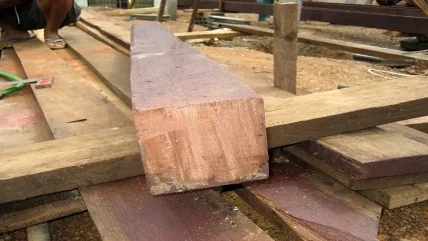
Wood recycling as part of a circular economy is an important trend these days, not only for the positive environmental message it projects but also because it opens up valuable additional raw material streams.
Furniture maker IKEA is of course a huge user of wood for its products around the globe and is one of the companies leading the charge on the circular economy message.
Tomra Recycling Sorting designs and manufactures sensor-based sorting technologies for the global recycling and waste management industry to transform resource recovery and create value in waste.
Both companies teamed up for a webcast “The future of wood recycling” recently to discuss the issue and outline how a circular economy for wood can become a reality and a profitable business case for the panel industry.
Jose Matas, segment manager wood at Tomra, kicked off the session by explaining current market trends influenced by the energy crisis in Europe, the impacts of climate change and industry’s increased reliance on recycled content in order to meet its sustainability targets.
“The energy crisis is hitting hard on us in Europe,” said Mr Matas. “Many households turn to wood as an alternative heating source, further driving up the already record high demand for wood.
“Combined with the general lack of materials on the market, sourcing wood in sufficient volumes and qualities has become increasingly difficult and prices are at an all time high.”
He added that in order to access material and maintain profitable operations, the panel board industry has recognised the possibilities a circular treatment for wood offers. If the massive amounts of waste wood generated annually are properly collected, sorted and recycled into individual material fractions, both recyclers and wood-based panel manufacturers reap commercial benefits.
Recyclers, on the one hand, are given the means to create individual waste wood fractions – from non-processed wood to MDF – and market it as high-quality secondary materials.
Manufacturers, on the other hand, profit from a constant source of input materials, maintain profitable operations thanks to a better price point of recycled wood compared to fresh wood, and help ensure the volumes and quantities demanded by the market.
Jan-Olof Fechter is material expert and technique engineer at IKEA of Sweden AB, responsible for purchasing wood and material in Sweden, and an engineer responsible for particleboard and fibreboard.
“For the last 20 years our motto has been affordability and sustainability,” said Mr Fechter.
“We are committed to transforming into a circular business. There are several ways of achieving this. We buy back the furniture we sell – we pay for it and try to sell it to somebody else. Another way is leasing of furniture to business customers, such as office furniture for three years like leasing with a car. And we are recycling material to make furniture again, something that has been done for many years in the particleboard industry.”
IKEA currently has a 25% recycled wood share for its particleboard.
“But our goals are more ambitious. The 2030 goal is set to 80% for particleboard because we see the advantages. Even for MDF and HDF, which are counted as unrecyclable, we have set a target of 15% because there are some ground-breaking technologies breaking through in the recent years which are now making this possible.”
Mr Fechter said recycling wood into particleboard is pretty easy using waste wood pallets and cable drums, but recycling fibreboard content is not as clean and it is traditionally burned instead.
He said sorting processes now existed to separate the solid wood for particleboard and the fibreboard fractions.
The mid-term target for 2025 sees IKEA planning to increase the amount of recycled content to 56% in particleboard and 9% in MDF/HDF boards.
In 2020, IKEA bought back 155,000 pieces of its furniture from customers, equating to about 2,500 tons or 1% of the company’s furniture, whereas some 800,000 tonnes of its furniture is recycled.
Murat Sanli, wood sales engineer at Tomra, explained how a holistic approach can maximise recycled wood content.
“To exploit the full potential of recycled wood, we must concentrate on three pillars: the collection, sorting, and recycling of waste wood.”
Technology-driven sorting solutions are central to the final product quality.
To help manufacturers become more sustainable and increase recycled content in their panel boards, they have to use the purest material fractions, such as non processed wood and MDF.
“Recovering individual wood fractions requires extensive cleaning and sorting processes because waste wood consists of numerous different materials, including contaminants and different types of wood such as OSB, MDF, plywood, coated materials and recyclable non-processed fractions.
“Using smart technologies throughout the sorting process gives plant operators a three fold competitive edge: they can recover wood by type as per their requirements, realise high throughputs and achieve purity levels that cannot be achieved with conventional technology.”
Tomra’s products use high capacity near infrared (NIR) technology to extract the most value from resources and keep materials in a loop of use and reuse. To date, more than 8,200 systems have been installed in 100 countries worldwide.