high quality of flooring on which the company based its sales message, Asia Dekor imported high density fibreboard (HDF) from European manufacturers such as Fantoni, Egger, Kronotex and Kaindl.
The panels imported are 2070mm x 2610mm because of the size of the printed decor paper sheets, which are also mainly imported from Europe. European suppliers of this paper are Schattdecor, Interprint, Mepa and others, as well as Schattdecor’s printing works in Shanghai.
Once the second factory was established, Asia Dekor also started to produce veneerfaced flooring on an MDF base, as well as skirting to match the flooring.
“Sales of laminate flooring in China are growing at 20-30% a year on the domestic market,said Mr Tong Guang Zhou, mechanical engineer and vice general manager with the company. He is the man responsible for the development of Asia Dekor’s latest, ambitious project, as well as for its existing flooring factories.
That latest project is the construction of a new state-of-the-art continuous HDF production line.
“Our production of laminate flooring in 2002 was six million m2 and in 2003 it was 10 million m2, with about five to ten per cent exported to South Asia, the Middle East, Australia and South America,said Mr Tong.
“In China we go for the top end of the market with the best quality in the country because we are using the highest level technology, as used in Europe, and our raw material is the same as Europe. So is the management of our company,he added.
“We actually started out selling laminate flooring imported from Europe in 1995 but the price has gone down a lot already on the Chinese market, with a lot more competitors. We need to have the best quality and the best service but also a competitive price.
“Imported board is expensive so we decided it was time to make our own board.We have those two laminating lines which, at full capacity, can produce 12 to 14 million m2 of laminate flooring a year, equivalent to 100- 120,000m3 of panel, so we already had the basis for a good-sized MDF/HDF factory.”
So the company decided to invest around US$36m in a 200,000m3 a year line which would provide 50-60% of its production for Asia Dekor’s own laminate flooring consumption and 40-50% for sale as raw board.
The first requirement for such a large production line is an adequate supply of wood and the warm climate of Guangzhou, together with the founding of eucalyptus plantations in the province up to 10 years ago, means that wood supply is plentiful. There is also availability of pine.
“I see no problem with raw material and we have already discussed with the local government renting land for plantations in the next two or three years, so our wood supply will increase,said Mr Tong.
Actually, of course, the first requirement for a factory of this size is scheduled industrial land. That Asia Dekor found in Heyuan City in the north of Guangdong Province, about 200km from its existing factories in Shenzhen.
It is a long and narrow strip of land sandwiched between the main road at the front and the river at the back. It is opposite the railway station on the Beijing to Hong Kong main line, which may provide opportunities for transport when the factory is up and running. At the time of purchase the land also sloped, with a fall in height of 14m from one end to the other.
“We first had to build what we call ‘the great wall’ alongside the river for nearly one kilometre, as a retaining wall to stop our land slipping into the river,recalled Mr Tong. “The land was also undulating and before we came, it was flattened by removing the tops of the high parts and using that material to fill the hollows. This meant that the land was relatively soft in the made-up areas and hard on the former high points. Thus we needed different foundations in different areas of the site – including along the length of the new continuous press.”
The other major requirement for a project of this size – a strong and reliable electricity supply – was no problem.
“Two years ago this was not the case and electricity supply would have been a problem, but the local government has supported industrial development in the area,said Mr Tong. “It also appreciates the help that the tree plantations give to the local farmers and has given a lot of help and support to our company.”
However, Heyuan is in a beautiful area, one that is popular with tourists. The river supplies the drinking water to Shenzhen and Hong Kong and there is a lake/reservoir nearby so the government would not encourage any polluting industries.
Asia Dekor’s new MDF/HDF line has a waste water settling and treatment plant which will enable it to recycle a lot of its process water, while solid waste will be removed by a specialist contractor for treatment, or burnt in the energy plant together with bark, sanding dust and other wood residues.
Groundwork started on March 26, 2003, but progress was then effectively halted until May by the rainy season. At the time of my visit in early March this year, all major machinery was installed and under final assembly and electrical installation for the main production line, while some parts, such as the resin plant, were still under construction; the latter being surrounded with bamboo scaffolding. The foundations for the boiler house and woodyard were also awaiting completion of ‘the great wall’.
It was expected that the first board would be produced by mid- to end-May this year.AThe total area of the new factory is 160,000m2 and the layout is very typical of a European MDF mill.
Asia Dekor appointed five main contractors for the project: Dieffenbacher was awarded the main contract for the CPS continuous press and associated line; Andritz the woodyard and refiner; Vyncke of Belgium the energy plant, Anthon of Germany the cut-to-size; and Imeas of Italy the sanding line.
