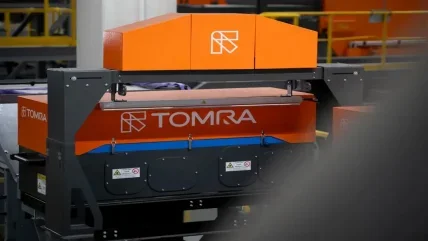
In 1972 two brothers, Petter and Tore Planke, founded the TOMRA company in Norway. It all began with developing a machine that could quickly and easily take back empty bottles and deliver a deposit refund receipt, in response to a request from a local grocer in the brothers’ home town of Asker, near Oslo.
Today, TOMRA says it operates globally and provides technology-led solutions that support the circular economy with advanced collection and sorting systems to optimise resource recovery and minimise waste in the food and recycling sectors (including the wood industry), as well as mining.
TOMRA was founded on that innovation in 1972, which began with the design, manufacturing and sale of reverse vending machines (RVMs) for automated collection of used beverage containers.
Today, TOMRA consists of four business units, of which TOMRA Recycling is one of those, and is dedicated to the production of sensor-based sorting machines for recycling businesses. More than 8,200 machines have been installed in more than 100 countries worldwide to recover plastic, paper, metal, glass and many more recyclables from waste streams.
In an interview with the wood segment manager at TOMRA Recycling, Jose Matas, and communications co-ordinator Michèle Wiemer, I asked Mr Matas why TOMRA decided to take its sensor technology into the wood sector.
“In 2012, we realised that by using the same technologies and sensors that we had already developed, suitably adapted, the wood and panels market could overcome the fact that the traditional sorting technologies could not create wood fractions that were of good enough quality to produce particleboard with a high percentage of recycled wood,” said Mr Matas.”Smaller amounts of recycled wood could be used, but the quantity was not sufficient.”
But, the use of recycled wood was becoming a necessity.
“Before, it had been optional to use recycled wood, but now there was a different situation because the cost and availability of fresh wood supplies meant that the industry was facing a difficult situation for the supply of fresh wood. The existing technologies could not meet the required standards [for the use of recycled wood],” explained Mr Matas.
“The NIR (near infra-red) and X-ray technology which we had already developed for other industries was suitable for wood sorting and, by 2012, there was this growing necessity in the wood panels industry to use recycled wood, not just for environmental reasons, but for economic reasons as well.”
Mr Matas pointed out that the coronavirus pandemic in 2020 added a new urgency to the use of recycled wood as supply chains were severely affected, causing delays in shipments of fresh wood and chips from Asia and America and other sources and thus increased costs for those shipments (sometimes more than the cost of the wood itself); and for the increasingly rare wood raw material. Demand exceeded supply and costs soared accordingly.
“Most European countries lacked an adequate domestic supply of wood and demand quickly began to exceed supply,” said Mr Matas.
“Then in the middle of all that, the situation with Ukraine and Russia started. We have sanctions on top of the existing problems so now there is a very, very difficult situation to get the material that the panel industry needs to keep the business running.
“Traditional wood and chip supplies from Belarus and Russia became unavailable, accelerating the demand for recycled wood. What, until then, had been an optional raw material for panel production became a very real necessity for the industry,” said Mr Matas.
“When we started [in the wood recycling industry] 10 years ago, we were the unique supplier of optical sorting technology to the industry,” said the wood segment manager. “We entered the market with our NIR and X-ray systems and once the industry realised the performance our technology offered, they realised this could help them to develop new solutions in their industry and to increase the possibility of using more recycled wood in their production.
“When we saw the potential in this market we saw another necessity for the industry, which was sorting the wood types. Before, it was just a question of cleaning the wood from impurities, but now we have this possibility to sort by wood types as well.
“However, the existing technologies the industry had were not good enough for the detailed sorting of recycled wood in this way.
“Traditional systems had relied on physical screening, magnets and wind-sifting to remove pollutants, but these systems only removed part of the contamination, still leaving pollutants which could damage the panel maker’s production machinery, and that of the end-user, while producing inferior quality boards.
“Now, with our technology, the panel industry could sort natural wood from processed wood and use, for example, natural wood for MDF production and processed wood for particleboard. Before it was possible to do this sorting, all the recycled wood was only used for particleboard.
“We are already working with multiple international players in the wood panel industry and the equipment that we are producing now is being welcomed by that industry,” said Mr Matas.
TOMRA also takes on a consultancy role, helping customers to find the best solution for their particular panel product needs.
I pointed out to Mr Matas that there was a lot of competition in the processing of recycled wood, from the large established suppliers of panel making machinery, among others, but he said that some suppliers in the market are in fact already using TOMRA’s technology in conjunction with their own physical sorting systems.
“Of course there are other suppliers of traditional sorting machines. The difference is that we are focused on optical sorters so we are not in direct competition, but those systems can be combined with and complement our optical systems.
“We know we are not alone in the optical market either, but we started in the wood industry 10 years ago, which has given us sufficient time to optimise our systems. Today, we now have a full wood sorting solution consisting of X-ray and NIR-based sorting systems that offers peak performance; and features leading to the achievement of unparalleled purity results,” asserted Mr Matas.
