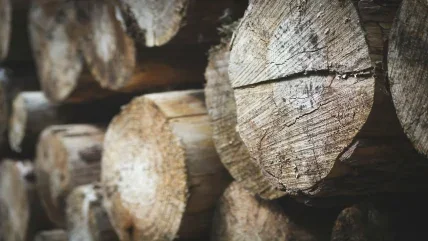
These are interesting and exciting days for biochemicals business Evertree.
When WBPI caught up with Evertree CEO Nicolas Masson recently, the company had made a number of important steps forward.
This included the 2019 successful commercial launch of Green-Boost, a plant-based binding intensifier for use in wood-based panels, following many years of development work and extensive 24/7 trials.
In addition, Evertree was selected just a few months ago by the French Environment & Energy Management Agency to lead the Respire project which aims to finalise the development of a plant-based binder to replace urea formaldehyde (UF) in MDF and particleboard (PB) manufacturing.
For Mr Masson, such developments are small but significant steps and represent the first fruits of the company’s hard work and high investment in recent years.
But first let’s rewind a bit and remind ourselves about the Evertree operation.
Evertree was founded by three main partners. The first is the Avril Group, a leading industrial and financial group in the vegetable oils and proteins sector which was founded as an initiative of French farmers to assure long-term markets for their products. In 2018 it achieved turnover of €6bn.
A second partner is French national investment bank Bpifrance, while the third is Biopolymer Technologies – an industrial science and technology startup, specialising in the domains of nano chemistry and biotechnology.
Biopolymer Technologies’ R&D team developed a broad range of technologies related to the use of plant proteins in applications such as wood composite boards and polyurethane foams.
Evertree’s creation in 2016 was backed by a €24m investment as it sought to deliver commercial plant-based solutions to significantly reduce the presence of petroleum-based resins in wood-based panels.
Targeted outcomes included more cost-efficient and greener manufacturing processes and a greater proportion of bio-based content with the added benefit of a significant reduction in panel product volatile organic compounds (VOC) emissions, which are of course known for harmful effects on health and the environment.
This latter point is important as studies have indicated that more than 50% of VOC emissions arise from everyday consumer products.
An innovation centre in Venette (Oise) was established in a €1.5m investment in 2017 to be the hub of continuing R&D, with three main units: a protein chemistry laboratory, an industrial unit to test applications and another unit to develop processes and manage product manufacture.
Green-boost
Wood-based panels represent the first target area for Evertree and its first product development – Green-Boost – commercially launched in 2019.
The product – an additive, which works as a binding intensifier – is based on rapeseed protein, the by-product after rapeseed seeds are pressed for their oil. Large volumes of the material are generated annually by the French agricultural sector and it is precisely that “waste” which Evertree is using to make a high-value product.
Extensive industrial trials of Green-Boost have taken place and now two woodbased panels plants in Western Europe – one particleboard producer and an OSB manufacturer – are in full commercial use of the additive within their resin operations.
Mr Masson said Evertree’s aim with Green-Boost is to attain the same performance from the manufacturing line but with reduced resin use. He says Green-Boost is achieving more than a 20% reduction of pMDI consumption, therefore reducing resin costs.
“We have seen during the trials that we can improve productivity of the line using the same equipment,” said Mr Masson. “To be able to decrease the use of synthetic resin allows the plant and panels to be greener. This is something that is becoming more and more important.”
“With 25% less resin we are obviously greener. Usually greener products are more expensive but Green-Boost is quite an efficient and cost-effective solution. It helps that Evertree is integrated in the Avril Group so raw materials are produced by the group and we can efficiently source them.
"We can also select the exact grade of raw material – something which is not directly available on the open market – and deliver it at the right prices.”
In doing so, Evertree believes it is solving the conundrum whereby green solutions are often viewed as more expensive and therefore less attractive/viable for widespread industrial use.
The Avril Group produces two million tonnes of the rapeseed protein raw material annually.
