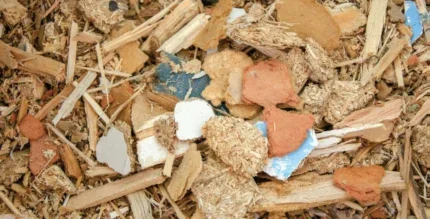
The prospect of real, commercial solutions arriving to solve the growing problem of consumer waste fibreboard are getting stronger all the time.
After extensive coverage charting of the journey of UK-based technology company MDF Recovery, which has developed technology to separate waste MDF fibres for re-use in new products, we are now seeing some landmark milestones.
This started last year with MDF Recovery’s (MDFR) agreement with prolific global recycling technology business PAL (part of the Italy-based IMALPAL Group), providing the latter with exclusive rights to integrate the MDFR process with its own leading wood cleaning and recycling technologies.
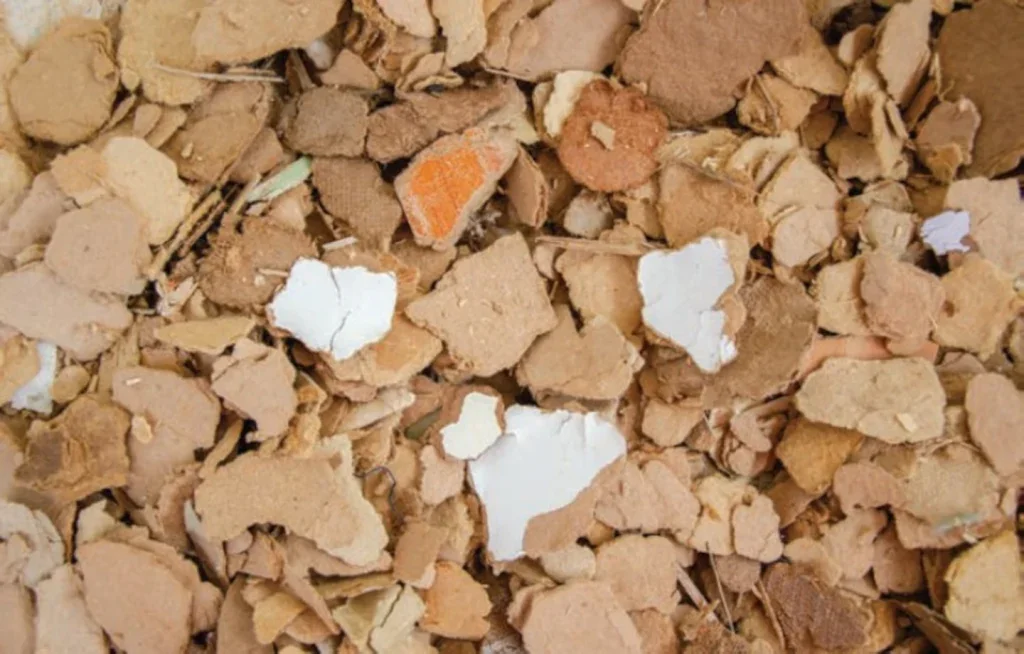
It is now being followed by the first commercial contract for recycling MDF fibre for use in the manufacture of woodfibre insulation.
The latter development will see PAL supply MDF recycling technology to UK MDF mouldings manufacturer W Howard.
We caught up with PAL to speak about the latest developments and ask its thoughts on where the trajectory on waste MDF recycling is going.
PAL AND MDF RECOVERY PARTNERSHIP
It was in May 2023 that PAL and MDFR announced their new partnership, providing PAL with the rights to integrate the MDFR fibre recycling process with its own leading wood cleaning and recycling technologies.
MDFR’s technology has, of course, been promoted as the world’s first low energy, low water solution for the effective recycling of waste MDF.
The deal is designed to give customers in the wood-based panels industry the ability to specify a complete ‘end to end’ recycling solution for this challenging waste stream, effectively allowing them to reduce costs, enhance both product and corporate sustainability and address the needs of the circular economy.
Waste MDF normally either ends up in landfill or incineration.
Luca Ballarin, of PAL, updated WBPI with the latest on the company’s work in bringing the solution to the commercial area.
