Imal srl was founded in 1970 and sister company Pal srl in 1978. For years the two companies operated entirely independently and in fact competed in some areas where their product ranges overlapped.
Both were highly profitable companies in their own right.
In 1998, the two companies’ owners saw an opportunity in combining their strengths and eliminating those product overlaps, so shares were exchanged in each company.
In 2006, Romeo Paladin, founder and president of Pal, decided to sell his shares in his company, Imal became the majority shareholder in Pal, and holding company Imal-Pal was born.
However, the two companies continued to trade as separate entities, complementing each others’ products and expertise.
Major complete plant supplier Siempelkamp of Germany had held shares in both independent companies for over 20 years but in 2008 Imal-Pal bought back those shares, becoming completely
independent on September 3 last year.
Pal and Imal are now owned by the three families who founded the businesses – Benedetti, Dal Ben and Zanasi, each currently represented by two generations in the business.
Loris Zanasi, managing director of Imal is, quite naturally, troubled by the current economic crisis.
“2008 was a record year for both Pal and Imal, with a combined turnover of approximately €86m,he said. “But orders have dropped off dramatically this year.
“Up to now, glue blending systems were the mainstay of Imal, with 38 being sold in 2008 and 1,407 blenders being sold in total – the largest number in the world for particleboard.”
The company has also supplied 768 glue preparation/dosing systems, 638 thickness gauges for use on the production line and 566 laboratory moisture meters, to name but a few products.
Orders included the gluing line for Homatherm’s thick insulation board line, which is a dry-gluing system using MDI resin in a blender; a new fibre resination system for Eucatex in Brazil; and one for Kastamonu in Turkey.
“Thick insulation board is in a growth mode due to building regulations,said Mr Zanasi. “Since the earthquake in Italy all new houses must be built with an external linked-box construction that will not fall down in earthquakes and the cavities between the walls must be filled with insulation at least 10cm thick. This offers good insulation in winter and summer.”
These rules came into effect on July 1 this year. Wall insulation was of course already compulsory, but thinner.
However, when markets take a dive, it is sensible to have another option to offer to the market and Imal has just that: The company’s pallet block manufacturing line, using a particleboard-like material extruded through a mould, has been very successful and can utilise urban waste wood easily.
A factory supplied recently was built on a greenfield site near Cork in southern Ireland (Eire) to utilise waste wood from the city. The complete wood cleaning system was supplied by Pal as part of a turnkey project for Imal which included the boiler, dryer and three press lines.
“Although we are aware that we are in difficult economic times, we are extremely optimistic for the future,said
Mr Zanasi.
For instance, the Ligna exhibition in May was a great success for the company, with 17 contracts being signed at the show. “These orders totalled over €3.4m, ranging from values of €5,000 to €1.2m,said the managing director.
A major new product shown on the Imal stand was the GA717-2 laboratory formaldehyde tester. The number refers to the appropriate EN standard number.
“Formaldehyde levels are becoming more and more important to furniture makers – particularly IKEA – and our system takes four hours to produce a result, compared with two weeks for the conventional chamber method. Ours is based on gas analysis,explained Mr Zanasi. “The California Air Resources Board [CARB] accepted this EN standard in March this year.”
Also new at the Ligna show was the TM200 thickness gauge for use on the panel production line at speeds of up to 210m/min. It is normally installed just after the press and is claimed to offer a resolution of 1/100mm.
The top and bottom heads are moved simultaneously by a pneumatic panel and the electro-valves are designed to close the heads as soon as the gauge detects the presence of a board, and to open them at the end of the board.
The visualisation software monitors thickness in real time at each position along the length and width of the board and provides averages and trend graphs.
Measurement of the fibre geometry in MDF production and the particle geometry in particleboard is also an important part of quality control.
FiberCam 100 is an optical fibre screen which operates with dry fibre and optical measurement, avoiding the problems of clogging screens. The measuring range is 0.05 to 25mm and as many as one million measurements a minute can be taken, measuring the width and length of the fibre.
ScreenCam 100 is an optical particle screen which operates on the same optical principle as the FiberCam and can be adapted for on-the-line operation as well as laboratory use. The measuring range is 0.15 to 50mm and the measuring time is said to be one minute, in real time.
So, Imal has plenty of established and new products to offer to the global panel producing market now and when things improve.
“This year will be quiet but we do still have big projects under discussion,concluded Mr Zanasi.
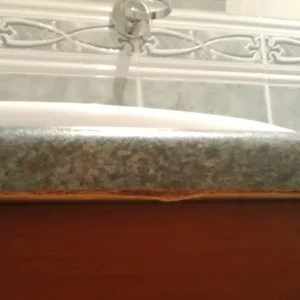