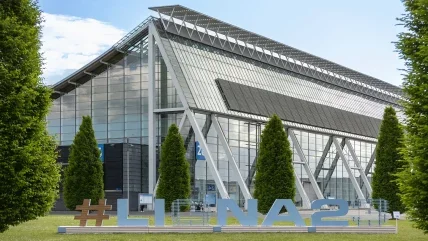
Hannover has been a rare meeting point in recent years due to the Covid pandemic.
So it was with some relief and enthusiasm that the international wood-based panels sector and technology providers could once again congregate at the Ligna exhibition to discuss markets and innovation.
In attendance terms it was busy, although visitor numbers were slightly down on the previous 2019 show.
Organiser Deutsche Messe said the event’s five-day run from May 15-19 had around 10,000 fewer visitors than the previous edition in 2019 (an 11% reduction), though Russian and Chinese visitors were largely missing due to the Ukraine conflict and reported visa issues respectively.
Nevertheless, some 80,000 people attended and companies lauded the value of seeing customers face-to-face again.
Ten halls showcased the best of solid wood and panel processing technology, covering the whole supply chain from forest to end user.
Hall 26 was again the location for the primary wood-based panels manufacturing industry.
Specific highlights included woodbased panels technology producer Dieffenbacher’s 150th anniversary party; new investor backing for Sunds Fibertech’s expansion plans; progress on autonomous manufacturing from Siempelkamp and Longoni’s premiere of its LamiDry process for melamine and phenolic resin impregnation in the HPL industry.
“In view of the uncertain situation currently confronting the woodworking and wood processing industry, the success of Ligna 2023 speaks volumes for its status as a source of momentum,” said Dr Bernhard Dirr, managing director of VDMA Woodworking Machinery.
“Not only is it a driver for the industry in good times, but above all, it delivers solutions for the challenges ahead.”
EXHIBITORS
Here we attempt to summarise news from exhibitors we visited, starting with Siempelkamp.
Siempelkamp’s new management team presented the company’s annual results, showing a €779.3m order intake in 2022, with sales of €611m and order backlog of €1.05bn. Twelve plant acceptances were recorded in 2022 and 10 new lines started up.
“We’re glad to be here after so many years of the Covid crisis,” said Martin Stark, Siempelkamp CEO. “We spent a lot of time in Zoom meetings in 2020-2022 but missed crucial contact.”
A re-energising of the company has seen much change at Siempelkamp’s Krefeld base.
Digitalisation, sustainability, and efficiencies with wood raw material, glue and energy have been key development points. AI software has been added to Prod-IQ, while a new forming machine with adaptive forming technology was highlighted.
A large video screen depicting a wall of data showed the innovation of Prod-IQ – SmartPress, an AI solution giving an autonomous process control solution.
Two such “smartpresses” are running so far, reporting a 10-15% boost in efficiency. It also allows a new inexperienced operator to run the line at the same level as an experienced operator.
Siempelkamp also had a section dedicated to alternative panel feedstocks, showing panel samples made from bamboo (MDF, PB and OSB), flax, recycled wool, recycled cotton and three-layer PB out of jute-stives.
At the Andritz stand at Ligna, Michael Rupp, vice-president Panelboard, told us that attendance had seemed to be at pre-Covid editions and he had been very happy seeing so many visitors at the booth.
The company, inter alia a front end technology specialist in the panelboard sector, shared a stand with Group company Modul Systeme – the largest store for second-hand equipment in the panelboard industry worldwide.
Mr Rupp reported that efficiency and production savings are still a top focus for customers. Andritz’s front-end energy saving innovations include steam recovery systems, advanced wear resistance, the SmartWoodyard advanced control system and the steam regulation module (SRM).
Waste water treatment is another area of expertise of Andritz (from its pulp and paper operations) which can further plant efficiencies.
Stand visitors were encouraged to “take a selfie” with a towering image of the world’s largest refiner – a S2074M single-disc refiner.
Andritz’s front-end packages span debarking, chipping, raw material handling, screening, chip washing systems and pressurised refining systems for fibre production with low energy consumption.
Schwabedissen had one of its doubleend tenoners on display. The machine processes tongue and groove end profiles on particleboard and OSB.
Arndt Bauer, director, told WBPI that the company was seeing many tenoner projects for wood fibre insulation boards in Europe.