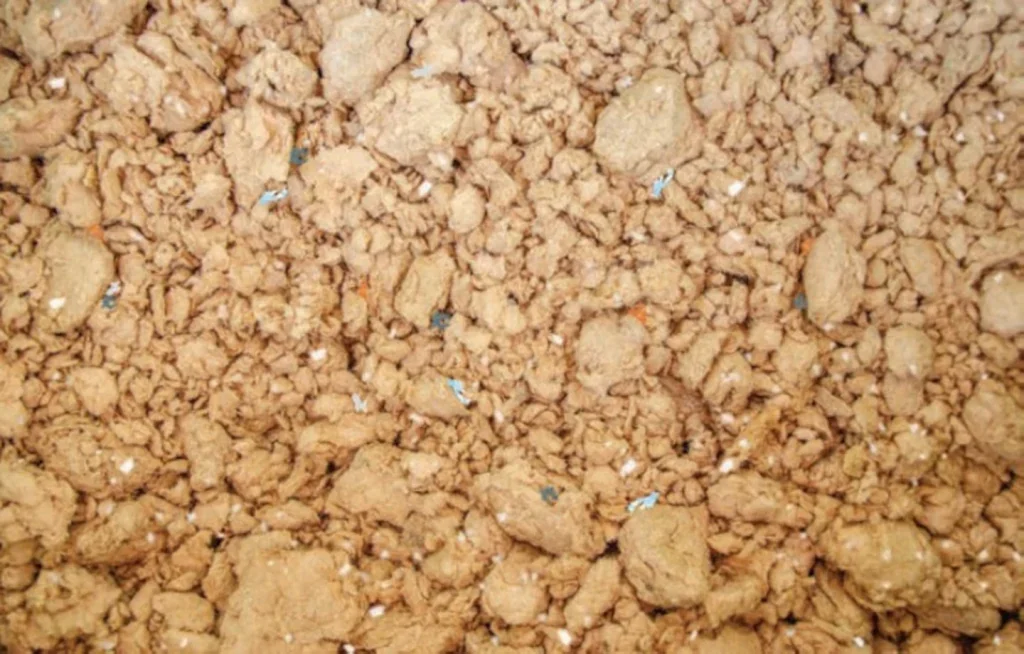
Mr Ballarin said PAL’s extensive experience in recycling technology had seen it heavily involved in the early days of using recycled wood in the particleboard industry, particularly in Italy where PB production uses a lot of waste wood.
It has since sold systems around the world.
“One of the key points of PAL is our research team working in the lab,” he said. “Many new materials and requests are coming all the time to the PAL lab.
“We’re also working on systems for municipalities (concerning consumer waste) and in biogas. People were burning all the material, but as legislation changes, the trend is to recycle more wood.”
PAL had already developed a sorting system to separate waste MDF from other waste wood, as this is a crucial requirement for PB manufacturers who do not want waste MDF fractions contaminating their waste wood material infeed.
“So, the question is now what to do with this waste MDF? It is a big issue.”
Mr Ballarin pointed out that major corporates such as IKEA are placing a high emphasis on the recyclability of the materials they use, creating demand for solutions.
But he said this raises questions on the quantity of the available MDF waste to be used for recycling and the economics of doing so.
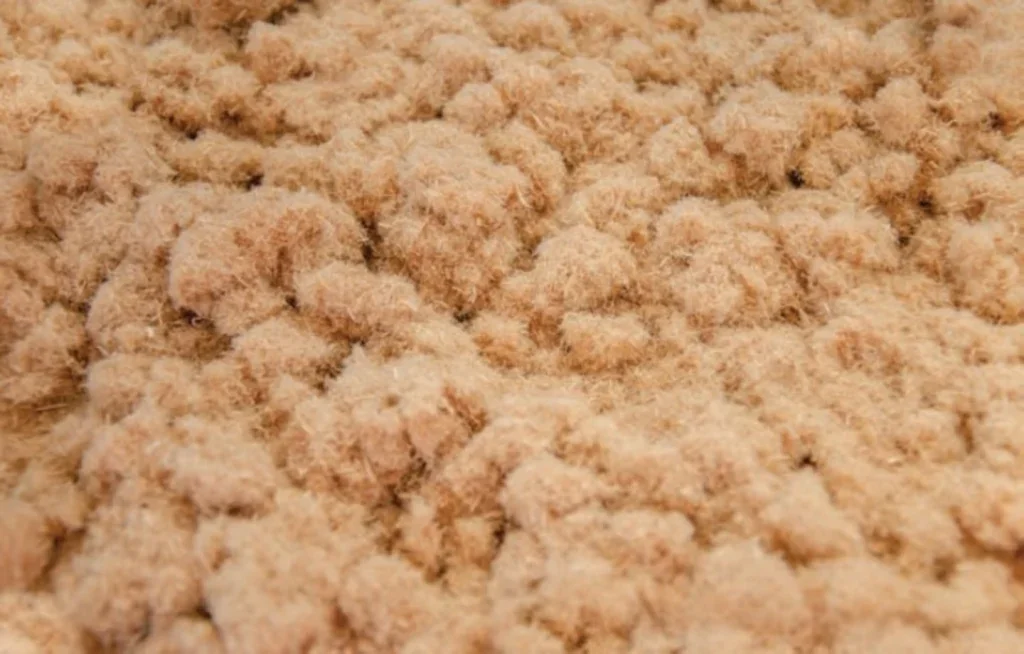
“Straw is available in very big quantities but may not be concentrated in the places where it can be used [by the panelboard sector]. The logistics are very important. It’s for this reason we think that a realistic starting point is to use between 10% and 20% recycled fibre in a new MDF board.”
