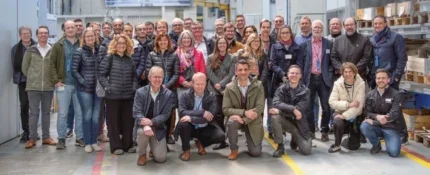
How to handle the problem of waste fibreboard has been one of those major conundrums in recent years.
MDF and HDF have been a great success as materials for the furniture and surfaces industries – the smooth and easy to finish nature of fibreboard has seen it become a firm favourite. Indeed, global fibreboard production is in the region of 100 million m3 per year.
Of course, refurbishing and remodelling work also results in older furniture and interiors containing fibreboard move into the waste stream, and this waste is becoming considerable.
The fibre and resin composition of fibreboard creates a difficult problem for recycling and is perhaps the last great problem to solve in the wood recycling arena. Currently, burning the material is the default, with smaller volumes recycled in particleboard production.
New fibreboards are therefore made mostly from refined virgin wood – harvested from the forest and processing residues from sawmills and plywood manufacture.
A flurry of R&D activities has been springing up in a bid to solve the problem with WBPI taking a keen interest in their progress over the past few years.
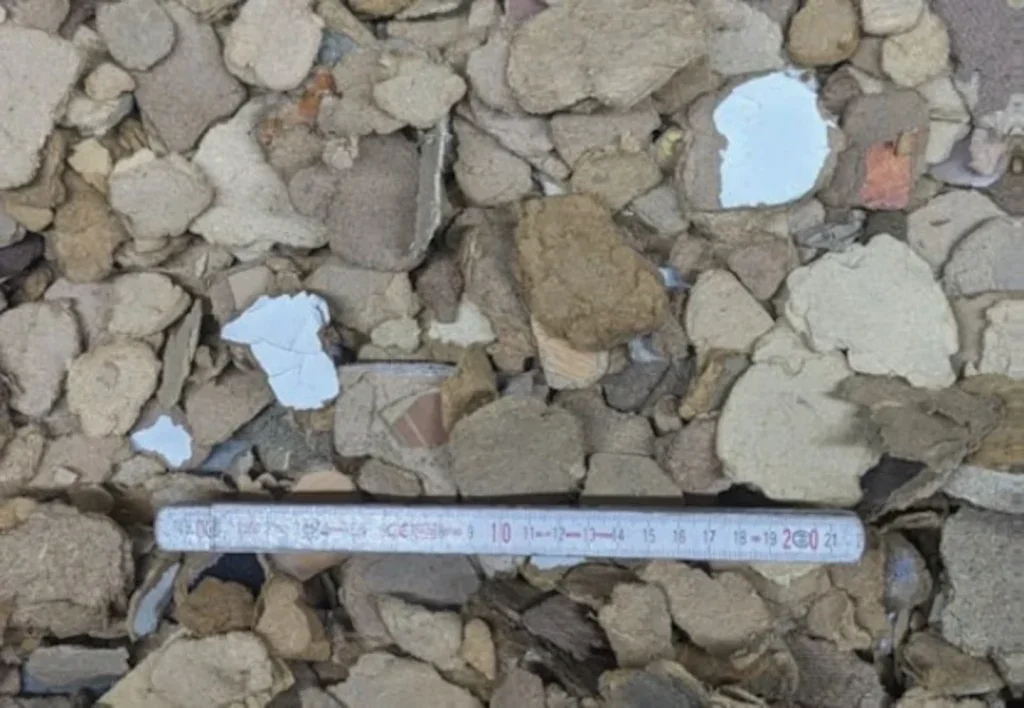
The largest multi-partner R&D approach, an EU-funded initiative called EcoReFibre, was launched in 2022 and runs until 2026. Five highly promising pilot studies are involved.
Funded by Horizon Europe, EcoReFibre explores smart technologies to recycle postconsumer waste wood back into fibreboards and other panel products (particleboard, biocomposite construction blocks, cyclic thin board, flexible woodfibre insulation products and hardboard).
Basically, the aim is to increase available wood resources in Europe through recycling and substituting up to 25% of the virgin fibres currently used in the European fibreboard market.
The project comprises 20 partners across seven countries, including industry, research institutes and industry associations – all of which are mentioned at the end of this article.
The industry partners include key technology partner Dieffenbacher and the wood-based panels producers Sonae Arauco, Homanit, Smartpanel and Soprema.
Research partners include Swedish University of Agricultural Sciences (SLU), Ecole Supérieure du Bois and Institut für Holztechnologie Dresden, while the European Panel Federation is also a key supporter.
