Adriano Stocco founded his business in 1979 in San Giorgio di Nogaro offering assembly, maintenance and repair services to the wood based panel manufacturing industry in Italy.
This led on to the design and development of pneumatic conveying systems and other specialised equipment fabricated from standard and stainless steel.
"At the end of the 1990’s we started to think about international markets as well as the Italian markets on which we had previously concentrated," said Mr Stocco. "Our products were already good for the international market and at that time I had new ideas for dryers, systems to be used in processing recycled waste wood and so on. These new ideas and innovations needed international markets."
The company’s international expansion soon spread to Nigeria, Vietnam, Canada, Germany, Ireland and the UK and now includes these countries and South East Asia, China and other markets too.
In June 2006, a major boost came for Instalmec’s international expansion plans when complete panel manufacturing line supplier Dieffenbacher of Eppingen, Germany bought shares in Mr Stocco’s business.
"With this agreement we were now ready to supply a very wide range of products, starting from the green area through to forming, including dryers, screening and gluing," said the chief executive.
One of the first fruits of this cooperation was a complete re-design of Dieffenbacher’s forming systems for OSB, which are manufactured in Instalmec’s factory.
"An interesting aspect of working with Dieffenbacher is the ability to increase our range of products through the relationship. We had a lot of ideas before the Dieffenbacher partnership but it brought a bigger market opportunity to develop these ideas and bring them to the market," said Mr Stocco.
From Dieffenbacher’s side, it has an experienced partner in designing and developing the relevant parts of its production lines and one that is located close to the ports of San Giorgio di Nogaro and Trieste, enabling cost-efficient transport to overseas customers.
A new product from Instalmec, launched at this year’s Ligna exhibition, is named ‘Ulysses+’. It is a completely new system for cleaning recycled wood.
This combines a rag separator, air gravimetric separator and pneumatic separator.
"This system has solved the problems of dust, of rags which could block rotary screens, and has eliminated all nets which could become clogged," said Mr Stocco. "This is because it employs an air gravimetric system."
The principle of Ulysses+ is based on separating the particles into three or four fractions, each with its own cleaning system, customised by adjusting the air flow to the type of material being cleaned. This means, says the company, that any kind of recycled waste wood can be accommodated in the system.
For instance, the pneumatic separator developed for fines removes those particles below 0.4mm to go to the dust silo for burning. Those above 4mm go to the particleboard production line.
Often contained among the fine dust is silica (sand) which will turn to glass in a furnace. However, Instalmec has also developed a special furnace to separate out the sand before that can happen.
The first Ulysses+ should be working at Xilopan’s particleboard mill in Italy soon after you read this.
Another new product for Instalmec is a pre-dryer to be installed before the drum dryer in particleboard mills. Having a pre-dryer is not a new idea, but previous examples have been of the omega type (referring to the shape of the pipe employed). Instalmec has designed a vertical pre-dryer to concentrate the drying effort on the larger core layer particles, without over-drying the surface layer material.
"This gives a big advantage in the press because it eliminates the problem of different moisture levels in the core material causing problems in the pressing process," explained Luca Zappetti of Instalmec’s sales department. "It also means you can run your press at a higher speed."
The pre-dryer also has a separation effect for plastic, stones and over-size wood pieces. The first installation of this pre-dryer was made successfully last year.
Other products of the company include dryers for MDF, particleboard, OSB and pellet production; combustion chambers (with the dryer or sold separately) which incorporate the silica extraction system; cyclone filters; pneumatic or mechanical screens; rotary glue blenders; and rotary valves for pneumatic systems.
The original basis of Instalmec’s business was in fabricating components out of steel sheet and this remains a core part of many of its products. Metering bunkers for particleboard or OSB are perhaps obvious examples.
Instalmec’s factory has already been expanded once and is soon to be further expanded, from 21,000 to 25,000m2, on an adjacent site. A 3,500m2 production building will form part of that development.
As the partnership with Dieffenbacher develops, and the range of Instalmec’s products increases, Mr Stocco anticipates that that space will soon be put to very good use.
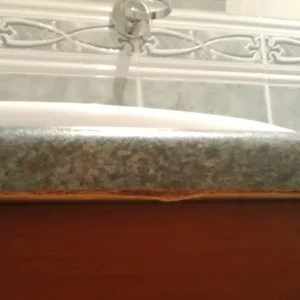