Recently, a German producer of wood fibre insulation boards expanded its existing production with another Schwabedissen tongue and groove profiling line.
“It’s very important for us to be here,” he said. “We have had a stop [at the Ligna show] for four years so that’s why it’s important to meet together again.”
The IMAL PAL Group went into Ligna believing it would be a success.
“This is why we opted for an exhibition area of over 900m2 to showcase various items of equipment and technology,” said managing director Loris Zanasi.
A large common square was created, composed of companies in the Panel Alliance team: IMAL – PAL – GLOBUS – VYNCKE – RECALOR – TRASMEC.
The stand presented a large number of machines, “attracting a host of visitors each day”, while Mr Zanasi reported eight new contracts concluded at the show.
The Smartlab featured over 40 devices to run tests on wood samples.
Online quality controls on show included the FBC Full Delamination Control, while a continuous press was shown on large screens and pallet block lines / a pressed pallet line were also presented.
IMAL PAL Group also demonstrated its expertise in insulation board lines and belt dryers, with eight of the latter currently being manufactured and assembled (six in Europe).
The sight and sound of Ipco’s moose on its stand was a welcome sight once again and a magnet for visitors’ photos as always.
For steel belt system specialist Ipco, Ligna was an opportunity to highlight its service and support services. Engineers explained repair and maintenance techniques, with tools on show including Shotpeener Pro, a portable unit used to restore deformed steel belts to a totally flat condition, without interrupting production.
The next generation Shotpeener Pro incorporates a number of technical advances, resulting in increased blasting effect for faster results. Flattening capacity has been increased by 30%, enabling the restoration of belts that might previously have been beyond repair.
Ipco also highlighted the QuickDisc Plus 500, a repair tool used for removing the damaged area of a belt and cutting out a replacement disc from the spare section that the company supplies with every belt. This is a self-contained cutting and welding system that can be used to repair damaged areas up to 480mm in diameter on steel press belts.
Electronic Wood Systems (EWS), measuring system and spark detection/ extinguishing system supplier, arrived at Ligna “fresh” after making several recent changes to strengthen the company.
Dr Konrad Solbrig was appointed technical director and Jan Deutschmann is the new commercial director.
Dr Solbrig reported satisfaction with customer meetings at Ligna, with both existing and new customers, while also spotlighting several new EWS developments, including the new generation spark detection and extinguishing system ALF 9000 and spark detector EWS HSSD.
The HSSD stands for High Sensitive Spark Detector and it works like a temperature sensor, detecting very low-energy ignition potentials depending on the material temperature.
EWS has also expanded its production building by more than 30%.
Dieffenbacher celebrated its 150th anniversary at Ligna (for more on this see a special report on page 40-41).
On its stand, digitalisation was a big focus, with a large video screen showing the second line to use its Evoris digital platform at Swiss Krono’s Menznau plant.
“The world is changing with megatrends such as digitalisation,” commented Dieffenbacher CEO Christian Dieffenbacher at the show. “Four years ago we had the idea but today we have solutions”
The company has 30 staff working on digital solutions today, a tremendous increase in just a few years.
Evoris features 12 apps to enable full machine and process connectivity across the entire plant, providing a modern user interface to panel producers to have visibility on plant efficiency.
“One of the key purposes of this platform is to help customers avoid stupid mistakes,” said Stefan Zipf, head of Dieffenbacher’s business unit wood.
Another four Evoris systems are being added this year and up to 20 in the next two years.
At the 2025 Ligna, Dieffenbacher expects to present autonomous operation AI, with an aim of reducing downtime and increasing quality. Testing of this has resulted in notable increases in efficiencies.
Industrial short-cycle press systems are the specialism for Wemhöner.
Wemhöner product manager Detlef Hanel reported a short cycle press line order early on at Ligna. Wemhöner’s stand this year featured an increase in space for meetings and less room for displaying machinery.
Wemhöner used its decades of experience in other laminating fields to develop the VARIOPRESS systems.
The company has further developed the VARIOPRESS for the production of furniture fronts and furniture components based on thermoplastic foils.
CMC Texpan had experts on its parent company Siempelkamp’s stand. Gianluca Gassa, project manager at CMC Texpan, explained that the Ecoformer SL was making waves for its improvements to the forming process.
The SL is an evolution of the traditional wind forming concept. Benefits include reduced energy consumption, a quick return on the capital investment, good air infeed, improved distribution of the material, faster operation, a reduction in maintenance time and a better surface quality.
