Balancing between spiralling costs, availability of high quality raw material and global efforts to preserve natural resources requires the panel industry to change its viewpoints, says Markku Levanen, head of sales at Dieffenbacher in Finland. “In fact, we are talking about changing the ideologies.
“There can be few mill and production managers who have not considered making use of the raw material that is increasingly available and comes with a tolerable price tag – and that is recycled wood material.”
The French particleboard producer Compagnie Francaise du Panneau (CFP), part of the Parisot Group, decided to take advantage of the ClassiCleaner wood raw material cleaning system from Dieffenbacher in its plant, which produces 500,000m3 of panels a year, mainly for the furniture industry.
Prior to investing in this screening and cleaning system, the plant was able to use only a small proportion of low quality chips in its process. The ClassiCleaner is CFP’s response to raw material prices and availability.
“The ClassiCleaner has allowed CFP to significantly increase the proportion of low quality chips that it uses because heavy contaminants such as stones and glass, and light impurities, are now efficiently separated from the raw material, the end-product quality is better and the lifetime of the flaking equipment is longer,said Mr Levanen. “Light impurities such as plastic foils and thin papers do not affect the panel quality any more either.”
Philippe Valdenaire, technical director of Parisot Group, said: “We chose the ClassiCleaner because of its compact size, screening accuracy, ability to separate light and heavy impurities and its low operating costs. An additional benefit has been the tidy surroundings.
“Since the installation in June [2009], we have been able to increase the use of low quality raw material. The efficient chip cleaning enables us to further increase the use of recycled raw material without compromising the board quality. In addition, we are impressed by the very low wood loss in the cleaning process”.
The ClassiCleaner provides for a screening result according to the overall process needs and the cleaning is carried out only to the enriched sub-flows. This innovative operating principle makes the patent-protected ClassiCleaner both efficient and economical, claims
Dieffenbacher.
The particleboard industry is not the only one struggling with the availability and quality of wood raw material; the pellet industry is seeking the same material sources as the panel producers. Quite logically, what suits the raw material preparation needs of the particleboard manufacturing process also suits the needs of pellet manufacture. Due to this evident synergy, the Dieffenbacher Group now serves the pellet industry as well as the panel industry.
“Chip cleaning is becoming increasingly important also in the wood pellet industry,said Mr Levanen. “Wear of dies and other process equipment correlates closely to the sand and silica content of chips and flakes, no matter if we are talking about panel or pellet manufacture. The norms of silica content in wood pellets require producers either to closely monitor the mineral quantity of raw material – or to take measures to remove it,he explained.
In pellet manufacture, screening the chips and flakes into different fractions can bring similar savings in energy consumption to those experienced in panel manufacture and Dieffenbacher says its ClassiCleaner fits well in both processes.
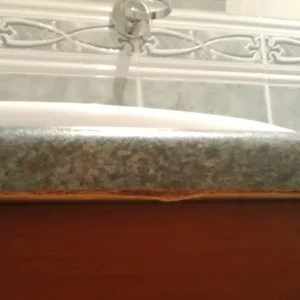