Globalisation and consolidation are much-used words these days in every industrial sector and the panel manufacturing industry is no exception as large corporations flex their muscles in overseas markets.
Thus we see European-based companies buying existing mills, building new ones or entering into joint ventures, notably in eastern Europe and Asia, but also in Latin America.
However, with their vast home market, the North American panel producers are less evident in other parts of the world, although there is a very notable exception. To give you a clue, it is the one which is hardest to spell. You’ve guessed, I am sure. We speak of the Weyerhaeuser Company.
Headquartered in Federal Way, Washington, US, the company is a major player in the North American wood products industry and owns extensive forestlands there and elsewhere. Founded in 1900, today the company can boast of annual sales of US$22.7bn and currently employs about 55,000 people in 18 countries.
Worldwide,Weyerhaeuser, as one of the largest forest owners in the world, owns, licenses or leases more than 38 million acres of timberlands in North America, Australia, New Zealand and Uruguay.
Weyerhaeuser Forestlands International was founded in 1995 and manages about 600,000 acres of timberlands in joint operating interests in Australia, New Zealand and Uruguay.
To use a clothing market analogy, Weyerhaeuser’s entry into Europe was by the ready-to-wear, rather than tailor-made, route when it bought fellow US-based company Willamette Industries after a drawnout hostile takeover battle, which it finally won in February 2002.
This not only brought Weyerhaeuser the large North American Willamette forestry, paper and wood products business, but also a European operation comprising three mills in the composite panels industry – two MDF and one particleboard.
Prior to that takeover,Willamette had a turnover of around US$4bn,Weyerhaeuser US$15bn; and Weyerhaeuser had no involvement in panel manufacturing in Europe.
But to put that recent history into perspective, we have to go back rather further, to the establishment of a European MDF mill by probably the most famous name in that business, the Medford Corporation, which launched the Medite brand on an unsuspecting and uninitiated world in the mid-1970s with its mill in Medford, Oregon in the US.
It is difficult to realise now that only 20 years ago MDF was an acronym which meant nothing to most people – nor indeed did the full version, ‘medium density fibreboard’.
Many regarded it as an unnecessary invention when they had particleboard and plywood with which they were perfectly happy (in their ignorance) and which they had been using for many years by then.
Undaunted by such scepticism, Medite built a 150,000m3 MDF manufacturing plant in Clonmel, Eire (the Republic of Ireland) which opened its doors in September 1983. At the time, this was one of the world’s biggest MDF plants and prior to that opening, western European total MDF capacity stood at only 145,000m3. A brave move indeed, then. Or, as it transpired, a far-sighted one.
Geoff Rhodes, marketing and sales director of Weyerhaeuser Europe (and formerly of Medite Europe and Willamette Europe), who could arguably be called ‘Mr MDF’ for his enormous enthusiasm for, and contribution to, the promotion of the product to an often sceptical audience over the years, remembers it well.
While working for the Canadian sales agency, Seaboard International, in London in 1976, Mr Rhodes obtained the first British order for Medite, imported from Medford in the US. “This was a product with many advantages but a market had to be created,he says. “We had a pioneering spirit and 30 years later we’re still pushing just as hard and still finding new markets and applications.”
The Medite mill in Clonmel is still one of Europe’s strongest MDF brands and has moved on from that first Washington Iron Works (WIW) multi-opening press.
The mill installed its first continuous press line in 1993. This was a Dieffenbacher CPS unit, 20.6m in length and 2.5m wide, which was installed specifically to give thin board capacity, down to 3mm thickness.
Until 2001/2, the WIW and Dieffenbacher presses ran side by side but then Willamette purchased a second Dieffenbacher continuous line and mothballed the WIW press.
The total MDF capacity of the Clonmel site is now 400,000m3 a year and all production is Forest Stewardship Council (FSC) certified, as the Irish forest resource itself is certified as sustainably managed.
In the late 1990s,Willamette, then owners of Medite, looked to expand their European operations and searched for a suitable mill to acquire with a good quality, sustainable and abundant wood resource.
“When Willamette bought Medite in Clonmel, it was only a small step for a US$4bn company, so it looked at growing its international business,explains Mr Rhodes. “We were now European MDF specialists and identified the Mediland mill in France as a good basis for the expansion of our activities – and it was for sale.”
Built by French company Seribo in the late 1980s as a testimony to its own engineering abilities and with the idea of selling MDF plants to the rest of the world, the mill had a design capacity of 140,000m3 (but was producing only 70,000m3) from a Pagnoni multi-daylight press line.
It was then bought by a diverse Belgian industrial entrepreneurial group in the early 90s, purely as an investment.Willamette bought it from that company in 1998.
“Mediland had a good geographical position, in south west France in the Landes de Gascogne for more southern European markets such as Iberia – and it was a long way from Clonmel so expanded our market,says Mr Rhodes.
Willamette invested in the plant, improving fibre handling, pressing and finishing and maximised the potential of the press, achieving 160-170,000m3 output today.