“We are focused on not only MDF but also woodfibre insulation board. Systems which are also able to be used in the woodfibre insulation board sector give much more possibility for the use of the recycled fibre.
“Maybe the future will not be the building of very big fibre recycling plants but with smaller modular plants, segregating the fibre with different uses.”
When PAL visited MDF Recovery’s operational prototype fibre recycling plant, it was very impressed with the system.
PAL conducted a number of different tests using its cleaning technology in tandem with MDFR’s process and saw “very good results”. PAL places a big emphasis on sorting the waste MDF fractions into the correct size. To be able to clean the material efficiently, PAL says it is important not to have too small a dimension of waste fraction.
“We made a comparison with other systems available and were convinced this system worked in a very easy way, so we think with this system it is really possible to segregate the fibres with very little loss of material,” explained Mr Ballarin.
“The MDFR system is a very smooth process, with the reaction concentrating on the hydrology of the glue. This convinced us to work on it and we found MDFR to be a serious company.”
Hence the partnership was born. For MDFR, having PAL on board with its recycling and cleaning expertise effectively means a complete system is able to be supplied for the sorting, cleaning and recycling of MDF waste.
For PAL, it means the possibility to scale something that is already a working prototype, up to industrial scale for the commercial market.
In general terms, the process of recycling waste MDF fractions into usable MDF fibres centres on hydrolysis. Waste MDF fractions are immersed in hot water and energy used to break the glue bond, separating the fibres.
After this process, the recycled fibres undergo a selection process, and the chosen recycled fibre is cleaned/dried before being ready to use.
The whole recycling process is designed to create a waste fibre that has a similar moisture content as virgin wood.
The benefits of fibre recycling systems are not limited to being able to use waste MDF fibres, but also, says Mr Ballarin, in the efficiency of the system itself.
“We are able to recycle the water and the heat used in the system.”
FIRST COMMERCIAL CONTRACT
The difference in fibre recycling capacity from a prototype to a big plant is approximately from 150 kg/hr to about 2.5 tonnes/hr throughput, says Mr Ballarin.
The first commercial plant to be supplied will be between those two figures at about 750kg/hr, with a contract now signed between PAL and UK MDF mouldings manufacturer W Howard.
W Howard, a longtime supporter of MDFR, will set up a plant to recycle waste MDF and manufacture loose woodfibre insulation for sale. It represents a multi-year licence for W Howard, with the insulation product being sold in the UK & Irish markets.
“This project with W Howard gives us the possibility to scale up the MDFR system. We can connect the plant to the cleaning system to create a solution that is very sustainable in terms of energy and water consumption.”
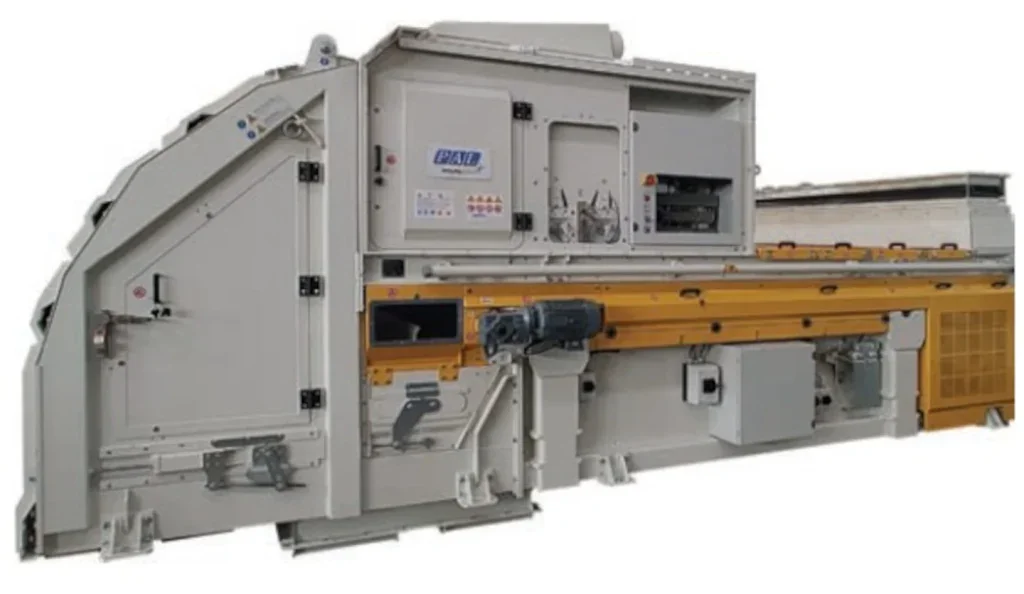
W Howard believes the new partnership will create an entirely new closed loop supply chain that can convert end-of-life MDF products back into wood fibre for insulation. This will also help to provide a much-needed new source of natural insulation – one of Europe’s fastest growing market sectors.
