Acivil engineer called Athanasios Sarantis entered the particleboard business on his own account in 1977 by building his first production line in a small village outside Alexandropoulis on the Aegean coast in the north east corner of Greece, close to the Turkish border. The company was called Akritas SA.
The main contractor for the line was German company Bison, with another German company, Dieffenbacher, supplying the press. Full production on this 11m single-opening press line began in 1980 and the nameplate capacity was 150m3 per day. The product was, and is today, trade marked Akripan.
In a sign of the future direction for the company, Mr Sarantis bought his first short-cycle press line in 1982. This was a line from Siempelkamp, also of Germany of course.
In 1986, Akritas took up another form of value-adding by installing a lay-up and press line for veneering its own particleboard, and bought-in MDF, panels. The sliced veneer was purchased from specialist suppliers and jointed and pressed at the Alexandropoulis factory, which today has 40,000m2 of production facilities under cover, on a substantial site. Jointing is by Rückle machinery and pressing is by Italpresse. Akritas offers 10 species of veneer, including reconstituted. Sanding of veneered boards is by Imeas of Italy.
Sales and marketing operations expanded over the years with regional offices and two distribution centres in Greece: in Athens and in Thessaloniki.
Further value-adding facilities came in 1997 with the purchase of two postforming lines – one conventional IDM line for high pressure laminate (HPL) and a Homag line for direct postforming of melamine foils and low pressure laminate (LPL).
In a major step for Akritas SA, the company became listed on the Athens stock exchange in April 2000, selling 25% of its shares. This was subsequently reduce to 22% in a buy-back of some shares by the Sarantis family.
Growth in value-adding continued apace with the purchase of a Wemhöner short-cycle press line in 2001, giving Akritas a total of two such lines.
Investments made after the company’s entry to the stock market continued and so 2002 saw the purchase of a new particleboard production line to replace the original Bison line (which was then sold to Russia).
This line was supplied by Dieffenbacher as the main contractor and employed a CPS continuous press of 25m long and 2.2m effective width. Capacity of this line was 1,000m3/day and it was in three-shift operation by end-January 2003.
Forming and pressing was by Dieffenbacher with chipping by Maier (recently absorbed by Dieffenbacher but at the time independent), sifting came from Pal, glue blenders from Imal, both of Italy and dryer from Büttner, Germany.
The major part of the resin supply for Akritas comes from the sole Greek supplier Hadjilucas, which is a licensee of resin technology supplier Chimar Hellas of Thessaloniki. Chimar also supplies ongoing support to Akritas, as it has done since the 1980s. Some additional resin supply comes over the border from Turkey.
Today, theoretical raw particleboard capacity at Alexandropoulis is around 270,000m3, based on producing 2.2m width board; however, most production is 1.83m, giving a lower factual capacity.
Continuing its investment programme, Akritas in 2004 bought a second Wemhöner melamine foil short-cycle press line – this time a double press that can take two panels end-to-end per charge.
The start-up of this line brought the company to an impressive figure of adding value to 90% of its particleboard production.
“With the veneering production as well, we laminate almost 100%, although we do still have some customers for raw particle- board,said Polychronis Dardabounis, strategic development manager with Akritas. He joined the company in 1995.
“The great thing was that we were now able to sell all our production, which was good quality and well-accepted on the market, especially after we installed the new line. We gained a big market share all over Greece as well as exporting to Cyprus, Turkey, Bulgaria, Albania, Serbia and Croatia.”
But growth did not end there. In 2008, Akritas bought its second direct postforming line to increase its capacity at Alexandropoulis.
In the same year, the company bought an old factory and warehouse at Chirpan, in Bulgaria, and is now installing a secondhand Siempelkamp short-cycle press line there. From 2010 this company is known as Akritas Bulgaria.
“Initially at least, we will ship our particleboard from here to that facility and add value to it there. We do not produce raw board there at this time,said Mr Dardabounis.
When the company built its first particleboard line at Alexandropoulis it was because there was a good availability of wood raw material from a large local forest. However, this is now an internationally protected area as a bird sanctuary. Over the years, Akritas has increasingly relied on imported wood from Bulgaria (the border is only 90km away) and now obtains the majority of its supplies from there, through its subsidiary, although 25-30% still comes from the Greek forest service.
“Bulgaria has a very good state-owned forestry department and, like Greece, has very good policies on sustainability and a good forest management system,said Mr Dardabounis, who himself has a strong background in forestry and so knows what he is talking about.
Particleboard production at Akritas is currently to E1 emissions standard, but the company is a member of the European Panel Federation (EPF) and plans to produce to the EPF-S standard soon, which equates to approximately ‘E0.5’. Density is normally 670kg/m3 and thicknesses produced are 6 to 40mm.
Akritas manufactures semi-finished furniture components, such as kitchen cupboard doors and worktops, under the ‘Polytheta’ trademark. It also makes ‘Artika’, a special range of products and direct postformed melamine doors, and ‘Evropanel’ lightweight honeycomb-cored panels. ‘Akripan’ is the trademark name of its raw particleboard.
“We produce to mechanical and other technical levels which are well above the requirements of any official standards and we are thus able to obtain a better price for our products – the name ‘Akritas’ means a lot in our markets,said Mr Dardabounis proudly.
The company is also economically important, being located in a remote area of Greece and employing some 300 local people as well as creating at least 500 outsourced jobs.
Market conditions in 2009 were no better for Akritas – or Greece – than for anybody else. The company saw the market drop by 20-25% over 2008 and expects much the same market conditions for 2010. Payment is a particular problem in Greece, with customers habitually taking very long credit without the agreement of the supplier.
A further uncertainty was introduced to the Greek market in December 2009 with the proposed takeover of Akritas’ rival panel maker, Shelman, by Greek wood products company Alfa Wood. This then received approval by the Hellenic Competition Authorities on January 11.
However, Mr Dardabounis is not too concerned by this development and believes that the quality of Akritas’ production, and the loyalty of its customers, ensures it a healthy future, although prices may come under some pressure, at least in the short term.
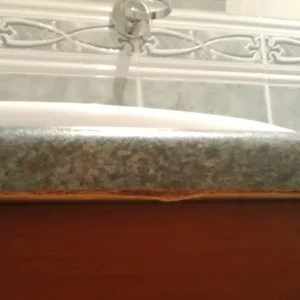