As at the end of October 2008, Siempelkamp Maschinen-und Anlagenbau GmbH & Co KG had sold 16 panel manufacturing plants during the year, giving it what Ralf Griesche, marketing and communications manager with the company, called “A brilliant year so far”.
This seems a fitting way to mark 125 years of Siempelkamp, which was and remains essentially a family-owned business.
A major new development for the company preceded 2008, when it acquired part of the Metso Panelboard company. This transaction took place on October 1, 2007, so its full effects were not really apparent until this year.
With this purchase, Siempelkamp assumed responsibility for the Metso Contipress (formerly the Küsters press) continuous press and all maintenance for existing Contipresses. The company will also take on the maintenance of the Bison and Mende-type presses supplied in the past by Metso and its predecessors.
Importantly, it also acquired the energy system of Metso Panelboard, which has become Siempelkamp Energy Systems, or SES.
“We have already tripled the business Metso had before in energy systems,said Heinz Classen, managing director of Siempelkamp Maschinen-und Anlagenbau, confirming the generally buoyant sales of the company in recent years. “There has been a boom for the last four years and we have an order book well into 2009, including 10 orders for our thin board lines since they were introduced in 2006, so we have had good success [in the market].”
However, with the current uncertainty in the global economy, Mr Classen admitted he was not sure how the future will shape up. Nobody is of course.
On the positive side, Mr Classen pointed out that world steel prices seem to have peaked. “This added 20% to our costs in the last three years although we have cut manufacturing costs during that time as well,he said.
Siempelkamp attributes part of its recent success to the latest evolution of its famous ContiRoll continuous press, as well as its special thin board lines employing that press as part of the whole
technology package.
“Generation 8 of the ContiRoll is not just an upgraded press but a revision of our whole production line for panels; we have made improvements from the complete area of the mat former to the press to the stacking area for finished boards at the end of the line,said Michael Vogel, manager of ContiRoll press design for the wood processing section of the company.
This rethinking of the whole line is also key to Siempelkamp’s recent concentration on, and successful sales of, thin board lines for MDF, mentioned by Mr Classen.
“Thin MDF with a thickness of 1.5 to four millimetres is increasingly replacing wet fibreboards and thin plywood and the market is demanding that machinery suppliers come up with concepts which ensure safe and economic production of these panels,said Mr Griesche.
Obviously, the only way to produce such thin panels economically is at very high speed and so this has been a major area of concentration for Siempelkamp in developing Generation 8.
The company now guarantees line speeds of 105m/min although it says its plants are capable of speeds up to 120m/min.
“We have optimised the fibre flow and the falling height of the fibre in the
forming bunker to achieve an even cross-wise distribution and to eliminate clumps of fibre and consequent damage to the steel belt of the continuous press,explained Mr Vogel.
“The StarFormer spreading head also has very fine gap settings to prevent any lumps getting through into the mat and to ensure an even lengthwise distribution of the fibre. We have achieved a forming accuracy of +/-2% for 3mm boards. There is then a downstream levelling unit to level the mat surface.”
Obviously the crucial phase is now the pressing of this carefully prepared mat and Siempelkamp has modified and enhanced its pre-press to cope with the higher line speeds.
For thin boards only, the company then offers its new compactor, which is installed after the pre-press and before the ContiRoll hot press.
“This has two wire mesh belts which evacuate most of the air from the mat. As the mat is compacted to nominal thickness, any lumps which might still be in the mat are squeezed out,said Mr Vogel.
“A precise head-cut following a mat dump, if any, enables the ContiRoll to continue at full speed of 2,000mm/sec. An accurate head cut is ensured by a special diagonal saw installed between the pre-press and the compactor for thin board production.”
If the panel maker wishes to make thicker MDF, he can simply open the compactor and allow the mat to pass through straight from the pre-press to the ContiRoll.
Now we come to the Generation 8 ContiRoll itself. For thin board production and shorter presses only, an option offered is to have directly-heated infeed drums, the shells of which are heated with thermal oil. Heat transfer from the stainless steel belts into the mat thus starts as soon as the mat enters the ContiRoll.
Not a new feature, having been available for nine years now, but an important one for thin board production as well, is the flexible press infeed. While the lower hot platen has a fixed geometry, the upper one is flexible and can be adjusted up or down by the hydraulic cylinders to any radius to enhance further de-aeration of the mat and start an optimal pressing process as early as possible. It also enables the achievement of high surface densities, thus eliminating sanding of the finished board, says Siempelkamp.