STEPPING STONE – SORTING THE WASTE WOODSTREAM
In April this year, EcoReFibre said a significant step forward was taken when the consortium assembled at Dieffenbacher’s Eppingen base to demonstrate and discuss interim results of the research project. This event, coupled with a further meeting at waste sorting systems specialist Tomra in Mülheim-Kärlich showcased the work done so far.
Project co-ordinator Stergios Adamopoulos, professor, wood science at the Swedish University of Agricultural Sciences (SLU), summarised.
“The project progresses very well,” Prof Adamopoulos told WBPI.
“We successfully passed the mid-term review with the European Commission, and now the consortium focuses its efforts in preparing the pilots and demos as we are gradually leaving the laboratory status.
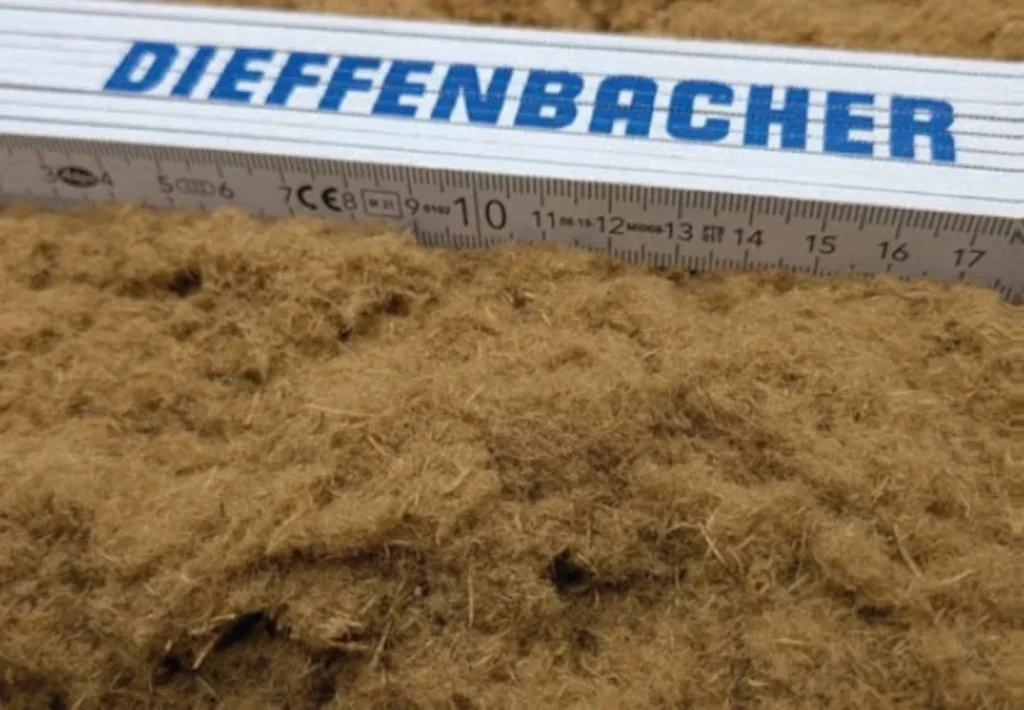
“EcoReFibre achieved its first industrial demonstration last April. For example, post-consumer wood waste was successfully sorted in terms of purity and yield into three fractions at Dieffenbacher’s partner Tomra: fibreboard fraction; solid wood fraction; and others (principally particleboard, plywood and other wood composites).”
The Dieffenbacher team, including Jonas Réssy, Dieffenbacher technologist and Jean-Christophe Zimmerman, head of sales Business Unit Recycling at Dieffenbacher, shared more detail on the company’s work in the project.
The company is a major global player in supplying wood-based panels production technology and has a constantly expanding recycling solutions business.
“We are already involved as a big player in waste wood recycling technology for particleboard production and that’s why we are taking part in this fibreboard recycling initiative,” explained Mr Réssy.
“There is a big potential for fibreboard recycling not only for MDF, but HDF as well. We get a lot of requests from our customers about this and the industry in general.”
Mr Réssy said no one currently knows what to do with fibreboard waste, except burn it. Material utilisation for this waste has not been possible to date, he adds.
“We can use waste wood in particleboard production, but the particleboard producers do not want to have large amounts of the waste MDF in their waste wood stream because it creates quality problems in their new PB boards.
“That’s why most of the material is selected at the waste collection site. It’s a pity because there is a lot of waste fibreboard and it’s a high-quality board.”
Increasing environmental and recycling initiatives in Europe have seen some big corporates names initiate sourcing and recycling policies not just for plastics but also other materials such as fibreboard. Giants like the Schwarz Group – owner of LIDL – and IKEA are two companies who have enacted strict policies on recycling as part of their overall green targets.