“We are looking to roll out the technology to other mill sites at our first two customers and also expecting to convince new customers as well,” added Mr Masson.
“The industry is still quite conservative and no-one usually wants to be the first to trial something new. But now we have done the first step it will be easier to roll out the technology to other customers.”
In North America, Evertree has been conducting trials with three wood-based panel producers, starting in 2017. It hopes to convert some in the near future.
“As of today, we have greatly improved the delivery mechanism for the additive. Since 2017 a lot has been done with the equipment.”
A small additional piece of equipment is necessary in the production line to ensure the additive is properly mixed with resin to deliver a consistent performance. The equipment, which Mr Masson says can be installed in under a day, is the result of inhouse and third-party collaboration.
He said extensive work by Evertree had been done on educating wood-based panel manufacturers about the product, while the company had also developed its own expertise on its customers’ production processes.
An holistic approach sees Evertree provide all the engineering technology and expertise as a package to minimise any time for manufacturers to adjust.
Of course, Green-Boost is not designed to completely remove resin use. That’s where Evertree’s second product technology comes in.
Bio-Adhesive
The second technology is a bio-adhesive, designed to act as the main binding agent in wood-based panel production.
Evertree is running industrial scale trials in MDF production with its binder, as a complete substitute for UF. The trials are taking place in a western European MDF plant with a 10-15% UF substitution rate.
Mr Masson said results showed good mechanical properties and same performance as UF, with the end product suitable for furniture production, but with an improved environmental profile.
Evertree received a big boost at the end of 2019 when it was selected by the French Environment & Energy Management Agency to lead the Respire project which aims to finalise the development of a plantbased binder to replace UF in MDF and particleboard manufacturing.
The binder product of course acts differently to Green-Boost.
The main raw material for this product is still protein generated from different plants. As well as rapeseed, sunflower and soya protein can also be used to produce the binder.
And Evertree is not stopping there. While its initial focus is on the wood-based panels industry, it sees multiple potential uses for its technology in the future, for instance in the plastics and insulation industries.
But Mr Masson emphasises that it is a step-by-step process.
“Synthetic materials will not be 100% replaced in the next 20 years. It will be step-by-step. I hope we will find solutions that are viable both from a performance and economic basis because you cannot argue that a bio-based solution is the best solution if it costs double the amount of a synthetic one.”
Mr Masson said green solutions generally across a range of industries were often more expensive than the non-green mainstay in their initial development phases, but as more people adopted the newer products then prices have been proven to come down.
“In the next 10-20 years we will have more and more green solutions that people use. The synthetic solutions that are in use today have been in development since the 1960s, so that’s 50+ years that their processes have been optimised. So it will take time for the green product to establish itself.”
Mr Masson said even plastic had been expensive when it first came onto the market.
“I believe our second [binder] product development is environmentally acceptable for customers and it will be adopted by the industry. And it will be one step in the right direction.”
While Evertree’s initial funding had been €24m in 2016, a further €15m investment was made in 2018 by Avril and Bpifrance through the Sociétés de Projets Industriels investment fund managed in the context of the French government’s Programme d’Investissements (Investments for the Future programme).
“We have the capital now to go industrial,” explained Mr Masson. “We have our first customers and are ready to build our own plant.”
Currently, Green-Boost and its bioadhesives are produced in combination between Saipol, part of the Avril group (which processes the rapeseed protein) and a third-party operator.
Saipol produces and sells in France refined vegetable oils for human foods, protein-rich oilseed meals for livestock feeds, biodiesel under the Diester brand and vegetable glycerin that has numerous industrial applications.
“I think that next year we will be able to make our own products in our own factory in France, so 100% of the process will be within the Avril Group.”
Evertree is confident that it is starting to establish itself as providing an alternative to the synthetic resins used at present, opening the way to a future where a new generation of wood-based composite panels (OSB, MDF/ HDF and particleboard) are based on bio- and renewable chemistry.