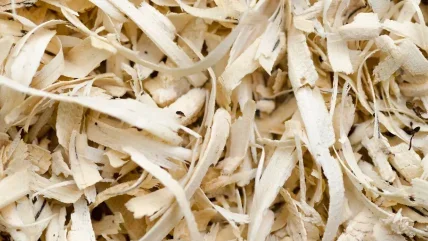
Used in the manufacture of panels such as OSB, MDF, particleboard and lightweight wood fibre insulation products, MDI (methylene diphenyl di-isocyanate) is, says Huntsman, a versatile and efficient binder which provides a supreme bond with the wood particles or strands as it has a reaction with the wood itself when put under intense heat.
With MDI resins you mainly have chemical bonds, whereas with formaldehyde-based resins you have mainly mechanical bonds. In the case of formaldehyde products, it is clear to see where one material starts and another ends.
However, MDI bonds by forming a diffusion interphase in which the resin spreads over the surface of the wood and penetrates into cracks, cell lumen and even cell walls. Penetration depths of up to 1mm are readily achieved, which is well beyond the three cell depth commonly assumed to be needed for wood resins to provide adequate adhesive strength. In the diffusion interphase, the MDI effectively becomes one with the wood and this, along with the penetration and the spread, is responsible for the high quality performance expected from MDI-bonded wood, including the resistance to thickness swell, and the high strengths.
Advantages that add up
The benefits that MDI, with its strong chemical weld, can offer wood panel producers include the following, claims Huntsman:
• Increased mill productivity, creation of better operating parameters and savings in drying, blending and pressing. Increased tolerance to a variety of wood species
• Increase in the panel’s physical property performance
• Increased ability to manufacture speciality products
• Reduced blender cleaning
• Fast curing
• Ease of adding biocides or fire retardants
• Finished panels that are smooth, light and more natural in appearance
• Improved moisture resistance
• Excellent strength to weight ratio
• Compared with traditional formaldehyde options, MDI resins require a lower dosage, making it a cost-effective binding option when comparing on a cost/m3 basis.
OSB: A case for MDI
OSB is an engineered wood strand panel designed to be very strong, hardwearing, smooth and defect free, making it a superior alternative to some plywoods available on the market. Ideal for all manner of building projects – from flooring, roofing and timber-frame housing to smaller scale applications such as packaging, exhibition stand construction and boarding-up open windows on site for temporary security – OSB’s strength and reliability originates largely from the way in which it is produced.
A key component in the production of OSB is of course the adhesive chosen to bind the strands of wood together; it has a huge part to play in determining the quality of the boards produced, says Huntsman.
There are various adhesives available for OSB production and the binder of choice differs from country to country, as Bart Singulé, business manager at Huntsman, explained: “Phenol formaldehyde (PF) resins have traditionally been used by OSB manufacturers, however this is no longer as commonplace as it once was. Driven mainly by the cost-effectiveness of MDI and the increased productivity rates offered, more manufacturers have been making the switch to standard polymeric MDI in the core layer of OSB boards.
“MDI is one of the most effective adhesives that manufacturers of OSB can use, either within just the core layers of the panel or within both the core and face layers, to give their panels strength. The real advantage of MDI is the strong bond it forms with the wood strands, which results in a tough construction at the pressing stage. MDI also allows for shorter press times than other resins and it works at lower temperatures, increasing productivity and saving energy for manufacturers”.
Mr Singulé continued: “In Europe, MDI resins have been fully embraced by the composite wood panel industry, with all OSB mills using MDI resins in the core layer, and many taking things one step further by switching to catalysed, or fast-cure, resins.
“Once the benefits of MDI resins are demonstrated to them, producers have quickly taken this up as their normal practice.
“The argument that using MDI resins in OSB production creates better economics when compared with using melamine-urea-phenol- formaldehyde (MUPF) is so convincing that many European manufacturers use 100% MDI in both the face and core layers of their boards.
“Significant improvements made in release agent technology to prevent the MDI sticking to the press platens have also been made.”
“Furthermore,”continued Mr Singulé, “When comparing MDI with MUPF, MDI performs better due to the nature of its adhesion to wood. The wood surface naturally has a lot of chemical groups called hydroxyl groups (-OH). MDI resins are terminated with isocyanate groups (-N=C=O), which react with the (-OH) hydroxyls on the wood, forming urethane linkages. These linkages help to make the MDI-bonded boards perform better when exposed to moisture”.
Constant innovation
When MDI resins were first used in the manufacture of OSB, a standard MDI grade was used for the core resin. Developments from Huntsman over the last 10 years have led to the introduction of faster grades of MDI that allow for ever-shorter press factors.
Fast-cure MDI resins typically improve the press factor – the measure an OSB producer uses to articulate the speed of the process – by around 15% compared to standard polymeric resins, said Mr Singulé.
“Huntsman has over 25 years’ experience in composite wood products and was the first company to commercialise such products in Europe, with our I-BOND OSB FC 4310 and IBOND OSB FC 4312 resins”.
Recently, Huntsman has launched its latest resin development for OSB production – enhanced fast-cure resins. Encompassing an all-new MDI technology which differs from the previous approach, the company says this resin range sets a new standard within the composite wood panel market and delivers a further 10% improvement over the rates achieved by its current fast-cure resins. It claims the benefit to the producer is quite considerable.
“An OSB producer can make more square meters of board by using our enhanced fastcure resins,” explained Mr Singulé, “which in turn means they can obtain more from their assets and therefore dilute their operating costs. It also results in reduced blender maintenance costs, in terms of time needed and frequency of cleaning required, lower formaldehyde emissions and lower drier energy requirements.
“We also provide complementary release solutions to ensure a smooth, complication-free production process. At the Ligna show last year, we launched the new I-RELEASE OSB 9126 external release agent, which is a new improved release system for external application for 100% MDI based OSB.
“These latest products demonstrate our commitment to leading innovation within this market to deliver real solutions with tangible benefits to the producer and end user.”
Global Trends
A report by consultancy BIS Shrapnel in 2011 predicted an upturn in the global economy over the next five years, with a general increase in demand for OSB and plywood, driven mainly by housing construction and furniture manufacturing.
“Although the overall outlook is positive, major events such as natural disasters and changes to taxation laws in countries renowned for the manufacture of plywood, will have a negative impact on the rate of production,” concluded Mr Singulé. “This will leave the demand for this particular material largely unmet and with all eyes quickly turning to more resourceful alternatives, many countries are predicted to increase their consumption of OSB. This switch will not only compensate the shortage of plywood, but will meet the increasingly stringent criteria for sustainable building.
“In anticipation of such a boost to the global economy over the course of the next five years, Huntsman believes that there will be strong growth projections for OSB in Asia, Eastern Europe and Russia in particular,” he said.
“With this in mind, there’s certainly a great opportunity for the growth of OSB on a worldwide scale as more countries recognise its practical, structural and environmental benefits. Furthermore, OSB is a competitively priced substitute for plywood and this will only encourage considerable growth in the near future. Producers will be looking to ensure they can meet this demand with OSB panels which are consistent in quality and cost-efficient to produce, while also meeting the demands of increasingly restrictive legislation, and MDI ticks all the right boxes as the ‘no added formaldehyde’ solution.”