Technocell Dekor, a name well known to anyone in the panel industry involved in adding value to panel surfaces, claims to be the world leader in the production of decorative laminating papers.
The company is part of the Felix Schoeller group and possesses eight of that group’s 10 paper machines. Three of these are located at Technocell Dekor’s main factory in Günzach, near Munich in the south of Germany. Other paper mills are located in Osnabrück, Penig and Neustadt in Germany and Drummondville in Canada.
Dr Mathias Rump, vice president of Technology for Technocell Dekor, outlined the structure of the whole decor market and where his company fits in.
“It is a long value-adding chain and very complex, from base paper to finished laminate,he said. “Our product covers all areas of design – we produce print base papers whose composition can be adjusted to anything you may require. That base paper is then printed, treated, pressed onto panels and those panels are then cut to size and perhaps shaped.
“Therefore it is necessary for us to take responsibility throughout the whole processing chain in order to arrive at good quality products and a stable market. It would be dreadful to foul up the market with poor quality products that don’t perform! Holding the leading position in the market means we must have a sense of responsibility to our business partners.”
To that end, Technocell has relationships with printers, woodworkers, panel producers and furniture makers, he explained.
“We try to ‘de-mystify’ the process and make all the steps that define quality understandable and to make that quality measurable,said Dr Rump, who went on to explain that the company is also trying to address the problems of terminology in the industry.
“For instance, the word ‘overlay’ means different things to different people. In the US it means any kind of surface – paper, vinyl or whatever; in Europe it mainly means the clear surface layers such as those applied to laminate flooring. Therefore we are trying to establish a uniform terminology in the material we publish and we’re trying to get a two-way exchange in communication,he said.
To disseminate its considerable knowledge, Technocell holds periodical seminars, or forums, and publishes the papers. It has also published a book called The analysis of decor paper: A compendium of quality parameters and test methods, as part of its contribution to that de-mistifying process.
The latter book, to give just one example, explains the Taber test with a definition, explanation including its relevance, and the method for carrying out the test.
“We see a trend towards integration of the value-adding steps – for example backward integration of panel producers into impregnation,said Dr Rump. “We also see a trend for printers to forward integrate into lacquering their foils on the printing line – the technology is there and varnishes have developed to become more usable in the printing process.”
Hans-Christoph Gallenkamp, senior vice-president of Technocell Dekor and a member of the Schoeller family, added: “Our task is to make the whole process more transparent and to supply our knowledge on to the value adding chain. It is not only knowing paper making but understanding that whole chain – a partnership approach with the customer and his value chain.”
Capacities of the eight Technocell decor machines range from 11,000 to 40,000 tonnes a year and they produce papers for making high pressure laminate (HPL), low pressure laminate (LPL) and continuous pressure laminate (CPL), paper foils, print base, saturating base and machine glazed papers. The three Günzach machines all have a 2.25m working width.
Drummondville is currently an exception to the other locations in that it produces pre-impregnated papers, but that is because it is a joint venture with the German Kunz Group which owns the panel maker Uniboard, the exclusive customer of Drummondville.
The company has three different kinds of paper machines, including a ‘top wire’ machine to produce symmetrical white papers.
“This is the only machine of its type in the world and it offers the advantage that the paper does not have a ‘top’ and a ‘bottom’ face but can be used either way up, avoiding the need for laminators to have to turn a pallet of paper over during their production cycle,explained Mr Gallenkamp.
The five hectare Günzach site, situated in a beautiful region of Bavaria at the base of the Alps, employs 232 people on its three paper making lines. One line makes white to brown pastel colour base papers, while the second makes backing papers and edgebanding and the third makes a full range of base colours, from white throughout to intense black.
The site gained ISO 9001 certification in 1994 and EMAS/ISO14001 in 1996. It was one of the first paper mills in the industry to gain the environmental 14001 certificate, driven partly by the fact that it is a very compact site which had nowhere to store waste and therefore every reason to avoid creating it in the first place.
In 1999, the company started producing paper from regenerated paper by recycling waste from its own production into backing paper.
A tour of the factory begins in the colour management laboratory, where the recipes are formulated in a process which simulates real paper production from pulp and the other basic ingredients.
The sample disc of paper so produced can be laminated to a piece of particleboard and colour-checked against a master sample. All data is stored in a computer for repeatability.
At the start of the production line, pulp is stored in bales of sheets, using short fibre from eucalyptus and longer pine fibre. The two types are mixed according to the required final paper properties.
The pulp sheets, together with Titanium oxide, fillers and dyes are mixed with water in the pulper in a swirling action which ensures good mixing. From the pulper, the mix passes to the refiner to equilibrate fibre length and on to a reservoir where other additives such as wet strength agents are added.
The mixture then passes to the machine vat where final online colour checking is carried out just before the paper machine.
A form of hydrocyclone then separates out any dirt or lumps from the mixture and several screens remove any small contaminants before the mixture passes to the machine head box.
The mixture, which is now 99% water, is sprayed onto an endless ‘wire’ and most of the water is removed by a combination of draining and a vacuum under the paper web. This leaves a higher concentration of fillers and fines in the top layer of the web and so this is equilibrated by the Dandy Roll.
A felt now picks up the web and passes it through a nip roller press. The web then enters the dryer at 50-60% moisture content where it passes over a series of heated cylinders, followed by cooling cylinders, the application of steam to adjust the moisture content, and passage through a three-nip Küsters calender press.
The calendering leads to compression of the outer layers for smoothing of the surface, while retaining the springiness of the core of the paper so that it remains permeable to resins.
The final paper product goes to a jumbo reel and is then edge-trimmed and cut to the customer’s required length on a rewinder system.
Another quality management lab checks the final product for all parameters such as ash content, weight, pH as well as colour, and all data is stored on a server to give traceability and repeatability.
Technocell’s quality standards are undoubtedly high in order to satisfy the very demanding decor paper market but Günzach has another, literally high, claim to fame: it is the highest decor paper mill in Europe, standing at 800m above sea level in beautiful Alpine scenery. This at first surprising location is a legacy from its original function of making papers to wrap locally produced butter and cheese. Technocell has come a long way from that speciality to its current specialist décor paper production.
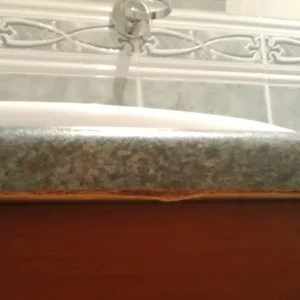