The message is clear – if a material can’t be recycled/reused then it’s viewed negatively in terms of the green circular economy and companies’ environmental profiles.
The demonstration at Dieffenbacher in April represented the culmination of phase one – sorting of materials in the waste wood stream. A line was built for cleaning and sorting the waste wood stream into solid wood fractions to use this for MDF production, to increase the recycling content of fibreboard.
“Then we sort out of the waste wood stream a pure fibreboard waste fraction to use for the fibreboard-to-fibreboard recycling,” said Mr Réssy.
Fibreboard material was shredded to chip size in the single-shaft shredder designed by Dieffenbacher. The chips were then fed into a Dieffenbacher ClassiSizer which reduces the fibreboard material to the desired particle size. After final screening on a Dieffenbacher oscillating screen, the fines produced can be used for the surface layer in particleboard production.
The demo then focused on fibreboard-tofibreboard recycling. Using a Dieffenbacher ClassiScreen, the waste wood provided by EcoReFibre project partner Veolia was separated into fines, chip-size and oversized fractions. In the same step, films, textiles and other lightweight materials such as paper were removed from the waste wood.
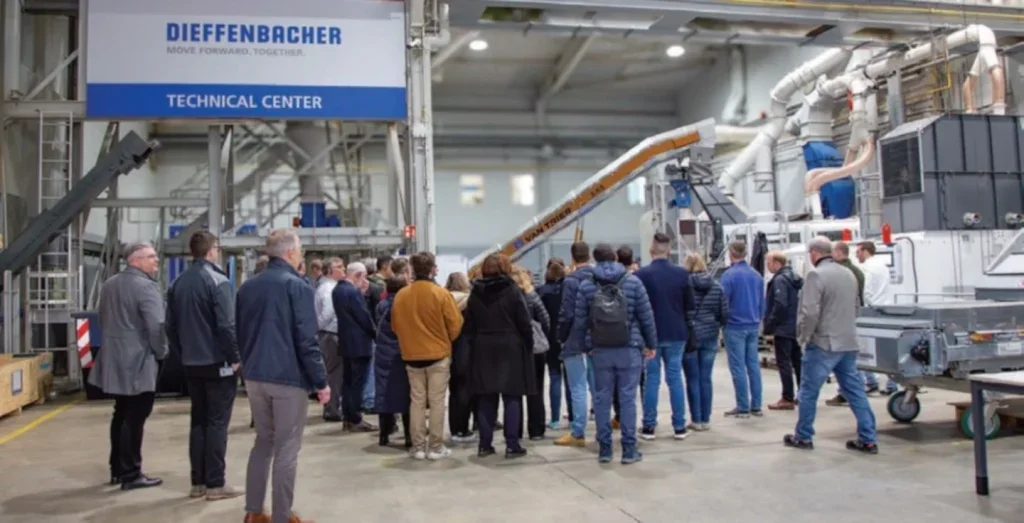
The chip-size material from the demonstration was made available to Tomra for the next day’s demonstration.
Tomra demonstrated sorting the recycled wood by type. Using its X-TRACT X-ray sorting machine, Tomra showed how impurities such as stones, glass, plastics and metals are detected based on their atomic density and efficiently removed from the recycled wood.
The next sorting step was performed with the intelligent GAINnext deep-learning technology, which is designed to reliably identify different types of wood, for example, solid wood or fibreboard, based on shape, size or other visual characteristics. GAINnext recovered unprocessed wood, referred to as wood A, from the mixed wood fraction collected by the X-TRACT™. In the third and last step, Tomra’s GAINnext effectively sorted and purified MDF from the processed wood B.
Dieffenbacher had already been working with Tomra for wastewood cleaning for PB production, with the latter’s technology being incorporated into the former’s lines for wood-based panels customers.
“Tomra had already started to sort out fibreboard from the wastewood stream before fibreboard recycling became a topic,” said Mr Réssy.
Development of new sorting technology incorporating AI, such as Tomra’s GAINnext, proved key in being able to sort pure fractions of solid wood and fibreboard.
“One of the biggest difficulties was the step from NIR sorting technology to the use of the latest AI technology,” said Mr Réssy.
This use of deep learning with cameras to correctly identify waste fractions was already being developed prior to EcoReFibre but the project was an ideal opportunity to test and develop it for creating a pure fibreboard waste fraction.
“It’s not possible to create a pure fibreboard waste fraction without deep learning, the sorting quality is not good enough.”
With this method, the image database needs to be comprehensive, and the system requires training to identify the different waste fractions.