Deurotech had a strong Ligna presence with its stable of companies, including VITS, IFA Technology, Wessel, airprotech, Eisenmann and Oschatz Power.
“We are quite happy with the show and we’ve had a lot of traffic,” commented CEO Werner Deuring.
Deurotech has had record order levels in the past 18 months, though Mr Deuring says orders have slowed down more recently.
The group expanded its offering with the acquisition in February of Oschatz Power, which supplies power plants, particularly steam boilers and incinerators, for the use of biomasses, recyclables, and other fuels.
Mr Deuring said energy is a hot topic, with efficiency and energy recovery needed to reduce costs for customers.
On the impregnation side, he said an industry focus was to eliminate the human factor as skilled operators were in short supply. So, automatic feeding systems and controls were of increasing interest.
SMARTECH was a first time exhibitor at Ligna and its offering of SMARTWAX and SMARTMDI suspension systems certainly chimed with the wood-based panels industry’s desire for increased production efficiency and cost savings.
As well as its expanding business in suspension systems, the company was promoting its Autonomous Manufacturing platform.
The AM platform has been implemented in the wood-based panel sector increasing production and stabilising the production line. Furthermore, SMARTECH is partnering with Siempelkamp on this venture, with the latter marketing it as ProdIQ – SmartPress.
The company’s background in process and mechanical engineering has been complemented by data and AI expertise to develop the ‘Autonomous Manewfacturing’ AI solution – designed to aggregate production data and human operator inputs to optimise critical production processes.
SMARTECH experts did technical presentations at the Siempelkamp stand and Oren Yahav, AI director at SMARTECH, presented “Is Autonomy the Future of Wood- Based Panel Manufacturing?” on the Ligna Stage in Hall 12.
CEO Hanoch Magid said SMARTECH’s advanced solution attracted a lot of attention at the show and reported many visitor requests for further information.
Steel belt specialist Berndorf Band Group, which counts the wood-based panels and decorative laminates sectors as being big customers reported a good Ligna attendance at its large stand. It has a number of training and service tool initiatives to help boost efficiency for customers.
Its Mobile Training Centre 2.0 helps operators to be able to repair minor damages by themselves and gain skills needed to recognise and evaluate risk factors for belt damage at an early stage.
Energy systems were very much a hot topic at Ligna and Turboden came to the show with the news it is supplying Turkish panels producer Kastamonu with two ORC systems (13.6Mwe each), with one already in operation.
Turboden says its ORC technology in the Kastamonu project would offer a CO2 saving for electricity production of 3,000t/year and for thermal of 6,200t/year.
Turboden says panel producers can exploit their wood waste to generate combined heat and power.
ITALIAN FINISHING TECHNOLOGY
Italian sanding technology manufacturer IMEAS promoted its range of EvoL sanders and automation solutions aimed at new market segments. This includes the EvoLSide which sands glulam beams on all four sides, while EvoL-CLT sanders can process CLT panels up to 3600mm (12ft).
Francesco Zenere, IMEAS CEO, reported requests at Ligna from Indian HPL manufacturers, as well as plywood and CLT producers. There were also discussions with traditional wood-based panels producers exploring entering CLT production.
For factory automation and integration IMEAS’ offer includes the Full Control System PLUS (FCS+), a complete hardware and software package capable of communicating with factory management systems (MES, ERP) to control the sanding process.
Fellow Italy-based company Cefla, a finishing technology specialist, conducted a press tour to show its innovations, including the patent-pending Easy oscillating spray coater with FCS (Fast Colour Switch). This enables batch one colour changing in less than 10sec without stopping the line.
Cefla says the new time-saving technology reduces downtime by approximately 45-60mins/day, with additional benefits of a significant reduction of wasted lacquer at each colour switch, reduced consumption of water or solvent used to flush out lacquer of the unwanted colour is also promoted as a benefit.
Another exhibit – Smartvacuum – is designed as a cost-efficient solution for edge finishing using vacuum technologies for 100% UV acrylic paints. Used together with Smartedge, it is designed for companies to match the edge and surface finish perfectly, depositing 100/140g per m2 of 100% UV lacquer in a single step.
