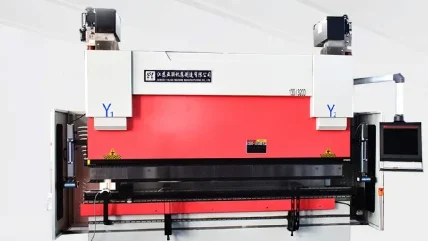
Mr Guo Xijiang, an entrepreneur from Jilin Province in north-eastern China, set up an MDF factory in Jilin in 2003.
Mr Guo realised that Mende-type (calender or drum) presses for making thin board were very expensive, so he decided to make one for himself.
It was obviously successful, as Mr Guo was approached by other Chinese MDF manufacturers asking him to make calender presses for them.
His new company, Jiangsu Yalian Machine Manufacturing Co Ltd, was set up in 2005 and sold a total of around 25 of these calender press lines, both in China and abroad, from 2003 to 2008.
Mr Guo moved out of MDF manufacture and into machinery production full-time. He felt that if he carried on producing MDF, he would be seen to be competing with his machinery customers.
Using the profits from his calender press production, Mr Guo set his sights on developing a full-blown continuous press that could compete with the two existing German producers’ presses.
There are two other producers of continuous presses in China but only Yalian is a privately-owned company, relying on its own investment, without any government financial support, which makes Mr Guo’s achievements seem all the more impressive.
The first Yalian continuous press was put into service in 2010, in Shanxian County, Shandong province. That first continuous press was 4ft x 38.6m and the line started up in 2010. The scope of supply was from forming to storage, which is typical for Yalian’s sales to Chinese customers to date.
However, for overseas customers, Yalian’s scope of supply covers the complete line, to make it easier for customers.
Yalian’s continuous press was successfully developed as a competitive one, creating a lot of interest – and orders – from MDF, particleboard and, latterly, OSB manufacturers in China.
This co-operation in development continues to this day, as Colin Zheng, international business manager, explained: “Mr Guo maintains a very good relationship with his customers and works with them.
“If any customer finds a problem on his line, or is willing to improve the performance of a piece of equipment, or the whole production line, Mr Guo will offer the solution, free of charge, including the modification of the equipment, and this helps with continuous development without the high cost of running our own test plant full-time,” said Mr Zheng.
Interestingly, I spoke to Mr Guo in person at the WMF exhibition in Beijing in 2010 when his first press was only just running: “We make the main components and buy in some sub-components,” he said at that time.
“Personally I think we are just a beginner. In technology terms we are not up to the standards of the two German manufacturers, who are very mature in their technologies, but the advantage of our continuous lines is that there are a lot of small-to-medium size companies in China who do not have much capital and our price suits them.
“Our market is only in China – we can’t compete with them in export with our lack of experience,” he said in 2010. “Maybe in 10 years or so, when we are strong enough, we will go to the international market.”
However, things progressed rather faster than he had anticipated and export orders came in earlier than Mr Guo thought.
In 2011, Berndorf of Austria bought a small, 7ft x 14m press for a project in Portugal.
In 2013, according to Yalian’s reference list (kindly supplied to WBPI by Mr Zheng) Melemin Saze Tabriz of Iran purchased a 6ft x 26m continuous press for particleboard production.
In 2015, Century Plyboards (India) Ltd bought an 8ft x 26m press for MDF.
Yalian Machinery’s best year for total continuous press sales was in 2016, when 17 projects were won. This included an extension to a Siempelkamp ContiRoll MDF line for Kronospan in Bulgaria.
In 2017, Yalian achieved sales of 10 projects and then another 10 in 2018.
Another export order was among the six lines sold in 2019, this time going to a South Korean customer, HWMSC Co Ltd, Busan, Korea.
Interestingly, this line was similar to an MDF line in principle, but instead of wood, it employed rock wool fibre. The rock wool panels are for decorative end-uses, explained Mr Zheng.
In 2020, a very difficult year for the world with the Covid pandemic raging, a very respectable nine lines were sold by Yalian but this time they were all destined for Chinese customers.
In 2021 there was a decline in the number of orders but there was a strong return to exports, with three lines out of the seven on the reference list going to overseas customers: Kronospan’s particleboard plant in Kaluga, Russia, is worthy of particular mention here as it has a daily capacity of 3,100m3, which equates to over one million m3 a year. That press is 9ft wide and 59m long.
