Formed by a team of dedicated scientists and engineers with over 20 years’ experience in the development, manufacture and application of formaldehyde-based resins for the wood panel industry, NTL says it provides the industry with “Professional consulting services and innovative practical, applied and proven solutions to improve the quality and efficiency of panel production”.
The company’s resin technology encompasses particleboard, MDF, plywood and OSB manufacture and decor paper impregnation.
Realising that in today’s increasingly demanding and competitive panel industry, mills are constantly seeking more cost-efficient and optimised resin processes in order to be more competitive, NTL says it has developed formaldehyde-based resin systems to increase board production while reducing glue dosage and formaldehyde emissions from both panels and dryers, without affecting the production process and board properties – and without any overall cost increase.
“This is the reason why NTL was formed and is the origin of its founding principles, providing wood panel mills with our state of-the-art, cutting-edge, proven and cost-efficient formaldehyde based resin binder systems,says Nikos Pargianas, technical director and founder of NTL Chemical Consulting. Mr Pargianis adds that he has worked in field application and technical support for many years and has been involved in projects with some of biggest wood panel plants worldwide.
“We’ve invested heavily in our R&D facility at EKETA Technology Research Institute, which is actively engaged in technological collaborations with renowned research bodies such as the Aristotle University of Thessaloniki and the Chemical Polymerization & Process Engineering Research Institute,says
Mr Pargianis.
“In addition, strategic relationships are in place with other European universities and technical institutes which allow NTL to follow closely any new technology developments and market trends in the wood panel industry.”
The technical director adds: “NTL’s biggest strength is its R&D, founded on years of industrial experience and the requests of our customers. The primary focus of our R&D is to develop resin technologies which are innovative, add value and are cost-efficient in meeting our customers’ specific needs”.
The modern, fully-equipped laboratory at the Technological Park of Research & Technology Centre in Thessaloniki was completed only last year.
“Our experienced scientists have already helped us to develop innovative resin technology products which have proved superior to some of the biggest competitors in the marketplace,says Mr Pargianis, proudly.
The company says its R&D is specifically targeted on providing its clients with solutions to their problems on a continual basis, to meet their ever-changing requirements and to anticipate industry trends.
“By relentlessly upgrading and developing resin formulation know-how, and by turning innovative ideas to realisable value-added and practical solutions, NTL can offer unparalleled services to its clients,claims the technical director.
“Importantly, all these developments are undertaken by NTL with the utmost responsibility for the environment,
he adds.
NTL says it has a global network of scientists who have hands-on experience in developing and applying a wide range of formaldehyde-based resins to more than 250 wood panel production mills around the world.
“We’re close to our customers because we truly focus on providing them with service, quality and an understanding of their exact needs,says Mr Pargianis. “Our role is in providing them sound solutions and ongoing technical support, including our complete technical/consultation
services and new resin technologies.
“This service extends from training our clients’ personnel at their R&D and resin plants to practical application of the technology in their panel manufacturing units.”
Mr Pargianis says it is because NTL is a relatively small company that it can give this personal approach to its customers, while larger companies may only be able to offer fixed technology, offering little flexibility to the client.
“In terms of our products we can provide clients with a diverse range of our high-performance formaldehyde based resin and resin additive technology systems which are suitable for virtually all wood based panel producers,he says.
The company says it can provide a wide range of resins for particleboard such as UF (urea formaldehyde), UMF (urea melamine formaldehyde), MUF (melamine urea formaldehyde) and PF (phenol formaldehyde) for E2, E1, E0 and Super E0 board production, as well as additives such as activators, scavengers and special hardeners.
For MDF, NTL provides a range of resins such as UF, UMF, MUF, PUF (phenol urea formaldehyde) for E2, E1, E0 and Super E0 board production, as well as additives.
For plywood, it offers a range of amino-based resins such as UF, UMF, MUF, MUPF (melamine urea phenol formaldehyde) for E2, E1 and E0 board production and phenolic resins such as PF for hardwood, softwood or tropical wood, PF fast-curing, PF low-cost and additives (hardeners).
In addition, NTL can provide other PF and PRF (phenol resorcinol formaldehyde) resins for laminated veneer lumber (LVL); and phenolic resins (core and surface), or MUF or MUPF for the surface layer (light colour) of OSB.
The company’s range of resin technology also includes impregnation resins and additives such as UF and MF for low pressure laminates. For post forming there are MF and PF for high-pressure laminates, as well as PF for phenolic film, hardeners, plasticisers, modifiers and release/wetting agents.
NTL claims all its resin technologies are environmentally friendly and capable of meeting or exceeding the various performance criteria required by the most stringent European, American and Japanese Standards, ensuring performance to V20, V313 or V100, as well as formaldehyde classes E2, E1, E0 or Super E0.
James Vlachos, NTL’s sales & marketing manager, says: “NTL is well poised to meet all the demands of our customers and as such we offer a wide variety of other product technologies including PF, PRF and RF applications in fibreglass (insulation), concrete forming, medium density overlay, parquet foil and door skin production. We also offer PF for electro-technical laminates, additives for manufacture of flame retardant Kraft and a range of resins used for foil and paper lamination on ‘hot roll’ laminators such as those made by Hymmen and in Gypsum board and plywood.”
Mr Vlachos adds: “We also provide other resins [for other industries], mainly through our associate partner network, while, apart from the wide range of resin technology we offer to our clients worldwide, we also offer our international experience in the engineering of formaldehyde and resin production plants.
“We provide clients with tailored design and procurement for turnkey formaldehyde, resin and resin additive plants of different sizes through our strong association with our professional partners.
“We offer complete process technology, engineering design, procurement, technical assistance, supervision and complete training services to our client’s plant personnel for the construction of formaldehyde production and resin plants for local manufacturing as the most cost-effective alternative”.
Mr Vlachos says the future of NTL is to strive to maintain its strong international presence.
“We are building on our worldwide reliability and proven cost-efficient resins, and on providing clients with just the right solutions wherever they are needed for attracting new licensees in new and growing markets,he says, adding that NTL has a strong client base in SE Asia and South Korea and is currently embarked on setting up new business licensees in Russia, India, China and Latin America.
“As far as we are aware, NTL is the only company that backs its motto in writing, which simply states: ‘If you
don’t save, you don’t pay’,concludes
Mr Vlachos.
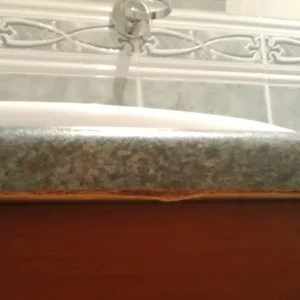