The company, whose name comes from Swiss Hellenic Wood Manufacturers, was founded in 1963 by Mr Panagiotis Iliadis and began by processing tropical wood for the production of sawn timber, plywood, block-board and decorative veneers. Then, in 1969, Shelman entered into the production of particleboard.
In fact, in recent years its main product has become particleboard – and its value-added products – plus some plywood.
The company today has two manufacturing plants: In Vassiliko Chalkis, where the company began; and in Komotini.
In the Komotini plant, particleboard, melamine faced particleboard (MFC) and impregnated films are produced, while in the Chalkis plant, particleboard, melamine and veneer faced particleboard and MDF, veneer lay-ons, conventional postformed and direct postformed products and plywood are manufactured.
The sawmill for tropical hardwood logs, which was also on the Chalkis site, closed down in 2006 due to a shortage of suitable tropical log supply.
Plywood remained a key product for the company for over 30 years, with maximum capacity of 150m3/day reached in 1995/6.
From the installation of the first plywood line in 1964, there was continuous investment in new machinery, culminating in the fourth line in 1989, purchased from Japanese companies Meinan and Taihei (the first such line in Europe), specifically to peel smaller-diameter logs.
Unfortunately for Shelman, the Asian financial crisis of the late 90s, and the currency crisis in Brazil, led to unsustainable price competition and, inevitably, to decreased production at Chalkis.
The switch from importing logs for veneer peeling to importing veneer from Africa and Brazil began in 1997 and today Shelman produces 50m3/day of tropical plywood, all from imported veneers, but this is high-quality material for niche markets.
The Chalkis factory also made block-board from 1969 until four years ago, when it stopped due to lack of demand.
Tropical veneer slicing began in 1970 on three lines, with a fourth added in 1979, but ceased five years ago. The clipping and jointing facilities are still used for imported veneer which is applied to Shelman’s plywood and particleboard and to bought-in MDF panels.
So the main product for Shelman today is particleboard. It has a capacity of 700m3 a day on its newest line, at Komotini – a Siempelkamp ContiRoll continuous press line which produced its first board in 2001. The press is 23.80×2.20m.
Komotini also has a 7.5m-long Siempelkamp short-cycle melamine press and a Vits paper impregnation line, housed in its own clinically clean building.
Both the Komotini and Chalkis factories are capable of producing 4 to 42mm particleboard to E1 standard as well as P5 moisture resistant (MR) grade; and fire resistant (FR) with P4 mechanical properties. If there is sufficient demand, they can also produce EPF-S very-low-formaldehyde-emission board as established by the European Panel Federation.
All production is certified to CE and formaldehyde emission standards by the WKI institute in Germany and around 15% is exported in Europe and to the Middle East.
The original site at Vassiliko Chalkis has a total of four particleboard lines (and all plywood and veneer production) although the oldest line is now inactive. This gives the site an active capacity of 430m3/day.
All four lines were supplied by Bison, with Dieffenbacher single-opening presses, and the latest was installed in 1992. The three active presses are 7.6, 6.2 and 14.8m long and all are 1.85m wide.
“We built this whole business with the philosophy that we had to produce one of the best-quality particleboards,said George Kalamaras, technical director of Shelman, who joined the company in 1979. “We sent a team of production and laboratory personnel to Germany for six months’ training with Bison and we set out to equip the factory with first class machinery and personnel to make a first class product with any quality of raw materials and with quality control. We achieved those targets.”
Mr Kalamaras is very proud of the attention to detail in both Shelman factories and claims excellent mechanical properties for the boards and an E1 formaldehyde emission standard since 1984.
“A big part of our achievement on formaldehyde is down to our cooperation with our partners, Chimar Hellas, since that time,said the technical director.
“Also, particle preparation is a ‘religion’ for us,he continued. “There are two main points: an optimum mixture of wood; and the geometry of the particles. We are experts in the art of particle preparation and have our own special way of doing it. The average and maximum thickness of the particles is part of this and we check, separately, in our laboratory every day, the result from each flaker for the thickness and slenderness ratio. These are very important factors in the quality of particles – and they are what particleboard is made from after all.”
Eighty percent of the raw material at Chalkis is recycled wood, which Mr Kalamaras said is cleaned very thoroughly.
“As the capacity of our factory is not very big, we can maintain our quality and that quality is well-known in Greece and in neighbouring countries such as in the Balkans and the Middle East.”
Value-adding is important to Shelman and 90% of production is surfaced with melamine films, using paper impregnated on the Vits line at the Komotini factory.
Chalkis has two Siempelkamp and one Wemhoner short-cycle press lines. There is also a postforming line with Homag machining and another Wemhoner press; and two direct postforming lines; while veneering of particleboard and MDF is also carried out, using imported sliced veneer.
“We have recently invested a lot of money in environmental processes, too, and are ISO14001 certified by TüV. This included installing a WESP (wet electrostatic precipitator) from EWK in 2006 and an industrial waste water treatment plant employing biological and chemical treatment,said Mr Kalamaras.
A very unusual feature of this large, 400,000m2, site located on an island just off the east coast of Greece, within 80km of Athens, is that it has its own private harbour which can serve three 30,000- tonne ships simultaneously for the export of finished goods and the import of raw materials and traded products.
In addition to its own manufactured products, Shelman also trades in Scandinavian and Russian solid wood (lumber) and trades in MDF panels.
In 2006, Shelman established a new company in Greece, as a 50/50 joint venture with the Sofianos family, called Shelman Sofianos, trading in solid wood and laminate flooring.
In the same year, it bought a 40% shareholding in Sofrom Parquet SA in Romania (also the property of the Sofianos family), which manufactures oak flooring.
Shelman also has two wholly-owned subsidiaries, in Patras and Athens, which trade in all kinds of wood products to the retail market.
Perhaps one of Shelman’s most significant subsidiaries is Greece’s only resin producer, Hadjilucas, of which it owns 85%. It was built by Chimar Hellas.
In a major move for the Greek panel industry, on December 2, 2009, fellow Greek wood products producer Alfa Wood bought around 72% of Shelman’s shares from the owners, the Iliadis family, and the deal was approved by the Hellenic Competition Authority on January 11.
“There are a lot of synergies [between the two companies],said Mr Kalamaras. “They have MDF production and we have particleboard; they produce veneer in Bulgaria and we use veneer. As a group we will be very strong in postforming and in semi-finished elements for the furniture industry. We also have our own glue factory and are working on new products for board manufacture and impregnation.
“Undoubtedly it [the takeover] will allow us to face with more optimism the difficult years that lie ahead of us,concluded the technical director.
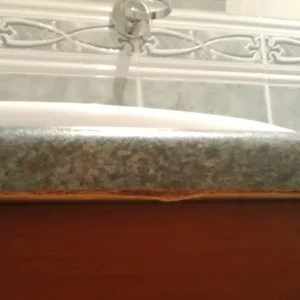