Longoni was excited to unveil its LAMIDRY technology at Ligna – a patented process that allows it to treat decorative and kraft paper surface with dry resin. Compared to the standard wet process, LAMIDRY is designed to use less resin, avoid polluted emissions and reduce energy consumption, machinery dimensions and investment cost. The company also says high speeds of 300m/ min can be reached.
“People are very much interested in it,” said president Roberto Longoni, reporting interest from South Korea and India.
Meanwhile, IMA Schelling’s two business units Woodworking and Board were represented on two stands at Ligna. For panels, it had video screens showing its technologies for conveying, lifting, sorting and storing boards.
The cutting, logistics and packaging solutions were aimed at manufacturers in wood-based panels, including plywood, plus solid wood boards.
Together with two regional partner companies from Austria, Künz Kranbau and LTW Intralogistics, IMA Schelling presented itself as an attractive partner for high-quality automation solutions in the panel-producing industry.
Stefan Hinterholzer, board business unit manager, said board industry projects were delayed in 2022 H2, when furniture industry demand fell after two strong years. However, he reported that by the end of 2022 demand was returning, with orders re-activated and more and more new projects coming forward.
“Currently, I get the feeling there is still demand and we see at the show that the direction we have been going in with automation at the finishing end of board production is getting more and more demand,” he said.
Customers, he added, were seeing product damage from forklift movements of panels, as well as a lack of efficiency from traditional handling methods.
Mr Hinterholzer reported five new enquiries for automated packaging lines.
Pressing line supplier Pagnoni Impianti celebrated its 175-year-old history at Ligna.
Director Michele Pagnoni reported that the Pagnoni stand was very crowded on Tuesday and Wednesday at Ligna.
Pagnoni has new lines to be delivered in Europe and Asia for the construction of multi-opening press lines for HPL production designed with a flexible solution, able to respond rapidly to the market requirements.
“Things are going very well and this exhibition was in the right moment,” said Mr Pagnoni. He reported several ongoing projects and discussions about new business as well.
Kleiberit had an exciting display where it demonstrated for the first time at a trade show what it calls a new dimension in surface quality using electron beam curing (EBC) under the name “HotCoating Extreme”.
Examples of applications include particularly highly stressed horizontal surfaces such as worktops or exterior applications. This technology is particularly aimed at large panel manufacturers.
Holger Scherrenbacher, Kleiberit’s head of technology centre, said examples of applications include particularly highly stressed horizontal surfaces such as worktops or exterior applications. This technology is particularly aimed at large panel manufacturers.
The EBC technology is designed to be integrated into a HotCoating system. Therefore, Kleiberit says, it is possible to switch from UV curing to ESH curing without major technical difficulties.
Outdoor terrace decking featuring digitally printed planks coated with HotCoating Extreme were exhibits on the stand.
Fire protection and measuring technology specialist Fagus-GreCon, had a strong presence at the show.
Managing director Uwe Kahmann told WBPI the long-established inline Thickness Control had been improved to increase accuracy and calibration.
Other innovations include EDGEINSPECT, a laser camera system capable of picking up the smallest of faults on furniture boards, as well as GasAnalyser MC – described as the next step in formaldehyde emission testing.
GasAnalyser MC enables emission testing without lengthy traditional chemical lab testing. The process takes just 15min per sample.
Mr Kahmann described emissions as a big topic for panel sector companies.
Meanwhile, in the fire prevention area, Fagus-GreCon’s digitalisation programme continues with the presentation of its intelligent extinguishment technology (IET). Its diagnostic properties can detect wear effects and prevent downtime.
Mr Kahmann said the company had enjoyed a successful 2022 and first quarter of 2023, which he described as “tremendous” in terms of orders. Customers, he added, were making orders earlier than in the past.
Swedish fire protection systems specialist Firefly AB specialises in creating customised system solutions.
Firefly says about 30% of its business is in the wood-based panels sector, with a strong market position in Asia, particularly Thailand. The company sees India and Pakistan as growing markets.
Firefly says its technology identifies ignition sources as soon as they emerge and targets them with water mist.
Fusoni’s Monica Bobes reported a “very busy show” in Hannover, reporting visitors from the likes of Asia and Canada. She said flame retardant products were a focus of attention for panel producers.
During the last three years, Fusoni has strongly worked in R&D to develop a complete range of high quality liquid flame retardant products suitable for the different type of panels as well as for laminates.
It also produces release agents and additives for wood-based panels.