Giben International, founded in 1947 in Pianoro as Gino Benuzzi, says that a revolution in the function of its machines was introduced in 2000, when it won the Challenger’s Award for technological innovation for its PM System at that year’s IWF exhibition in Atlanta in the US.
In Giben panel saws, the ‘PM System’ (PM stands for ‘pinze mobili’ in Italian and moving grippers in English) is the system which automatically positions each individual gripper along the length and cross axis of the machine pusher.
The position is controlled by the saw computer, ‘Giben G-Drive Control’, and is always optimised depending on the size of the boards, the cut sequence, the size of the strips or the size of the parts. The PM System is now an established feature of most of Giben’s machines.
This year the company introduced a brand new model, the Y-3000 SPT/MR panel saw in its ‘Professional line’ series, with automatic loading of boards from the lift table and a pusher with moving grippers along the ‘X’ and ‘Y’ axes. It also features Giben’s MR rotation system.
Giben claims this represents the simplest and most effective solution to carry out both first and second rotation of the in-fed stack of boards. Overall dimensions of the machine remain unchanged, since rotation is carried out in the space between the machine working table and the front air flotation tables.
The machines in this series offer high performance saw carriage speed (170m/min) and pusher return speed (90m/min) and also feature pneumatic saw blade release, a split and independent pressure beam and an automatic side-aligning device with two independent rollers.
“The single cutting line model Y-3000, with manual or automatic loading from a lift table, is a high performance and versatile panel saw designed for the furniture industry,said marketing manager Stefano Conti.
For big sawing jobs, Giben offers the Formula S model, an angular system with two cutting lines featuring the PM System on the cross-pusher which can be equipped with robotic unloading systems and is controlled by G-Drive Control. This can also be equipped with a panel rotation system for staggered and/or checkerboard head cuts.
Giben has always supplied the panel processing industry with big sizing plants with two or more cutting lines, such as the Matic 17/170 and Hypermatic 19/200 models, but it is the Tetramatic which tops off the product range. It is claimed to be the biggest saw in the world and can cut stacks of panels 220mm to 310mm high (upon request), offering “huge yieldsaccording to Mr Conti.
“Every Tetramatic cutting centre has two saw carriages, one on the top and one on the bottom, each equipped with two blades, thus combining the cutting height with high speed,he said. The key feature is that the two main saw blades, of 470mm diameter and 4.4mm thickness, share the cutting strain equally on a stack of boards 220mm high as if it was a stack of 110mm.
Because of these features the cutting strain is reduced and a higher feed speed than would be possible using blades of 700/800mm is achieved, he explained.
The other two blades are scoring saws: the traditional bottom scoring saw prepares the cut on the bottom side of the stack and the top scoring saw avoids any chipping on the top of the stack.
“The Tetramatic has been designed to meet different tasks such as high capacity, extreme flexibility according to cut-to-size components, lower cost for tools and higher cutting speed,Mr Conti said. “Tetramatic can be integrated into highcapacity cutting lines for largedimension panel processing industries, in full loading and unloading lines and robotized stacking and strapping lines which can be equipped with an anthropomorphic robot, with an automation level never achieved by any sizing system.”
Under assembly in the factory at the time of my visit was a Sigmatic angular system with 6000 x 2700mm cutting length, complete with an ‘SR’ stack rotation system for the execution of one or more head cuts with the length panel saw.
This sizing system was on its way to a customer who makes hardboard, suggesting that the rotation system is capable of handling thin wavy panels as well as rigid ones.
Of course none of the automation of the PM System moving grippers, optimised saw movements, panel rotation and automatic robotised unloading would work without a coordinating system: the G-Drive machine control software. This was developed by Giben to run on Microsoft Windows multitasking operating system and to control all the complex machine movements.
The machine layout and cutting pattern being processed are displayed to scale on the screen and the cutting operations and panel movements are simulated in real time.
A further software system available to Giben’s customers is the Optisave (Optiwin) optimisation software, which it says provides the best cutting patterns, taking into account the waste factor, cost of the saw, cutting time and the cost of the material.
Although Giben is a regular attendee at major exhibitions, the company also has a large, permanent showroom at the Pianoro factory, where machines from its product range are always operating. It also held an open day in November last year and in 2002.
“This complements our attendance at the shows, in fact every year this showroom hosts many customers who can touch with their own hands the Giben solutions and newest products,said Mr Conti.
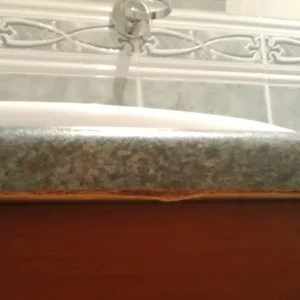