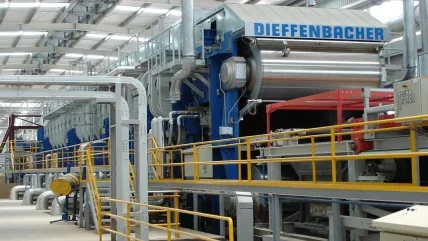
Dieffenbacher’s appearance at Ligna this year had more significance than merely being the first opportunity for four years to present its solutions to the wood-based panels industry at the world’s leading wood industry exhibition.
The banners emblazoned with “150” on the extensive stand in Hall 26 gave notice of a very special occasion – the company’s 150th anniversary.
This length of time is simply mindboggling and the milestone stands as a great achievement for a family-owned manufacturing company.
Dieffenbacher held a special party on Ligna’s first evening to celebrate the occasion, with people attending from across the wood-based panel industries.
And later at Ligna, current chief executive officer Christian Dieffenbacher gathered the world’s panel industry press for interviews at the show – updating on the progress the company has made and innovations it is pushing forward on.
Mr Dieffenbacher, the fifth generation family member to become CEO, pointed to the company’s anniversary motto at Ligna – “150 years of transformation on solid ground”.
“We have always been adapting to trends in the world,” he said.
He pointed to his great, great-grandfather Jakob Dieffenbacher who founded the company in 1873 as a young man, starting in Eppingen with a small locksmith’s shop for cash registers, before later specialising in hydraulic presses for processing fruit, wine and cooking oil.
By the 1950s the company had entered the wood industry.
Today, the global business has 1,850 employees and a turnover of more than €400m, focused on developing, planning and manufacturing complete production systems, including digitalisation solutions for controlling processes.
Of course that word “transformation” on the company’s banner at Ligna is a thread that has run through Dieffenbacher’s history, with its presses transforming various materials into products.
Three of the four business units – wood-based panels, recycling, forming – are dedicated to making the most out of materials.
The fourth – energy – is a business area expected to grow following the acquisition of the Austrian power plant manufacturer BERTSCHenergy, which has led to the formation of Dieffenbacher Energy GmbH. An additional 150 employees joined the group from BERTSCHenergy.
STEADY GROWTH
Mr Dieffenbacher said the company’s turnover reached approximately €420m in 2022 and predicted further growth to around €500m in 2023. The addition of the new energy division would, he added, lead to further increased turnover in the future.
“In general the market is slowing down [for wood-based panels],” he said.
“The last two to three years were quite extraordinary and we do not expect the pace of development to continue at that level.”
Mr Dieffenbacher predicted there would be fewer new wood-based panel line projects but, instead, a continuing focus on making lines more efficient. He does see increasing potential in special panel products, such as wood fibre insulation boards.
Orders in the forming business have reportedly been picking up, while recycling order levels are healthy.
The background macro-economic climate has seen high inflation and interest rate levels having a dampening effect on demand for wood-based panels.
On the wood-based panels plant project front, Dieffenbacher is finding India to be a very active regional hub for MDF investment, while Australia and New Zealand are also positive due to the proliferation of older equipment in existence there needing updating.
The US market is described as strong and Dieffenbacher has supplied the line for the first wood fibre insulation plant in the country.
CHINA MARKET
China has been stable in terms of orders over the past two-and-a-half years.
“The shift from MDF to particleboard is still going on [in China ] and the Fine OSB trend is continuing,” noted Mr Dieffenbacher.
He also referenced the wheat straw board trend in China, with customer Wanhua Ecoboard’s No 9 and 10 plants (supplied by Dieffenbacher) using this material due to start up in 2023.
“We see customers moving towards more and more of these new materials.
“It’s very important for our customers to have a green product these days,” said Mr Dieffenbacher.
Stefan Zipf, head of the Business Unit Wood, referenced the success of the recent date palm board project – “Desert Board” – in the UAE and said Dieffenbacher had agreed a similar second project for a customer in Egypt, though it was currently too early for further details to be released.
By the time of the Ligna exhibition, Dieffenbacher had reported four new woodbased panel line project orders in 2023. This comprises three orders for the Eppingen operation – two Chinese Fine OSB lines and an MDF project in South America – and one order for Dieffenbacher’s Shanghai-based SWPM in the local Chinese market.
On the R&D front, Dieffenbacher is participating in the multi-agency EcoReFibre project aimed at recycling waste MDF for reuse in new MDF boards. The company is the only primary wood-based panels machinery manufacturer involved in EcoReFibre.
The ambition is to substitute up to 25% of the virgin fibres currently used in the European fibreboard market. Currently, the project is at the lab and pilot plant stage.
Clearly, Dieffenbacher believes waste MDF has potential as a future panelboard feedstock and has recognised the large amount of waste material that is expected to be generated in the coming years.
Staying with the sustainability agenda, customers’ desire to have a small CO2 footprint has led the company to work with INEC (Institute for Industrial Ecology) at Pforzheim University in order to develop CO2 footprint calculator software. The aim is to identify CO2 emissions and reduce the numbers in order to improve the carbon footprint of companies.
Already, technology such as the belt dryer supplied by Dieffenbacher is enabling energy use to be reduced at customer plants.
Dieffenbacher’s digitalisation developments are also a big area of focus (to read more about this please see WBPI’s Ligna Review on pages 26-30).
CONTINUOUS PLYWOOD PRODUCTION
Among the many innovations being promoted by Dieffenbacher at Ligna was its new continuous production concept for the global plywood industry.
A video screen on the company’s stand showed visitors how Dieffenbacher had supplied China’s first continuous plywood line and in doing so presented a model for more profitable and efficient operations for the plywood sector.
The project, supplied by SWPM, features a 150,000m3 annual capacity plant and involved the supply of a microwave heating system, gluing system for PMDI glue, lay-up and press. A total of 18 robots also feature in the hi-tech operation.
Regarded by Dieffenbacher as a “genuine first”, the project was completed in 2022. The line has the flexibility to produce various board lengths.
Mr Dieffenbacher emphasised that the company wants to broaden its horizons in terms of the scope of work it can do.
Beyond China, Dieffenbacher also sees potential for such continuous lines in the US and India, which are very big plywood markets.
“We are ready to tap the global plywood industry,” said Mr Dieffenbacher.
“We want to come up with an optimised concept for this audience.”
This involves increasing production speed, capacity and quality.
Compared to production on a multiopening press, you can produce plywood with more consistent mechanical board properties and significantly lower thickness tolerances with less or even no sanding.
Dieffenbacher says the fully automated continuous laying and pressing technique can achieve significant savings in labour and wage costs, while reducing resin and energy consumption.
The plywood technology enables board thicknesses from 9mm-120mm and with all kinds of resins (PMDI, PF or MUF) and the production of either single plywood (usually with no veneer overlap), continuously produced plywood (Conti-Plywood), LVL and cross-banded LVL on the same line.