The press cylinders themselves are the same as those used in the previous generation. However, their number is increased and their position optimised for thin board production, it says.
Another special feature for thin boards in Generation 8 is the presence of pressure distribution plates in the lower half of the press to give greater stiffness and more equal pressure distribution, explained Mr Vogel.
Returning to those pressure cylinders, each cylinder row in the calibration zone is fitted with a position encoder, interacting with the automatic feedback from the board thickness sensors at the press discharge end.
Pressure and distance can also be precisely adjusted, row by row, for the right, inside right, inside left and left cylinders to give even thickness distribution.
“Because of the speed of these thin board lines, we offer a triple diagonal saw after the press, or the customer can opt for a clipper adapted from the carton industry for panels up to 3mm thick,said Mr Vogel.
The ContiRoll press essentially comes in three sizes. Size 1 has a frame height of 3.7m, while size 2 has a frame height of 5.1m to cope with the higher pressing forces involved when pressing wider boards up to 12ft. Size 2 is also used for very long presses.
Siempelkamp holds several world records according to Mr Vogel. For example, the first press of size 2 at Duratex, botucatu has a 50m ContiRoll for MDF, installed about seven years ago, and this was followed by even longer presses: Huber of Oklahoma has a 60m OSB press and Tolko Slave Lake a 70m unit, again for OSB production.
Now there is a new record, with Duratex again. This press was undergoing installation in November and is 77m long and nine feet wide. It is scheduled to begin producing 2,400m3 a day of MDF in the middle of 2009. However, 77m is just the effective pressing length. Total length is 90m and the overall line length is 174m. Total weight of the press is 2,200 tonnes and, if you really like statistics, the total pressing force is 53,000 tonnes.
A stronger roller rod chain has been developed to cope with these long presses and has more than twice the breaking load of a size 1 press.
At the other end of the scale, Siempelkamp has supplied the first of its new ‘size 0’ four-feet wide ContiRolls to Lishui of China. This press is 33.8m long and is due to start up in January or February of 2009, to produce something over 100,000m3 of MDF annually.
The markets for continuous press lines have moved quite dramatically in a geographical sense in the last 15 years or so.
Western Europe and North America have been less active in installing new capacity, while China of course has made spectacular advances in the last eight to 10 years.
A recent strong market for Siempelkamp has been Turkey, with five complete lines sold in a short period of time. The company has been in the Turkish panel market for nearly 50 years, initially with single- and multi-daylight presses, and supplied the first ContiRoll for MDF in 1994, to Çamsan. Since then, it has sold a total of 19 such plants to Turkey.
Three of the recent contracts are up and running, while a fourth is under construction on site. Number five is in manufacture at Krefeld.
Turanlar, whose factory is about one hour’s drive from Samsun on the Black Sea coast, bought a thin MDF plant to make board of 1.5 to 4mm at 2,000mm/sec. Capacity is 650m3/day at 3mm thickness and the first panel was produced in August 2008.
Meanwhile, Yildiz Entegre is currently installing a multi-opening-press doorskin line supplied by Siempelkamp complete with dies, which is due to start production early in 2009.
Kastamonu’s factory in Kastamonu City has a 7ftx55.3m ContiRoll to produce standard thicknesses of MDF and HDF. It started production in March 2008 and has a capacity of 900m3/day, 18mm thickness basis.
Yildiz Sunta, another major panel maker in Turkey, has ordered a particleboard line which is currently under manufacture in Krefeld. First board from this 7ftx42.1m press is expected in April 2009 and capacity is nominally 2,000m3/day, 18mm basis.
Starwood, also of Turkey, produced its first thin MDF on June 27, 2008 on its 7ftx28.8m ContiRoll press.
Apart from Turkey, Siempelkamp has also seen increasing sales to Russia in the last couple of years as Russian-owned
companies – as opposed to western European panel makers building lines in Russia – have set up production there.
Customers for ContiRoll lines include Ugraplit particleboard, Ivatsevichdrev particleboard in White Russia and Apscheronsk MDF.
The Siempelkamp group is not solely involved in the wood based panels market, but has products in the foundry and nuclear industry and other energy markets. It has recently invested heavily in these production facilities too and this balance of markets should hopefully reduce the exposure of the company to market fluctuations in the panel industry as the group enters its 126th year.
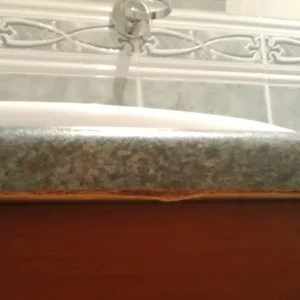