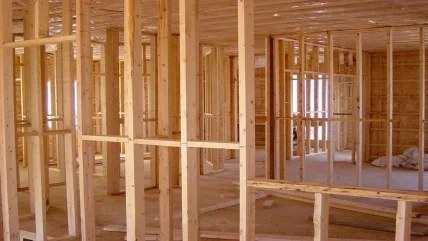
Given their own current experiences, Europeans may be perplexed by the upbeat tone that seems to prevail throughout most of the North American market for wood products early in 2013.
North American producers of lumber, plywood, OSB and MDF/HDF have exhibited considerable euphoria in recent months. Over the past 15 months, FOB mill prices for a whole host of forest products have climbed, and in some cases even soared, to flirt with past peak levels (at least on a nominal or unadjusted-for-inflation basis). Not a bad reason to be euphoric after years of despair!
Some examples: since the end of 2011, key commodity wood products prices have rocketed – in some cases by more than 100%. OSB prices have displayed the greatest strength with 7/16in OSB up 142% between the end of 2011 and the end of February 2013, climbing from US$173/m3 to US$418/m3.
At the February level, OSB prices were just 15% off the record pace of US$495/m3 set at the last cycle peak. Other wood products enjoyed substantial, but more moderate, increases over the same 14-month period.
Plywood prices are up over 40%, softwood lumber prices 50-65%, depending on species and grade. Table 1 illustrates several softwood lumber, LVL and panel prices; how much they have changed since the end of 2011; and also how close they have come to matching or, in the case of particleboard and MDF, exceeding their previous cyclical peaks.
Clearly this improvement in producer pricing has had major impacts on industry profitability. After several years of struggling to reach break-even levels, most North American panel- and saw-mills are profitable.
Why this turnaround? The answer lies with the shifting balance between demand and supply for each product. The collapse of the US housing market (the single largest market for most wood products) after 2005, illustrated in Figure 1, was followed by declining production and substantial capacity attrition. As producers struggled for several years to balance supply with declining demand, they permanently closed many older and less-efficient facilities and moth-balled other capacity.
The drop in demand ended in 2009 and subsequently we have seen a hesitant and slow recovery that finally gained firmer momentum in 2012, especially in the second half. However, just as supply adjustments lagged plummeting demand when housing slipped to its recession-low in 2009, so has operating capacity been slow to climb as demand has recovered modestly since 2009.
Given the painful experience of the severest depression in the wood products industry in decades, and several false starts in the market recovery, North American lumber and panel producers have been hesitant to increase production by adding back shifts at operations currently running sub-optimally, let alone reopening mothballed capacity. The fear that increased supply would again depress prices to sub-cost levels has resulted in highly cautious management which needs to be convinced "this recovery is indeed for real"!
North American production of lumber in 2012 climbed 8.5%, from 112.6 million m3 in 2011 to 122.2 million m3. However, lumber production in 2012 was still 31% below its 2005 peak! Similar stories can be told for all other wood products – year-on-year increases in 2012 production of around 10% for growth products such as OSB and MDF; and much smaller increases (2%) for mature products such as softwood plywood.
Two products were data outliers; North American LVL output jumped close to 20%, but particleboard output slumped 6%. Despite these overall increases, 2012 production ran 20-45% below previous peaks (generally recorded in 2005-6 when housing starts reached their apex). Table 2 summarises key production data for lumber and panels, as well as US housing starts. Of interest is the fact that 2012 US housing starts were up 28% over 2011, a much larger increase than for production of lumber, LVL or any panels tracked.
Looking Ahead: Outlook 2013-15
Producer attitudes started to shift markedly in the second half of 2012 and this move has gained further momentum in 2013 as companies have announced plans to re-open sawmills and OSB operations. Driving these changed attitudes were not only higher product prices and improved profitability, but also the growing belief that the recovery in new residential construction and R&R (residential repair & remodelling) demand for wood products will be sustained. At year-end 2012, monthly housing starts had reached a rate of 900,000 units, up from around 700,000 at the end of the previous year, and it looks as if US conventional housing starts will climb above the one million unit threshold during 2013. The forecast used here assumes 1.075 million starts for the whole of 2013 and close to 1.5 million in 2014 (Figure 1). This is a much more bullish outlook than the view one year ago and reflects the elimination of much of the excess US inventory of unoccupied homes.
