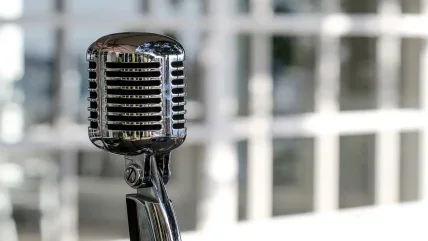
Can the Kleiberit Hotcoating (HC) process even be called a coating process?
We attach importance to the term “coating process”. Coating has its origin in the desire to protect and/or enhance valuable objects. This is exactly the intention of our process technology today. Kleiberit is the first manufacturer worldwide to develop a process which enables the wood-based panel manufacturing industry to carry out final upgrading of their semi-finished products themselves. Until then this was traditionally left either to their customers (such as furniture manufacturers) or to a highly specialised industry (contract lacquerers/ car lacquerers).
What is the fundamental difference, or, what are the main advantages, when potential investors decide to invest in this technology?
Split into the following categories: First is the cost of investment. The investment costs for a PUR HotCoating line depend on the working width as well as the properties of the raw product. In general, we distinguish between lines for coating flat materials (such as particleboard, MDF, HPL) and lines for coating roll materials (such as paper, PVC, PE and many other roll substrates). The configuration of the lines, which are producing worldwide with the KLEIBERIT PUR HotCoating process, are generally very similar. Differences can be found when special materials require additional processing steps, for example, plywood and OSB. The costs of the total investment correspond to the expenses which are incurred for widely known large scale coating lines.
Secondly, it is the space, energy and personnel requirements of a running line.
The space requirements of a new line depend on the planned maximum capacity.
While a line for roll goods requires relatively little space, a panel line requires much more floor space. The 65 lines that are producing worldwide with PUR HotCoating technology range between 15m–178m long, and the overall process requires between 100m² and several thousand m² of production and logistics space. An average 1,250mm wide line for high-gloss has an energy requirement of around 400kW which corresponds to a “normal” coating line as it has been known for decades. As far as personnel is concerned, an average of three line operators are needed per eight-hour shift.
Thirdly, it is about the quality, cost and benefits of the final product. It was, of course, very important to us to define a process that would enable the user to supply its products to the market in large quantities and without compromises in the quality.
This requires perfect quality and an end product with convincing properties. These criteria remain a focus in our daily business, combined with the desire to constantly improve and to test new properties and to integrate them as needed. The cost factor always plays an important role in these processes. Through the use of modern coating line technology, costs have been optimised and are only a fraction of the costs that were the norm before the introduction of our technology to the market. The high quality, combined with unlimited availability, has revolutionised and completely changed the market for fine surfaces. Previously unknown properties, which were achieved through the use of PUR HotCoating, have also naturally led to its worldwide growth.
Fourth comes the environmental aspects (emissions, energy consumption, raw material use). It must be mentioned that our customers only use VOC-free products.
This factor, combined with a loss-free roller coating technology, results in a modern and environmentally friendly coating process which will continue to exist in the future due to its environmental balance. All products are completely radiation polymerised or cross-linked due to the process. Therefore, there are no measurable emissions from the surface.
The fifth aspect is implementation of a line after the investment decision.
We consider ourselves as an all-round partner of the industry. Our work begins with the initial presentation and continues from the sampling process up to providing training for the future operating team. The implementation process depends on the lead-time for the new line. For most projects, we have about 10 months to prepare the customer completely. This includes marketing support and production training at our subsidiary dekoraPUR GmbH.
Here we offer our customers the opportunity to send their panels and to coat them in their presence under real factory conditions. This allows us to introduce our future customers to the new products and all of their properties.
Lastly, there are additional advantages. A major advantage of the Kleiberit system technology is the large product portfolio which is available today. In addition to high gloss and super matte products, we also offer special products for outdoor applications (façades, decking etc) or laboratory facilities. The possibility to add an anti-microbial treatment or an anti-graffiti coating is currently of particular interest.
Therefore, we cover all of the requirements of modern decorative panels for interior and exterior use. Such a product portfolio, together with a high degree of efficiency during commissioning usually leads to a production start 10-14 days after completion of the installation work of a new coating line. In the meantime, the process has developed enormously in terms of application diversity.
What are the most important milestones for Kleiberit HC?
We see the milestones as follows:
- 2009: Commissioning of the first industrial installation for the coating of flooring elements at LICO in Muestair, Switzerland
- 2012: Commissioning of the first industrial roll-to-roll installation for coating of wrapping material at Versatrim in the US
- 2012: Commissioning of the first industrial installation for the coating of wood-based panels at KASTAMONU in Istanbul, Turkey
- 2013: Commissioning of the first PUR HotCoating line at DURATEX / Itapetininga
- 2017 Commissioning of the second PUR HotCoating line at KASTAMONU in Istanbul, Turkey
- 2018: Commissioning of the first industrial installation for the coating of fibre-cement based flooring panels
- 2019: Commissioning of the world’s first industrial installation for the coating of 0.8mm HPL laminate sheets
- 2020: Commissioning of the first HiGloss & SuperMat panel line in North America
Today we serve 72 industrial coating lines worldwide. In 2021, more lines for customers in Asia and the Americas are confirmed and under construction.
What unique advantages or properties does the HC end product offer?
Products coated with PUR HotCoating are characterised by properties that are difficult to achieve with conventional coatings.
For example, one unique property is the long-term flexibility of our PUR HotCoating, which does not become brittle, even after several years, and thus provides a perfect basis for areas that are exposed to substantial thermal fluctuations (facade/ garden). This flexibility also results in exceptionally good processing. Sawing or drilling do not cause any cracks in the edge area and therefore enables perfect results when edging valuable fronts, and so on, in the furniture and kitchen industries.
The dreaded “chipping” does not occur, so penetration of moisture into the lacquer and possible delamination later is avoided.
Another advantage is the in-line embossing of PUR HotCoating finishing.
With the aid of an embossing or a static press, deep textures can be created in a continuous process.
This applies to both panel and roll products.
The process is not only suitable for the finishing of panel material but can also be used in the roll-to-roll process due to the flexibility of the coating.
What are the main applications HC has opened up for this?
In this area, our customers produce a wide range of laminating and wrapping materials. All products are characterised by high flexibility and post-formability and achieve the smallest radii (<2 mm) in further processing.
A very new but no less interesting product is the coating of decor material suitable for short-cycle presses, when finished with a texture by using a suitable press plate, an overlay is not needed and thus offers a considerable price advantage, providing the typical PUR properties like warm feeling and soft step to the flooring panels.
What role does your affiliate company Dekorapur Gmbh in Germany play with regard to the presentation and promotion to future investors or interested parties?
Our subsidiary dekoraPUR GmbH has a significant share in the overall success of our technology.
We offer all interested parties the opportunity to visit dekoraPUR to get an impression of the technology during ongoing production. Delegations from all continents have already taken advantage of this offer and seen the processes on-site.
We also offer our customers, probably unique worldwide, the possibility to send their own panels and to join personally the coating process on-site. Another important point is the development of new surface products in close co-operation with dekoraPUR, especially testing there in an industrial environment, similar to the production line at the customers.