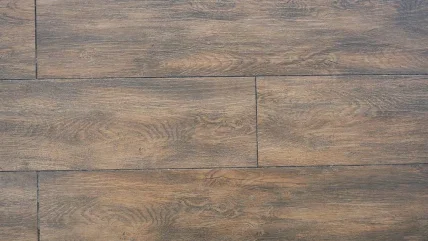
Wood-based building materials have been in vogue for a few years now because they tick many of the boxes demanded these days – use of natural materials, carbon friendly, a strong environmental profile and high-performance.
Wood-based insulation materials, whether rigid boards used in roof sarking and wall sheathing applications, or less dense flexible batts for use as infill insulation or indeed loose fill material, have seen strong growth over recent years.
Demand for these products has soared and manufacturers have been investing in additional production capacity. Indeed, we are looking at a number of new factories going on line in the next few years, with the growth rate in production outstripping traditional wood-based panels such as particleboard and MDF.
WBPI’s conversations with plant technology providers over the past 12 months have revealed a number of new capacity projects in Europe which will increase production capacity further in the coming years.
PRODUCT GROWTH
A look at the European Panel Federation’s (EPF) 2020-21 Annual Report shows some of the most recently available statistics for the product, categorised as ‘softboard’.
It was the strongest performer in the EPF family in 2020, with production up 5.7% for the year to 5 million m3. That’s a bigger growth rate than PB, OSB, MDF and plywood. 2019 did see a sharp contraction due to some capacity closures, but looking back over a longer period it’s clear that there is a growth trajectory.
Rigid softboard accounted for 61% of the output and flexible softboard for the remaining. The vast majority of that production stayed within the European area.
Poland is by far the largest producer of the material, followed by France and Germany.
Poland rigid board production, says the EPF, was 1.74 million m3 in 2020, while its flexible product capacity was 1.05 million m3. Norway is also a significant producer of flexible products.
EPF records installed European production capacity for rigid products at 3.42 million m3 in 2020, while the corresponding figure for flexible products was 2.87 million m3 – the latter grew by 350,000m3 in 2020 due to new capacity in Poland.
The largest individual product sector within softboard is the rigid product for building shells – typically roof sarking or in wall applications – making up 36% of total softboard sales. The second largest (28%) was flexible product used in the building shell. Underlays and standard boards were among the other applications
“It’s really very strong growth, accelerating in the second half, definitely related to some changing trends we are seeing in Europe driven by the new European Bauhaus, and to slightly changing the way we are living and drawing on nature-based solutions,” the EPF said.
“Softboard is right at the heart of this,” the EPF continued. “We expect to see another steep acceleration in 2021.”
Those figures should be available in the coming months.
Poland produces half the rigid and one third of the flexible insulation boards in Europe. Over 60% of products are used as insulation to improve energy efficiency of private homes and offices.
The largest individual producer of wood fibre insulation in Europe is Germany-based Steico, which has extensive production operations in Poland.
As WBPI went to press, Steico published its annual results, showing recording-breaking figures for the group. It should be pointed out that Steico’s products also extend to LVL and I-joists.
Its preliminary results for 2021 show revenues of €388.2m, an increase of 25.7% on 2020, while earnings before interest (EBIT) were at €67.9m (+102.2%).
However, Steico did caution that when comparing the figures with the previous year, it had to be borne in mind that earnings in 2020 were depressed by the Covid-19 pandemic.
The group said the positive earnings result was despite the increase in the prices for raw materials.
The positive trend in sales and earnings also continued on a quarterly basis, making Q4 2020 the most successful fourth quarter in the company’s history.
Revenues in Q4, 2021 were €99.6m, up 22.1% from a year ago, while EBIT rose a staggering 94.8% to €17.8m.
“Management is very positive about 2022,” said Steico.
“Demand for environmentally-friendly insulation material and construction products continues to be high and the underlying regulatory conditions support further growth.
“What is more, in the opinion of the company’s management, Steico is the only manufacturer of wood-fibre insulation materials that will increase capacity significantly in 2022.
“To the extent that the prevailing growth in costs does not result in any further negative effects, the board of directors believes that revenues will grow by around 15% with an EBIT margin of between 13% and 15% (in terms of total operating revenue).”
Steico’s operations extend to three plants in Poland and one in France.
The Czarna Wood site is near Gdansk, while at Czarnków Steico operates the world’s largest integrated plant for the production of wood fibre insulation materials, covering some 100 hectares.
At the French site of Casteljaloux (near Bordeaux), Steico has a total area of 34 hectares, of which nine hectares are currently used for production. The site is ideally located to supply the French market and neighbouring southern European markets such as Spain and parts of Italy.
At the Gromadka site in Poland, Steico is currently building a new insulation materials plant on a site covering around 18.6 hectares.
“In Gromadka, we plan to start the commissioning phase at the end of 2022 / beginning of 2023,” Steico reported to WBPI.
Other extension work has been taking place at Casteljaloux and Czarna Woda. A plant for rigid insulation boards from the dry process with a capacity of 250,000m3 has been built in Casteljaloux and a plant for rigid insulation boards from the wet process with a capacity of 135,000m3 has been added at Czarna Woda.
