Stunning. That is the only word to describe the location of Fantoni’s factory complex in Osoppo.
The company’s multiple panel production lines and its furniture factory nestle in the shadow of the southern Alps, which provide a spectacular backdrop under a clear blue sky.
As we reported on our last visit to Fantoni Spa, the sympathetic nature of the architecture of this industrial complex, and its landscaping, minimise its impact on this especially scenic area. This is a company which takes its environmental responsibilities seriously, as becomes clear during talks with commercial director Dr Paolo Fantoni.
His company has been involved in the generation of electricity in hydro-electric plants for some years, holding a 45% stake in Cons CURI, a consortium involved in this technology, and Fantoni operates eight such plants in the Friuli area, assisted by the region’s high annual rainfall.
Now Fantoni is becoming more and more involved in the development of biomass. In partnership with Vivai Alasia and the University of Udine department of agriculture, it is developing plantations of selectively bred (not genetically modified) poplar.
Growth rates of 12m in 24 months have been achieved and the trees are ‘coppiced’ (cut at the base of the trunk which then sprouts new growth) on a two-year cycle. This produces wood raw material suitable for particleboard manufacture.
Dr Fantoni explains that the fibre is not suitable for MDF production as it is too soft and not sufficiently homogeneous.
“The first 300ha of this poplar have been planted in the Trieste region with the cooperation of the government and local agriculture. This is in line with the EU policy of reducing food production and increasing non-food production,explains Dr Fantoni.
His company directly owns 15ha of plantation adjacent to its factory, eight of which are planted with poplar, but he points out that the planting is mainly done in cooperation with farmers.
“This initiative looks promising, especially in view of the competition from energy producers for biomass, and I see it as a must to engage in such research,says the commercial director.
Returning to the business for which Fantoni is better known in our industry, Dr Fantoni confirms that there are currently five panel production lines in operation at Osoppo.
All are designated Plaxil, because that was the name of the subsidiary company responsible for panel production which was absorbed into the main Fantoni group in 1990. Historically (and that means going back to 1896) the Fantoni name was associated with furniture production only.
There is a 38,000m3 a year Mende line producing thin particleboard, then a Pagnoni 13-daylight press line of 3.66m x 1.87m, producing 130,000m3 a year of MDF. Next comes another Pagnoni press line, with 16-daylights of 4.25m x 2.2m, producing 170,000m3 a year of MDF.
There are also two continuous press lines, the first a Küsters, 2.8m wide and 38m long, with a capacity of 300,000m3 a year of MDF, the second a Siempelkamp ContiRoll line of 2.4m x 39m, with a capacity of 360- 390,000m3 a year of particleboard.
The Küsters press produces Fantoni’s ‘light’ and ‘ultra-light’ panels.
Another subsidiary company is Novolegno in Avellino, further south in Italy, and this has another Pagnoni press line of four daylights, 11.2m x 2.2m, giving a capacity of 130,000m3 of MDF, glued with MDI binder, mainly for the Japanese market. It also has two calender press lines, one 2.2m wide and the other 2.4m wide. Combined capacity is 205,00m3 of thin MDF.
Fantoni also has a 95% stake in Lesonit DD in neighbouring Slovenia. This has a capacity of 90,000m3 a year on a 10-daylight Motala press, which is 5.6m long and 2.08m wide.
That gives the Fantoni group a total raw board capacity of 1.025 million m3 of MDF and 428,000m3 of particleboard.
“We have carried out major works to optimise the production of Plaxil 7 [the ContiRoll particleboard line] and increase its efficiency, as well as starting up two Siempelkamp melamine facing lines parallel to it,says Dr Fantoni.
The ContiRoll line was bought secondhand, but unused, from Russia in 1999 and erected in Osoppo.
The Lesonit operation is an older line which Fantoni took over and which it is still in the process of restructuring.
“We have totally rebuilt the chipping line and carried out a lot of other work on the green end. We plan to build a second line there as soon as the market gives more significant signs of recovery and that could be either MDF or particleboard,says the director. Fantoni has also installed a secondhand melamine facing line, from the former Medaspan Italian particleboard factory, at Lesonit.
Other operations under the control of the group include LaCon spa, Patt spa and Flooring SA.
LaCon carries out melamine facing of panels and production of thin CPL on a Hymmen continuous press and has two Vits impregnation lines for decor paper.
Patt Spa, in which Fantoni has a 24% share, produces laminate flooring and acoustic panels.
Flooring SA is 40% owned by the company and produces laminate flooring.
The Italian panel market has changed quite dramatically in recent years and this has been reflected in the manufacturing industry, according to Dr Fantoni.
“A lot of mills have ceased production in Italy in the last 18 months and this has led to an improved equilibrium, especially in the particleboard market,he says.
He lists the closed mills as Medaspan, Novasep, Novameblo (just over the border in Slovenia), Stat, Panda, Trada and Sipav.
“This has taken a total of 1.5 million m3 off the particleboard market and offers an opportunity to get the price up from the terrible levels of 2003,he says.
