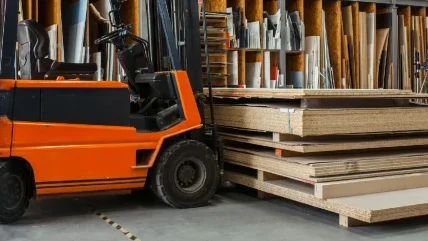
For the wood-based panels industry and woodworking enterprises, the brand names IMA and Schelling have been long-established in their fields of processing solutions. Schelling was founded in 1917 and IMA in 1951.
The former’s expertise is centred on the woodworking side: edgebanding, CNC machining and drilling solutions for example, and it is also a leading supplier of batch-size- 1 work cells for a digital, fully automated networked production, together with handling/conveyor systems.
Schelling has traditionally been focused on cutting technology for the wood-based panels, metals and plastics manufacturing, finishing and distribution sectors.
The companies merged in 2015 to form IMA Schelling Group, with the following years seeing the group companies being consolidated into the new structure and in 2019 the creation of four business units under the Group brand: Woodworking, Board, Precision and Consulting.
The goal is simply to provide expertise in developing solutions for the wood, metal and plastic processing industries.
The different divisions are now working very closely together at their main factory locations of Schwarzach in Austria, Luebbecke in northern Germany and at Sroda Wielkopolska in Poland, the latter of which is the subject of a large current investment to expand capacity in the automation/handling segment.
The Board division is on a journey of diversification and expansion, one that started before the merger.
I spoke to Stefan Hinterholzer, director of the Board business unit and who has been with IMA Schelling since 1993.
Mr Hinterholzer explained that the Board division comprised about 25-30% of the Austrian based business and operated in project management and implementation of cutting solutions, together with project management and implementation of storage, handling and conveying solutions, sales of used machines and project management and implementation of IT solutions.
“Within our experience of big automated angular saw plants, we have always done a lot of transport logistics and we have learned to lift materials and handle material in various processes – pushing, vacuum and using other tooling,” he explained.
“We learned to manage all that by having the necessary control tools and software tools.”
In 2014-15, IMA Schelling had already started to work with large panel factory customers on highly efficient logistics solutions – so-called automated warehouse solutions.
For example Egger, together with the IMA Schelling Board division, is optimising its material flow and warehouse logistics to improve performance and flexibility.
EGGER PROJECT
For Egger, production of decorative panels for furniture manufacturers and interior construction contractors is an important requirement.
It often needs fast supply of quantities that can be produced in single component manufacture, with diversified small batches often the key requirement.
“The diversification in the board companies is getting higher and higher,” added Mr Hinterholzer. “The times are almost gone when companies are producing the same material and laminations all week.”
Both companies have been co-operating on such a flexible logistics system, initially at Egger’s HQ site, and then in several expansion stages.
IMA Schelling’s Board division works with automated warehouse specialist LTW to deliver such projects, which can feature a high-bay storage system
IMA Schelling supplies a comprehensive work cell in the solution, including conveying systems, lifting systems, panel cutting, panel processing, sorting, stacking, engineering and planning, packaging, order picking/ feeding, storage systems and digitalisation.
All the transportation and commissioning sections have been made within IMA Schelling Group.
Sanded raw panels enter the warehouse on 5m-high stacks and weighing up to 50 tons. Here, the order picking system breaks the large stacks down into smaller stacks, one metre high, which are then stored in the LTW high-bay warehouse.
In the opposite direction, when the order picking system takes panels from the high-bay warehouse, it arranges the panels in tall order-based stacks for the short-cycle press lines. In this process, the system stacks single panels or panel packages on top of each other so that they are in the right sequence.
The warehouse has approximately 1,450 storage positions for panel stacks. In addition to storage and order picking of raw particleboard panels, the high-bay warehouse is also utilised for MDF panels. Moreover, it supplies panel stacks to the IMA Schelling panel cutting cell.
Material stacks are pre-commissioned in exact sequence in various material types/ thickness.
In the first expansion of this concept, Egger invested in a high-bay warehouse at the Brilon site.
This system, also delivered by LTW, sees impregnated papers and decorative panels stored. A semi-automatic order picking system for the decorative papers is located in the zone in front of the high-bay warehouse.