These projections may also be somewhat stronger than the assumptions being entertained by many lumber and panel producers, but providing the monthly housing reports continue to be positive, then we expect corporate housing forecasts to be revised higher as the year passes.
Nevertheless, US housing starts will remain well below their historical peaks, while the mix of units built will be heavier to less-woodintensive, multi-family, units rather than to wood-intensive, detached single-family homes. But whatever the mix, an increase in total housing starts will add considerably to wood product demand over the next few years.
Growing residential R&R activity will also supplement the increases in new residential construction in driving wood product demand higher (Figure 2). Lastly, non-residential construction demand should also turn the corner soon and add to total demand, while industrial markets will continue to expand, albeit at a moderate rate.
Despite this improvement, demand will not match its recent historical peaks any time soon, but nor will supply (production plus imports)! Consequently, focusing on the fact that both US housing starts and wood products production all remain well below their historical peaks is largely irrelevant to analysing current markets.
The painful adjustments made to capacity, and therefore production, during 2006-10 mean the market for lumber and panels in future will be determined by the change in demand yearon- year, rather than the absolute level of demand. And it is this change in demand, in relation to the change in supply, that will continue to determine pricing behaviour.
Sawmills and panel mills are being reopened and shifts are being added to already operating facilities, but the painful experiences of the past several years will likely continue to hinder the production response over the next year or two. If the increase in supply continues to trail the increase in demand in 2013-14, then North American lumber and panel prices will break previous records across almost all product categories.
Only if demand grows more slowly than expected (eg if housing starts move sideways rather than higher), could there be significant downward pressure on product prices as the ramp-up in supply, at least temporarily, outpaces the increase in demand.
OSB Case Study
This assessment is particularly relevant to the OSB industry in North America. Price increases for OSB have outpaced those for all other lumber and panel products, in part reflecting their low starting point in late 2011.
However, demand growth in 2012 was relatively moderate (in the range of 10-12%), even as prices soared 100% as dealers, distributors and builders scrambled to cover their needs resulting from a better-thanexpected rebound in residential construction activity. As a result of limited production (and insignificant levels of imports from offshore), stocks of OSB panels throughout the distribution system were drained. Consequently, OSB mills were able to maintain surprisingly solid order files through most of the year as buyers were forced to place orders on a frequent and steady basis in order to cover their growing needs.
In response to the best profitability in several years, OSB mills have added shifts at operations which were running at sub-optimal levels (below seven days a week), and companies have started to announce that they will re-open ‘moth-balled’ capacity, that is those mills that had been closed indefinitely in the period 2006-09.
As of mid-March 2013, we count seven OSB operations that are either in start-up or that will be re-started later this year or early in 2014. Three of the operations are located in the US (Georgia-Pacific, Manning, South Carolina; Louisiana-Pacific, Thomasville, Alabama; and Norbord, Jefferson Texas). In Canada, we count four re-starts (Arbec Forest Products, Miramichi, New Brunswick; Ainsworth, High Level, Alberta; Tolko, Athabasca, Alberta; and Louisiana-Pacific, Dawson Creek, BC. (The L-P Dawson Creek mill is not a firm announcement, but the author believes this mill will most likely be running by the spring of 2014). In total, these seven operations represent an additional 3.79 million m3 of capacity.
However, this capacity addition does not equate immediately to an equivalent increase in OSB production. It will take several quarters after mills do re-start for them to approach their nameplate capacities. In some cases, this ramp-up curve could be longer than a year, particularly if a moth-balled operation had received only minimal maintenance during its closure. Table 3 represents an attempt to balance the anticipated increase in OSB demand through 2015 with the anticipated increase in North American OSB production.
For demand, given our US and Canadian housing starts assumptions, North American OSB consumption is expected to climb from around 15.3 million m3 in 2012 to 22.5 million m3 in 2015 – growth of 47% over three years.