The scope of supply of Dieffenbacher actually covered from the Schenkmann & Piel dryer to the Scheuch of Austriadesigned complete dust filtration system, gluing, forming, pre-press, main press and a sub-contract to Kontra for cooling and panel handling after the press.
The cyclone tower, still under construction, will be the tallest building in the city when it is finished, topping out at 67m.
Debarking will be carried out by a locally- made debarking drum. Chipping is by Andritz Oy of Finland and the Andritz of Austria refiner is a 54/60in unit, to be started at 54in as Asia Dekor will build up its capacity over a period of time; it anticipates producing 75-80% in its first year.
There are two, 15m-high, concrete chip silos and chips will be transported underground to a bucket elevator to lift them up to the chip screen by Andritz Oy. Behind the silos, the Vyncke energy system was under construction.
The dryer tube is 2.6m in diameter and will transport 30 bone dry tons per hour (bdtph) of fibre across the site. Forming is mechanical with a scalper located very close to the Schenck/Dieffenbacher weigh-scale for a rapid reaction time. An Imal bottom belt dampening unit precedes the former and there is another before the hot press to damp the top surface of the mat.
“The pre-press is a new generation which does not have an endless belt, but one which we can joint on site and this makes belt changing much easier,said Mr Tong.
The Dieffenbacher CPS press has 24 frames and is 31.5m long and 2.65m (net) wide. It is extendable to 35.5m. The master panel ex-press will be 6.3m x 2.65m.
A combined quality control unit by GreCon has five thickness and 12 blow detector heads.
After cooling, the boards will be handled by an automatic robot stacking system byKontra, employing a rail-based system and concrete bearers. There is capacity for eight days’ production here.
To meet local safety regulations, unusually the whole storage area is surrounded by a brick fire wall. Asia Dekor already has equipment from Firefly of Sweden to protect its laminate flooring factories from the outbreak of fire and also awarded it the contract for the new continuous line.
As of March, Asia Dekor had few experienced staff to operate the new line, admitted Mr Tong. However, he was in contact with some experienced Chinese personnel and was also considering employing some European technicians on short-term contracts to get the line under way. He anticipates that 120 staff will be needed to run the entire Heyuan operation.
Its sales and distribution network is already well established.
“We have two completely separate systems operating in the company: production and marketing and the two are totally separate,said Mr Tong. “The headquarters for all the company’s sales operations are located in Shanghai and the factories manufacture to order from there.We store all the various kinds of MDF and decor paper at the factory and when we get an order from Shanghai we decide which kind of production to schedule.
“We have 700 shops throughout China selling our flooring products.”
Asia Dekor has joined forces with another major MDF producer in China, Dare Wood (WBPI June/July 2003, p14) to achieve this coverage.
However, there is more to Asia Dekor than just laminate flooring, especially with the new Heyuan line coming on stream and able to offer raw board.
But that is still not the end of the story for this ambitious company. Plans are already foot to build a particleboard line near Huizhou, about half way between Heyuan and the flooring factories in Shenzhen. This will be another continuous line with a similar capacity to Heyuan – about 200,000m3 a year.
The company is already laminating some furniture panels in its Shenzhen facilities, using particleboard imported from Europe.
“Guangdong accounts for about 80% of Chinese furniture exports, to Europe and North America; Donguan, about 150km from here, has a lot of furniture production and one factory I know there is importing 450 containers a year of particleboard from Thailand.
“Particleboard is cheaper than MDF but the transport cost is high. If we make our own board, we can get the quality we want and save those transport costs,said Mr Tong.
Further possible developments for Asia Dekor include the construction of a laminating factory behind the new MDF line at Heyuan, on the same site.
“There are four important points for a factory: resources, money, technology and marketing,asserted Mr Tong. “We have all those.
“We aim to be a ‘show factory’ and we told all our machinery tenderers that. They will be welcome to bring their customers here to see our factory as a reference plant. We will be the best in China for MDF.”
Mr Tong is even talking to a Japanese landscaping company about making the outside of his factory look as good as the inside and helping it to ‘blend in’ as far as possible in a popular tourist area.
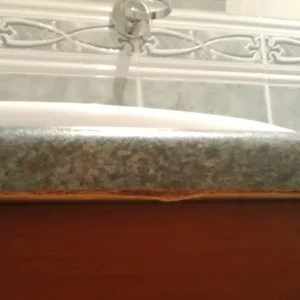