Banking, luxury watches, cuckoo clocks, chocolate, cheese, skiing holidays. Ask anyone what Switzerland is famous for and at least one of these products or services will be quoted – unless you ask someone in the panel manufacturing industry. Then you will very likely hear the word Steinemann.
Established in 1917 producing textile machines, the company started making wide-belt sanders for the panel industry in 1960.
In 1976, it added UV varnishing machines for the graphics industry to its product range and has continued to specialise in those two market areas ever since.
Part of the Stürm Group since 1987, Steinemann Technology AG has grown into a company with a turnover of e45m with 240 employees and a worldwide market to which it exports 98% of its
production.
In January 2003, in response to the continuing growth of the company’s business, Steinemann moved into completely new premises in St Gallen, near Lake Konstanz (or Bodensee) in the north of Switzerland.
This move was only a few metres from the company’s original home, but provided much-needed extra space to accommodate the increasing production demands in both its major markets.
Steinemann’s wide-belt sanding business has benefited from the very healthy demand from the panel industry in the last three or four years, as have most machinery suppliers, and the company has seen its typical delivery time extended from five or six months to 12 months, particularly since the Linga exhibition in May 2007.
“The sander accounts for probably less than 2% of the total project cost for a new panel mill, but its failure can shut the whole factory down,pointed out Hansjörg Fritsche, vice president of Steinemann Technology AG.
“The customer wants consistent panel quality to his required standard and that is what we offer. But the machine is only part of that. We are a total solution provider with the machines, spare parts, abrasives, service and process support. First-class panels can only be achieved when all these parts of the process are perfectly attuned to each other. And the abrasives themselves are as important to panel quality as the machines are.”
This may explain why the company has established its own conversion plant for these abrasive belts, in Shanghai, going into commercial production early in 2008.
“We will deliver about e2m-worth of belts in this, our first year of operation, supplying to markets such as Asia, Asia-Pacific, Turkey, South Africa, the US and Russia, initially. We have installed the most modern conversion machinery from Italy and are producing a high-quality product,said Mr Fritsche.
The Chinese operation is only supplying paper- and polyester-backed belts at present, but in early 2009 plans to start converting combination belts, which have a backing that’s a mix of paper and cotton.
Another recent development from Steinemann to optimise sanding quality is the SprintSystem sanding platen. This is a replaceable insert in the platen which can be quickly exchanged as wear takes place. It consists of a carrier of foam, felt or latex, depending on the customer’s specific sanding requirements, with a graphite surface on top, which bears on the back of the abrasive belt.
The two ranges of sander offered by Steinemann are the Nova-H and the Satos.
The Nova-H is the smaller of the two. It has a steel cast frame and can sand panels up to a maximum width of 1700mm.
This range of sanders is also produced at Steinemann’s factory in Jiading, close to Shanghai, where the abrasive conversions are done. The company makes smaller graphics machines here for regional markets as well. The factory employs 65 people.
The Nova-H tends to be popular with plywood manufacturers as well as smaller composite panel mills but machines for plywood sanding are mainly produced in St Gallen as they require some more
special attention.
In October 2008, a Russian customer took delivery of a Nova-H for its plywood plant, having already purchased a Satos eight-head unit in 2001 for its particleboard line.
The Satos, launched in 2001, is in a different league and is produced only in St Gallen. The sanders in this range are all built on mineral cast (siliceous limestone/epoxy polymer) frames. The reason for using this form of construction, according to Steinemann, is that it offers low vibration and temperature-stable machine components, is corrosion-resistant, non-conductive and has good noise transmission characteristics.
Currently the Satos is available in three sizes, with maximum panel widths of 2250mm, 2850mm, or 3300mm respectively.
“We have sold approximately 920 Satos heads to date and over 700 of those are in operation, with the rest on the way to the customer, or in the production pipeline,said Mr Fritsche.
Steinemann has nine service centres worldwide, in North and South America, western Europe, Russia, China, Malaysia and Australia.
“These are not just offices but our staff are out and about working with customers. We started building up these service centres about 10 years ago, beginning with Malaysia,said Mr Fritsche, who used to run the Malaysian centre before returning to Switzerland to take up his current position.
Sales manager Michael Schmid outlined the more active markets of recent times.
“The hot markets recently have been Turkey and Russia,he said. “We have sold at least 150 Satos heads to Turkey so far and they are all big lines with 10 to 12 sanding heads.”.
This is mainly because the customers are finishing their panels with direct printing, lacquering or thinner papers and so need a particularly fine surface, explained Mr Schmid.
A factory in Gagarin, Russia, started up in September with a Satos eight-head machine for particleboard.
In early October, a Nova-H six-head sander was delivered to The Perm Plywood mill owned by the major Russian plywood group Sveza.
“We have sold a total of 16 lines to Russia, including recent orders from Pfleiderer for its Novgorod plant, Rimbunan Hijau for its plant in Siberia, and Ugraplit. All these are due for shipment soon,said Mr Schmid when WBPI visited St Gallen on the last day of October 2008.
There have also been two recent ‘firsts’ for the Satos: the first Satos machine to be delivered to South Korea was shipped in early December to Kwangon MDF and the first to Japan will go to Okura, for particleboard, in the first quarter of 2009.
Looking to the future, the St Gallen factory employs, on average, 30 apprentices in a special area of the factory which has recently been equipped with a brand new five-axis CNC milling machine just for the apprentices, in addition to other drilling, milling and tapping machinery. The main factory is also equipped with the latest computer-controlled machines.
Senior apprentices take some responsibility for quality control in the factory and many stay on as full-time employees.
While manufacture of some of the larger basic components is contracted out, all contact rollers, and all other kinds of rollers, are manufactured inhouse in St Gallen. The contact rollers are machined with grooves, coated with Arctec chromium alloy for wear resistance and re-machined in the factory.
All components are extensively tested for balance and vibration-free operation. All machines are sub-assembled in the factory and similarly tested before despatch to the customer’s site, where they are united in the full machine.
Many companies are fearful of what lies ahead in these uncertain economic times, but Mr Schmid is sanguine about Steinemann’s market in the coming months.
“Next year [2009] was always going to be quieter after all the capacity established in the last three years and the global economic situation adds to the uncertainty, but I see no reason to expect ‘disaster’ in 2009, although there will probably be some projects delayed – there already have been some.” n
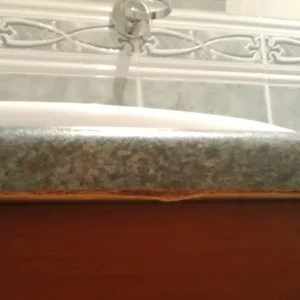