The original foundation for the Pallmann company, in 1903, was the flour milling industry, in which the company was involved in both milling and the design of wind- and water-powered mills. That essential basic element of size reduction is still the focus of this seventh- generation family-owned firm.
The company now employs around 700 people worldwide and is involved in a variety of industries from food to chemicals, plastics and wood, as well as the agricultural residues used to make panels. However, the panel industry accounts for the majority of the company’s turnover.
Pallmann says it has largely based its success in these very diverse fields on a heavy concentration on research and development (R&D).
The company is headquartered in Zweibrücken in south west Germany, where it has a large R&D facility which includes the largest size reduction test station in the world. The space devoted to R&D alone is 20m x 80m in a separate building. There are three floors, with a training centre on the top floor, smaller demonstration/testing machines on the second floor and three sections for larger machines on the ground floor. These last three areas are for plastic recycling and food processing; the wood processing department; and the main R&D labs.
The size reduction test station employs the company’s smallest machines, but these are not small-scale versions; they are small production machines, emphasizes Harald Fried, area sales manager for North America.
“We have very precise scale-up factors for these machines, enabling us to produce very precise results,he says. “This means there is very little ‘surprise factor’ when we deliver a machine to the customer’s mill – the specification with regard to throughput and so on will be met.”
The test set-up is a PZU 16-525 OSB production system with a theoretical production capacity of 20 bone dry tonnes per hour (bdtph) of standard OSB flakes.
“People from all over the world send their logs here and we make flakes on a production machine with real production runs,says Hartmut Pallmann, chief executive of his family’s business. “The flakes then go to an existing board mill for test boards to be produced – it is almost like pre-certification of the panel product.”
The R&D carried out over the years has resulted in a product range which comprises around 800 different machines and models.
“We carry out lots of special designs for customers,says Mr Pallmann. “Continuous improvement of the machines is one of our main aims and another reason for our large R&D facility – and our test department. After our tests, the machine is run in trials at our customer’s factory before we ‘go public’ with any new development.”
Pallmann began its involvement in the wood panel business principally in particleboard and OSB, then moved into MDF and now claims to be the second largest supplier of refiners in the world for MDF.
The machines produced by the company are identified by a two, three or four letter name, all of which begin with the letter ‘P’ for Pallmann. The other letters describe the function of the machine, in German.
Thus there is the Drum Chipper, PHT and the disc chipper PHS. The former processes sawmill waste, roundwood, peeler cores, veneer waste and wood from forest thinnings and annual plants for particleboard, fibreboard, wood combustion and the paper industry. The latter is a chipper for the paper industry.
The re-chipper PSN is for re-chipping material such as butt ends; gang saw, veneer and particleboard waste; screen rejects; shavings; and splinters.
The Series PZKR covers the family of knifering flakers which have the patented system of counter-rotational flaking and a knife ring exchange system. Pallmann produced its first knifering flaker in the 1950s.
These flakers are designed to produce flat flakes of exact thickness from chips, veneer waste, purchased flakes or any kind of coarse raw material. A fast rotating impeller leads the chips to the knives of the counter-rotating knife ring. It is this counter-rotating feature which Pallmann claims gives trouble- and obstruction-free operation and flake discharge, even with very wet incoming material. The company also says that it promotes good knife utilisation and uniform wear.
The feeding device for the PZKR, named the Cleanomat, offers continuous feeding with simultaneous separation of undesirable material. Metal is removed by drum magnets in the Cleanomat, which is a heavy particle separator, removing grit and stones in a similar way to an air classifier. A vibro-feeder with integrated screen deck at the infeed to the flaker allows the bypassing of fines, thus saving knife wear.
The so-called quick knifering change system developed by Pallmann has reduced the time required for this essential operation to between five and 20 minutes, according to machine size. The door of the flaker is opened, an exchange jig is moved into position and the knifering clamps released. Pushing a button then initiates the hydraulic removal of the ring to be transferred to a transport carriage to go for sharpening. A reconditioned ring is then inserted and clamped.
The removed ring can now be sharpened on the fully automatic PZSE sharpening and setting robot which reduces the man hours needed for the sharpening process from about 21⁄2 hours manually to around 10 minutes and gives far higher sharpening accuracy. The man-hours in a manual system are absorbed in disassembling the knife packages, cleaning and grinding the knives and then setting the packages before final assembly into the ring again. The 10 minutes used in the automatic system are for getting the ring into and out of the robot. Wear shoes can also be re-ground as required in the same machine to ensure constant knife protrusion. The setting and grinding process takes about 40 to 50 minutes, depending on the size of the ring, the degree of wear and the knife length.