The nearest press to that capacity was supplied by Yalian to Bazhong Jianfeng New Materials Co Ltd of Chengdu, Sichuan Province. That was a 2,000m3 a day particleboard line employing an 8ft x 43.8m continuous press.
PT Indonesia Fibreboard Industry was another overseas customer, buying a 4ft x 38.7m continuous press for MDF production. The capacity of this line is 630m3 per day.
The third overseas order came from Metro Decorative Pvt Ltd of India. Again this was for MDF production, and this press is 4ft x 31.9m with a stated daily capacity of 600m3.
Obviously Yalian’s principle market is China and it has supplied continuous press lines to Anhui, Fujian, Guangdong, Guangxi, Hebei, Henan, Hubei, inner Mongolia, Jiangsu, Liaoning, Shandong, Sichuan, Xinjiang and Shejiang.
Today, Yalian has four locations: Yalian Machinery Co Ltd, Beijing office; Yalian Machinery Co Ltd, Dunhua; Yalian Machinery Tangshan; and Yalian Bytter.
Tangshan manufactures all press parts, hydraulic systems and the press heating system, while Dunhua covers the electrics, forming, conveying, pre-press, trimming saws, diagonal saws and raw board handling.
Continuous steel press belts are produced at the Yalian Bytter works, which was set up in 2010.
Over the four sites, Yalian employs some 296 people.
From this you will see that Yalian is not just a press maker, but supplies the whole line from forming to intermediate storage.
Chipping and refining are currently bought-in, though the company is working on bringing chipping/flaking in-house.
Yalian supplied its first OSB line, to Shandong Province, in 2016, with a daily capacity of 500m3.
To date, Yalian has supplied 61 MDF continuous lines, 23 for particleboard, five composite panel lines, four OSB lines and that one rock wool line, for a total of 94 continuous press lines since 2010.
When it comes to raw materials used in manufacturing panels, wood is obviously the main substrate used.
However, Yalian has supplied a line to Liaoning Province which uses reeds to make particleboard successfully, as well as that rock wool line, which was mentioned earlier.
One more victim of the pandemic, of course, was the holding of physical exhibitions such as Ligna in Germany and WMF in China.
However, Yalian did attend the WMF in Shanghai in September 2020. The company has never attended the Ligna show.
As he told me at WMF in 2010, Mr Guo’s attitude to exports was that there was a big enough domestic market to tap into, although he did believe that exports would increase as word spread.
In fact, Yalian has achieved 10 overseas orders so far, apparently without really trying, and well within the 10-year period he predicted would be required.
I asked Colin Zheng about the current market in China.
“The Chinese economy has not been so good in the last two years, with travel restrictions and freight problems, which have meant that raw material prices have increased a lot. Wood-based panel prices have been increasing all the time.
“However, we still received orders from overseas customers who had visited us before the pandemic – It would be hard to imagine anyone buying such an expensive production line without seeing it!”
I then asked him about the performance of the Chinese panel market specifically and he said: “Particleboard and MDF sales are not so good, but special types of board are doing better.
“Our sales manager reports that OSB is trending now and also super strength particleboard is doing well.”
This product is a five-layer board, with three thin layers of particleboard material faced with very thin OSB-like layers. These are made up of very thin strands which are much finer than normal OSB but give the extra strength characteristics to the board. This make-up suits the fibre supply available to Chinese mills, such as poplar.
“I predict that in 2022 we will have orders for five lines to produce OSB and super-strength particleboard,” said Mr Zheng.
“In China, people always want some new product, even if it is not that different [to what is already available]. Lightweight boards are popular, although low density boards are not so popular.
“High density board up to 1200kg/m3 in the surface layers and 1,000kg/m3 average density is popular as well. It uses a high volume of resin but that also offers increased moisture resistance and we have an Indian customer who is particularly interested in that.”
Mr Zheng went on to say that resin availability during the pandemic has not been a problem, although the price did, unsurprisingly, increase.
“The important trend now among our customers is towards the reduction of production costs; every yuan is critical these days,” added Mr Zheng.
WBPI couldn’t end the interview without mentioning the highly experienced competition for Yalian’s continuous press and wondering how competitive are Yalian’s lines?
Mr Zheng seemed to suggest that the difference in price between Yalian’s offering and that of the two German suppliers was not that great.
However, he did add that every line is custom-made to the client’s requirements.
“Because they are custom-made, it is difficult to compare prices between projects or competitors,” he said.