His story is somewhat different for the MDF market. “The success of MDF producers in recent years is largely due to laminate flooring – it equates to slightly less than 40% of European consumption – so almost four million m3 of total production goes to flooring.
“Italy has a market of 5.5 to 6.0 million m2 of laminate flooring, which means about 60,000m3 of MDF, compared with a national capacity of around 1.3 million m3. That represents four to five percent of output. Thus there is diversified development between north and south Europe and consequently a difference in strategy between the two regions in the last four years or so.”
Dr Fantoni sees another peculiarity developing in the market, with powder coating finding increasing acceptance.
“At the recent furniture supply exhibition, the Salone Internazionale del Mobile in Milan, at least five large producers of furniture were introducing powder coated panels. Two major kitchen manufacturers – Febal and Aram World – both offered lacquered powder coated MDF doors, while Herman Miller, Frezza and Dazato all offered powder coated office furniture.
“We believe strongly that there has been great progress in this technology and that it will open up a strong flow of new products,Dr Fantoni predicts. “Italy already has five lines owned by service companies ready to coat any components for the furniture industry and we offer a particular type of MDF which is conductive to encourage a more homogeneous spread of the lacquer.”
Called Metalwood, this panel was developed by Fantoni’s R&D department and, by the use of special salts in its manufacture, is 10 times more conductive than normal panels. It is also claimed that it has a high degree of workability which allows epoxy powder paint to be applied, even to milled surfaces, without the need for sanding.
“We think this will take over the market for white, grey and black in bathroom and kitchen furniture and TV stands. The cost is higher than for melamine facing, but the panels do not need to be edge-banded,points out Dr Fantoni, who is an obvious enthusiast for this technology.
But this is not the only area in which this innovative company is seeking new markets for its MDF production. In the south of Italy, adjacent to its Novolegno factory, it is creating another new company to add to the Fantoni family, named Xilopack.
Fantoni’s R&D department has developed a new type of packaging for fruit boxes to be made and marketed by the new company. Made from thin MDF, the fruit box comes ‘flat-packed’ with ‘hinges’ on the chamfered edges so that it can be assembled by folding and clipping to make an opentopped box. In early June the company won a major prize from the packaging industry for this product and has a target of 20 million boxes a year. “We will also produce a half-size box as families are looking for a smaller box these days,says Dr Fantoni.
“The law requires that all these boxes are recycled and so these will probably finish up back in panels as particleboard,he adds.
Another unusual MDF-based product, developed by Swiss company Nueholz and now licensed to Fantoni, is TopaKustik. This specially machined MDF panel, first introduced at Interzum 2000, is gradually gaining acceptance in the construction market where noise reduction is a priority, such as in concert halls, and the company sees a good future for it.
As mentioned earlier, Fantoni began by producing furniture and its Osoppo factory still consumes 1,300m3 a month of particleboard and MDF in the manufacture of office furniture, although currently that market is still disappointing, says Dr Fantoni. “We are facing very tough competition, like the rest of Europe, although competition here is not as bad as it is in Germany where there is 40% less production than three years ago; Italy fell about 20% in the same period.
“We are aware that the office furniture sector multiplies the effects of a normal economic cycle. When GDP falls to zero, the furniture market goes into negative figures, but as soon as GDP improves, office furniture improves dramatically. So, we are waiting for better times.”
Dr Fantoni finds the current state of the MDF market less easy to explain: “I don’t really understand why this market did not rebound in September last year. It normally improves at that time of year, but it did not happen but I hope that, as particleboard has finally rebounded, MDF will follow.
“In the past, I thought equilibrium would be maintained by a growing market, but the loss of competitiveness in the European furniture industry on a world scale is changing the perspective. So I believe that explains why it has not improved and why there will not be an expansion in MDF capacity in western Europe.”
Dr Fantoni has always been a great supporter of the European Panel Federation (EPF) and its predecessor, the Euro-MDF Board (EMB), but feels that it needs to readdress its reporting strategy.
“Poland, Romania, the Czech Republic and other east European states are damaging the furniture industry – especially in Germany – and I think that, in future, the EPF must re-analyse the situation in east and west Europe and treat the two areas separately and not analyse Europe as a whole.”
After visiting the Osoppo factories, one comes to the inescapable conclusion that Fantoni is not just another panel producer.
Apart from the fact that it has maintained contact with its original roots as a manufacturer of quality furniture, it has also invested considerable resources in its R&D centre (doubled in size recently) and developed several very innovative products, as well as adding value to much of its production.
Now, with its involvement in plantation poplar, Fantoni has become fully vertically integrated and, quite possibly, unique in the west European panel industry.
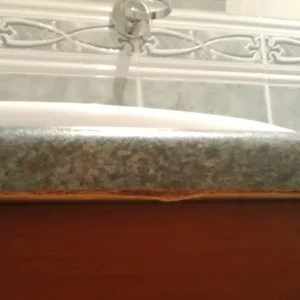