Chimar is not itself a resin producer, but its direct customers are. Eleftheria Athanassiadou, Chimar’s R&D support and Industrial Property Rights (IPR) Protection manager explains:
“Chimar is a developer and provider of industrial technology for resins and chemicals for wood based panels, offering technology licensing, manufacturing support and application support.
“It is also active in industrial engineering and plant procurement for formaldehyde, urea formaldehyde condensate (UFC), resins and chemical additives.”
To use as an illustration the client nearest to Chimar’s home, resin manufacturer Hadjilucas SA has a factory in Komotini in northeast Greece producing urea based resins. This production plant was designed, procured and built by Chimar and consists of two units: The first went into production in 2000; the second in 2002.
Chimar’s connection with that plant did not end with its completion, but is ongoing to this day, with the company supplying technical know-how and support and continually refining and developing resin recipes in cooperation with Hadjilucas. The latter company is in fact a licensee of Chimar and is one of a number of such licensees around the world.
“We have licensees in all continents and many of them have been licensees for 30 years or more. We consider them as partners,says Ms Athanassiadou.
Chimar does not just have resin producers as customers, but also works with its customers’ customers, who are the panel makers themselves. Hadjilucas supplies resin to all the panel makers in Greece and also has customers in other countries, notably Bulgaria, and Chimar works with those companies as well. Using its expertise, and its laboratory and pilot line facilities, Chimar develops solutions to the problems and needs of those panel makers. For instance, they may be utilising a new wood raw material, or wanting to produce a new specification of panel, and this is where Chimar can assist.
Some panel makers are also themselves resin producers, having resin plants on their panel sites and then they can become direct customers and licensees of Chimar.
“However, even if the panel maker buys its resin from another supplier, we can and do help them to improve their process,says Ms Athanassiadou.
An increasingly important area in this regard is formaldehyde emission and a lot of Chimar’s work is in helping panel makers to achieve, or indeed exceed, regulatory limits in their country of production.
“We are a forward-innovating, knowledge- intensive company focused on providing green technologies and on fulfilling ecoefficiency principles,continues Ms Athanassiadou. “We offer customer-focused R&D, technical support and training, as well as value-added services such as industrial property rights protection and quality management systems (QMS) development and application. And we are continually developing our know-how in house.”
Chimar Hellas is a privately owned business in which the main shareholders are Mrs Effy Markessini, chairman of the company, and Mr Dimitris Alexandropoulos, managing director and main point of contact with the customers.
Mr Alexandropoulos speaks English and German fluently and, between them, the staff of Chimar speaks many languages, including Arabic, Russian and Bulgarian as well as the more commonly spoken western European languages.
“The ability to speak other languages is one of the key attributes of potential employees as we are a very international company,says Mrs Markessini.
It is of course also a very technically based company and out of 28 employees only six have non-technical, administrative, roles. The technical people include, among other disciplines, chemists, chemical engineers (such as Mrs Markessini’s son Charles), wood and petroleum technologists and electrical and computer engineers.
The R&D activities in Chimar comprise medium- and long-range projects as well as short-range or troubleshooting; technical support with field chemists and engineers serving customers in situ; and the funding and administration of long-term projects.
“There is a continual feedback to R&D,explains Panagiotis Nakos, a chemical engineer and senior representative with Chimar. “Our people in the field have a rapid response from our R&D department to get answers for our customers if we do not have an immediate solution to the problem on the ground. They have immediate priority for answers from R&D.”
Facilities at the R&D laboratory in central Thessaloniki include a near-infra-red (NIR) spectrophotometer for analysing the spectra of resin samples to gain important information such as polymerisation path; gel permeation chromatography (GPC); and high-performance liquid chromatography (HPLC).
“GPC tells us about the molecular weight distribution of polymers in a resin sample and enables us to calculate an average molecular weight for the resin, while HPLC is used for the analysis of the oligomers and additives in the resin,explains Mr Nakos.
“The NIR is a new development for fast analysis of resin and raw material, which produces a fingerprint of the resin in just one second, or to a higher accuracy in one minute. All these techniques are used for quality assessment of the resins.”
There are also laboratory reactors for quantities up to 10 litres. The results can then be scaled up in the larger reactors at the Chimar pilot plant outside Thessaloniki.
Conditioning chambers in the laboratory enable humidity and temperature experiments for formaldehyde and board sample property testing.
A Kjeldahl system is also available for analysing the molar ratios of resins. This process takes three to four hours and is used as a reference for developing other methods such as that based on the use of near infra red (NIR), like the Chimar trademark GNOSSI system.
Differential scanning calorimetry (DSC) is used in the laboratory as a thermo analytical technique to determine heat changes during the heating of a resin sample. As these heat changes are characteristic for a specific resin sample, this technique serves as a screening procedure and helps to predict the resin curing (polymerisation) behaviour.
