Efficient transport of panels through the various processes in a factory is of course key to the efficiency of the whole operation.
Founded in 1986, EMG (the name stands for Engineering Manufacturing Group) set about specialising in that field and the end of April 2009 saw the completion of its biggest and highest-speed project to date, at Nelson Pine Industries MDF line in New Zealand.
Murray Sturgeon, managing directory of Nelson Pine in Richmond, Nelson, takes up the story.
“The background to this project was developed when we visited the Ligna exhibition in Hanover, Germany, in 2007,said Mr Sturgeon when interviewed at Ligna this year.
“Nelson Pine Industries’ objective was to install a new sander line from Steinemann and a new cut-to-size saw line to complement the existing MDF finishing line, consisting of three Steinemann sanders, two saws and packing lines. This would enable us to sand, cut and pack the total output from our three Küsters continuous press lines, producing 1200m3/day over seven days, in a finishing line operating on day-shift only over five days, Monday to Friday.”
Mr Sturgeon went on to explain that to feed the new sander line required a high-speed panel feeding and stacking system.
“I had witnessed EMG sander infeed equipment, introduced to me by Mr José Lobo of Tafisa Brazil in operation in their plant at Piên in Brazil and was satisfied that EMG could handle our requirements,he said.
The Steinemann Satos sanding line was itself a major project, having 14 heads and a designed maximum running speed of 150m/min.
“To this end, at the time of placing our order with Steinemann, and for the saws, Nelson Pine Industries Ltd favoured EMG to supply and supervise the installation of our panel handling equipment, which incorporated EMG’s patented Sequential Panel Feed System to reach sander throughput speeds of 150m/min for thin panels,said Mr Sturgeon.
“I am happy to report that our programme was completed in March 2009 and all plant and equipment is operating to our satisfaction and at Nelson Pine Industries Ltd we have reached our objective and now process all MDF on a five-day-per-week basis.”
The line that EMG supplied for the sanding operation included loading and unloading stations, transport to and from the sander, and a system to guarantee that only one thin board feeds into the line at a time, explained Marco Conzadori, sales manager and son of one the founders of EMG.
“The sanded master panel is 2.75×7.3m. The complete line took only three months to assemble on site, including all the mechanical and electrical work,he explained.
Other recent contracts for EMG include all panel handling after the Dieffenbacher continuous press for line 3 at Eucatex’s mill in Brazil, with delivery completed in July this year, and handling for an Imeas sanding line for a Russian client, which was due for delivery in August.
While the panel industry provides the vast majority of EMG’s work, the company has also employed its handling expertise in the steel sheet industry, where the synergies are obvious.
Four years ago, the company branched out into a completely different field with the design and manufacture of a gun cartridge filling line, bringing automation to what had previously been a largely artisan-based operation.
Returning to the panel industry, EMG has other projects in the pipeline, including one of similar size to the Eucatex order, and was expecting a down-payment from the client imminently at the time of WBPI’s visit to Cremona in June.
“South America is traditionally our main market, though Russia has been growing for us recently,said Mr Conzadori. “We have also had a lot of interest from India.”
That South America is important is illustrated by the fact that EMG has its only manufacturing operation outside Italy located in Curitiba. EMG do Brasil was set up in 2007 and today employs 32 people, while the Cremona operation employs 35. One of the main products made in Curitiba is a conveying system for chips in the green end of panel mills.
Globus of Italy, a manufacturer of wood size-reduction machinery, is moving the manufacture of its smaller machines to EMG do Brazil, which also produces lines for pellet production.
Mr Guido Conzadori, Marco’s father, is leading the business and reflected on the current market.
“We are a young company in years but not in experience,he said. “At the moment, in spite of the global crisis, we have used our flexibility and skill to cover our manufacturing needs until the end of 2009 and possibly half-way through 2010. This is largely due to our special relationships with our customers/friends, like Nelson Pine, Duratex, Eucatex, Outokumpu and so on, who have helped us to promote our success.”
Close cooperation with other companies, such as Arco International of Pontevico, Brescia in sawing systems, and the creation of Novopellet as part of the group to produce pellet systems, has helped EMG to weather the economic storm and to fill the extra 33% of extended factory space which the company opened in June 2008.
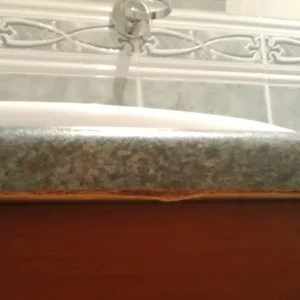