“At the Casteljaloux and Czarna Woda sites, we produced the first insulation panels in December 2021, and further technical optimisations are currently being carried out,” said the company.
“The demand for wood fibre insulation has increased dynamically since the middle of 2020, so that Steico was able to realise the most successful business year in the company’s history in 2021. We are also very positive about 2022. We expect growth in pretty much all markets, with our large core markets such as Germany and France likely to again bear a large part of the growth.
“We see that in addition to Steico, existing competitors are also increasing production capacities and individual new competitors are planning to enter the market.
“At the moment, we cannot judge exactly when their projects will be completed, but in 2022 Steico will be the only company to realise significant capacity increases.
“The new capacities will certainly have an impact on the intensity of competition. However, due to the rapidly growing market for wood fibre insulation materials, we do not expect permanent over-capacities.”
The trend of sustainable building and carbon friendly construction and product selection is certainly benefiting the specification of wood fibre insulation.
“We see a paradigm shift in many European countries. In the past, the focus of government regulations and subsidies was primarily on the pure energy efficiency of the finished building. Whether the building products used were manufactured in a climate-friendly way was irrelevant.
“Now the systems are increasingly changing so that the entire building process should be as sustainable and climate-friendly as possible.
“For Steico, this is a positive development. We produce in a climate-friendly way and our products are a carbon store at the same time. This makes us an excellent fit in the changing market environment.”
In terms of innovation, Steico highlighted its STEICOflex 036 product, which is billed as having the lowest lambda value of all known natural insulation materials to the extent it is competitive even with conventional competitor products. Protection against overheating in the summer, as well as staying warm in the winter, is one of the advantages attributed to the product.
Steico is also putting great emphasis on being a system provider – supplying the load-bearing structure via its I-joists and LVL, with its insulation products to complete the building envelope from a single source.
“We would like to further strengthen this system in the future,” Steico told WBPI.
“At the moment, however, we are putting all our efforts into increasing production capacities in the insulation sector in order to meet the growing demand in our core business.”
With its current production capacities, Steico can insulate around 53,000 buildings per year, whether new build or renovations.
BUILDING CAPACITY
It’s not just Steico that is investing in new capacity, of course.
Schilliger Holz AG wants to set up a production plant for wood fibre insulation boards in Perlen, Switzerland.
It is to be built on the Perlen Papier AG factory site. Commissioning is scheduled for 2023.
The new plant will close a current gap in the processing of Swiss wood that arose following the cessation of insulation board production in Switzerland some years ago.
The CPH Group is leasing the company a 20,000m2 land plot for the plant’s construction, and will also supply power and water for the new operation.
Soprema Group, owner of the Pavatex wood fibre insulation brand, is investing €50m in two additional manufacturing plants in France, which will be operational by 2023.
One will be in PUR insulation and the second will be for its natural insulation products, such as its Pavatex brand.
Both production sites will be built in Nîmes, in the south of France. Pierre-Etienne Bindschedler, CEO of Soprema, has stressed that “Nîmes is located at an important geographical location” and is not far from the Soprema plant in Avignon.
Meanwhile, in Sardinia, a new wood fibre insulation board factory has just been completed and the first board produced.
The Bioedil facility will have a capacity of 4 tons/h of fibre and will produce rigid insulation boards with a density of between 110 and 270kg/m3 and thickness ranging from 8mm to 240mm.
It will use cork raw material – believed to be the world’s first manufacturer of insulation board using this material – as well as local wood waste.
IMAL PAL was the complete turnkey technology supplier for the project, including biomass electrical co-generation energy plant to produce 1MW of electricity and power for the press and dryer, plus complete line from wood infeed right up to packed and stacked boards.
The company is also dealing with three customers for three separate factory projects for wood fibre insulation board – two of which are outside Europe and currently under discussion.
Over in the US, plans to establish the first wood fibre insulation board plant in the country are nearing realisation, with Go Lab Inc’s plant expected to be completed in the coming months.
Equipment was transferred to the Maine site from Europe (Homatherm’s Berga site in Germany).
Dieffenbacher originally supplied the equipment in 2009 and supported Go Lab in the relocation and planning of its re-installation. Dieffenbacher has also modernised the plant and installed new equipment, including a gluing system and dryer.
GO Lab will be producing boards, batts and loose fill under the brand name TimberHP. It hopes to build on wood fibre insulation’s proven market success in Europe.
Go Lab believes wood fibre insulation made in America – with much lower raw material and energy costs compared to importing it from Europe – will enable it to enter the market at a price point similar to other insulation options.
“We’ll be able to offer a high-performing, sustainable, comprehensive insulation product with a negative carbon footprint priced for mainstream adoption,” it said.
Dieffenbacher recorded four orders in 2021 for plants to produce wood fibre insulation boards used for ecologically smart and climate-friendly insulation in house construction.
It is these driving factors – the environment, sustainable construction, use of natural materials and performance – which will surely continue to push the market for wood fibre insulation board.