The lab Ultra Violet Visible Spectrophotometer (UV-Vis) has many applications, such as measuring formaldehyde in the resin as well as in a board and, uniquely to Chimar, measuring the melamine in a resin.
The perforator method is also used in the laboratory to carry out measurements of formaldehyde levels.
One of the latest pieces of equipment is a stereo optical microscope.
“We have the software for creating a chemical reaction simulation before designing a reactor for a particular resin, using computational fluid dynamics, or CFD,says Mr Nakos. “It can also be used to predict resin distribution in dry resination, or to analyse the mixing of resin and hardener in a mixing pipe and so improve the mixing; we solved a mixing pipe problem in South Africa by this method in only 48 hours.”
The laboratory is also equipped with Zwick equipment, necessary to test the mechanical properties of panel samples.
The pilot plant is located 30km northwest of central Thessaloniki in a small town called Gefyra.
Here Chimar has a computerised press in which it can make 50x50cm samples of particleboard, MDF, OSB or plywood and it can set the pressing profile and thickness control just like a full-size panel production press.
There is also a blender to resinate the particles for particleboard samples. Chimar uses sieves to maintain a constant geometry of chips and an oven to maintain stable moisture content of the chips.
“It is important that the process is reliably repeatable,explains Panagiotis Koumakis, a chemical engineer and head of the engineering department of Chimar.
The pilot facility has two reactors: a 50- litre one with steam generator, vacuum system and distillation unit; and a new, one tonne reactor which is similarly equipped. These allow for scaling-up of laboratory tests.
“We have everything we need here for laboratory-scale board production for engineering test purposes,said Mr Koumakis. At the time of WBPI’s visit in early December, the engineers had also just completed a prototype mechanical blender for MDF.
One of the projects recently completed by the R&D department was the development of a continuous process for resin making, as opposed to batch production, but as yet this is still in the experimental stages.
There are obvious disadvantages for Chimar Hellas in having its offices, laboratory and pilot plant in different locations and a suitable plot of land has been located near Thessaloniki airport for the company to have built a purpose-made complex where all three operations can be housed under one roof. It is hoped that this project can be completed in about two years’ time.
The products and services offered by Chimar Hellas are: • Formaldehyde based resins of all types
• Laminating syrups for paper impregnation – urea formaldehyde (UF) and melamine formaldehyde (MF)
• Low-emission systems to EPF-S, CARB II and F standards
• Bio-based resins
• Speciality resin systems for laminate flooring, doorskins and MDF mechanical blending
• Additives such as hardeners, formaldehyde scavengers, resin extenders, fire retardants, water resistance and recycling agents
• Additives for laminating syrups
• Plants for the production of formaldehyde, UFC, resin and additives.
One major development created by Chimar is its trademark GNOSSI process. This stands for General Non-destructive Online Spectroscopic Interpretation. The patented process is unique and is used to control UFC solids and molar ratio, on- or off-line; to follow resin production online to ensure consistency and correct mistakes; to test raw materials for common contaminants and to test conformity; and online monitoring of impregnation lines for percentage of volatiles and resin take-up.
In paper impregnation, it can produce a usability index of impregnated paper to show whether the paper is still suitable to be used, thus cutting costs of impregnated paper wastage by unnecessary rejection of older papers which may still be perfectly viable.
In green technologies, Chimar is always looking at producing resins from renewable sources, halogen-free fire resistant panels and panel recycling technologies to produce produce new MDF.
Panels produced from annual plants are another area of ongoing research.
The company is also continually looking at new technologies to reduce formaldehyde emissions and the pressure is increasingly on the industry to achieve ever-lower targets.
Chimar claims to have produced formaldehyde emission levels at the level of natural wood in 1993.
In its scientific activities, Chimar Hellas has participated in 26 European-funded projects and three scientific networks.
A new area for the company is in industrial property (IP) rights, where it offers what it calls ‘techno-economic advice and support’ with regard to protection, exploitation and IP strategy formation and portfolio management.
Also new for the company is its service in Quality Management Systems – developing, applying and auditing them.
So Chimar Hellas can trace its origins back 32 years, with projects in 36 countries, and many of its licensees have been with Chimar for over 30 years.
It aims to be a facilitator, working in cooperation with its customers – and with its customers’ customers – not only in setting up and helping to manage complex resin manufacturing systems, but also in continually adapting its licensed resin production systems to meet the needs of the market – and of regulatory authorities around the world.
The company feels that these ‘traditional’ services, combined with its more recent activities in QMS and IPR, will ensure a long-term future for the business.
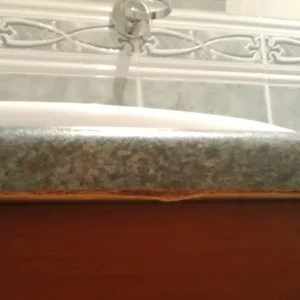