Five years ago a hangover spark from an earlier dryer fire kindled flames that raced through Boise-Cascade’s plywood plant in Medford, Oregon.
On the last day of operations before a 1998 holiday shutdown, a pitch fire behind the cooling section in the mill’s number two dryer broke out. The sprinkler heads quenched the flames, but just 20 minutes before the mill closed a spark in the rafters flared up again and flashed into dust. It was like dynamite detonating.
The fire exploded over to lay-up, down to the finish end and ran the length of the long crane shed. Fire crews focused on saving the power house but they lost the entire plywood plant and the planer mill.
Shift supervisor Phil Brown, an employee here since 1965 recalls the event: “I came from home and helped move veneer and vehicles away from the building. We couldn’t move fast enough. We saved maybe a third of the veneer. We had so much veneer stacked in the crane shed. It was a half mile long and the roof fell in 15 minutes.”
The mill is located on a large 124 acre site. With the ruins still smoking, management debated the future. They finally decided to rebuild, but only a high production four-press dry end. The salvageable veneer equipment would go to Boise’s green end at White City, six miles away. The Medford mill would import veneer from the company’s four veneer plants in the area.
The first panel in the ‘new’ mill came out of the press just one year later – the mill was essentially the same, except for the green end.
Mr Brown said: “During the rebuild, supervisors chased down different things. Two others and I helped put the glue loft together. A lot of our own people put the spread line back together. Many people were involved in the project.”
In some ways the fire was positive in that past experience could work into the new layout. Much of the existing equipment was salvaged. “We were able to design the plant so that when trucks pull in with veneer we have a steady process forward so that nothing moves backward. I think we dropped eight Hyster forklifts, just by everything running consistently forward,Mr Brown added.
He said dryer production is now at an all-time high and lay-up is better. It resulted in a mill producing 356 million ft2, 3/8in basis, of plywood annually with a crew of 400.
However, the project is still not finished. A chalked X on the mill floor marks the spot where an MDO press will be installed later this year. This 20-opening press, in storage, was replaced by a 40-opening after the fire. Its plates are being resurfaced.
The mill runs Douglas fir, pine, spruce, fir, and hemlock. Green veneer in 1/10in, 1/25in, 1/40in and 1/6in thickness is trucked to the site. The mill carries about 2.5 million ft2 of green veneer in the yard. It is parceled out to the two 16-section, three 14-section and one 12-section steam-heated Coe and Moore dryers which offbear air through two GeoEnergy RTO systems. Ventek moisture meters are installed on all of them and a Ventek scanner on one. Four Jeddeloh Sweed feeders are in place.
There are two 16-section, three 14-section and a 12-section dryer. Three dryers offbear to Jeddeloh Sweed stackers. Two tenders monitor the dryers. Twenty four hour dryer production is one million ft2 while 1.1 million is laid up in the 24 hours.
A Clarke’s Sheet Metal spark detection system is installed.
Veneer that does not come out in full sheets goes to a Panel Equipment composer that makes it into either a 4x8ft or an 8x4ft sheet for the lay-up lines.
The mill aims for 13% re-dry for good production. Four of the dryers are equipped with Metriguards to assure proper specifications for LVL. The Medford mill supplies about 30% of the blanks for Boise’s White City, Oregon, LVL mill where they are finger- jointed into long beams. This material, with everything laid up parallel, is plywood laminated veneer, or PLV.
The mill has an elaborate flow-through Raimann patching installation with 25 machines, 22 of them in a line. Before the fire, two patching shifts were required, now just a single shift does the job. These machines produce solid faces for special products. The three satellite machines patch for specialised products. A Holt glue loft is run by a single operator.
A Coe spray line and a company-built curtain coater line lay up panels. Both lines were in place before the fire, but required much work to restore operational ability. Mill superintendent Tom Gilman said the spray line requires nine or 10 people to run, but productivity is so great that it replaces about a dozen people. The line uses 11 people for seven-ply and eight for five-ply. This line offbears to a line feeding the 40-, 30-, 36- and 32-opening presses. The computer keeps track of required panel mix. The mill has about 45 different lay-ups from three ply to seven ply. The thickest panel is 13/4in.
The curtain line operates with a crew of four – an operator for the main station, two offbearers and someone to clean up.
Sandwiches move to pre-presses then to 32-, 36-, 30- and 40-opening presses. These are Globe, Globe Raute conversion, Columbia Raute conversion, and SparTek.
Vacuum feeding serves all the machinery on the finish end. Another move was to elevate all the machinery to ease clean up.
A Globe feeder serves the Globe saws which offbear to a five-bin stacker. A fourman putty line, Globe T&G machine, (working predominately 3/4in, but also 5/8in, 3/4in, and 11/8in) and a Kimwood six-head sander round off the finishing side, along with an oiler for concrete form material.
Shipping is 40% by rail and 50% truck. Exports are a thing of the past with the state of California as the principal market along with other areas of the US southwest and eastern seaboard.
In plywood, specialities are a necessity these days. Mr Brown says: “Our grade faces aren’t as available as they were 15 or 20 years ago. You have to compensate with some occasional sheathing. We’re trying to get more into the industrial panel business, such as providing material for window and door part manufacturers. We’re laying up about 13 trucks a week for windows and doors – maybe 4% to 5% of production.
“Our engineered wood business took off and the plywood market followed that trend,he concluded.
One unusual feature is a horizontal ‘cooling tower’ which cools water from the power plant. Water, at over 100°F, is sprayed into a pond for cooling.
Safety is an important consideration as it is in all Boise Cascade mills. One example is a harness system suspended from the ceiling of the covered truck loading slab. Drivers working on top of their loads tie on to prevent falls, should they slip.
“Your best resource is your employees,said Mr Brown. “They can tell you what does and doesn’t work. A lot of input from our employees helped with the rebuild after the fire. We had experienced people who knew what they were talking about when they set up this machinery.”
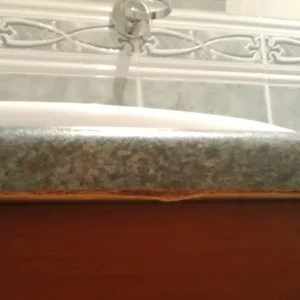