The PHMS is the Pallmann high-speed hammer mill series, while the PHPH is the impact hammer mill, particularly suited to processing waste and recyclable wood.
For refining chips for the fine surface layers of particleboard, the double stream screen basket mill PSKM is offered with a grinding path diameter of 600-1500mm and working width of 220-1180mm.
Pressurised refiners for the preparation of fibre for MDF production are identified by the letters PR and the largest of these built to date is a 62in diameter unit, of which there are several in operation. One of the most recent was installed at Yildiz MDF in Turkey and this has a 24in plug screw feeder. Although this is the largest refiner installation to date, Pallmann is prepared to produce refiners up to 72in.
The Yildiz mill also has the largest drum chipper in the world, at 2.4m diameter, and a Pallmann chip-washing system.
The vast majority of these machines are made in-house at Zweibrücken, with only the very largest components being outsourced. To this end the factory is equipped with an array of heavy engineering machinery, including flame cutters which can cut steel up to 300mm thick.
In the past, mills wanted the size reduction equipment supplied as a package, ready to go, but things have changed.
“Customers more and more want to get involved and to build up the equipment on site,says Mr Pallmann. “It is cheaper in terms of transport costs, taxes and so on. We do all the engineering and quality control and certified welders do the on-site assembly.
“For instance in a chip washing plant, much of the installation can be carried out by the customer, including the steel work for the building. We supply the controls, electronics and key components such as pumps, chip washer, de-watering screw etc, but the rest is built by the customer.”
He continues: “Globalisation is not just a word, it is real. We do the complete engineering here, and some key components, but the rest is done on site under our supervision.”
Brazil offers an example of this approach: Pallmann supplied the Fibraplac project from green end to pressurised refiner as a complete line, using its subsidiary in Brazil to assist in the realization of the project.
China is a major market for Pallmann. Gaofeng, among the largest MDF lines in China, is currently under construction and involves the supply of the complete fibre preparation system, including rotary debarker, chippers, cleaning and refining, all as a turnkey contract. The company already has two Pallmann refiners.
“More and more people worldwide want complete packages,says Mr Pallmann. “However, there is a trend for customers not only to want a turnkey green end, but to specify the machinery using their own experience.”
Hence the concept of ‘Pallmann Wood Yard Systems – complete systems from one supplier’. The first of these to be built in-line to an MDF line was at Kronopol in Zary, Poland, but several such lines have been supplied for OSB.
“In the last two years, business was good for us in OSB flakers and we got all the orders for the new mills in Europe. That meant 10 flaking lines, including nine debarkers,Says Mr Fried.
The growing interest in agricultural fibre based boards has also provided opportunities. The company has supplied bamboo chippers to India and Bangladesh, depithers and hammermills for sugar cane bagasse mills, a special version of the PSKM double stream mill to Isobord wheat straw plant in Manitoba, Canada and a specially designed pressurized refiner for cotton stalks to China. Gypsum and cement bonded board mills are supplied as well.
“We have also done a lot of work on oil palm empty fruit bunch preparation and sold a line to Kalimantan,says Mr Fried.
Recycled wood gets ever more popular as a raw material for panels and Pallmann has machines for processing this sometimes challenging resource.
Refurbishment of wear parts such as plug screws and refiner plates has become increasingly important to the business. “Today, more and more we have to offer a full service,affirms Mr Fried.
That includes the new service centre in Zweibrücken, which has six distinct groups of engineers specialising in different machine types. Pallmann service centres around the world are computer-linked to the service centre to give a 24-hour service. Engineers are also available to travel anywhere in the world at short notice.
For the future in this currently slow market, Pallmann still expects some growth in China for MDF, the rest of Asia for particleboard and some MDF, with North America providing opportunities in OSB. Some modifications and upgrades to MDF lines in Europe are also anticipated, as well as a few new lines.
“We are a horizontally integrated business, from the original idea to its realisation,says Mr Pallmann. “Anything from the 10hp lab machine to the 10,000hp refiner we can do; as long as it is a size reduction machine, we can do it. The overall concept must be good but it is the little details that count.
“When you need to produce a board, come and see Pallmann about the raw material preparation to make it.”
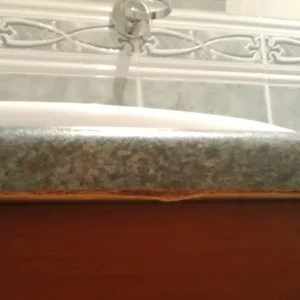