PHASE 2 – RECYCLING FIBRES
After successful sorting of the waste wood fractions, the second and current phase is recycling the fibreboard fraction waste for re-use in new panel products.
A first prototype machine to break up the glue and expose the fibres has already been tested and a second larger prototype in industrial size is now being assembled in the Dieffenbacher’s Technical Centre. A demonstration of the fibre recycling process is planned by EcoReFibre in April 2025.
“At the beginning of the project we investigated all existing research projects on recycling fibre, and we then decided on our approach,” added Mr Réssy.
“We are not using a water bath, but steam instead to hydrolyse the glue because you need to have some moisture to break down the glue, using as small amount of water as possible.
“MDF is a high-quality board but fortunately most of the glue is water soluble, this is why we are using the steam to keep the water consumption as small as possible.”
Jean-Christophe Zimmerman, head of sales Business Unit Recycling at Dieffenbacher, believes the end result of the project will be a commercial application for use in the industry.
“Since we started on EcoReFibre we see we’re in a good position for the reuse of fibreboards in an industrial process,” he s aid.
“Of course, in the end it needs to be economic for industry. The project is still ongoing, and we have approximately two more years to reach the milestones and our goal is to arrive with an economic process for the industry.”
After the next demonstration in April 2025, the plan is to produce up to 160 tonnes recycled material such as recycling fibres, recycling fines and recycling solid wood to supply to project partners like Soprema, Sonae Arauco and Homanit for test use in the industrial scale production of MDF, HDF and woodfibre insulation boards with 25% recycled fibre content from December 2025. Some limited test boards have already produced in the Ecorefibre project.
The performance quality of the boards produced with recycled fibre, Mr Zimmerman added, was as good as with virgin wood fibre. There are of course further trials needed to proof this performance.
Mr Zimmerman explained that the level of recycled waste wood in PB production had initially started with lower percentages before increasing to levels now approaching 100% by some Italian producers.
“As soon as we see it is a proven process with the 25% recycled fibre, I’m pretty sure the goal will be to use a higher proportion of recycled fibre.”
An important factor will be the cost and reliable availability of the recycled content.
Mr Zimmerman said that while most of Europe has waste collection and pre-sorting systems, many countries around the world are less developed.
Mr Réssy said there were different possibilities to increasing the recycled content of new fibreboards.
“We can use the recycled fibres, but we can also put solid wood waste in to increase the recycled content. So, effectively either fibreboard to fibreboard recycling or waste wood to fibreboard recycling.”
Potentially there is a lot of waste solid wood and waste fibreboard available. In the EcoReFibre project the focus is on fibreboard from waste wood, but in general also fibreboard production waste is possible to use for recycling.
“In Germany in the year 2020 we used only 17% of the waste wood for material utilisation and the rest was thermal utilisation,” he added.
“If we have a circularity or cascade use in the board production there is a big potential in the material supply.”
Mr Zimmerman said Dieffenbacher was excited about the EcoReFibre project and happy to play a role. “We’ve learned that you need partners to talk to about solving challenges.
“It is easier using solid waste wood as the recycled material,” added Mr Réssy.
“Real fibreboard to fibreboard recycling is the tricky part, but it is possible and we are happy being part of EcoReFibre and having this key role.
“It is not a research project that nobody cares about. There are a lot of requests from our customers for a solution to the fibreboard recycling.”
THE FUTURE
So, what can we expect to see in regard to fibreboard recycling in 3-5 years’ time?
“There will definitely be some MDF manufacturers with this technology in their lines by then,” said Mr Réssy.
“It will be Europe first, then maybe Asia because we have a lot of fibreboard lines there and perhaps South America.”
The economics of using recycled fibre versus virgin wood will obviously play a role in the timescale of technology takeup, but the ideal scenario is for both the economics and sustainability to converge.
More information and visibility on postconsumer fibreboard waste volumes are being sought. Part of the EcoReFibre project is a survey to predict fibreboard waste quantities accurately.
The initiative is based on Crowd Wisdom which relies on the collective knowledge and insights of a diverse group of people. By posing questions to a wide audience, EcoReFibre aims to tap into the wisdom of the crowd to create an accurate predictive model.
This survey centres around the lifespans of products containing fibreboard, from their initial purchase to replacement. The information collected will be crucial in better understanding the lifecycle of fibreboardcontaining products and, ultimately, in reducing waste and promoting sustainability in Europe.
Visit survey for more details.
Of course, EcoReFibre is one of several different initiatives looking at MDF recycling technologies, with different R&D approaches being employed.
