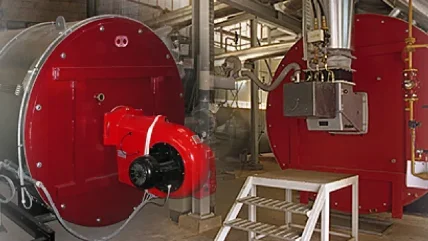
INTEC Engineering GmbH will be approaching its 30th year in business in 2025.
The company, which is based in Bruchsal near Karlsruhe, was set up in 1995 after experienced energy systems executive Edwin Karrer decided to set up his own enterprise.
Mr Karrer had been involved with two energy systems firms before founding Intec, dealing with thermal heating systems that were very common in wood industry industrial applications.
He introduced the step grate combustion system for biomass firing while at a former company and further developed the product at INTEC. He has been a known, respected specialist in the field of heat transfer and thermal heating systems for many years.
While still active in the company, Mr Karrer has now handed over the management reins to his son Denis, who has been managing director for the past year.
INTEC serves a variety of industries, ranging from the wood industry to textiles, food, chemicals, palm oil, pulp and paper and consumer goods.
In its early days, Intec specialised in secondary circuits, such as temperature control equipment to regulate the heat input to separate zones of a continuous press.
Now its services start from system concepts, through to production and delivery, including complete turnkey plants.
For manufacturers of particleboard, MDF, OSB, LVL or other wood-based products, INTEC offers complete energy plants with various heat transfer media: thermal oil, steam, hot water or hot gas.
The range of INTEC products consists of gas or oil-fired thermal oil heaters from 30 kW up to 100 MW, steam or hot water boilers, waste heat boilers, electrical power plants, ORC modules and secondary circuits for press heating.
Energy and power plants generally have a capacity of 100 MW thermal or 20 MW electrical output.
INTEC sales director Christian Daniel spoke to WBPI after a recent extensive trip to overseas markets and customers.
“The business has been developing very well,” he explained.
“We have the manufacturing centre in Germany where we produce all our own equipment. We also have offices elsewhere in Germany and around the world – India, Malaysia and the US.
“We try to have representation on each continent and be very close to the customer, so we are in the same time zone and give them a good service.”
INTEC has been working in the woodbased panels sector since 2001, offering complete biomass plants, thermal heaters and secondary control circuits and loops.
It formerly completed many projects in tandem with Dieffenbacher, until about 2006, when the latter set up its own energy systems division.
INTEC has a strong relationship with leading international wood-based panels manufacturer Kronospan, having completed many projects for the company.
Typical INTEC products supplied in Kronospan plants include three stage rocket heaters, thermal heating systems and heat recovery equipment.
“Kronospan has 20-30 plants with such a rocket heater. Beyond that we have also delivered up to10 biomass plants to Kronospan.”
One of the most recent projects for Kronospan was for the company’s Sanem plant in Luxembourg.
Other global projects for the wood industry include biomass plants in South America, with INTEC actively seeking to develop new markets. It has many biomass plant reference projects in Asia, though Mr Daniel said this particular region could sometimes be a “battlefield market” with independent suppliers vying with large groups for business.
Previous Asia customers include the likes of HeveaBoard, Geruco MDF, Segamat MDF and Green Panel, while in Europe Kastamonu Entegre has also purchased INTEC equipment.
He said INTEC’s expertise – many of its staff have been working at the company for multiple decades – and product offering allowed it to still have a powerful reach as an independent supplier, with projects to provide heating systems for panel presses sometimes still being contracted independently outside of the main contractor’s scope of supply.
ENERGY TRENDS
INTEC sees that most wood industry manufacturers have some form of biomass combustion systems, even if it is just to burn their waste wood for heat.
“Biomass is a very hot topic and the business is going nicely,” said Mr Daniel.
“For us the focus is shifting to the power generation side, like a waste to energy plant or standard power/co-generation systems.
“This is one of the things customers may eventually do in the wood industry. If they currently have a gas turbine, they may think about having an additional biomass power plant to be independent of the gas supply.
You have more independence from the grid and price increases.”
This interest in a more complete power plant can be delivered in a number of ways, including steam turbines and Organic Ranking Cycle (ORC) systems.
Intec has noticed that some smaller sites have started to diversify.
“If they only had gas burners, they are thinking of going for fuel systems to be more independent from one fuel alone. That allows them to react better to the individual energy pricing developments, whether for gas, light fuel oil and so on.
“For other customers in other industries, discussions are coming up to have a burner to burn hydrogen if possible. We already have some of these units in operation, but this is more of a future development.”
RDF (refuse derived fuel) – fuel produced from municipal solid waste, industrial waste or commercial waste – is currently seldom used by the timber sector, Mr Daniel explained.
“If you have to burn plastics and other things you could have big issues, because you get pollutants in the hot gas and the hot gas goes to the dryer and then you could get these pollutants in the board. You have to include sophisticated flue gas cleaning equipment, which is costly.
“RDF can be used as an additional, alternative fuel, but we have not seen much demand in the last year. The demand has been more towards recycled wood use for board production and some as waste to be burned.”
The importance of fuel/energy diversity was demonstrated on Mr Daniel’s recent trip to South America where a number of hydro power plants have seen their energy production limited because there is not enough rain.
In terms of technical developments, INTEC thermal heaters have achieved a level of high efficiency where up to 94% of the fuel can be used.
“The important thing for the wood industry is that the products are very durable and the accessibility is good for service reasons,” said Mr Daniel.
“If customers have downtime, the question is not often what is wrong but how many shifts do I have to stop. Accessibility is designed so we can run for about 4,000 hours without stopping for major maintenance. This is a major request.”
THE FUTURE
So how does INTEC see the future energy market situation?
“It is difficult to say, as the impact from the Covid era and war in Ukraine is still there and has a big impact on the pricing of the equipment,” explained Mr Daniel.
“It is a difficult time for investment. It could be that customers will wait longer to commit [to projects], and for a further normalising of supplies.”
Companies like INTEC obviously look at all market areas to ascertain prospective machinery investment levels. That includes keeping track of consumer and wider market factors.
“We have to see what the development will be with the consumers because they have the same issues with inflation and higher costs for living. We had a feeling that the consumption is getting a bit quieter in this area.
“What is booming is the food industry, but consumer goods are not developing very strongly. Maybe it’s not critical for consumers to invest in furniture currently and they feel they can wait before investing in it.”
Mr Daniel, who has himself worked for INTEC since 2001, said the company had a big focus on technical development, with many reliable solutions and different approaches for the customers.
He acknowledged that European subsidies for businesses to generate their own electricity were not as available these days, though subsidies for industrial development projects on greenfield sites could be.
Finally, the topic of sustainability is worthy of a mention, as it’s a definite focus of the company.
INTEC not only aims to boost sustainability for customers with its energy-generation solutions, but it practises what it preaches by having an array of solar panels and heat pumps at the Bruchsal site, with company cars charged with its own generated electric power.
In 2013 it scored a first – building the world’s first hybrid solar/biomass heat and electrical power plant on a commercial scale, near Barcelona, Spain.