He went on to talk about TOMRA’s Deep Learning Technology. This is an artificial intelligence system, based on artificial neural networks that are trained to recognise images of all different types of wood such as MDF, particleboard, plywood and solid wood, as well as pollutants such as melamine laminate particles. It can also be trained, just as you would train a new human employee said Mr Matas, to recognise particleboard of all different types, thicknesses, moisture resistant (green pigmented) or fire resistant (red pigmented) and so on and to recognise specific pollutants in the wood stream, the removal of which is of particular interest to the customer.
“So, after being shown thousands of different varieties of the same product, this new employee will know exactly what is chipboard,” explained Mr Matas. “Then we do exactly the same with the rest of the wood types: with the plywood, with the melamine, with the MDF and with the natural wood. So after this training, this employee will be able to identify all the different types.
“So if we translate this to our technology, we have trained our machine in the same way. We have shown thousands of pictures of different wood types to the machine and the machine has learned to identify them all through its specific technology. And thanks to the computing power of the neural network that we have developed, the computer is able to do a similar task to a human. After the material is scanned and the information processed, the type of material will be identified and, depending on the sorting task that we tell to the machine, at the end of the process it will have sorted it.
“We were the first to offer this Deep Learning Technology for the separation of wood by type to the panel industry, and that is a unique selling point for our company,” said Mr Matas.
“A lot of companies are trying to recycle MDF back into MDF and it is a headache for the industry, because you can’t use MDF fibre in particleboard,” he said. “But thanks to our Deep Learning Technology, we can sort MDF fibre from mixed fractions.
“We will continue to develop and improve the sorting of MDF fibre to produce a very, very clean fraction, but this is really already a reality with our technology.”
Turning to the global markets for TOMRA’s sensor technology, I asked Mr Matas about the trends for the use of recycled wood around the world.
“Italy has been a leading country in the use of recycled wood for many years and recent legislation in Germany is forcing more use of recycled wood there,” he said.
“Spain also recently introduced such legislation and this means there is a strong increase in demand for sorting technology in these countries.
“On the other hand, the US has a huge production and consumption of wood and less than 10% of that is from recycled material, although there is a trend in California to increase recycling there.
“South Korea and Japan also have legislation about recycling but China apparently does not, although specific information is hard to come by.”
“Our USP is that our technology enables plant operators to define different combinations of materials they want to sort,” added Michèle Wiemer, communications co-ordinator for TOMRA’s wood segment. “Combined with our Deep Learning Technology, this adds a lot of flexibility to the sorting process.
“With regard to USPs, I think it’s also important to say that we have 50 years’ experience in circular waste management. We were the first to develop NIR sensors for waste sorting applications and we are continually developing that technology. I think that is something which makes us unique as well.”
Mr Matas continued: “The main solution that we offer to the market is first of all the X-ray because this is the best technology for separating wood from the impurities in the waste wood stream. Thanks to the X-ray penetration technology we are able to identify the atomic density of all the material that is running through the mill and it is an easy task for us to separate the wood from everything that is not good. The performance level of the X-ray technology has no comparison to any other cleaning technology for impurities,” he claimed.
“After this first step with the X-ray you would have a very clean material but it will be a mixed grade material so that means we will have a mixture of natural wood with MDF, with particleboard, with plywood, with coating materials and so on. So after the X-ray screening, the material will of course be good enough for particleboard production.
“But if we want to use recycled wood for higher performance applications, for example MDF or special types of particleboard or something like that, we cannot use this material, so for this we need a second step and in this second step we are combining the NIR technology with our Deep Learning Technology so with the NIR we are able to identify material characteristics, based on which sorting decision will be made. In combination with the neural network of our Deep Learning Technology, we are able to identify the different types of material – if it’s particleboard or MDF or plywood, or a piece of natural wood – and we can sort it by types. We are using this technology as a whole concept, a whole solution for the industry.”
In fact, said Mr Matas, TOMRA has 50 years’ experience with NIR technology, which still plays a pivotal role in the company’s sorting technology, together with the X-ray systems. And it has 10 years’ experience in X-ray systems specifically tailored to wood sorting.
TOMRA’s wood segment is headquartered near Cologne in Germany.
The segment also has seven test centres worldwide, enabling customers to bring their raw material to be tested and for a specifically trained sensor system to be developed for their specific needs.
“Material streams are getting more complex, so there is more need for testing, so we offer the full solution actually around the globe.”
In fact, the test centre at the segment’s headquarters is currently being expanded to cope with the increased demand.
TOMRA also has its own offices in the US, throughout Europe and in Asia to serve customers in their home region.
TOMRA is also working with companies that are recycling industrial wood, demolition wood and so on, thus dramatically reducing the amount of material being wasted, or going to landfill.
With both environmental and cost pressures on the panel industry, it seems that further dramatic growth in the use of recycled wood is inevitable worldwide and that suggests a bright future for technology to sort that material.