“I think there will be one kind of fibreboard recycling in the future, but it could take some years before the industry will decide which is best,” said Mr Réssy.
“The first plants will run; the producers will need to optimise the process and in a few years there will probably be only one kind of fibreboard recycling. We are convinced of our steam solution, but of course it’s a new technology and it needs to be proven first.”
SONAE ARAUCO SEES THE POTENTIAL FOR USE OF RECYCLED MDF FIBRE
Leading wood-based panels producer and EcoReFibre partner Sonae Arauco is an enthusiastic participant in the project.
The company, which has MDF, PB, OSB and wood fibre insulation board production facilities throughout Europe, is working with EcoReFibre research and technology partners.
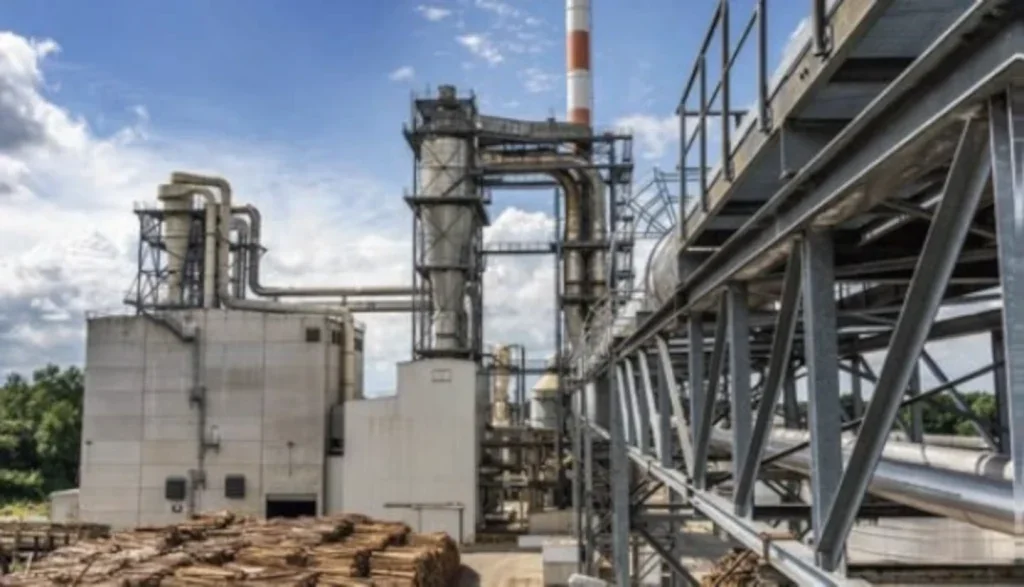
“Recycling is a strategic issue for Sonae Arauco, both in terms of our sustainability credentials and the company’s competitiveness,” it told WBPI.
“In this sense, in recent years we have made continuous investments to increase the incorporation of recycled wood in our products, both in our own recycling centres and in our industrial plants. As a result of these efforts, some of our product ranges currently contain more than 70% of recycled wood.”
One of the EcoReFibre targets – Dieffenbacher leading the development of an industrial process allowing the reuse of MDF in new particleboard solutions – is seeing Sonae Arauco involved in laboratory trials.
Sonae Arauco was responsible for carrying out all the laboratory trials to validate the possibility of incorporating reused MDF in particleboard and to find the best process for this reuse, which has now been completed.
The company is also conducting further laboratory tests, in collaboration with SLU, to define the conditions for using these used fibres in MDF solutions, including fibre analyses, the boards’ production and the boards’ analysis.
“This is a complex process, once the fibres are developed through two types of processes, one by Dieffenbacher and the other by IHD,” the company said.
“The potential is very high. The fact that so many renowned European players are working on this is directly related to the potential we have identified for the EcoReFibre project. The members of this consortium strongly believe that society needs to leverage a circular economy model and that, although MDF is already recyclable, there is great potential for growth in the recycling of MDF.”
Sonae Arauco says once the technologies have been validated and the conditions developed for industrial level production, it intends to trial industrial level manufacturing using recycled MDF fibre in both PB and MDF products.
ECOREFIBRE PARTNERS
Research partners: Swedish University of Agricultural Sciences, Ecole Supérieure du Bois, FCBA, NIBIO, Institut für Holztechnologie Dresden, The Swedish Environmental Research Institute.
Association supporters: the European Panel Federation, Innovawood, Federlegnoarredo and Steinbeis Europa Zentrum.
Industrial partners: Dieffenbacher, Sonae Arauco, Homanit, Smartpanel, Soprema, Cormatex, Biesse, Manifaktura, Veoila and MET4.