A certified ISO 9001-2000 company, today Imal not only specialises in gluing systems, blending equipment, on-the-line quality controls and laboratory testing equipment, but also more recently in the supply of patented blending systems for the production of MDF.
In its early days, the company’s product range included a number of more mechanical machines for wood preparation, but 10 years ago Imal and another Italian company Pal, of Ponte di Piave, Treviso (see p34), exchanged a small percentage of each other’s shares and removed areas of overlap in their product ranges. This led to Imal specialising more in the electronic and glue blending areas, leaving Pal to concentrate on the more mechanical aspects of wood preparation and, particularly, cleaning. Synergies between the two companies were of course exploited too.
In 2006, the cooperation of the two companies was further strengthened when Imal acquired the shares of Romeo Paladin, one of the two founders of Pal, and Loris Zanasi, managing director of Imal, became president of Pal as well. Pal remains an independently-acting company under its managing director and major shareholder Antonio Dal Ben but the two companies have, over the years, increasingly exploited their synergies in R&D and manufacturing to become like the two different faces of the same coin. "In R&D there are lots of projects where Pal and Imal join together, keeping product development ‘in-house’, such as Pal’s Cleaning Tower,explained Marco Zanasi, son of Loris and sales manager with Imal. Certainly the success of the partnership seems borne out by the increase in turnover just in the last two years. It has been a strong market for all suppliers to the panel making industry but Pal and Imal’s 25% increase in turnover in 2007 and a predicted 30%-plus for 2008 tell a cheering story. Next year is already showing promise for both companies, too. We are the biggest supplier of resin dosing systems in the world, in MDF, particleboard and OSB,said Stefano Benedetti, son of the founder of Imal and, together with his sister Alessandra, a director of the company.
“This year we have sold a lot of mechanical blending systems for MDF. The rising price of glue is forcing many panel makers to think about our mechanical blending system as opposed to the conventional blowline blending because we guarantee around 20% savings in glue consumption; that is what we guarantee, but in reality it is not normally less than 30%.”
Kastamonu of Turkey, Eucatex of Brazil and Homatherm of Germany have all bought these systems this year and Mr Benedetti said Imal is talking to a number of other companies. "When there is a dramatic rise in resin costs, as in recent months, the investment is well worth making,he said. Customers with existing blowline systems may choose to use a combination of the blowline and Imal’s mechanical blending system, but new lines can go for 100% mechanical. "We are expecting many orders in the coming months and into next year,continued Mr Benedetti. “The payback period is between 12 and 24 months – and we can calculate that for the customer – it is easy to prove.”
Mechanical blending is not an entirely new concept as it was first tried in the 1980s. However, mills then experienced problems with mechanical properties of the resultant boards and glue spots.
“Our blender is much better,said Marco Zanasi. “There are a lot of patented systems around the blender such as for the injection of glue involving hot air, glue injection and then cooling; and in other areas. "We guarantee no glue spots and we guarantee the mechanical properties of the boards.There is a total of 19 panel manufacturing plants running the system to date. Another area where Imal has employed its blending expertise is in the manufacture of OSB. The company began its research about three years ago but has paused with the slump in the market in North America. "Today, everybody believes the drum blender and injection system is outdated and needs updating because of maintenance and efficiency problems,said Mr Benedetti. “Also, in mills using MDI resins, there is a health risk when operators have to go inside a conventional blender for some hours in order to clean it.
“Thus we have devised a completely new philosophy for resinating the strands using our experience from MDF where the blender is fixed and a central shaft turns. There is no maintenance required, no stopping the blender to clean it. The resin is applied to the strand flow before it enters the blender and the nozzle system is thus on the outside and easier to monitor and control. "In a conventional drum blender, the glue is applied by a spinning head inside it, which can plug up – hence the need to go inside the machine to clean it.” Imal believes that, as with the MDF blending system, resin savings will be significant, while resin distribution on the strands will be improved.
In its quality control equipment for panel production lines, Imal has, after around 10 years, completely redesigned its Blow and Thickness Detector to produce the Bond Classifier. In common with the old system, it still employs ultrasound but is said to be much more accurate: “Due to new technology and a lot of R&D,said Mr Zanasi.
The CPD 600 on-the-line vertical density profiler is now on its fourth generation and continues to have big success in the market, he said. “We are developing and improving all our machines, cooperating with several Italian universities who we are always working together with to find ways to reach the required result,added Alessandra Benedetti. “We take on engineers from those universities and have students here on work experience.”
Another recent Imal development, the PSD (Press Security Device), installed before a continuous press to protect the stainless steel belts from damage from foreign bodies in the mat, is currently under further development too. “We are still the main supplier of mechanical testing machines for panel mill laboratories, offering tests for modulus of elasticity and rupture, density profile, moisture analysis and internal bond,said Mr Benedetti. “Our IB600 model is becoming increasingly popular in the particleboard market and several major groups have one in each of their factories.Another product, the IBX600 machine, combines mechanical tests with density profile analysis. In January this year, Imal opened a new company, Imal Inc in Atlanta, Georgia, US, under director Carlo Santosuosso to better support the North American market with service and a spare parts warehouse. Imal Inc still has its long-established sales office in Washington State as well, run by sales manager Mike McNeeley.
The company also plans to open a subsidiary in Moscow, Russia next year and to set up a formal sales arrangement in China. Imal and sister company Pal are both looking at bulging order books, as are many machinery suppliers to the industry at the moment, and 2009 looks to be set fair as well. Nobody is sure why business is currently so good, but of course everybody hopes it will continue that way!
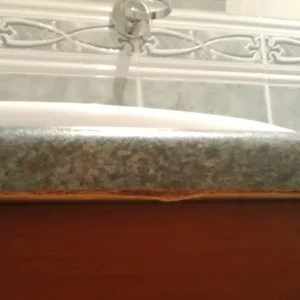