There are no overlaying facilities, with the emphasis being on the Medite approach of making specialist grades of ‘raw’ board.
Not content with this addition to its portfolio of mills,Willamette then had the opportunity, in 1999, to acquire another mill utilising the same French forest resource, but this time making particleboard – a new departure for the European operation.
The mill is located in Linxe, 30km from Mediland, and was already producing a well-respected brand of particleboard, Darbo, under family ownership.
It again had a Dieffenbacher continuous press, with a planned extension that the original owners had not carried out.
“Willamette completed those plans, extending the press from 33m to 42m and investing US$23m to increase the capacity from 250,000m3 a year to 430,000m3. We also invested heavily in overlaying, installing a Dieffenbacher short-cycle press line with annual capacity of 100,000m3,says Mr Rhodes. The work, at what is now know as Weyerhaeuser Darbo SAS, was completed in early 2002.
The Darbo mill produces standard grade and moisture-resistant particleboard as well as flooring grade tongued and grooved (T&G) board and those melamine-faced panels.
Readers will now realise that the combined capacity of the Medite, Mediland and Darbo mills is just under one million m3. To be as precise as one can: 970,000m3 a year.
So to bring our story up to date, we now have Weyerhaeuser Europe Ltd with its Medite brand MDF produced in Clonmel, Ireland;Weyerhaeuser Mediland SAS producing MDF in Morcenx, France; and Weyerhaeuser Darbo SAS producing particleboard in Linxe, France.
The sales offices for Europe are located in Southend-on-Sea, Essex, England and at Roermond in the Netherlands, complementing the French sales office, which is based in Morcenx. All the European businesses come under the European Composite Panels Business sector of parent Weyerhaeuser, which also has offices in Brussels.
“We have three stand-alone brands [in Europe] and, from a marketing standpoint, had to present them as distinct brands but under the Weyerhaeuser banner – it was a challenge for us in maintaining a consistent approach to the market,says Mr Rhodes.
“Commercially it has been very important to have specialist grades of MDF, such as flame-retardant, moisture-resistant and exterior and we can expect increasing growth in these markets.
“We have been producing exterior grade for 16 years now and are one of the few producers of it. Several of the many shopfronts in the UK made of Medite Exterior date back nearly 15 years and are still looking good.We are also producing the latest lightweight boards, following the investment in the Medite line in 2001/2.
“We also have complementary products from the two factories because Medite can produce down to 3mm thickness, while Mediland can make 50mm and above due to its Pagnoni press.”
The Medite mill, together with its standard MDF production, produces Medite 313 for use in humid conditions, Medite FR flame-retardant panels used in many prestigious building projects, Medite Exterior for external signs, shopfronts, fascias and mouldings, Medite ZF (zero added formaldehyde) for use particularly in museums and laboratories, and Medite FQ (flooring quality), a high density moisture-resistant panel for laminate flooring manufacturers. Medite Lite has a density of only 600kg/m3 and is the latest addition to the Medite range.
The mill offers Mediland LP for finely detailed work, Mediland M1 flame retardant, Mediland UL lightweight panel (550kg/m3), Mediland MH moisture resistant and Mediland MC. This last is a panel made from Landes region pine with highly refined fibres for delicate routing and overlaying with PVC foils, or lacquering.
Darbo also has its own range of branded particleboard products. These include Darbopan standard grade, Darbobati intended for areas of short exposure to humidity, Darbodal T&G panel, and Darbodeco overlaid with decorative melamine paper on both sides. A complementary product to Darbodeco is Darbochan edging strips.
Of course the company still has to face the strong competition in the market like everybody else and Mr Rhodes is the first to admit that things have not been easy in recent years. “Since 2001, the general value of the MDF market has fallen away due to over-capacity,he points out. “The industry has had to get through the installation of three million m3 in the early 2000’s when decisions were made that resulted in a consumption of around 7.5 to 8 million m3 facing a capacity of 11.5 to 12 million m3.
“Even with double-digit percentage consumption growth, we could still see overcapacity, so millions of euros have been lost over the last four years or so. The industry [in Europe] overall lost around 50% of its previously established value of production and by early 2005, we had only recovered about half of that value – the whole European MDF industry has been trading at a real loss.”
Mr Rhodes feels that the market at the end of 2004 was probably reaching 11 to 12 million m3 “So maybe in 2005 we will finally get it back into balance,he suggests.
“The European industry hasn’t learnt to make investment decisions in a coordinated fashion because it is so fragmented. Maybe there is something to be learnt about the penalty which has to be paid for those kinds of decisions when they affect capacity so strongly. Those who made investment decisions in 2000 needed to realise that it could be an extended payback. But I am sure that MDF is a product that will continue to grow in usage and has much more technical potential.”
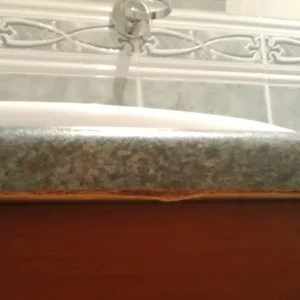