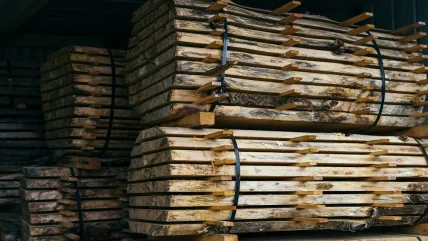
Several conversations recently have reminded me of the diversity of timber species available, yet there is a tiny fraction that we are geared up to using in industrial processes.
Every region has its dominant or preferred species, whether for lumber or panels production. This dates from an era when optimisation and technology went hand in hand. Matching the resin used to the species available locally led to better bonding, higher performance, higher efficiency. Precise chip geometry – optimised for the rate of steam mobility and heat transfer were also subjects of deep scientific investigation. Listening to those engaged in R&D, perfection was attainable.
Roll forward by 30 years and the industry has adapted to greater diversity. Not only does recycled chip contain a huge range of wood species, it also reduced our attitude to perfection in chip geometry. In parallel, researchers have shown that many nontimber residues can also be formed into panels, whether from the core of hemp or flax stems, or cereal straw or nut hulls. We’ve seen boards made of almost any biomass.
So why the reluctance in the middle ground? If the forester offers a minor species like silver fir or Western hemlock, surely we can use it just as easily as spruce. Or what if short rotation coppice generates small diameter chestnut, willow or other species, can’t they just drop in? Each region has its minor species, yet these may carry myths about being ‘not suitable’ for panels in one way or another.
One theme this month for me has been emerging species: chosen by foresters for a changing climate. Not the minor species we are used to having on the edge of our awareness, but species new to our region. Species selected to be better able to survive in the predicted climate of 2040, 2050 or beyond – whether this is predicted to be wetter, drier, hotter or windier than current conditions. If foresters today are considering diversifying, taking a punt on new tree species, it will only be 15-20 years before we see thinnings of these species reaching the mills. This will be a good opportunity to revisit all the fundamentals of panel making. To think through the reasons behind the optimisation processes we have inherited – whether in resin or chipping technology.
Looking to the tropics I see a precedent too. Where once plywood was a predictable commodity, made of the dominant species for the region, now we see such expansion of production, coupled with decreasing supply of these favoured species of peeler logs.
A wide range of plantation species are sought for panel manufacture, but as limits are reached, new countries are encouraged to sell to ever-hungry mills in the leading producer countries (China, India). Better prepared countries such as Malaysia and Indonesia rely on plantation species such as Acacia mangium, possibly with cores of softwoods like Radiata pine.
For many mills the range of species used has shifted, with low density core plies of poplar becoming common, but a wide range of less known domestic species supplementing this. Eventually a hungry industry requires material and compromises on species. The face veneers become thinner and thinner to utilise the small quantity of high quality keruing, balau or merbau, as it is only the face which must be of ‘tropical hardwood’ in tropical plywood.
Which brings me back to the role of plantations. A steady supply of peeler logs with few knots and good straight form would be desired. The forester’s supply to market needs to better match the rate that the industry consumes, or vice versa. We have seen successful products based on newer species in recent years, such as poplar, paulownia and parica, not hiding under a tropical veneer but as products in their own right.
The mills can eventually accommodate a range of species, if they are consistently available. As the foresters respond to warnings of a changing climate the mills can remain open to new developments and opportunities as the species mix shifts.
After all, it is a good opportunity to get back to our favourite game of optimising, with a new set of species, new wood chemistry and a shared global challenge.