The growing market will also require a larger operating inventory through the distribution network to service this expanding market (and to replenish inventories depleted through 2012 and early 2013). Adding inventory change to actual consumption, we estimate that the actual demand for OSB placed on North American mills (and offshore suppliers) will climb 51% from 14.9 million m3 in 2012 to 22.6 million m3 in 2015 (Figure 3).
How can North American mills supply this growth? Assuming the 2012 production of 14.9 million m3 as a base line through 2015, to this can be added increased output from those mills running short-time in 2012 as they all transition to seven-day operations. This development is estimated to add 2.1 million m3 of production per year by 2014. The re-start of the seven facilities listed above will add an estimated 1.16 million m3 of production in 2013, 3.20 million m3 in 2014 and 3.59 million m3 in 2015 (Table 3). For all mills, it is assumed that the OSB industry will average an operating rate equivalent to 95% of rated capacity in 2014-15.
In total, North American supply (production) will therefore climb from 14.9 million m3 in 2012 to 17.6 million m3 in 2013, 20.2 million m3 in 2014 and 20.6 million m3 in 2015. For each year we consequently estimate a supply shortfall will prevail. This shortfall will be a modest 0.86 million m3 in 2013 and a more significant 2.0 million m3 annually in 2014-2015.
Given this imbalance it is hard to expect near-term softening in OSB prices, or reduced price volatility. The anticipated experience with price behaviour in 2013-15 could well be similar to that of 2003-04 when OSB prices peaked even though both housing starts and OSB demand did not reach their peaks before 2005-06. The weakening price behaviour at the last cycle demand peak reflected the fact that total supply had caught up with demand after the initial jump in prices as offshore imports of both plywood and OSB surged to supplement higher domestic production.
How can the anticipated 2013-15 supply "gap" be filled, other than by substantially higher prices that force users to either substitute other products for OSB (eg softwood plywood) or simply defer projects? Three factors will come into play as markets either strengthen further or even if they simply remain close to recent peaks.
First, "capacity creep" can be expected at existing mills as the pressure to debottleneck production lines will be reinforced by the desire to sell more panels to customers. "Creep" of 1% per year on a compound basis would add approximately 0.2 million m3 annually to the North American OSB capacity base. This could represent as much as an additional 0.5 million m3 of production by 2015.
Second, other moth-balled capacity could be re-opened. There is approximately 2.4 million m3 of potential capacity to be reopened, above and beyond that already announced. In addition, Ainsworth is resurrecting the possibility of constructing a second line at Grande Prairie, Alberta. If built, this would add over 500,000 m3 of capacity. However, start-up before 2015-16 is unlikely, given the need to first secure capital.
Third, offshore imports could also help fill the void. OSB supplies, either from Europe or from South America, could be supplemented by increased volumes of substitute products such as sheathing plywood from Brazil. Note: at the cycle peak in 2005, the US imported 1.38 million m3 of plywood from Brazil, 0.49 million m3 of OSB from Europe and 0.17 million m3 from South America (largely Brazil). While Brazilian plywood capacity has contracted since 2005, OSB capacity in both Europe and South America has expanded. At the same time, European OSB producers are facing a prolonged economic recession, which may dampen local consumption.
Conclusions
Many assumptions on both the demand side (eg the pace of the housing recovery) and on the supply side (eg slower or faster start-ups of re-opened mills) are not hard and fast. Alternative outcomes could lead to a significantly different set of market scenarios over the next three years than that suggested here. Possibly the North American OSB market may not have to continue to scramble to secure supplies beyond this spring. However, without a larger than expected increase in supply, or greater than expected substitution, OSB markets are likely to continue to experience: continued pricing strength; great price volatility; and high overall profitability.
In turn, North American plywood producers will continue to enjoy spill-over benefits from strength in OSB markets, with upward pressure on their prices. Lumber, EWP and MDF producers will also enjoy substantial improvement in volumes, pricing and profitability as the US housing recovery gathers momentum over the next two to three years. And eventually the euphoria will spread to reach the North American particleboard industry, as domestic production of both furniture and cabinets rebounds.