Using a special drum-type turnover machine, the impregnated paper stacks for the undersides of the decorative panels are rotated through 180° when the base board is exactly aligned to the correct distance from the decorative paper.
These order-based stacks of impregnated papers stay in the high-bay warehouse until they are processed by the presses. Depending on the order, panel stacks as well as impregnated paper stacks – sorted in the order in which they will be processed – can be fed from the warehouse. The press then joins together raw panels having the required thicknesses and the applicable decorative surfaces exactly as ordered.
IMA Schelling says the material flow significantly reduces the set-up times of the presses, because pre-sorted stacks of panels and decorative papers are fed to the presses in accordance with the quantities and types specified in the orders, with no remaining products needing to be returned. The decorative panels, after they have been surfaced, are either re-entered into the high-bay warehouse, or they are fed to the panel cutting cell or carried directly to the packaging line.
Mr Hinterholzer said the Board division had already supplied four such automated warehouse systems, with a fifth currently on the order books.
“It is more common that we are doing things besides just saws these days,” he explained. “We get enquiries for storage systems, a flat storage system on our own, commissioning systems and fully automated packaging solutions.
“We have robot technology in house and we can do all these things. We are doing complete automation to the wrapping point.”
“All these things are becoming more in demand in the major field of board manufacturing, whether it is fibreboard businesses or ‘massive wood’ business.”
Expertise in such technology has inevitably attracted attention from solid wood industries.
Mr Hinterholzer said advantages of the automated warehouse approach include a reduction of product damage and accidents.
“The main issue you normally have is that a lot of internal transportation by board producers is done by forklift trucks. If you have a fully automatic solution you can control it 100%, 24hrs a day and the damage and accident situation is almost completely reduced.
“If you can reduce damage by 50-60%, and this is readily done, this is quite a substantial amount of money saved, which allows you to reinvest.”
The different expertise within the IMA Schelling Group’s various business units is useful to pool knowledge when board industry projects require linking the saws with profiling lines in fully automated lines.
MARKET DYNAMICS
In terms of general market dynamics during the pandemic, 2021 was described by Mr Hinterholzer as “extremely good” for order levels.
“It was the best year I can remember and I have been with IMA Schelling since 1993. I can also remember 1999/2000 when it was very good business. Last year was far above what we scheduled and we had already scheduled a good year.
“A lot of the increased business had to do with demand created by the requirement to cocoon and work at home [creating demand for home furniture].”
This, he added, was a time when demand was so high that furniture companies could not service all the high demand and the wood-based panels producers’ storage facilities were empty.
In 2022, the Board business unit is predicted to record an additional 50% more business, so it is almost fully booked and quite substantially booked for orders for 2023 as well.
“We have been in a good situation but it could also have gone a different way, so we need to take it as it is because times could change. In the machine building industry there are waves.”
IMA Schelling is having to invest in production capacity to service the demand.
“The automation, logistics and handling side of things has grown because of rising orders but also because the company is pushing in this direction.
“In the future we want to get 50% and more of our business unit turnover not directly linked to saws.”
To that end, building work has started at the Polish manufacturing site to double capacity in handling and automation.
The new 7,000m2 factory hall and associated offices is scheduled to be completed before the end of 2022. Longer-term, IMA Schelling is targeting a centralisation of the handling systems at the Polish site.
CORE CUT-TO-SIZE PLANTS
As for supplying its core cut-to-size plants, the company has completed some big installations, especially for thin boards in eastern Europe but also plants in the US and China.
A big angular unit was sold to a Polish customer, and a further two units for its HDF production at its Lithuania factory.
A big angular sawing unit for OSB boards was also supplied for a Swiss customer.
Recent innovations have included development of a high-speed batch size one saw line.
Other potential for growth lies in the mass timber construction industry, following the trend for finished solid wood elements, providing opportunities for different business units in IMA Schelling.
“This is giving us a lot of possibilities in the future,” said Mr Hinterholzer.
“We have extremely high demand for automated manufacturing within the furniture business but also board producers are looking for solutions to increase output and flexibility.
“We see the future demands more automation, especially in Europe.”