The new recycling facility is being sited in Newtown, Powys.
When W Howard announced its intention to build such a facility last year, Jonathan Grant, Group Chief Executive of W Howard, said the company was showing it was putting the environment at the very centre of its business.
“Once production begins in 2024 our valued customers will be able to buy our MDF products safe in the knowledge that they can be recycled at the end of their natural life, offering a closed loop supply chain,” he said.
TARGETING PANEL MANUFACTURERS
Of course, it is the intention of PAL and MDFR to supply complete fibre recycling solutions to global board manufacturers themselves.
“Now we can say that we are selling this system, so it is a real industrial system,” added Mr Ballarin.
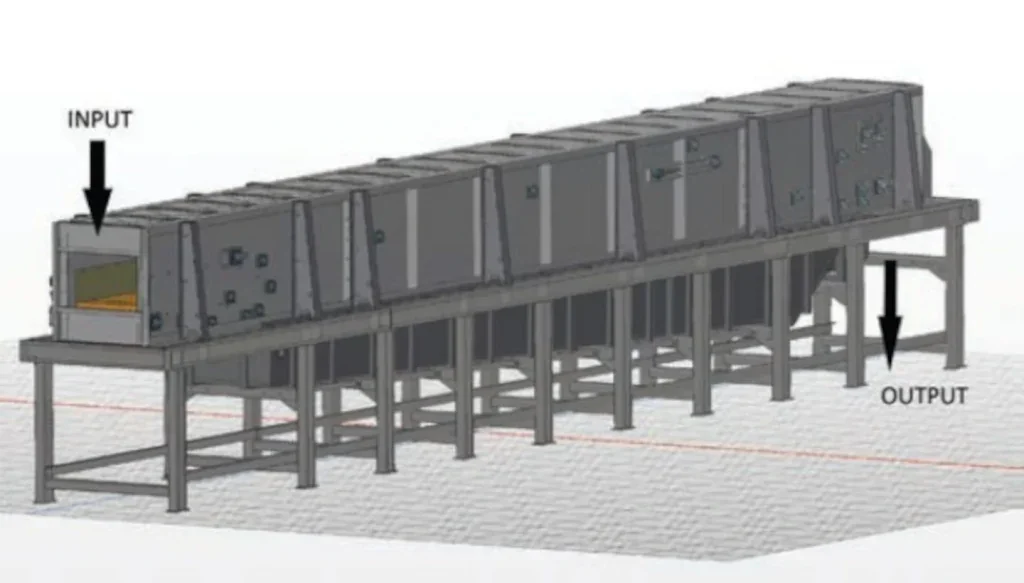
He said that MDF fibre recycling systems supplied for MDF production will be different to that supplied to that of the first UK project, with each commercial enquiry likely to have specific requests.
“We are starting to speak to MDF manufacturers with a view to technology supply and I think we will agree something maybe within 2024. Obviously, to have an industrial plant operating that we can show to the MDF producer is very important.
“We have many requests from companies asking to come and visit us and for meetings. We feel there is a high demand for this type of technology, and we will be ready for the next step within the MDF industry this year.”
One of the key questions from interested parties will be what the commercial viability is for an MDF manufacturer to invest in the recycling systems.
Mr Ballarin said board manufacturers can easily make cost comparisons between using virgin wood fibre and recycled fibres, while there were obviously energy costs to the MDF fibre recycling process.
But PAL says the return on investment on the technology itself is around three years – earlier if you use higher proportion of recycled fibre in a new board and waste MDF material can be sourced locally to the factory.
Material availability and costs will of course differ in different countries.
“This system is easy to adapt not only to an MDF plant but also for woodfibre insulation manufacture, and we are making interesting tests also for PB.”
Another reason why PAL & MDFR think they will find takers on the market is because it can supply a fairly small system without specialist operators and due to the advanced nature of the cleaning and sorting technologies.
PAL is also doing R&D with the hydrolysis technology on PB waste fractions but can’t yet go into detail on this but expects to update in the future.
In summary, PAL and MDFR have reached a major milestone in the commercialisation of the MDFR process, with a first project getting started in the UK and conversations happening with MDF producers about the potential supply of the solution for including recycled MDF fibre in new MDF board production.
“We are very excited in PAL about this project,” concluded Mr Ballarin. “We know competition is strong and it is not an easy project, it’s ambitious for sure. But we are completely sure we can bring our expertise to a success in this application. This project involves PAL 100% and involves the whole IMALPAL Group.”