In what is currently a very quiet market for new panel production facilities, Instalmec of San Giorgio di Nogaro in Udine, has its eye on new products which will help to strengthen its position as a supplier of systems for cleaning and drying the raw material for the production of MDF and particleboard.
Instalmec has been present on the Italian panel market since its formation in 1978.
That experience is important in that Italy is one of the major users of recycled, or urban, wood in the production of panel products, due to its lack of trees. It has enabled Instalmec to reach a position where it currently exports around 70% of its production all over the world, utilising this expertise.
“Most of our clients are using recycled wood and the contamination in this raw material is a major problem in the management of these mills,said Adriano Stocco, managing director and founder of the company. “Many of the conventional systems on the market at the moment have some problems and consume a lot of energy,he added. “The problem for the panel makers using recycled material is the quality of the final product as well as the wear and tear on their production line – and we must not forget the danger of fire; the quality of cleaning of this material is very important.
“Our aim is to produce reliable machines which reach a constant, high production quality in the final product – the panel.”
His company has patented three new machines in the past year aimed at achieving this end. One of these is a new, pneumatic, screen at the outlet of the dryer, which can also be used in the wet area of the mill.
“Traditional screens oscillate and they can get blocked after a few hours, leading to reduced effectiveness and the larger particles staying on the screen. Then it has to be cleaned,he explained. “Our screen is selfcleaning by a counter-flow mechanism and, due to its shape, it gives better separation of the different fractions, taking out all the very fine fraction, which can contain silica, metal, plastic and so on, which would otherwise end up in the surface of the panel.”
He claims that this produces a whiter, smoother panel, as well as increasing production on the press line by 10 to 20%, according to several customers who have bought this system.
The pneumatic screen is also claimed to eliminate problems of spontaneous combustion in silos, partly because it allows for de-gassing of the particles, but also because the dryer and screen operate in a vacuum rather than a pressure system.
The second of the new patents is for part of Instalmec’s new layout for the production of raw material from the woodyard to forming, for both MDF and particleboard.
This is a new cleaning system in the wet area with a gravimetric separator – the subject of the patent – for larger contaminants such as glass, rocks, metal, silica and rubber. The system is claimed to have low energy consumption and to reduce wear and tear in other parts of the production line.
The third new patent is a complete, integrated, low-temperature system for the drying of sawdust in the preparation of fuel pellets. These used to be produced from fresh wood, but rising demand for the product has led to recycled wood being increasingly used in its production, said Mr Stocco.
“The particular problem with these pellets is that the moisture content has to be just right to ensure that the sawdust sticks together to form the pellets. It needs to be in the range of eight to 12%,he said. He believes this dryer will interest panel makers who have excess waste from their production lines.
In collaboration with Geoenergy, Instalmec is also developing a new generation of wet electrostatic precipitators, or WESPs, which Mr Stocco said will have many improvements on the existing units.
Another new product, which he said is unique to Instalmec, is a new generation of vacuum dryers for particleboard, single- or triple-pass.
“We guarantee five years of no wear and tear for the complete dryer system – the combustion chamber, dryer and cyclone battery,he said.
Instalmec has also developed a new combustion system to burn sawdust from the screens and waste dust from the WESP. “The combustion chamber has been studied and re-designed,said Mr Stocco.
“As before, it has fully automatic ash extraction, which means no downtime for cleaning. But now we have introduced new technologies for the pneumatic system, including the vacuum system in the dryer.”
Operating the dryer in a vacuum rather than pressure situation means it avoids wear and tear to the fan. The company has also re-dimensioned the drum’s internal parts to improve the drying process, by improving the mix of air and particles and reducing wear and tear there also. “In this way we guarantee even drying throughout the material in the dryer, whether it is large or small particles,said Mr Stocco.
“The experience of Instalmec, and our R&D, are very important,he said, stating that Instalmec spends around €500,000 a year on R&D.
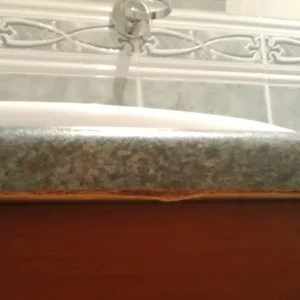