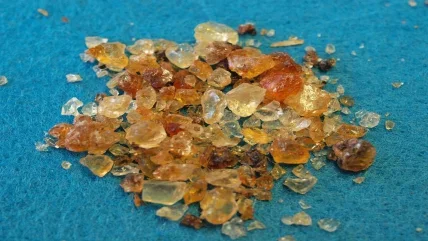
PUR hotmelts are widely used in furniture manufacturing. Conventional adhesives, however, contain monomer isocyanates that can cause irritations and allergies upon exposure during machine processing if the processing guidelines are not fully adhered to.
Isocyanate compounds are a fine thing for chemists. Compounds such as methylene diphenyl diisocyanates (MDI) have a weakness for OH groups, chemical functional groups that occur abundantly in wood. When the two meet, they react to form permanent bonds. In other words: they stick together reliably – come heat or cold, high or low humidity, mechanical or chemical stress.
But this highly useful cross-linking capability in classic two-component adhesives and polyurethane hotmelts also has serious drawbacks: monomer isocyanates in high concentrations are harmful to human health. Users of furniture that contains such adhesives are at no risk – in the finished product, the adhesive is fully cured and releases no more monomers. The hazardous stage is during processing when hot vapours are discharged. Improper use can cause serious damage to health.
The EU authorities have long had an eye on this group of compounds. Among others, the REACH regulations were changed in 2020 to include better protection of staff in processing facilities. The transition period ends on August 24, 2023, after which every employer who processes products containing more than 0.1% of diisocyanate will be obliged to train their staff accordingly. Such trainings are extensive and must be repeated at least every five years. In addition, complex technical provisions such as extraction units and containment will become obligatory, and every employee must be provided with appropriate protective equipment.
Furniture manufacturers are also subject to these regulations. In order to sidestep the expensive training obligations (and to ensure a non-hazardous working environment for their staff), most companies are turning to the newer generation of micro-emission (ME) adhesives. Weingarten-based Kleiberit already offers its customers appropriate solutions since some years.
But that’s not all. In an ongoing research and development project, the PUR adhesives specialists are in constant contact with their customers from the textile, automotive, and furniture industries. Kleiberit is already looking much further into the future.
“Wood industry manufacturers, in particular, are today much more interested in where raw materials are sourced,” said Kleiberit managing director Leonhard Ritzhaupt.
He knows this from numerous discussions with customers, while end users also have a heightened awareness for the ecological footprint of furniture.
Wood sourced from certified forestry, fair trade textiles, lacquers and varnishes based on renewable raw materials – all these have long become important sales arguments for well-informed customers. In turn, flooring and furniture manufacturers, to name just some examples, are scrutinising their suppliers accordingly – also when it comes to the use of adhesives. Several large accounts from the wood industry have expressed a strong interest in isocyanate-free adhesives, in order to meet their standards of ecological and sustainable production.
With this in mind, Kleiberit set about developing a new generation of reactive adhesives that surpass the ME standard and get by without any isocyanates while still providing the same functionality.
As reluctant as the adhesives experts are to reveal their formulas, they are more enthusiastic about the results of their intensive engineering efforts.
“It is no less than a world first,” said Kleiberit marketing manager Peter Mansky.
“We have managed to develop an isocyanate-free reactive hotmelt that is as effective as the existing systems and can be used with conventional processing equipment and the established methods to produce the same, if not actually better, results,” he said.
CEO Mr Ritzhaupt added that the processing temperature is even a few degrees lower, which also helps to save energy.
This new Kleiberit 736-hotmelt series has undergone several trials in the company’s own Technology Center which, with its edge banding, hotcoating and flat lamination equipment, at first sight looks like a small furniture factory.
The result, Mr Ritzhaupt said, is an adhesive that proves itself beyond the wood sector and can cope with mineral surfaces such as glass or metal significantly better than isocyanate-containing products.
“Not only have we covered PUR applications, but we have also opened up completely new fields of application,” he said.
“With this new hotmelt, furniture manufacturers will be able to convince their customers and, at the same time, shelve the REACH training obligations. On top of that, they will be sending an important message to their staff that they take health issues seriously and give a lot of thought to the working environment in production facilities.”