There is often a connection between panel resins and chemical products for other markets and thus Sadepan also supplies fertilisers, as well as chemicals for water softeners, fibreglass (GRP) manufacture and leather tanning. For the Viadana plant, Sadepan is currently installing a pipeline for transporting methanol from the Po River to the factory so that it can be piped direct from barges which have travelled up the Po from the port of Venice. The company has also reached agreement with the authorities for a rail connection to be built from Casalmaggiore to Viadana, a distance of 14km, to bring raw materials from the east coast of Italy.
“This is another environmental move by the group to reduce truck usage and emissions, by increasing rail and water transport. Any time we see the possibility to be ‘green’ we will invest – in technology, logistics, any aspect that can enhance our ‘green’ approach,said Tullio Gozzi, chief executive of Sadepan Chimica, who, like his brother Luigi, chief executive of panel making arm Saviola (see p46), is very keen to promote the ‘green’ credentials of the Saviola group. The Belgian factory has already established this kind of transport for its raw materials and finished goods. Sadepan has three methanol storage depots in Italy, at Venice, Livorno and Genova, with 50% of the company’s consumption coming from Venice. The Viadana factory has six formaldehyde plants and 12 reactors for UF liquid glue, as well as MF and UF resins for impregnation. It also produces powder UF and MF resins and fertiliser. Castelseprio has one formaldehyde plant and UF liquid glue production. Truccazzano produces phenolic resin for HPL and CPL manufacture and Kraft phenolic papers.
At the Genk plant, the company started up a new formaldehyde plant in March of this year, with a capacity of 120,000 tons per year (tpy) of 36% formaldehyde. This brings the total Genk capacity, in three plants, to 350,000tpy (36%). Total glue capacity at the site is 400,000tpy of urea formaldehyde (UF), melamine urea formaldehyde (MUF) and melamine formaldehyde (MF) paper impregnating resins.It has three formaldehyde plants, UF and MUF glue and resin production, and plans are afoot for paraformaldehyde synthesis in the near future. At the beginning of next year a further investment will come on stream here, with the start-up of a paraformaldehyde (powdered product) plant with a capacity of 20,000tpy. We decided to make these increases in Genk’s capacity mainly because we have the space there, but also because we have a production licence and the existing infrastructure,said Mr Gozzi.
Although methanol supply was tight in 2006/7, he said that the downturn in volumes in the panel industry generally has meant an increased availability of that important ingredient. Things have been rather different in the urea market since China decided to impose a 135% export tax on it, leading to a fall in exports of five million tons a year. Urea is required to produce melamine, as well as being a constituent of glues and resins.
As a result of the Chinese action, the world price went from US$400 per ton to US$650 between April and June this year (prices fob Black Sea/Baltic Sea), said Mr Gozzi. The reasoning behind the Chinese decision is that urea is a major constituent of fertiliser and China requires more fertiliser in order to produce more rice. All this has led to calls from melamine producers for a 20% price rise as a result of the combination of both the urea price increase and rising energy costs.
“The prices of urea, melamine, and probably methanol next, are thus increasing and will continue to increase, putting the panel market into even more difficulties – this is a very serious problem for European panel producers in a poor market,said Mr Gozzi. With the major push for reducing formaldehyde emissions from panel products, Sadepan has been very active and says it was one of the first to produce low emission formaldehyde-based glue to F**** standard and better. Known as LEB (Lowest Emission Board) by sister company Saviola, its development was driven by companies such as international furniture retailer IKEA, which wanted formaldehyde levels minimised. We have an advantage over our competitors in formulating special UF glues in that we can test them in Saviola’s mills before bringing them to the market,said Mr Gozzi. The vast majority of Sadepan’s resin production is exported outside Italy because the major national panel producers have their own resin production facilities. Thus exports go to Germany, Austria, France, Slovenia, Croatia, Spain and Switzerland – that is, more to southern Europe.
The Genk factory exports to northern Germany and France, central and northern Europe and the Benelux countries, as well as the domestic Belgian market.
Looking to the future, it seems hard to predict much light at the end of the current tunnel: “I think the wood panel market will be very difficult for all of 2008,said Mr Gozzi, “The euro is too strong and that is particularly affecting the flooring market’s exports to the US, as well as furniture exports.Meanwhile, Sadepan Chimica will hope to fight this trend by increasing sales of its low-emission formulations.
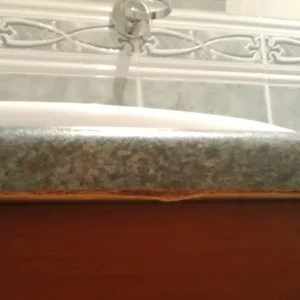